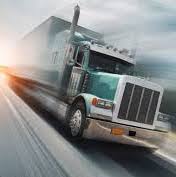
Integrated supply chain management is a process which allows companies monitor and optimize the performance their supply chain. It results in a more responsive and efficient production network. Your supply chain will be more efficient the more it is streamlined and responsive. Integrated supply chain management can increase profits and reduce waste. This means that your products will be of better quality, more reliable, and less costly to produce.
Integrated supply chain management can improve your order reliability. Your production schedule will be easier to manage, inventory levels will be more accurate and delivery times will be more flexible. Integrated supply chains are also better at managing risk. It can also reduce greenhouse gas emissions. This helps you to meet environmental goals.
First, you need to create a contract for integration with your vendors. These agreements should be tailored for your company's specific needs. It should include information about your production schedule, the materials you require, and the costs involved. It should also include information about your production schedule, the materials you require, and how they will benefit your company. Purchasing a larger volume of goods or services can also lead to cheaper prices.
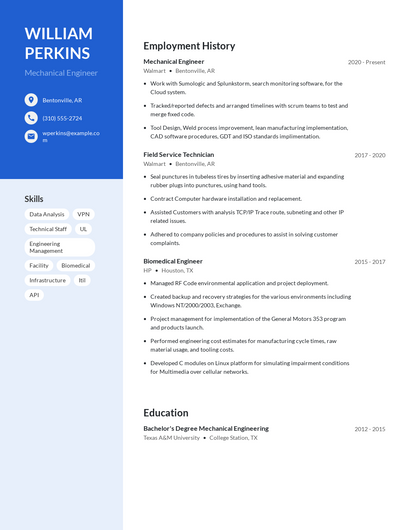
Having a solid understanding of your connections, and how they affect your business, is an important component of integrated supply chain management. This helps identify areas for improvement and to avoid making mistakes. It is important to have a comprehensive, end-toend plan that meets your needs. This plan should be flexible enough for any production differences. This will help avoid delays.
Just-in time distribution is an example of an integrated supply system. This strategy helps to decrease operational costs and reduce warehouse space requirements. This strategy can also be used to forecast accurately. A well-designed integrated supply chain can also help reduce greenhouse gas emissions. Reduce your use of large, fixed assets to achieve this.
Vertical integration means that all necessary elements are present for a particular product. This could be a manufacturer or vendor. This could provide a manufacturer with a greater share in profits. A widget manufacturer or firm that produces widgets might be a good option. This can give you the ability to manage your competitors and guarantee that you are offering a fair price for widgets.
A container management strategy is another example of integrated supply chain. This allows you view your inventory and make adjustments to container pull strategies as required. You can also make changes to the production schedule right away.
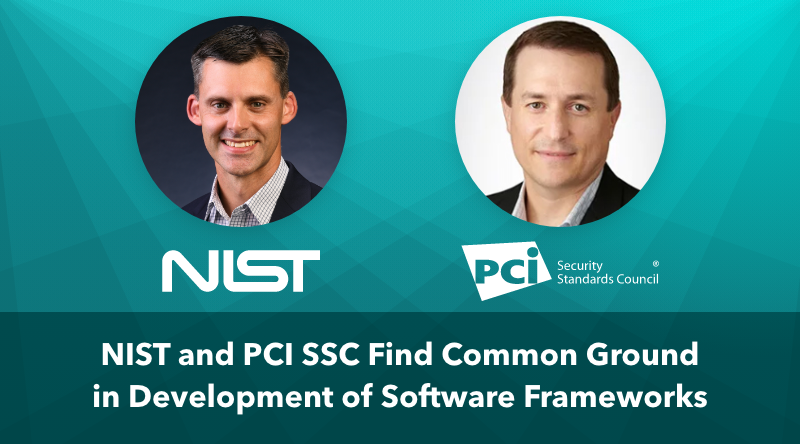
A supply chain management system that has clear goals is more effective. Integrated supply chains aim to improve performance and provide customers with the best possible products. An integrated supply system can help reduce the amount plastic and other waste that is produced during the manufacturing process. This can help increase your profit margins and decrease your greenhouse gas emission.
FAQ
How can manufacturing prevent production bottlenecks?
The key to avoiding bottlenecks in production is to keep all processes running smoothly throughout the entire production cycle, from the time you receive an order until the time when the product ships.
This includes planning to meet capacity requirements and quality control.
Continuous improvement techniques such Six Sigma can help you achieve this.
