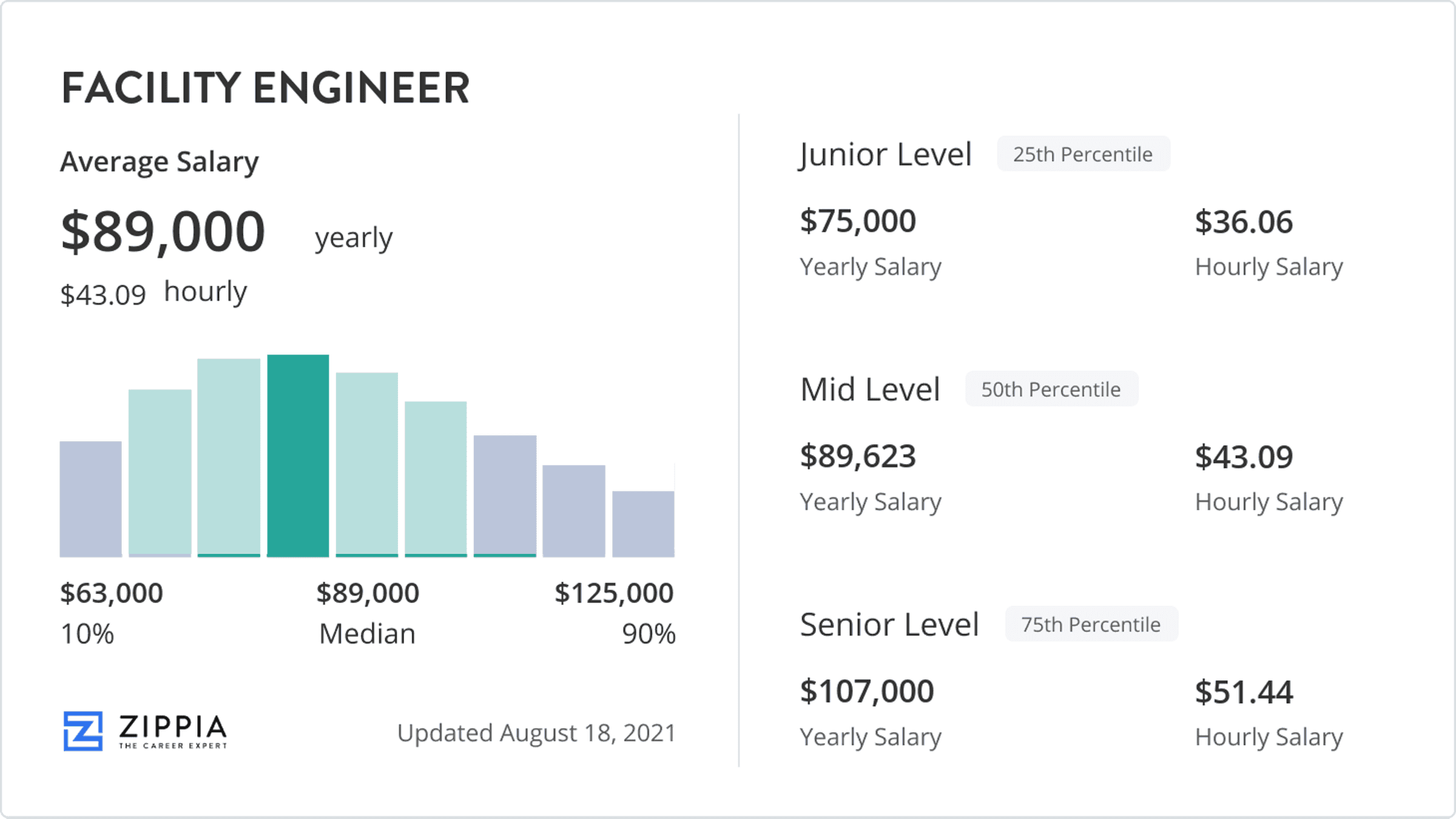
When you want to ensure that your product is profitable, you need to think about the manufacturing cost. For example, if you want to sell wooden tabletops furniture, you might need to purchase wood glue and other materials. For your products to last, you will need to be able find reliable suppliers of high quality raw materials. You can end up with a defective item and lost revenue if your supplier does not provide high quality raw material.
The most effective way to understand manufacturing cost is to break it down into three main categories. Each of these types of costs will affect the final price of the product that you are selling. The unit cost is a key component of manufacturing costs. It's the cost it takes to produce an item. It is a good place for you to start but can be tricky to define.
The units-per-hour or unit-per-unit ratio is a good rule of thumb to use when determining the most cost-effective manufacturing process for your company. For example, if you are planning on making 5,000 wooden tables, you can figure out the average cost of making each unit by calculating the number of hours it takes to complete the project.
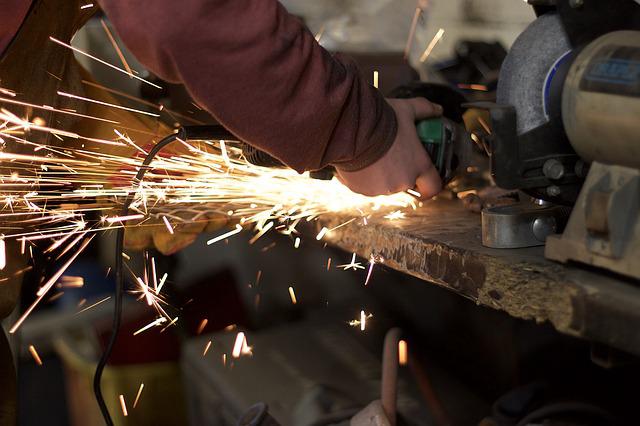
Budgeting for administrative and general expenses is essential in addition to direct labor costs and equipment manufacturing. These can include advertising costs, office supplies, rent, and sales commissions. Compliance with regulatory requirements will require you to spend substantial amounts. However, you can minimize the cost of these expenses by using online inventory control software to track production and forecast production.
