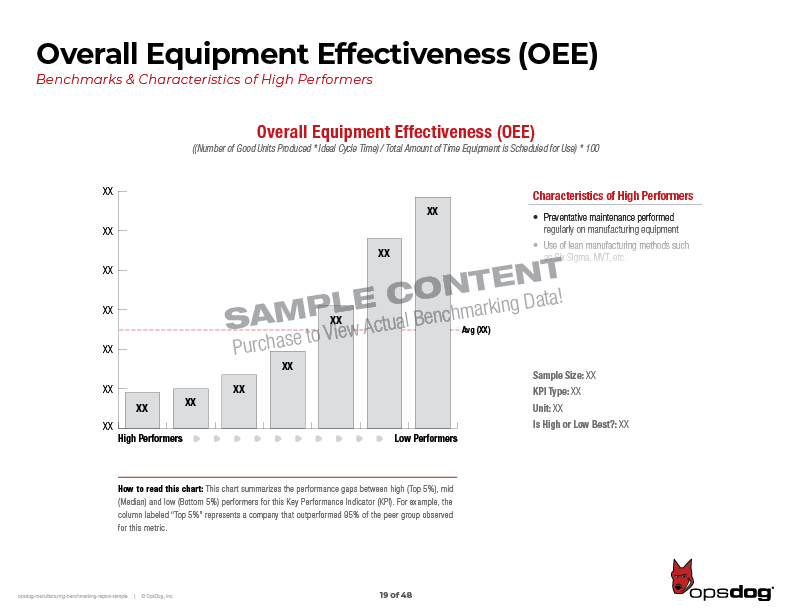
You will need to have the right education and training to be a manufacturing engineer. A master's degree program is available for some graduates that focuses on product, business and process knowledge. Majority of manufacturing engineers get their majority of their training in their degree program. They learn through practical experience with standard tests, measurements, and experiments. Employers must grant them a license to work in business. This signifies that they have the right qualifications for the position.
Manufacturing engineer skills
Manufacturing engineers can rise from an entry-level to a managerial position depending on their position. Their job description will include the skills they will need to be successful. They must be proficient in math and critical thinking. A manufacturing engineer should be able to communicate effectively with people at all levels of the organization. These are only a few of many skills required for a manufacturing engineer to succeed in their role.
Manufacturing engineers are responsible for the design, maintenance and modification of different processes and systems. They will also be responsible for the environmental impact of manufacturing processes. They need to be creative thinkers, designers and have a good understanding of manufacturing processes. A manufacturing engineer must keep current with current trends and regulations, as well as stay on top of industry news. A manufacturing engineer must be able work well with other engineers.
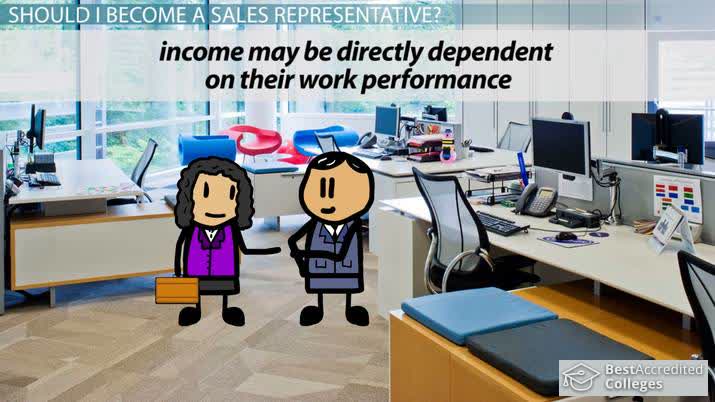
Responsibilities as a Manufacturing Engineer
Manufacturing engineers are responsible for developing and determining production costs. Apart from designing and developing production processes they also make mathematical calculations, troubleshoot, and evaluate manufacturing materials and processes. While most of their work is done in the office, they might be required to travel to other locations (e.g. to the factory floor). Some manufacturing engineers may be required to supervise production personnel or direct technicians. These employees are responsible the smooth running a production line.
