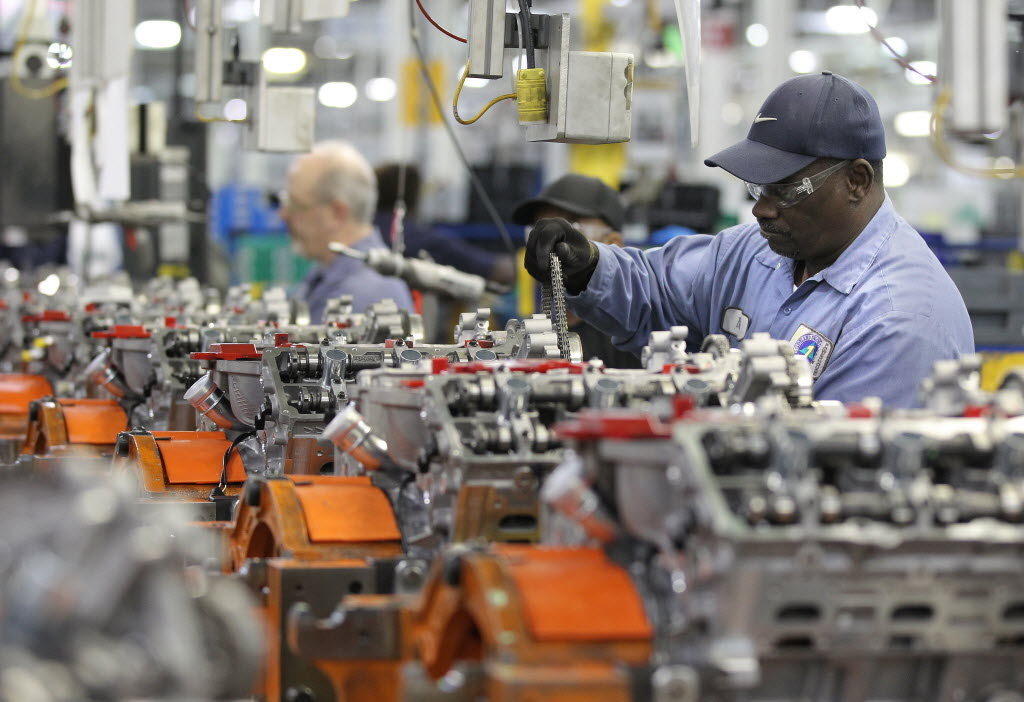
The United States is third in manufacturing in the world and saw its manufacturing output reach a record at $2.00 trillion in Q1 2018. This was nearly twice the amount it had before the Great Recession. Despite having a strong national economy, the United States’ manufacturing industry is taking a very aggressive approach to its current challenges. We need to be more aggressive in addressing the industry's challenges, regardless of whether this is due to a lack or skilled labor.
Jobs have declined by 5 million since 2000
Five million US manufacturing jobs were lost between 2000 and now. Although some believe that trade with China has contributed to the decrease in manufacturing jobs, this accounts for only a quarter of the total decline. Trade with China was not the only reason for manufacturing jobs being lost. Local markets were also affected by Chinese imports. But the reasons for the decline in manufacturing jobs are many. Here are some of these reasons:
In the last 20 years, nearly a quarter of the jobs in the US manufacturing industry have been lost. It was 17 million people in 1965. In 2010, it was only 12 million. While the decline in manufacturing jobs is not the fault of trade, it has been the result of structural problems - a decline in capital investment, output, productivity, and trade deficits - which are not sustainable. While productivity increases played a major part in the decline, these were not enough for the replacement of lost manufacturing jobs. The problem is not productivity gains but automation.
Strong demand is for manufactured products
The United States has a strong demand for manufactured products despite the fact that consumer spending on these goods has fallen over the past several decades. In 1945, personal expenditures on durable goods accounted for 58% of total spending, compared to just 28% today. This is because both the manufacturing cost and the sale price have declined, but the content has increased. Computers, televisions, sound equipment, and other electronic devices have seen significant drops in their prices.
The US's recovery in manufacturing activity has resulted in an increase in the production of manufactured goods. The Fifth District Manufacturing Activity Survey shows that demand for manufactured goods is strong and production is ramping up, although supply chain bottlenecks are hampering output. The increased production has put stress on supply chains, and respondents have reported supply chain disruptions that affect their ability to maintain necessary inventories. The backlog of orders has increased, as well as the lead time for vendors.
