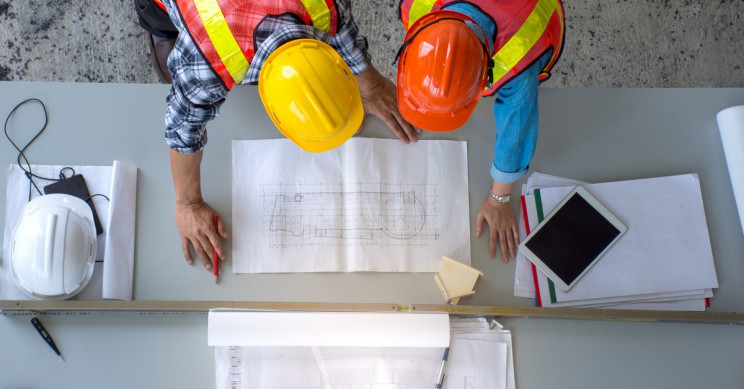
Are you looking for a job in Walmart asset security? Learn more about the salary and safety procedures associated with these positions. You are sure that Walmart is the right place to work, so apply today. Here are details about the Walmart Asset Protection Associate Salary Range and Compensation. Safety procedures can also be found. Find out more about this position. Online applications are available for more information. An account is required to get started.
Walmart asset protection associates can expect a range of salaries
The average salary for a Walmart Asset Protection Associate is between Rs 1.8 Lakhs and Rs 2.2 Lakhs per year. This is based on statistical methods and actual salaries of 6 employees working at the company. To learn more about this job, please review the following information. The salary estimates are based upon 6 anonymous salaries submitted to Glassdoor.com by Asset Protection Associates. This information does not include overtime or bonuses.
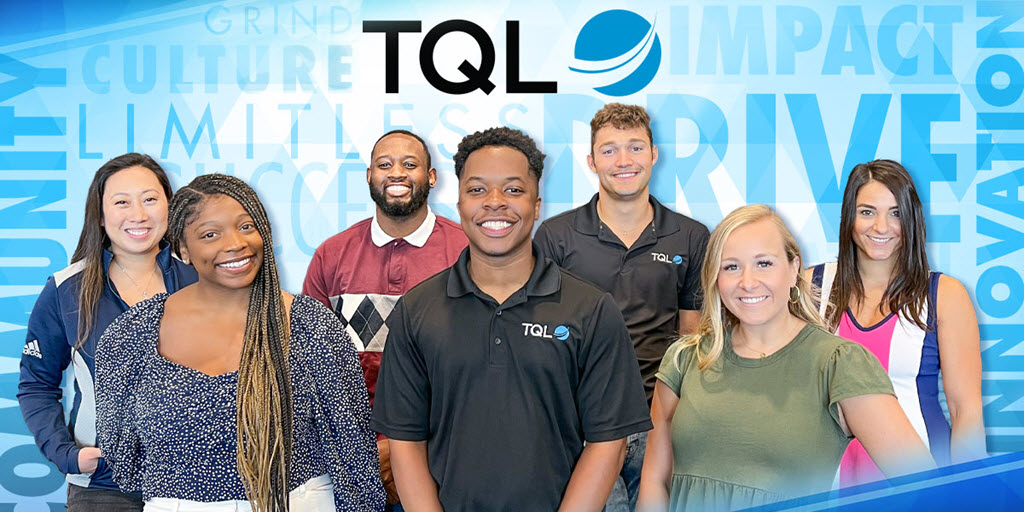
This job is a great match for people with criminal justice and retail loss prevention backgrounds. Walmart offers many career opportunities and salary ranges to asset protection associates. Walmart Careers allows interested applicants to access job descriptions and learn about the job responsibilities. To apply, simply sign the disclosures and create a profile. If you're applying for an AP Manager position, then you can fill out a job application and upload a resume.