Manufacturing engineers are responsible for designing and implementing manufacturing processes. They also have to monitor their efficiency. Manufacturing engineers analyze manufacturing processes, design equipment, and implement quality control systems that ensure the highest quality products. Manufacturing engineers are responsible for the design and development of manufacturing processes. They also adhere to safety and quality regulations. Manufacturing engineers have a variety of duties beyond what they do at work. They must conduct research, write reports, and maintain documentation.
Career outlook for manufacturing engineers
Manufacturing engineers have a great career outlook. Although their growth is slower than that of other occupations, job creation is expected higher than average. Manufacturing engineers will be more employed as a result. For manufacturing companies to succeed, they need to be successful in planning, logistics, as well as new methods of production. Despite slow growth there is a high demand for mechanical engineering. Most job seekers will come from the school system.
According to the Bureau of Labor Statistics in the United States, the number of manufacturing engineers is expected to rise by 9% between 2026-2026. These professionals should enjoy teamwork, as well as a challenging work environment. Manufacturing engineers enjoy high levels of job satisfaction and are often able to stay in the field for many years. Manufacturing engineers may be employed in factories that manufacture cars and trucks. You may also find manufacturing engineers in research and development companies, wholesale trade, or consulting services. Some industrial engineers quit engineering to seek managerial jobs.
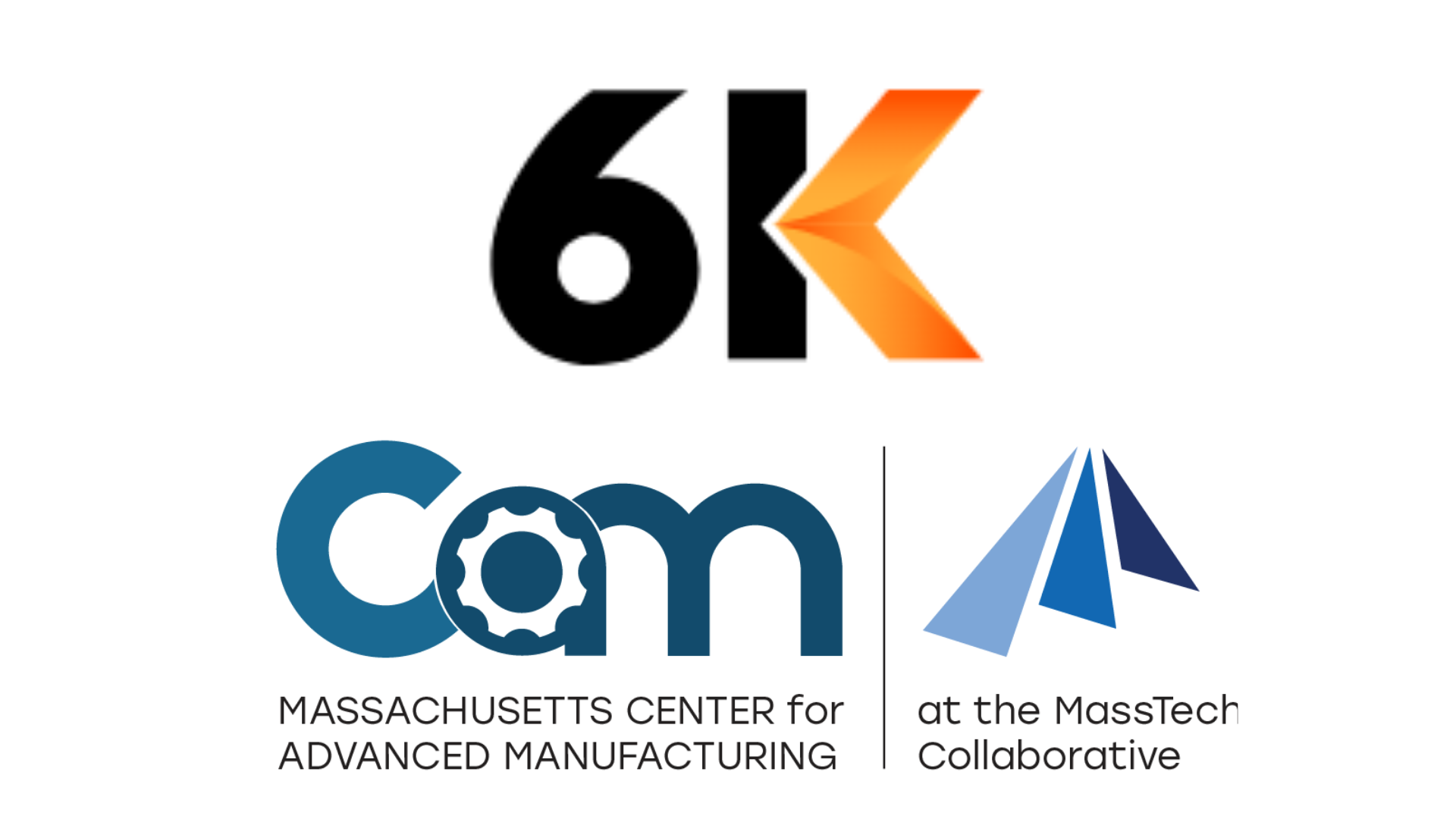
Education requirements for manufacturers engineers
For most jobs as a manufacturing engineer, a bachelor's degree in engineering (BSE), is required. Students can expect to learn about general science, math, and engineering concepts as well as computer-aided design (CAD) software. Students can expect to learn communication skills, as well as a solid foundation of mathematics. Additional courses that may be required include courses in ethics and the humanities. Education requirements for manufacturing engineers can vary widely, but in general, BSEs are well-rounded.