Direct labor costs are the wages paid to workers in a factory, and includes employees engaged in the actual preparation of the goods for manufacturing. They can also include maintenance personnel, sanitation personnel and bookkeepers. Generally, the hourly rate of direct labor is about $150 per hour.
Manufacturing has indirect costs. These include utility bills and maintenance costs. To calculate the unit-per-hour you need to include the costs of preparation, assembly and delivery. A manufacturing overhead account will help you to calculate the total cost of your operation, and will provide you with an estimate of what your overhead will be for the coming fiscal year.
You should also take into account the cost of manufacturing a product. Examples of these are wood, thread, and cotton. You should not use low-quality materials. If you are a food producer in certain regions of the globe, you will need to test your products for safety.
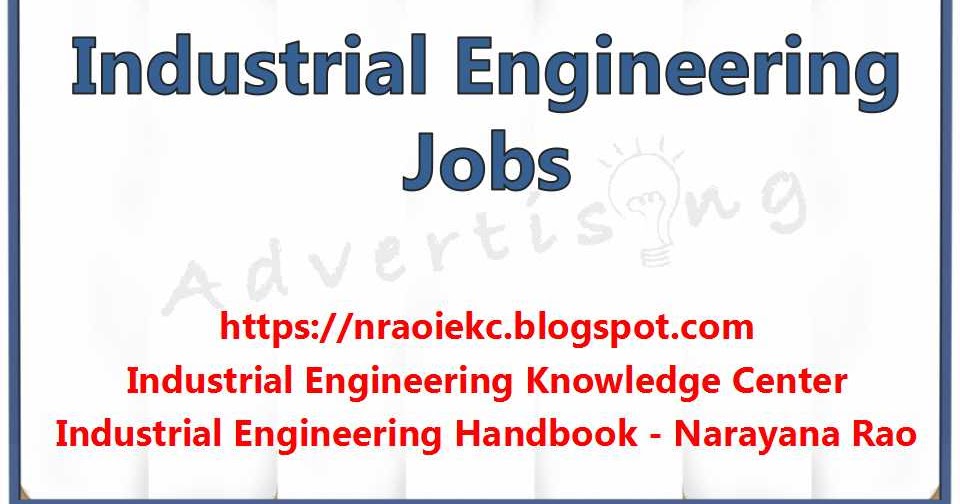
Knowing the unit-per-unit ratio and the manufacturing cost of your products will help you to figure out whether you should start producing a new product. You should also know the price you should charge for your products to increase your business' profitability.
FAQ
What is the role of a production manager?
A production planner makes sure all project elements are delivered on schedule, within budget, as well as within the agreed scope. They ensure that the product or service is of high quality and meets client requirements.
What are the products and services of logistics?
Logistics is the process of moving goods from one point to another.
They encompass all aspects transport, including packaging and loading, transporting, storage, unloading.
Logisticians ensure that products reach the right destination at the right moment and under safe conditions. They assist companies with their supply chain efficiency through information on demand forecasts. Stock levels, production times, and availability.
They monitor shipments in transit, ensure quality standards, manage inventories, replenish orders, coordinate with suppliers and other vendors, and offer support services for sales, marketing, and customer service.
Is automation important for manufacturing?
Not only are service providers and manufacturers important, but so is automation. It allows them provide faster and more efficient services. In addition, it helps them reduce costs by reducing human errors and improving productivity.
What does warehouse mean?
A warehouse is an area where goods are stored before being sold. It can be either an indoor or outdoor space. It may also be an indoor space or an outdoor area.
What skills do production planners need?
Being a production planner is not easy. You need to be organized and flexible. It is also important to be able communicate with colleagues and clients.
Statistics
- According to the United Nations Industrial Development Organization (UNIDO), China is the top manufacturer worldwide by 2019 output, producing 28.7% of the total global manufacturing output, followed by the United States, Japan, Germany, and India.[52][53] (en.wikipedia.org)
- (2:04) MTO is a production technique wherein products are customized according to customer specifications, and production only starts after an order is received. (oracle.com)
- Many factories witnessed a 30% increase in output due to the shift to electric motors. (en.wikipedia.org)
- [54][55] These are the top 50 countries by the total value of manufacturing output in US dollars for its noted year according to World Bank.[56] (en.wikipedia.org)
- It's estimated that 10.8% of the U.S. GDP in 2020 was contributed to manufacturing. (investopedia.com)
External Links
How To
How to Use the 5S to Increase Productivity In Manufacturing
5S stands to stand for "Sort", “Set In Order", “Standardize", and "Store". Toyota Motor Corporation created the 5S methodology in 1954. It allows companies to improve their work environment, thereby achieving greater efficiency.
This method aims to standardize production processes so that they are repeatable, measurable and predictable. Cleaning, sorting and packing are all done daily. Because workers know what they can expect, this helps them perform their jobs more efficiently.
Implementing 5S involves five steps: Sort, Set in Order, Standardize Separate, Store, and Each step requires a different action to increase efficiency. For example, when you sort things, you make them easy to find later. When you arrange items, you place them together. You then organize your inventory in groups. Labeling your containers will ensure that everything is correctly labeled.
This requires employees to critically evaluate how they work. Employees need to be able understand their motivations and discover alternative ways to do them. In order to use the 5S system effectively, they must be able to learn new skills.
The 5S Method not only improves efficiency, but it also helps employees to be more productive and happier. They feel more motivated to work towards achieving greater efficiency as they see the results.