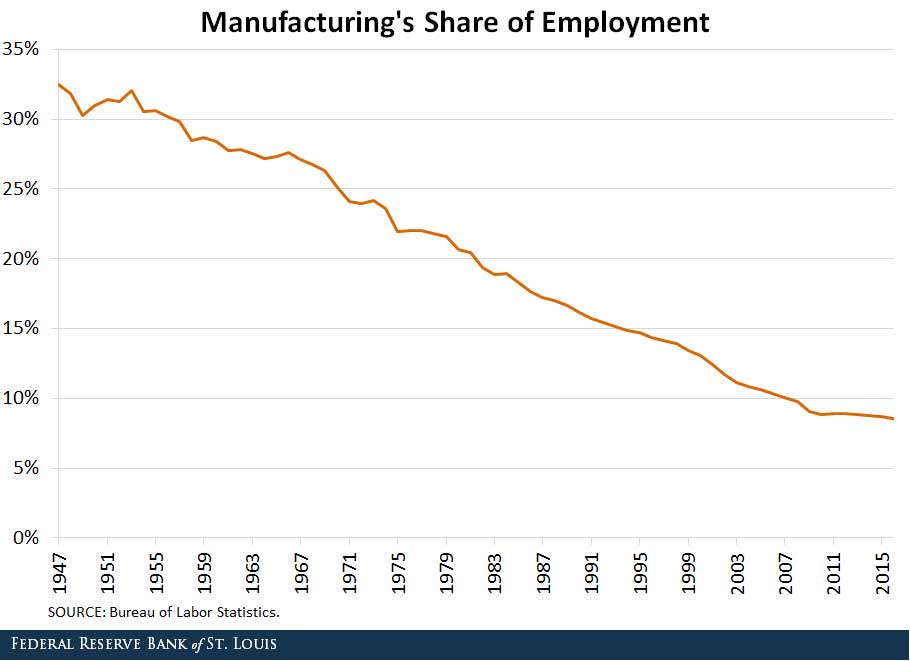
Founded in 1898, the National Association of Manufacturers (NAM) is a trade association that represents nearly 14,000 member companies from every industrial sector in the U.S. NAM works to ensure the success of 12 million American manufacturers. It promotes new and innovative industries, as well as increasing awareness of manufacturing. NAM has offices throughout the United States.
NAM, the nation's most influential advocate of manufacturers, is the best. Its members are small and medium-sized manufacturing businesses. It supports advanced manufacturing and new industries. NAM plays an important part in Washington policymaking. Its executives aim to reduce regulation and support trade, export and investment. Washington, D.C., houses the headquarters for NAM. The organization's executives are skilled at researching and developing products and services that enhance the competitiveness of manufacturers.
Texas Association of Manufacturers (TAM), praised the 84th Legislature's passing of SB 1. The legislation will allow Texas businesses to grow through broad tax relief. Senator Bill Nelson and Representative Bill Bonnen sponsored the bill. The legislation also addresses state's tax code, Chapter 312, that allows temporary tax exclusions.
Texas' aerospace and aviation manufacturing sector makes up a significant part of its economy. It generates nearly 49 billion dollars of economic activity and provides 200,000 jobs. The industry must remain competitive to maintain its strong position in the state. To ensure that the sector is competitive and grows, reforms to TSCA are essential. AMT's USMTO Program provides support to members companies in Brazil to set up operations. Its USMTO Program reported over $400 million in manufacturing orders during May.
The Texas aerospace and aircraft manufacturing sector needs to remain competitive in order to continue to generate revenue and create jobs in Texas. The sector has made significant efforts to boost the state's manufacturing industry.
Texas Association of Manufacturers support the renewal of Chapter 312 of Texas Tax Code. The Association supports payments made under the Operating Reserve Demand Curve. These payments are used to help manufacturers pay dispatchable generation. This payment is crucial for protecting the grid's security. The ORDC payments increased after Winter Storm Uri. This was due to changes to the "phase one” operations of Public Utility Commission.