The education requirements for a career in manufacturing engineering require strong mathematics and science backgrounds, as well as analytical and problem-solving skills. As well as being creative, they need to be able to work in a team. Manufacturing engineers often work full-time after graduating. As part of their job, they are often required to travel and observe manufacturing operations from different locations. Manufacturing engineers must possess a strong work ethic, as well as the ability to keep up with current trends in manufacturing.
FAQ
What are the 7 Rs of logistics?
The acronym 7Rs of Logistics refers to the seven core principles of logistics management. It was developed by International Association of Business Logisticians (IABL), and published as part of their "Seven Principles of Logistics Management Series" in 2004.
The acronym is composed of the following letters.
-
Responsive - ensure all actions are legal and not harmful to others.
-
Reliable - Have confidence in your ability to fulfill all of your commitments.
-
Reasonable - make sure you use your resources well and don't waste them.
-
Realistic - consider all aspects of operations, including cost-effectiveness and environmental impact.
-
Respectful - Treat people fairly and equitably
-
Resourceful - look for opportunities to save money and increase productivity.
-
Recognizable: Provide customers with value-added service
Are there any Manufacturing Processes that we should know before we can learn about Logistics?
No. No. Knowing about manufacturing processes will help you understand how logistics works.
What is meant by manufacturing industries?
Manufacturing Industries are businesses that produce products for sale. Consumers are those who purchase these products. These companies employ many processes to achieve this purpose, such as production and distribution, retailing, management and so on. These companies produce goods using raw materials and other equipment. This includes all types manufactured goods such as clothing, building materials, furniture, electronics, tools and machinery.
What is the responsibility for a logistics manager
A logistics manager ensures that all goods are delivered on time and without damage. This is done by using his/her experience and knowledge of the company's products. He/she must also ensure sufficient stock to meet the demand.
What does it mean to warehouse?
A warehouse is an area where goods are stored before being sold. It can be either an indoor or outdoor space. In some cases it could be both indoors and outdoors.
