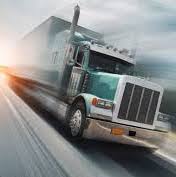
The creation of a "Smart Factory", however, is not just about installing new technology. It's all about changing your factory's mindset, and adapting for new demands. You can help your customers and your business in a new stage of manufacturing with the right technology.
The first step is to decide what you want to achieve. For example, you may want to build a smart factory to respond to dramatic swings in demand. You may also want to create a smart factory that helps your global supply chain partners. You may also want to build a smart factory to respond to an industry heavily dependent on manual labor. Whatever your goal, you need to create an ecosystem supporting it.
One key obstacle to a smart factory is a lack of connectivity. This can be difficult to overcome when you have old machinery and equipment. It can also make it difficult to obtain the required information about your machines and systems. The study found that 33% surveyed said that IT infrastructure is a significant obstacle to building a smart factory.
Technology is the second most important aspect to consider. There are many advanced manufacturing technologies that are currently available. You can use these technologies to enhance your productivity and quality. These technologies can also make your plant more cost-effective.
People are another important factor. It is important to invest in the right skills at just the right time. You must have the right people, and also a skilled talent strategy. It is essential to establish a clear scope of work, and for everyone to agree on their priorities and timeframes. You should ensure that only the right people have access to the projects.
The process is the third most important thing to think about. It is essential that your applications and processes can be connected to a network. This will help you to share information with other systems and processes in your factory. Last but not least, make sure you have analytics and data in place. This will allow data-driven decisions to be made and help you self-heal.
People are fourth in importance. You need to ensure that your executive team is committed to the initiative. It can help to have a convener that can help coordinate and align efforts across multiple vendors. It can also be helpful to ensure that the scope and goals of the project are aligned with your executive staff.
Security is the fifth most important factor. There are many new technologies that can be used to decrease the likelihood of cyberattacks in manufacturing settings. You should make sure that you have the best cybersecurity strategy. A cybersecurity strategy must be maintained.
You should also consider how you will connect your equipment and machines. Although you can use your existing systems, you might consider looking at newer solutions. This will enable you to create data sets that can be used to support smart factory initiatives.
FAQ
What does it mean to warehouse?
Warehouses and storage facilities are where goods are kept before being sold. It can be an outdoor or indoor area. It may also be an indoor space or an outdoor area.
What is the job of a production plan?
Production planners ensure all aspects of the project are delivered within time and budget. They also ensure the quality of the product and service meets the client's requirements.
Are there any Manufacturing Processes that we should know before we can learn about Logistics?
No. It doesn't matter if you don't know anything about manufacturing before you learn about logistics. But, being familiar with manufacturing processes will give you a better understanding about how logistics works.
How can I learn about manufacturing?
The best way to learn about manufacturing is through hands-on experience. If that is not possible, you could always read books or view educational videos.
What is the role of a logistics manager
A logistics manager makes sure that all goods are delivered on-time and in good condition. This is done using his/her knowledge of the company's products. He/she also needs to ensure adequate stock to meet demand.
Statistics
- [54][55] These are the top 50 countries by the total value of manufacturing output in US dollars for its noted year according to World Bank.[56] (en.wikipedia.org)
- Many factories witnessed a 30% increase in output due to the shift to electric motors. (en.wikipedia.org)
- According to a Statista study, U.S. businesses spent $1.63 trillion on logistics in 2019, moving goods from origin to end user through various supply chain network segments. (netsuite.com)
- According to the United Nations Industrial Development Organization (UNIDO), China is the top manufacturer worldwide by 2019 output, producing 28.7% of the total global manufacturing output, followed by the United States, Japan, Germany, and India.[52][53] (en.wikipedia.org)
- It's estimated that 10.8% of the U.S. GDP in 2020 was contributed to manufacturing. (investopedia.com)
External Links
How To
How to Use Lean Manufacturing in the Production of Goods
Lean manufacturing is a management system that aims at increasing efficiency and reducing waste. It was developed by Taiichi Okono in Japan, during the 1970s & 1980s. TPS founder Kanji Takoda awarded him the Toyota Production System Award (TPS). Michael L. Watkins published the book "The Machine That Changed the World", which was the first to be published about lean manufacturing.
Lean manufacturing refers to a set of principles that improve the quality, speed and costs of products and services. It emphasizes eliminating waste and defects throughout the value stream. The five-steps of Lean Manufacturing are just-in time (JIT), zero defect and total productive maintenance (TPM), as well as 5S. Lean manufacturing seeks to eliminate non-value added activities, such as inspection, work, waiting, and rework.
Lean manufacturing improves product quality and costs. It also helps companies reach their goals quicker and decreases employee turnover. Lean manufacturing can be used to manage all aspects of the value chain. Customers, suppliers, distributors, retailers and employees are all included. Lean manufacturing can be found in many industries. Toyota's philosophy has been a key driver of success in many industries, including automobiles and electronics.
Lean manufacturing includes five basic principles:
-
Define Value - Identify the value your business adds to society and what makes you different from competitors.
-
Reduce Waste - Remove any activity which doesn't add value to your supply chain.
-
Create Flow – Ensure that work flows smoothly throughout the process.
-
Standardize & Simplify - Make processes as consistent and repeatable as possible.
-
Build Relationships - Establish personal relationships with both internal and external stakeholders.
Although lean manufacturing has always been around, it is gaining popularity in recent years because of a renewed interest for the economy after 2008's global financial crisis. To increase their competitiveness, many businesses have turned to lean manufacturing. According to some economists, lean manufacturing could be a significant factor in the economic recovery.
Lean manufacturing is now becoming a common practice in the automotive industry, with many benefits. These include improved customer satisfaction, reduced inventory levels, lower operating costs, increased productivity, and better overall safety.
Lean manufacturing can be applied to almost every aspect of an organization. This is because it ensures efficiency and effectiveness in all stages of the value chain.
There are three main types of lean manufacturing:
-
Just-in Time Manufacturing (JIT), also known as "pull system": This form of lean manufacturing is often referred to simply as "pull". JIT is a process in which components can be assembled at the point they are needed, instead of being made ahead of time. This method reduces lead times, increases availability, and decreases inventory.
-
Zero Defects Manufacturing (ZDM): ZDM focuses on ensuring that no defective units leave the manufacturing facility. If a part is required to be repaired on the assembly line, it should not be scrapped. This also applies to finished products that need minor repairs before being shipped.
-
Continuous Improvement: Continuous Improvement aims to improve efficiency by continually identifying problems and making adjustments to eliminate or minimize waste. Continuous improvement refers to continuous improvement of processes as well people and tools.