AMT is one the most prominent trade organizations in the country. It has offices in more than 30 cities across the United States. Its executives are experienced in both business and public policy. Its mission promotes advanced manufacturing and technology. It supports regulatory convergence between the U.S. and the European Union. It promotes and protects manufacturers from every industry sector. It has developed several industry-specific committees, including one for small and medium-sized manufacturers. It promotes innovation and technology.
AMT's new video presents "MT Ambassadors", young professionals who are dedicated to educating others about the manufacturing industry. The USMTO program helps members companies travel to Brazil, and AMT promotes it. Its Top Shops conference and Top Shops programs help manufacturers benchmark their businesses and identify opportunities. To promote interoperability in manufacturing systems, the association works with the Association for Manufacturing Technology. Its MTConnect Program improves the ability for manufacturers to gather and transmit data across all manufacturing technologies.
FAQ
What are the 4 types of manufacturing?
Manufacturing is the process of transforming raw materials into useful products using machines and processes. It includes many different activities like designing, building and testing, packaging, shipping and selling, as well as servicing.
Can we automate some parts of manufacturing?
Yes! Automation has been around since ancient times. The wheel was invented by the Egyptians thousands of years ago. Nowadays, we use robots for assembly lines.
Actually, robotics can be used in manufacturing for many purposes. These include:
-
Automated assembly line robots
-
Robot welding
-
Robot painting
-
Robotics inspection
-
Robots that create products
There are many other examples of how manufacturing could benefit from automation. 3D printing is a way to make custom products quickly and without waiting weeks or months for them to be manufactured.
How can manufacturing efficiency improved?
First, determine which factors have the greatest impact on production time. Next, we must find ways to improve those factors. If you don't know where to start, then think about which factor(s) have the biggest impact on production time. Once you have identified the factors, then try to find solutions.
What's the difference between Production Planning & Scheduling?
Production Planning (PP), also known as forecasting and identifying production capacities, is the process that determines what product needs to be produced at any particular time. Forecasting and identifying production capacity are two key elements to this process.
Scheduling refers to the process of allocating specific dates to tasks in order that they can be completed within a specified timeframe.
What are the products of logistics?
Logistics refers to the movement of goods from one place to another.
They cover all aspects of transportation, such as packing, loading, transporting and unloading.
Logisticians make sure that the right product arrives at the right place at the correct time and in safe conditions. Logisticians help companies improve their supply chain efficiency by providing information about demand forecasts and stock levels, production schedules, as well as availability of raw materials.
They coordinate with vendors and suppliers, keep track of shipments, monitor quality standards and perform inventory and order replenishment.
What are the 7 Rs of logistics management?
The 7R's of Logistics is an acronym for the seven basic principles of logistics management. It was published in 2004 by the International Association of Business Logisticians as part of their "Seven Principles of Logistics Management" series.
The acronym is composed of the following letters.
-
Responsible - to ensure that all actions are within the legal requirements and are not detrimental to others.
-
Reliable - have confidence in the ability to deliver on commitments made.
-
Use resources effectively and sparingly.
-
Realistic - Take into consideration all aspects of operations including cost-effectiveness, environmental impact, and other factors.
-
Respectful - show respect and treat others fairly and fairly
-
Responsive - Look for ways to save time and increase productivity.
-
Recognizable is a company that provides customers with value-added solutions.
How can we reduce manufacturing overproduction?
Improved inventory management is the key to reducing overproduction. This would decrease the time that is spent on inefficient activities like purchasing, storing, or maintaining excess stock. This could help us free up our time for other productive tasks.
You can do this by adopting a Kanban method. A Kanban Board is a visual display that tracks work progress. Kanban systems allow work items to move through different states until they reach their final destination. Each state represents a different priority.
To illustrate, work can move from one stage or another when it is complete enough for it to be moved to a new stage. A task that is still in the initial stages of a process will be considered complete until it moves on to the next stage.