What are the essential elements of running a logistics firm?
To be a successful businessman in logistics, you will need many skills and knowledge. Good communication skills are essential to effectively communicate with your suppliers and clients. It is important to be able to analyse data and draw conclusions. You will need to be able handle pressure well and work in stressful situations. In order to innovate and create new ways to improve efficiency, creativity is essential. You must be a strong leader to motivate others and direct them to achieve organizational goals.
To meet tight deadlines, you must also be efficient and organized.
How can we improve manufacturing efficiency?
First, identify the factors that affect production time. We must then find ways that we can improve these factors. You can start by identifying the most important factors that impact production time. Once you've identified them all, find solutions to each one.
Statistics
- (2:04) MTO is a production technique wherein products are customized according to customer specifications, and production only starts after an order is received. (oracle.com)
- In 2021, an estimated 12.1 million Americans work in the manufacturing sector.6 (investopedia.com)
- In the United States, for example, manufacturing makes up 15% of the economic output. (twi-global.com)
- According to a Statista study, U.S. businesses spent $1.63 trillion on logistics in 2019, moving goods from origin to end user through various supply chain network segments. (netsuite.com)
- [54][55] These are the top 50 countries by the total value of manufacturing output in US dollars for its noted year according to World Bank.[56] (en.wikipedia.org)
External Links
How To
How to use the Just-In Time Method in Production
Just-in-time is a way to cut costs and increase efficiency in business processes. It's a way to ensure that you get the right resources at just the right time. This means that you only pay for what you actually use. Frederick Taylor developed the concept while working as foreman in early 1900s. He saw how overtime was paid to workers for work that was delayed. He then concluded that if he could ensure that workers had enough time to do their job before starting to work, this would improve productivity.
JIT teaches you to plan ahead and prepare everything so you don’t waste time. Also, you should look at the whole project from start-to-finish and make sure you have the resources necessary to address any issues. If you expect problems to arise, you will be able to provide the necessary equipment and personnel to address them. This will ensure that you don't spend more money on things that aren't necessary.
There are several types of JIT techniques:
-
Demand-driven JIT: You order the parts and materials you need for your project every other day. This will enable you to keep track of how much material is left after you use it. It will also allow you to predict how long it takes to produce more.
-
Inventory-based: This type allows you to stock the materials needed for your projects ahead of time. This allows one to predict how much they will sell.
-
Project-driven: This approach involves setting aside sufficient funds to cover your project's costs. Once you have an idea of how much material you will need, you can purchase the necessary materials.
-
Resource-based JIT: This is the most popular form of JIT. This is where you assign resources based upon demand. If you have many orders, you will assign more people to manage them. If you don't receive many orders, then you'll assign fewer employees to handle the load.
-
Cost-based: This approach is very similar to resource-based. However, you don't just care about the number of people you have; you also need to consider how much each person will cost.
-
Price-based: This is similar to cost-based but instead of looking at individual workers' salaries, you look at the total company price.
-
Material-based is an alternative to cost-based. Instead of looking at the total cost in the company, this method focuses on the average amount of raw materials that you consume.
-
Time-based JIT: A variation on resource-based JIT. Instead of focusing on the cost of each employee, you will focus on the time it takes to complete a project.
-
Quality-based: This is yet another variation of resource-based JIT. Instead of worrying about the costs of each employee or how long it takes for something to be made, you should think about how quality your product is.
-
Value-based: This is one of the newest forms of JIT. In this case, you're not concerned with how well the products perform or whether they meet customer expectations. Instead, you're focused on how much value you add to the market.
-
Stock-based is an inventory-based system that measures the number of items produced at any given moment. It's useful when you want maximum production and minimal inventory.
-
Just-in-time (JIT) planning: This is a combination of JIT and supply chain management. This refers to the scheduling of the delivery of components as soon after they are ordered. It's important because it reduces lead times and increases throughput.