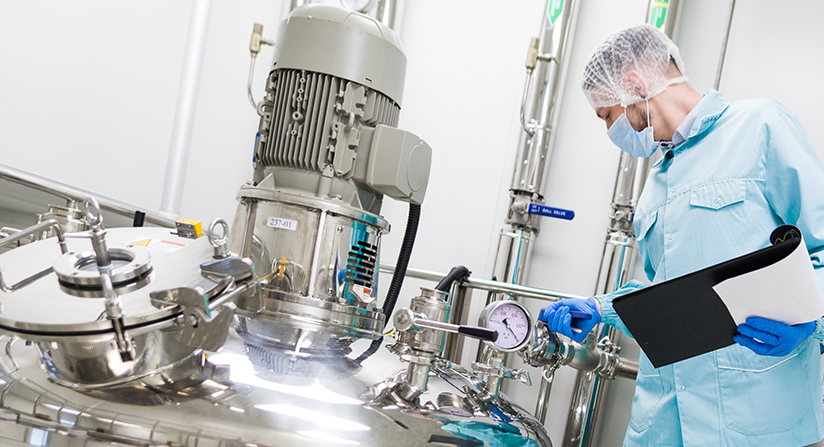
In lean manufacturing, an andon is a visible indicator that draws the attention of the user to specific problems in order to resolve them. It's a tool to empower plant floor operators, and speed up teamwork.
Andon (
) - a word of Japanese origin, it comes from the fixed paper-enclosed lanterns of the Edo period, namely the era between the 17th century and the 19th. In Japanese it can also refer to the system of attaching light signals and sounds to specific processes in order to alert employees.
Toyota uses the term "build-in" quality as a core principle of its Jidoka. It is a component in their TPS system (Toyota Production System). In the US it is often cited to be the basis of a business concept that allows workers on the production lines to stop the line if a quality or safety problem occurs.
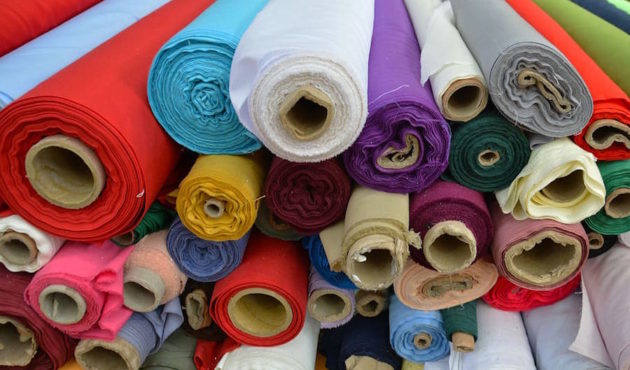
What is anon?
Toyota is the pioneer of Andon. It's a lean system for manufacturing. The system is very simple. It consists of a white board with green, orange and red lights. Each color indicates the different status of production. The green light indicates that the production line is operating normally. The yellow light means that the problem has been identified and is being dealt with. The production is stopped when the red light comes on. Workers can stop production, take a rest, go help, fill their bins or prepare parts.
Andon's board is simple to operate and supervisors understand exactly what has occurred. The system is designed to provide immediate feedback and ensure all problems are resolved as soon as possible.
Many types of adons are available, but the most popular is a bright red light combined with a loud sound or buzzer that alerts production teams. These signal alert and resolve systems help identify problems that might lead to downtime, or repeat issues.
When a problem occurs, a good andonboard can keep production running. It is a simple but effective tool which increases productivity and reduces downtime. It also improves the product quality and safety.
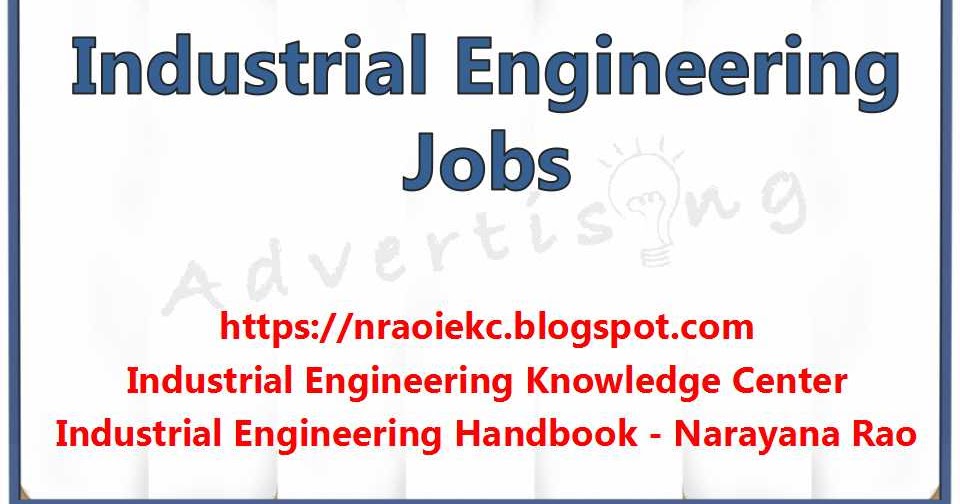
What is andon toyota?