Over the past decade, the trade deficit for manufactured goods has more then doubled
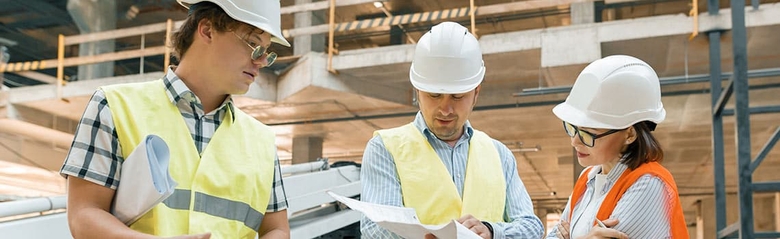
Some economists fear that the U.S.'s trade surplus may lead to lower global economic growth and greater instability among its trading partner. Others point out that high imports of US manufactured goods are not necessarily a bad thing for the U.S. economy, which is a key to maintaining global economic stability. The trade deficit may even be a necessary evil, since the U.S. relies heavily on foreign markets to generate its economic output, while high levels of foreign demand may make it difficult to achieve full employment.
Since 2000, the U.S. has almost doubled its trade deficit for manufactured goods. Partly, this is due to an increase in Chinese imports. The bigger problem is that the imbalance is concentrated within the manufacturing sector where wages and employment have declined since the 1990s. US manufacturing employment has declined dramatically, from 26 percent in 1970 down to 8.5 percent in 2016. Some economists attribute China's increasing competition to the decline, but most blame the decline on automation, productivity increases and the shifting of consumer demand away form goods to services.
The shotgun approach of industry is the best.
The US manufacturing sector is well-known for its many advanced manufacturing initiatives. Some countries, however, are taking a more focused approach to bringing the internet into manufacturing. The US, by contrast, focuses on multiple technologies and mixes traditional mass media and Internet advertising. The result is a shotgun approach. Companies focus on many technologies and target a broad client base.
FAQ
Why is logistics important for manufacturing?
Logistics is an integral part of every business. They are essential to any business's success.
Logistics plays a significant role in reducing cost and increasing efficiency.
What skills do production planners need?
Being a production planner is not easy. You need to be organized and flexible. Communication skills are essential to ensure that you can communicate effectively with clients, colleagues, and customers.
What do we need to know about Manufacturing Processes in order to learn more about Logistics?
No. You don't have to know about manufacturing processes before learning about logistics. Knowing about manufacturing processes will help you understand how logistics works.
What is the role of a logistics manager
A logistics manager makes sure that all goods are delivered on-time and in good condition. This is achieved by using their knowledge and experience with the products of the company. He/she must also ensure sufficient stock to meet the demand.
Statistics
- In 2021, an estimated 12.1 million Americans work in the manufacturing sector.6 (investopedia.com)
- In the United States, for example, manufacturing makes up 15% of the economic output. (twi-global.com)
- According to a Statista study, U.S. businesses spent $1.63 trillion on logistics in 2019, moving goods from origin to end user through various supply chain network segments. (netsuite.com)
- (2:04) MTO is a production technique wherein products are customized according to customer specifications, and production only starts after an order is received. (oracle.com)
- It's estimated that 10.8% of the U.S. GDP in 2020 was contributed to manufacturing. (investopedia.com)
External Links
How To
Six Sigma and Manufacturing
Six Sigma refers to "the application and control of statistical processes (SPC) techniques in order to achieve continuous improvement." It was developed by Motorola's Quality Improvement Department at their plant in Tokyo, Japan, in 1986. Six Sigma's basic concept is to improve quality and eliminate defects through standardization. In recent years, many companies have adopted this method because they believe there is no such thing as perfect products or services. Six Sigma's primary goal is to reduce variation from the average value of production. If you take a sample and compare it with the average, you will be able to determine how much of the production process is different from the norm. If the deviation is excessive, it's likely that something needs to be fixed.
Understanding how your business' variability is a key step towards Six Sigma implementation is the first. Once you understand that, it is time to identify the sources of variation. Also, you will need to identify the sources of variation. Random variations happen when people make errors; systematic variations are caused externally. If you make widgets and some of them end up on the assembly line, then those are considered random variations. It would be considered a systematic problem if every widget that you build falls apart at the same location each time.
Once you have identified the problem, you can design solutions. You might need to change the way you work or completely redesign the process. Once you have implemented the changes, it is important to test them again to ensure they work. If they fail, you can go back to the drawing board to come up with a different plan.