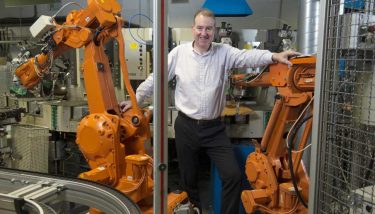
Denver in Colorado offers many different jobs. The city is also home several logistics firms that offer different logistics services. Some of these services include freight-forwarding, trucking, logistics and supply chain consultancy, as well.
There are several jobs you can apply for if you want to work in the industry of logistics. These include dispatch manager and transportation director. All of these positions have the responsibility of ensuring that logistics are run smoothly in an organization.
Dispatch Manager
A dispatch manager coordinates and directs the activities of an entire team in a warehouse, call center or other workplace. This includes training new employees, delegating tasks, coordinating the workload of other team members, documenting productivity, and overseeing incoming and outgoing shipments. Dispatch managers typically have a bachelor’s degree in business administration or logistics, and they are familiar with the organization of workflow.
Transportation Director
A transportation manager is responsible for logistics in a business, school or government department. This involves setting up distribution routes and arranging for transportation methods such as trucks or busses to transport products from one location to another.
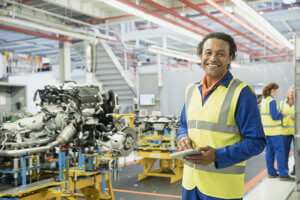
This career is best suited for those looking to join a larger organization or government. As this is a highly-competitive job, you will need excellent organizational skills as well as the willingness to work long shifts.
Warehouse Associate
If you are looking for a job that is not as competitive, but offers a more flexible schedule, consider a warehouse associate. A warehouse employee is usually responsible for small projects like picking shipments, packaging products and moving merchandise.
To begin your search, create a Monster.com profile. This will allow you to be notified about all of the relevant logistics jobs in your area.
In addition, you will be able to receive expert advice about how to make the most of your job application, how to negotiate your salary, and more.
Logistics Manager
If you are interested in becoming a logistic manager, then you need to have a Bachelor's Degree in Supply Chain Management or Business Administration. It is necessary to have a minimum of a year's professional experience in warehouse environments, and strong organization skills. You can also earn a master's degree in supply chain management or another related field to become a senior logistics manager.
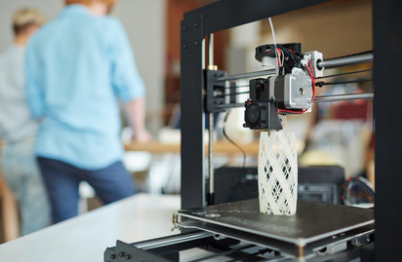
Logistik Analyst
A logistician monitors and changes the logistics within a business to better help them achieve their goals. This involves evaluating inventory levels and scheduling delivery times. A logistics analyst must hold a bachelor's in business or engineering, and have prior experience in the logistics of an industry.
Logistics is a growing industry and there are a lot of jobs available. Set up a free Monster Account today if this is your dream career. You will have a better chance to find the perfect logistics job.
FAQ
What skills is required for a production planner?
Being a production planner is not easy. You need to be organized and flexible. You must also be able to communicate effectively with clients and colleagues.
What are the essential elements of running a logistics firm?
To run a successful logistics company, you need a lot knowledge and skills. You must have good communication skills to interact effectively with your clients and suppliers. You will need to know how to interpret data and draw conclusions. You need to be able work under pressure and manage stressful situations. To improve efficiency, you must be innovative and creative. You will need strong leadership skills to motivate and direct your team members towards achieving their organizational goals.
It is important to be organized and efficient in order to meet tight deadlines.
What does manufacturing industry mean?
Manufacturing Industries are businesses that produce products for sale. Consumers are the people who purchase these products. These companies use a variety processes such as distribution, retailing and management to accomplish their purpose. These companies produce goods using raw materials and other equipment. This includes all types and varieties of manufactured goods, such as food items, clothings, building supplies, furnitures, toys, electronics tools, machinery vehicles, pharmaceuticals medical devices, chemicals, among others.
What is the responsibility for a logistics manager
A logistics manager makes sure that all goods are delivered on-time and in good condition. This is done using his/her knowledge of the company's products. He/she should also ensure enough stock is available to meet demand.
What are the responsibilities for a manufacturing manager
Manufacturing managers must ensure that manufacturing processes are efficient, effective, and cost-effective. They should be aware of any issues within the company and respond accordingly.
They should also be able and comfortable communicating with other departments like sales and marketing.
They must also keep up-to-date with the latest trends in their field and be able use this information to improve productivity and efficiency.
What are the 4 types manufacturing?
Manufacturing refers the process of turning raw materials into useful products with machines and processes. Manufacturing can include many activities such as designing and building, testing, packaging shipping, selling, servicing, and other related activities.
What are the logistics products?
Logistics refers to all activities that involve moving goods from A to B.
They cover all aspects of transportation, such as packing, loading, transporting and unloading.
Logisticians ensure that products reach the right destination at the right moment and under safe conditions. They provide information on demand forecasts as well stock levels, production schedules and availability of raw material.
They keep track and monitor the transit of shipments, maintain quality standards, order replenishment and inventories, coordinate with suppliers, vendors, and provide support for sales and marketing.
Statistics
- In the United States, for example, manufacturing makes up 15% of the economic output. (twi-global.com)
- [54][55] These are the top 50 countries by the total value of manufacturing output in US dollars for its noted year according to World Bank.[56] (en.wikipedia.org)
- According to a Statista study, U.S. businesses spent $1.63 trillion on logistics in 2019, moving goods from origin to end user through various supply chain network segments. (netsuite.com)
- Many factories witnessed a 30% increase in output due to the shift to electric motors. (en.wikipedia.org)
- According to the United Nations Industrial Development Organization (UNIDO), China is the top manufacturer worldwide by 2019 output, producing 28.7% of the total global manufacturing output, followed by the United States, Japan, Germany, and India.[52][53] (en.wikipedia.org)
External Links
How To
How to Use 5S for Increasing Productivity in Manufacturing
5S stands for "Sort", 'Set In Order", 'Standardize', & Separate>. Toyota Motor Corporation developed the 5S method in 1954. This methodology helps companies improve their work environment to increase efficiency.
This method aims to standardize production processes so that they are repeatable, measurable and predictable. This means that daily tasks such as cleaning and sorting, storage, packing, labeling, and packaging are possible. This knowledge allows workers to be more efficient in their work because they are aware of what to expect.
There are five steps that you need to follow in order to implement 5S. Each step involves a different action which leads to increased efficiency. If you sort items, it makes them easier to find later. When you set items in an order, you put items together. Once you have separated your inventory into groups and organized them, you will store these groups in easily accessible containers. Finally, label all containers correctly.
Employees need to reflect on how they do their jobs. Employees need to be able understand their motivations and discover alternative ways to do them. In order to use the 5S system effectively, they must be able to learn new skills.
The 5S method not only increases efficiency but also boosts morale and teamwork. Once they start to notice improvements, they are motivated to keep working towards their goal of increasing efficiency.