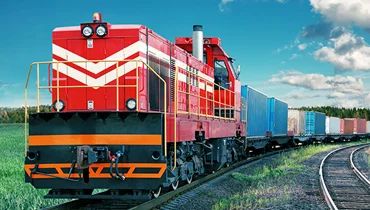
Demand management is a technique used to ensure that a company meets the demands of its customers. It's essentially about bridging gaps between marketing and supply by enabling companies to predict future demand. This process can increase speed and quality of delivery and reduce invoice disputes. It also lowers the cost of running a business.
Companies with a well-developed demand management system tend to be more responsive when the market changes occur. This is possible because they have a system that can identify the ideal customer and lead to effective marketing.
Demand management can be used to assist businesses in planning for future demand and increasing customer satisfaction. It can also help reduce the number invoice disputes and improve asset usage if done right. A well-designed demand management strategy can help improve operational flexibility, operational resilience, and operational flexibility.
A project management program can improve the demand management approach. This software helps teams coordinate their work and prevents silos. Also, a change management plan can help companies course correct supply chain problems quickly.
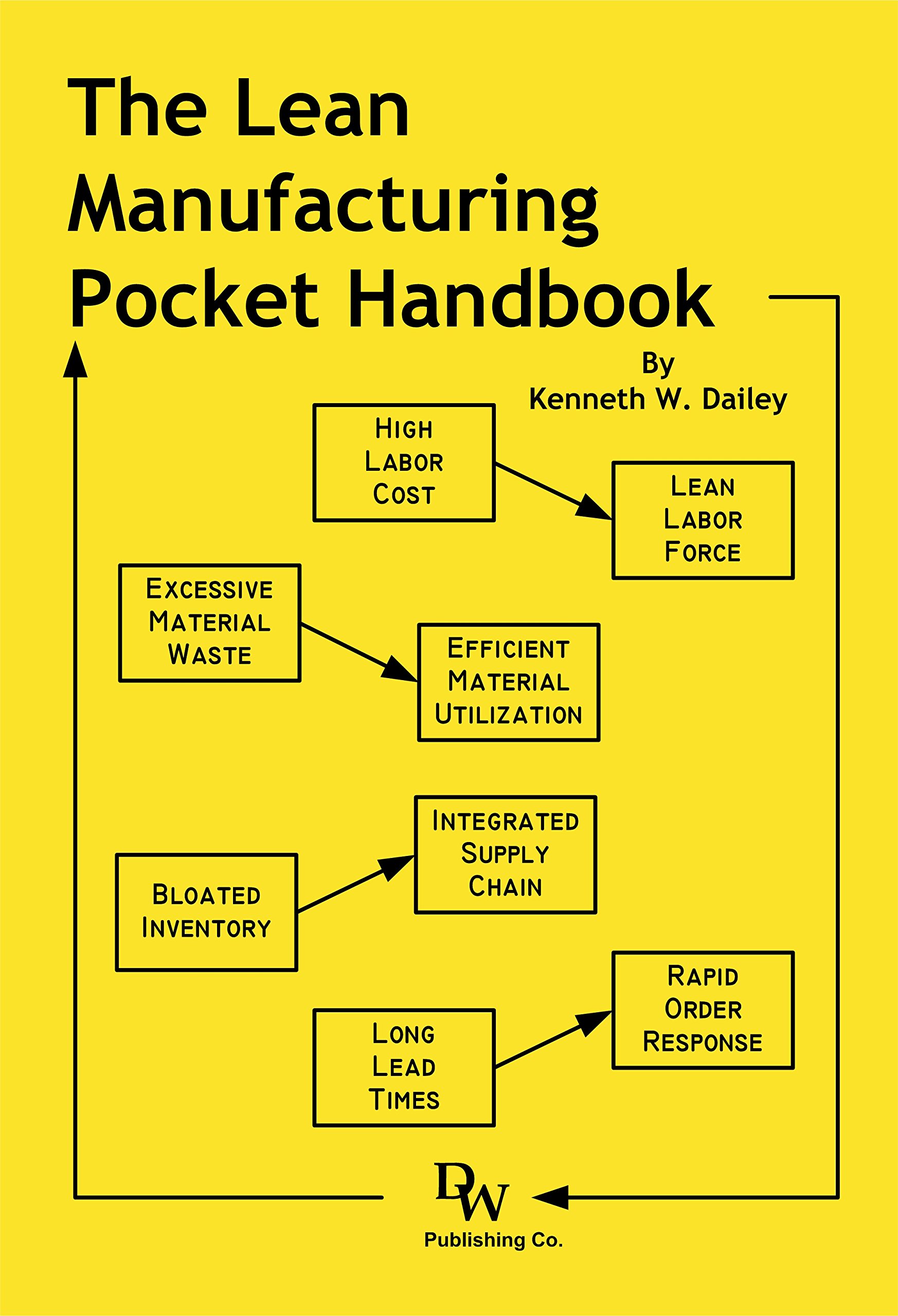
ILOG's PowerOps Suite, for example, integrates manufacturing scheduling functions. Dynasys, QAD, and Dynasys also offer applications that help organizations create a demand- and supply plan. These applications can help organizations visualize the impact of changes on their supply chains. Optiant offers ERP solutions for organizations that help them develop efficient, consistent order management and supply chain processes.