Toyota has a special cord which any employee can pull when they see a possible issue with their car. By pulling the cord, a worker could stop the production of a car if the worker believed it was compromised.
Modern andon systems also use technology to curate information, which makes it easier to identify emerging problems, send notifications to stakeholders in real-time, and determine the root cause of a problem that requires a long term fix. Nevertheless, a human touch is required to interpret and act on this information.
How to make the andon system work?
To start with, it is crucial to create a culture where workers and managers don't hesitate to identify and address problems. The more they are hesitant, the more they're likely to conceal problems and miss a chance to fix them. It is best to link line stops and problem resolution to encourage workers to pull the cord or press the button when they notice something wrong.
FAQ
How can manufacturing efficiency improved?
The first step is to determine the key factors that impact production time. Next, we must find ways to improve those factors. If you don’t know how to start, look at which factors have the greatest impact upon production time. Once you identify them, look for solutions.
What skills does a production planner need?
You must be flexible and organized to become a productive production planner. It is also important to be able communicate with colleagues and clients.
Why should you automate your warehouse?
Automation has become increasingly important in modern warehousing. Increased demand for efficient and faster delivery has resulted in a rise in e-commerce.
Warehouses must be able to quickly adapt to changing demands. Technology investment is necessary to enable warehouses to respond quickly to changing demands. Automating warehouses is a great way to save money. Here are some benefits of investing in automation
-
Increases throughput/productivity
-
Reduces errors
-
Improves accuracy
-
Safety increases
-
Eliminates bottlenecks
-
Companies can scale more easily
-
Increases efficiency of workers
-
It gives visibility to everything that happens inside the warehouse
-
Enhances customer experience
-
Improves employee satisfaction
-
It reduces downtime, and increases uptime
-
Ensures quality products are delivered on time
-
Removes human error
-
It helps ensure compliance with regulations
What is the importance of logistics in manufacturing?
Logistics are an essential component of any business. They can help you achieve great success by helping you manage product flow from raw material to finished goods.
Logistics plays a significant role in reducing cost and increasing efficiency.
Can we automate some parts of manufacturing?
Yes! Automation has been around since ancient times. The Egyptians invent the wheel thousands of year ago. To help us build assembly lines, we now have robots.
There are many applications for robotics in manufacturing today. These include:
-
Line robots
-
Robot welding
-
Robot painting
-
Robotics inspection
-
Robots that produce products
Automation could also be used to improve manufacturing. 3D printing, for example, allows us to create custom products without waiting for them to be made.
What are the four types of manufacturing?
Manufacturing is the process by which raw materials are transformed into useful products through machines and processes. Manufacturing can include many activities such as designing and building, testing, packaging shipping, selling, servicing, and other related activities.
Statistics
- [54][55] These are the top 50 countries by the total value of manufacturing output in US dollars for its noted year according to World Bank.[56] (en.wikipedia.org)
- You can multiply the result by 100 to get the total percent of monthly overhead. (investopedia.com)
- (2:04) MTO is a production technique wherein products are customized according to customer specifications, and production only starts after an order is received. (oracle.com)
- It's estimated that 10.8% of the U.S. GDP in 2020 was contributed to manufacturing. (investopedia.com)
- Job #1 is delivering the ordered product according to specifications: color, size, brand, and quantity. (netsuite.com)
External Links
How To
How to use 5S to increase Productivity in Manufacturing
5S stands for "Sort", "Set In Order", "Standardize", "Separate" and "Store". The 5S methodology was developed at Toyota Motor Corporation in 1954. It helps companies achieve higher levels of efficiency by improving their work environment.
The basic idea behind this method is to standardize production processes, so they become repeatable, measurable, and predictable. This means that tasks such as cleaning, sorting, storing, packing, and labeling are performed daily. Because workers know what they can expect, this helps them perform their jobs more efficiently.
Five steps are required to implement 5S: Sort, Set In Order, Standardize. Separate. Each step is a different action that leads to greater efficiency. You can make it easy for people to find things later by sorting them. You arrange items by placing them in an order. Then, after you separate your inventory into groups, you store those groups in containers that are easy to access. Make sure everything is correctly labeled when you label your containers.
Employees will need to be more critical about their work. Employees need to be able understand their motivations and discover alternative ways to do them. They will need to develop new skills and techniques in order for the 5S system to be implemented.
The 5S Method not only improves efficiency, but it also helps employees to be more productive and happier. As they begin to see improvements, they feel motivated to continue working towards the goal of achieving higher levels of efficiency.