Safety procedures
As one of the largest and most diversified retailers in the world, Walmart has a variety of safety and security concerns. The following are the safety procedures and top priorities of Walmart's Asset Protection program. Mike Lamb, vice president of Walmart US's asset protection and safety department, explains how these policies help protect Walmart's assets, while addressing the most common problems and opportunities. This program allows associates to protect company assets and keep customers and associates protected.
Associate: Walmart Asset Protection program associates work as the frontline for crime prevention. This includes helping store managers and employees protect their stores from theft and fraud. Although entry-level positions are not required, managers must possess a Bachelor’s degree or Loss Prevention Qualified Certificate. Entry-level positions do not require a Loss Prevention Qualified Certificate, but a degree in criminal law or a Loss Prevention Qualified Certificate can be very beneficial.
Compensation
Based on 974 workers with this job title, the average Walmart Asset Protection compensation amount is $33,000 per annum. This figure includes tips, taxes, bonuses, and wages. It can vary depending upon education and experience. This information is anonymous and does not reflect the actual salary of Walmart Asset Protection employees. It is a good starting point to determine the salary you are entitled to.
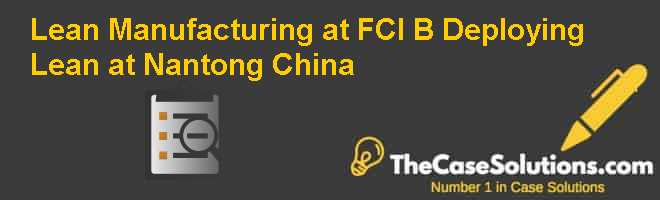
Wal-Mart keeps giving bonuses to store manager that are tied to store performances, despite all this. Walmart also acknowledges that longer-term employees are likely to be given raises than those who only started. Associate with years of experience may request raises one or two times per year. The hourly rate is between $12 and $16. The following table lists the typical Walmart Ap customer host salary. For more information, visit the official Walmart site.
FAQ
How can we improve manufacturing efficiency?
First, determine which factors have the greatest impact on production time. The next step is to identify the most important factors that affect production time. If you aren't sure where to begin, think about the factors that have the greatest impact on production time. Once you identify them, look for solutions.
What is the role and responsibility of a Production Planner?
Production planners ensure that all project aspects are completed on time, within budget and within the scope. They make sure that the product and services meet client expectations.
Why automate your warehouse?
Modern warehouses are increasingly dependent on automation. The rise of e-commerce has led to increased demand for faster delivery times and more efficient processes.
Warehouses must be able to quickly adapt to changing demands. To do so, they must invest heavily in technology. Automating warehouses is a great way to save money. Here are some of the reasons automation is worth your investment:
-
Increases throughput/productivity
-
Reduces errors
-
Increases accuracy
-
Safety is boosted
-
Eliminates bottlenecks
-
This allows companies to scale easily
-
This makes workers more productive
-
The warehouse can be viewed from all angles.
-
Enhances customer experience
-
Improves employee satisfaction
-
Minimizes downtime and increases uptime
-
High quality products delivered on-time
-
Removing human error
-
This helps to ensure compliance with regulations
What skills does a production planner need?
You must be flexible and organized to become a productive production planner. Also, you must be able and willing to communicate with clients and coworkers.
What are the 7 Rs of logistics?
The 7R's of Logistics is an acronym for the seven basic principles of logistics management. It was developed by International Association of Business Logisticians (IABL), and published as part of their "Seven Principles of Logistics Management Series" in 2004.
The following letters make up the acronym:
-
Responsible - to ensure that all actions are within the legal requirements and are not detrimental to others.
-
Reliable - Have confidence in your ability to fulfill all of your commitments.
-
Use resources effectively and sparingly.
-
Realistic – consider all aspects of operations, from cost-effectiveness to environmental impact.
-
Respectful - Treat people fairly and equitably
-
Be resourceful: Look for opportunities to save money or increase productivity.
-
Recognizable: Provide customers with value-added service
What is the distinction between Production Planning or Scheduling?