Similarly, tools like CDC Software, Terra Technology and Real-Time Inventory offer real-time forecasting solutions that can reduce the number of supply chain disruptions. The collaborative management strategy allows companies to share information and other resources. It also includes performance indicators, knowledge sharing and joint planning.
A few key factors should be considered before you decide to implement a strategy for demand management. These factors can help professionals better understand the process and focus on the most important aspects.
Leadership buy-in is a critical factor in demand management. This is because demand management is a highly collaborative process that involves various levels of management. High-ranking executives and managers are responsible in ensuring everyone is on the right page. Those at lower levels are also important to the success of the initiative.
While there are many applications that can help organizations implement a demand and supply plan, some of the key aspects to remember include:
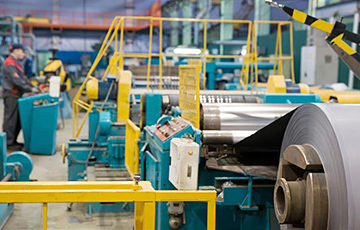
It is crucial to understand the market and identify the ideal customer. In addition to knowing who to target, the organization should be able to effectively measure and analyze the results of its efforts.
Businesses must devise a demand management strategy that is flexible enough to adjust to changes in order to remain agile. A well-designed plan will reduce supply chain disruptions and tactical forecast errors. Last but not least, demand management is an important tool for helping to create and implement portfolios and strategic plans.
FAQ
How does a Production Planner differ from a Project Manager?
The main difference between a production planner and a project manager is that a project manager is usually the person who plans and organizes the entire project, whereas a production planner is mainly involved in the planning stage of the project.
What is the difference in Production Planning and Scheduling, you ask?
Production Planning (PP), is the process of deciding what production needs to take place at any given time. Forecasting and identifying production capacity are two key elements to this process.
Scheduling refers the process by which tasks are assigned dates so that they can all be completed within the given timeframe.
What is the role and responsibility of a Production Planner?
A production planner ensures all aspects of the project are delivered on time, within budget, and within scope. They also ensure that the product/service meets the client’s needs.
What do we need to know about Manufacturing Processes in order to learn more about Logistics?
No. No. Knowing about manufacturing processes will help you understand how logistics works.
Statistics
- In the United States, for example, manufacturing makes up 15% of the economic output. (twi-global.com)
- In 2021, an estimated 12.1 million Americans work in the manufacturing sector.6 (investopedia.com)
- You can multiply the result by 100 to get the total percent of monthly overhead. (investopedia.com)
- [54][55] These are the top 50 countries by the total value of manufacturing output in US dollars for its noted year according to World Bank.[56] (en.wikipedia.org)
- Job #1 is delivering the ordered product according to specifications: color, size, brand, and quantity. (netsuite.com)
External Links
How To
How to Use 5S for Increasing Productivity in Manufacturing
5S stands as "Sort", Set In Order", Standardize", Separate" and "Store". Toyota Motor Corporation invented the 5S strategy in 1954. It assists companies in improving their work environments and achieving higher efficiency.
This method aims to standardize production processes so that they are repeatable, measurable and predictable. This means that daily tasks such as cleaning and sorting, storage, packing, labeling, and packaging are possible. Through these actions, workers can perform their jobs more efficiently because they know what to expect from them.
There are five steps to implementing 5S, including Sort, Set In Order, Standardize, Separate and Store. Each step requires a different action, which increases efficiency. By sorting, for example, you make it easy to find the items later. When items are ordered, they are put together. Once you have separated your inventory into groups and organized them, you will store these groups in easily accessible containers. Finally, label all containers correctly.
Employees must be able to critically examine their work practices. Employees need to understand the reasons they do certain jobs and determine if there is a better way. To be successful in the 5S system, employees will need to acquire new skills and techniques.
In addition to increasing efficiency, the 5S method also improves morale and teamwork among employees. They will feel motivated to strive for higher levels of efficiency once they start to see results.