This allows work to move forward and ensures that no work is missed. Managers can view the Kanban board to see how much work they have done. This data allows them adjust their workflow based upon real-time data.
Lean manufacturing, another method to control inventory levels, is also an option. Lean manufacturing focuses on eliminating waste throughout the entire production chain. Anything that does not contribute to the product's value is considered waste. These are some of the most common types.
-
Overproduction
-
Inventory
-
Unnecessary packaging
-
Materials in excess
Manufacturers can increase efficiency and decrease costs by implementing these ideas.
Statistics
- Many factories witnessed a 30% increase in output due to the shift to electric motors. (en.wikipedia.org)
- You can multiply the result by 100 to get the total percent of monthly overhead. (investopedia.com)
- In the United States, for example, manufacturing makes up 15% of the economic output. (twi-global.com)
- [54][55] These are the top 50 countries by the total value of manufacturing output in US dollars for its noted year according to World Bank.[56] (en.wikipedia.org)
- It's estimated that 10.8% of the U.S. GDP in 2020 was contributed to manufacturing. (investopedia.com)
External Links
How To
How to Use Lean Manufacturing in the Production of Goods
Lean manufacturing refers to a method of managing that seeks to improve efficiency and decrease waste. It was first developed in Japan in the 1970s/80s by Taiichi Ahno, who was awarded the Toyota Production System (TPS), award from KanjiToyoda, the founder of TPS. Michael L. Watkins published the book "The Machine That Changed the World", which was the first to be published about lean manufacturing.
Lean manufacturing can be described as a set or principles that are used to improve quality, speed and cost of products or services. It is about eliminating defects and waste from all stages of the value stream. The five-steps of Lean Manufacturing are just-in time (JIT), zero defect and total productive maintenance (TPM), as well as 5S. Lean manufacturing is about eliminating activities that do not add value, such as inspection, rework, and waiting.
Lean manufacturing is a way for companies to achieve their goals faster, improve product quality, and lower costs. Lean manufacturing can be used to manage all aspects of the value chain. Customers, suppliers, distributors, retailers and employees are all included. Lean manufacturing is widely practiced in many industries around the world. Toyota's philosophy is the foundation of its success in automotives, electronics and appliances, healthcare, chemical engineers, aerospace, paper and food, among other industries.
Five fundamental principles underlie lean manufacturing.
-
Define Value - Identify the value your business adds to society and what makes you different from competitors.
-
Reduce Waste - Remove any activity which doesn't add value to your supply chain.
-
Create Flow - Make sure work runs smoothly without interruptions.
-
Standardize and Simplify – Make processes as consistent, repeatable, and as simple as possible.
-
Building Relationships – Establish personal relationships with both external and internal stakeholders.
Although lean manufacturing isn't a new concept in business, it has gained popularity due to renewed interest in the economy after the 2008 global financial crisis. To increase their competitiveness, many businesses have turned to lean manufacturing. According to some economists, lean manufacturing could be a significant factor in the economic recovery.
With many benefits, lean manufacturing is becoming more common in the automotive industry. These include higher customer satisfaction, lower inventory levels, lower operating expenses, greater productivity, and improved overall safety.
It can be applied to any aspect of an organisation. However, it is particularly useful when applied to the production side of an organization because it ensures that all steps in the value chain are efficient and effective.
There are three main types:
-
Just-in Time Manufacturing (JIT), also known as "pull system": This form of lean manufacturing is often referred to simply as "pull". JIT stands for a system where components are assembled on the spot rather than being made in advance. This approach reduces lead time, increases availability and reduces inventory.
-
Zero Defects Manufacturing (ZDM): ZDM focuses on ensuring that no defective units leave the manufacturing facility. Repairing a part that is damaged during assembly should be done, not scrapping. This is also true for finished products that require minor repairs before shipping.
-
Continuous Improvement (CI),: Continuous improvement aims improve the efficiency and effectiveness of operations by continuously identifying issues and making changes to reduce waste. Continuous improvement refers to continuous improvement of processes as well people and tools.