Production Planning (PP), is the process of deciding what production needs to take place at any given time. This is done through forecasting demand and identifying production capacities.
Scheduling is the process of assigning specific dates to tasks so they can be completed within the specified timeframe.
Statistics
- According to the United Nations Industrial Development Organization (UNIDO), China is the top manufacturer worldwide by 2019 output, producing 28.7% of the total global manufacturing output, followed by the United States, Japan, Germany, and India.[52][53] (en.wikipedia.org)
- According to a Statista study, U.S. businesses spent $1.63 trillion on logistics in 2019, moving goods from origin to end user through various supply chain network segments. (netsuite.com)
- In 2021, an estimated 12.1 million Americans work in the manufacturing sector.6 (investopedia.com)
- You can multiply the result by 100 to get the total percent of monthly overhead. (investopedia.com)
- Job #1 is delivering the ordered product according to specifications: color, size, brand, and quantity. (netsuite.com)
External Links
How To
How to Use Lean Manufacturing in the Production of Goods
Lean manufacturing (or lean manufacturing) is a style of management that aims to increase efficiency, reduce waste and improve performance through continuous improvement. It was developed in Japan between 1970 and 1980 by Taiichi Ohno. TPS founder Kanji Tyoda gave him the Toyota Production System, or TPS award. Michael L. Watkins published the "The Machine That Changed the World", the first book about lean manufacturing. It was published in 1990.
Lean manufacturing is often defined as a set of principles used to improve the quality, speed, and cost of products and services. It emphasizes eliminating waste and defects throughout the value stream. Lean manufacturing is also known as just in time (JIT), zero defect total productive maintenance(TPM), and five-star (S). Lean manufacturing emphasizes reducing non-value-added activities like inspection, rework and waiting.
Lean manufacturing can help companies improve their product quality and reduce costs. Additionally, it helps them achieve their goals more quickly and reduces employee turnover. Lean manufacturing can be used to manage all aspects of the value chain. Customers, suppliers, distributors, retailers and employees are all included. Many industries worldwide use lean manufacturing. Toyota's philosophy is the foundation of its success in automotives, electronics and appliances, healthcare, chemical engineers, aerospace, paper and food, among other industries.
Lean manufacturing includes five basic principles:
-
Define Value - Identify the value your business adds to society and what makes you different from competitors.
-
Reduce Waste – Eliminate all activities that don't add value throughout the supply chain.
-
Create Flow - Make sure work runs smoothly without interruptions.
-
Standardize & simplify - Make processes consistent and repeatable.
-
Building Relationships – Establish personal relationships with both external and internal stakeholders.
Lean manufacturing is not a new concept, but it has been gaining popularity over the last few years due to a renewed interest in the economy following the global financial crisis of 2008. Many businesses have adopted lean manufacturing techniques to help them become more competitive. In fact, some economists believe that lean manufacturing will be an important factor in economic recovery.
Lean manufacturing is becoming a popular practice in automotive. It has many advantages. These include higher customer satisfaction, lower inventory levels, lower operating expenses, greater productivity, and improved overall safety.
You can apply Lean Manufacturing to virtually any aspect of your organization. Because it makes sure that all value chains are efficient and effectively managed, Lean Manufacturing is particularly helpful for organizations.
There are three types principally of lean manufacturing:
-
Just-in-Time Manufacturing (JIT): This type of lean manufacturing is commonly referred to as "pull systems." JIT is a method in which components are assembled right at the moment of use, rather than being manufactured ahead of time. This method reduces lead times, increases availability, and decreases inventory.
-
Zero Defects Manufacturing - ZDM: ZDM focuses its efforts on making sure that no defective units leave a manufacturing facility. If a part is required to be repaired on the assembly line, it should not be scrapped. This is true even for finished products that only require minor repairs prior to shipping.
-
Continuous Improvement (CI),: Continuous improvement aims improve the efficiency and effectiveness of operations by continuously identifying issues and making changes to reduce waste. Continuous improvement involves continuous improvement of processes and people as well as tools.