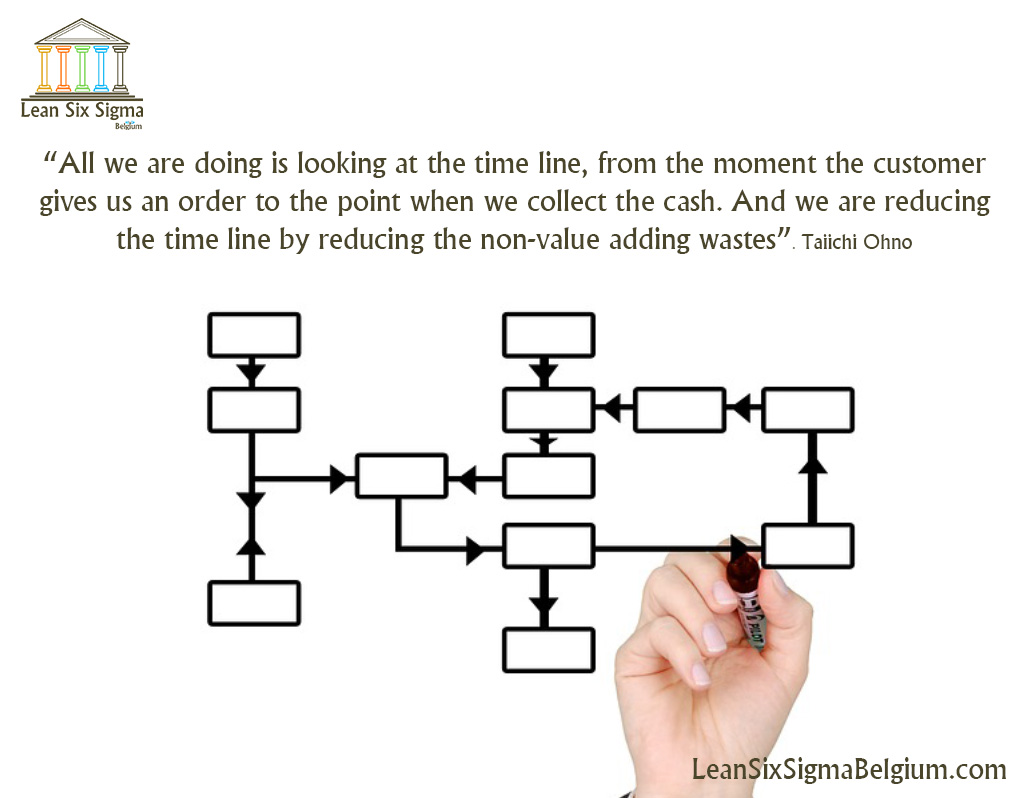
Manufacturing can be brought back to America by relocating, Opportunity zones, Deregulatory and other policies. What can the United States help to do? Here are a few ideas:
Relocation
Companies are shifting production to the U.S., with Intel investing $20 billion to create two new Arizonan semiconductor plants. General Motors and other companies are moving their battery production to Michigan. Michigan is poised for growth as a center for lithium-based products. US Steel is instead building a plant in Alabama and Arkansas, rather than investing $3 billion to build its new steelmaking facility abroad. Others are looking into reshoring opportunities, including Lockheed and General Electric as well as Thermo Fisher.
Opportunity zones
Trump's administration is a strong supporter of opportunity areas. In January of 2017, it established a council, the White House Opportunity and Revitalization Council, to further support the development of these zones. The council has expanded the quoting form and prioritized them. California local investors have one arm tied when referring to opportunity zones. Below are five strategies local investment professionals can use to maximize their investment opportunities.
Deregulatory policy
The United States has struggled long to attract large manufacturers. Fortunately, the tide has begun to turn. Major companies like Walmart are increasing their investments in the U.S., and a recent study released by the Manufacturing Institute shows that American manufacturing is 9 percent cheaper than manufacturing in nine other high-cost countries.
Transport costs are reduced
Transport costs can be a major factor in companies moving their manufacturing to America. Companies are able to move manufacturing jobs to the United States because labor costs are less than in other countries. It is not easy to move manufacturing operations to the United States. However, it can take several years to bring new jobs to the United States. As a result, the cost of goods would rise, but the benefits would be manyfold. Covid-19, a pandemic that ravaged the supply chain in the United States, brought these issues to the attention of the American public. Products like pharmaceuticals, toilet paper, and other products were affected.
Qualified labor
Manufacturing is a key political issue, as has the surprise revelation of recent presidential election results. Commentators declared, "U.S. manufacturing has a moment." Unfortunately, campaign rhetoric rarely leads to long-term commitment. Washington D.C. has a tendency to discuss trade and other issues which don't directly affect manufacturing. They neglect to mention strategies that would strengthen communities and clusters of manufacturing.