Six Sigma management is a system that improves quality and reduces waste within your organization.
It focuses on eliminating variation and creating consistency in your work.
What does warehouse refer to?
A warehouse, or storage facility, is where goods are stored prior to being sold. It can be an outdoor or indoor area. In some cases it could be both indoors and outdoors.
Can we automate some parts of manufacturing?
Yes! Yes. The wheel was invented by the Egyptians thousands of years ago. To help us build assembly lines, we now have robots.
Actually, robotics can be used in manufacturing for many purposes. These include:
-
Line robots
-
Robot welding
-
Robot painting
-
Robotics inspection
-
Robots create products
Manufacturing could also benefit from automation in other ways. 3D printing, for example, allows us to create custom products without waiting for them to be made.
What do we need to know about Manufacturing Processes in order to learn more about Logistics?
No. No. Knowing about manufacturing processes will help you understand how logistics works.
Statistics
- Many factories witnessed a 30% increase in output due to the shift to electric motors. (en.wikipedia.org)
- In the United States, for example, manufacturing makes up 15% of the economic output. (twi-global.com)
- According to the United Nations Industrial Development Organization (UNIDO), China is the top manufacturer worldwide by 2019 output, producing 28.7% of the total global manufacturing output, followed by the United States, Japan, Germany, and India.[52][53] (en.wikipedia.org)
- [54][55] These are the top 50 countries by the total value of manufacturing output in US dollars for its noted year according to World Bank.[56] (en.wikipedia.org)
- In 2021, an estimated 12.1 million Americans work in the manufacturing sector.6 (investopedia.com)
External Links
How To
How to Use Lean Manufacturing in the Production of Goods
Lean manufacturing refers to a method of managing that seeks to improve efficiency and decrease waste. It was developed in Japan between 1970 and 1980 by Taiichi Ohno. TPS founder Kanji Tyoda gave him the Toyota Production System, or TPS award. Michael L. Watkins published the "The Machine That Changed the World", the first book about lean manufacturing. It was published in 1990.
Lean manufacturing can be described as a set or principles that are used to improve quality, speed and cost of products or services. It emphasizes reducing defects and eliminating waste throughout the value chain. Lean manufacturing is called just-in-time (JIT), zero defect, total productive maintenance (TPM), or 5S. Lean manufacturing focuses on eliminating non-value-added activities such as rework, inspection, and waiting.
Lean manufacturing improves product quality and costs. It also helps companies reach their goals quicker and decreases employee turnover. Lean manufacturing is considered one of the most effective ways to manage the entire value chain, including suppliers, customers, distributors, retailers, and employees. Lean manufacturing can be found in many industries. Toyota's philosophy, for example, is what has enabled it to be successful in electronics, automobiles, medical devices, healthcare and chemical engineering as well as paper and food.
Lean manufacturing is based on five principles:
-
Define Value: Identify the social value of your business and what sets you apart.
-
Reduce waste - Get rid of any activity that does not add value to the supply chain.
-
Create Flow – Ensure that work flows smoothly throughout the process.
-
Standardize and simplify – Make processes as repeatable and consistent as possible.
-
Build Relationships - Establish personal relationships with both internal and external stakeholders.
Although lean manufacturing has always been around, it is gaining popularity in recent years because of a renewed interest for the economy after 2008's global financial crisis. Many businesses are now using lean manufacturing to improve their competitiveness. In fact, some economists believe that lean manufacturing will be an important factor in economic recovery.
Lean manufacturing is now becoming a common practice in the automotive industry, with many benefits. These include higher customer satisfaction, lower inventory levels, lower operating expenses, greater productivity, and improved overall safety.
Any aspect of an enterprise can benefit from Lean manufacturing. Lean manufacturing is most useful in the production sector of an organisation because it ensures that each step in the value-chain is efficient and productive.
There are three main types:
-
Just-in-Time Manufacturing (JIT): This type of lean manufacturing is commonly referred to as "pull systems." JIT stands for a system where components are assembled on the spot rather than being made in advance. This method reduces lead times, increases availability, and decreases inventory.
-
Zero Defects Manufacturing (ZDM): ZDM focuses on ensuring that no defective units leave the manufacturing facility. Repairing a part that is damaged during assembly should be done, not scrapping. This also applies to finished products that need minor repairs before being shipped.
-
Continuous Improvement (CI): CI aims to improve the efficiency of operations by continuously identifying problems and making changes in order to eliminate or minimize waste. Continuous improvement refers to continuous improvement of processes as well people and tools.