FAQ
What does it mean to warehouse?
A warehouse or storage facility is where goods are stored before they are sold. It can be an outdoor or indoor area. It may also be an indoor space or an outdoor area.
Can we automate some parts of manufacturing?
Yes! Yes. The Egyptians discovered the wheel thousands and years ago. Nowadays, we use robots for assembly lines.
In fact, there are several applications of robotics in manufacturing today. These include:
-
Automation line robots
-
Robot welding
-
Robot painting
-
Robotics inspection
-
Robots create products
Manufacturing can also be automated in many other ways. For instance, 3D printing allows us make custom products and not have to wait for months or even weeks to get them made.
Is automation important in manufacturing?
Automation is essential for both manufacturers and service providers. Automation allows them to deliver services quicker and more efficiently. It also helps to reduce costs and improve productivity.
What are manufacturing and logistic?
Manufacturing is the production of goods using raw materials. Logistics is the management of all aspects of supply chain activities, including procurement, production planning, distribution, warehousing, inventory control, transportation, and customer service. Manufacturing and logistics are often considered together as a broader term that encompasses both the process of creating products and delivering them to customers.
Statistics
- According to the United Nations Industrial Development Organization (UNIDO), China is the top manufacturer worldwide by 2019 output, producing 28.7% of the total global manufacturing output, followed by the United States, Japan, Germany, and India.[52][53] (en.wikipedia.org)
- You can multiply the result by 100 to get the total percent of monthly overhead. (investopedia.com)
- According to a Statista study, U.S. businesses spent $1.63 trillion on logistics in 2019, moving goods from origin to end user through various supply chain network segments. (netsuite.com)
- [54][55] These are the top 50 countries by the total value of manufacturing output in US dollars for its noted year according to World Bank.[56] (en.wikipedia.org)
- In the United States, for example, manufacturing makes up 15% of the economic output. (twi-global.com)
External Links
How To
How to use Lean Manufacturing in the production of goods
Lean manufacturing is a management style that aims to increase efficiency and reduce waste through continuous improvement. It was developed in Japan between 1970 and 1980 by Taiichi Ohno. TPS founder Kanji Tyoda gave him the Toyota Production System, or TPS award. Michael L. Watkins published the book "The Machine That Changed the World", which was the first to be published about lean manufacturing.
Lean manufacturing, often described as a set and practice of principles, is aimed at improving the quality, speed, cost, and efficiency of products, services, and other activities. It emphasizes reducing defects and eliminating waste throughout the value chain. Lean manufacturing is also known as just in time (JIT), zero defect total productive maintenance(TPM), and five-star (S). Lean manufacturing focuses on eliminating non-value-added activities such as rework, inspection, and waiting.
Lean manufacturing improves product quality and costs. It also helps companies reach their goals quicker and decreases employee turnover. Lean manufacturing can be used to manage all aspects of the value chain. Customers, suppliers, distributors, retailers and employees are all included. Lean manufacturing is widely used in many industries. Toyota's philosophy has been a key driver of success in many industries, including automobiles and electronics.
Five basic principles of Lean Manufacturing are included in lean manufacturing
-
Define Value - Identify the value your business adds to society and what makes you different from competitors.
-
Reduce Waste - Eliminate any activity that doesn't add value along the supply chain.
-
Create Flow: Ensure that the work process flows without interruptions.
-
Standardize & simplify - Make processes consistent and repeatable.
-
Develop Relationships: Establish personal relationships both with internal and external stakeholders.
Lean manufacturing isn’t new, but it has seen a renewed interest since 2008 due to the global financial crisis. Many businesses are now using lean manufacturing to improve their competitiveness. Many economists believe lean manufacturing will play a major role in economic recovery.
Lean manufacturing is becoming a popular practice in automotive. It has many advantages. These benefits include increased customer satisfaction, reduced inventory levels and lower operating costs.
You can apply Lean Manufacturing to virtually any aspect of your organization. Because it makes sure that all value chains are efficient and effectively managed, Lean Manufacturing is particularly helpful for organizations.
There are three types principally of lean manufacturing:
-
Just-in Time Manufacturing, (JIT): This kind of lean manufacturing is also commonly known as "pull-systems." JIT is a method in which components are assembled right at the moment of use, rather than being manufactured ahead of time. This strategy aims to decrease lead times, increase availability of parts and reduce inventory.
-
Zero Defects Manufacturing, (ZDM): ZDM is focused on ensuring that no defective products leave the manufacturing facility. If a part is required to be repaired on the assembly line, it should not be scrapped. This also applies to finished products that need minor repairs before being shipped.
-
Continuous Improvement (CI: Continuous improvement aims to increase the efficiency of operations by constantly identifying and making improvements to reduce or eliminate waste. It involves continuous improvement of processes, people, and tools.