
Materials engineers research, design, and develop new materials that enable tomorrow's technology. They work with metals ceramics plastics composites and composites in order to create materials that satisfy chemical, electronic, and mechanical requirements.
What does a materials engineer do?
Material engineers process, test and develop raw materials to be used for a variety products like aircraft wings, computer chip, biomedical device, or golf clubs. These engineers evaluate and study the properties and structures of metals such as ceramics or plastics. They also examine nanomaterials which are extremely small substances.
Materials engineers' responsibilities vary depending on the type of material they work with and the sector in which they work. The responsibilities of a materials engineer vary depending on the type of material they work with and the industry in which they work.
What does a materials engineer do?
A materials science engineer works with a variety of different materials including metals, ceramics, and composites to make them stronger, lighter, and more durable. They can also develop new materials that improve existing ones.
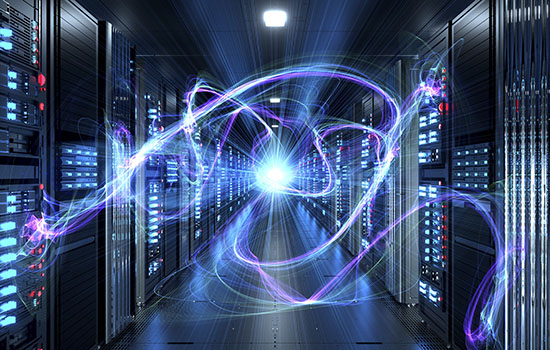
What do materials engineers need?
For a career as a materials engineer you will need to have a bachelor’s degree in an engineering or materials science field. This degree must include both classroom and laboratory training with an emphasis placed on engineering principles. This program may take a couple of years to complete.
After graduating, you may find work as a materials scientist and expect to earn around PS25,000 annually. With experience, the salary you earn will increase.
How to become a material engineer
Materials engineers have different qualifications depending on their industry. The majority of materials engineers require a degree in materials engineering or material science. This will involve studies in chemistry, math, and physics.
A materials science engineer's qualifications are usually a high school diploma, and a bachelor degree in an appropriate field like physics or chemistry. Most higher-level research jobs require a doctorate or master's degree.
How much money can I make as a materials engineer?
The salaries of materials engineers can vary depending on their level of expertise, the industry in which they work and the size of the company. You can also expect bonuses and other benefits for your work.
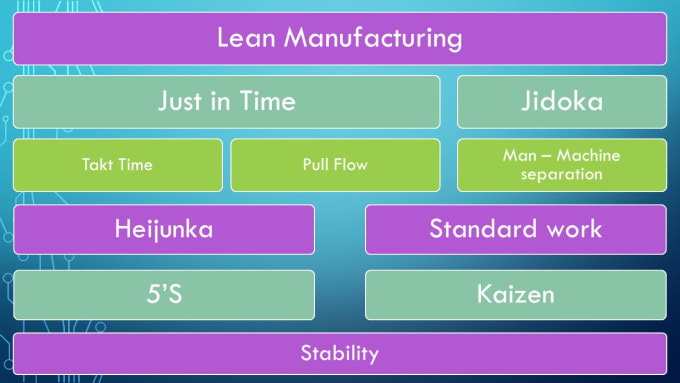
What are the prospects for a career in materials engineering?
The future of the materials engineering career is expected to be very good, with a lot of new opportunities opening up for those who want to get into this line of work. The demand for more advanced and newer materials is increasing in areas such as architecture, medicine, and communication.
Studying metallurgy or chemistry can lead to a career as a materials engineer. You can then pursue a career as a materials engineer. You will benefit from a degree, such as in chemistry, if you want to improve your research skills. For more experience, you could work at an engineering company specializing in a particular field of materials.
FAQ
Why automate your warehouse?
Automation has become increasingly important in modern warehousing. The rise of e-commerce has led to increased demand for faster delivery times and more efficient processes.
Warehouses should be able adapt quickly to new needs. They must invest heavily in technology to do this. The benefits of automating warehouses are numerous. These are just a few reasons to invest in automation.
-
Increases throughput/productivity
-
Reduces errors
-
Improves accuracy
-
Safety enhancements
-
Eliminates bottlenecks
-
This allows companies to scale easily
-
Workers are more productive
-
It gives visibility to everything that happens inside the warehouse
-
Enhances customer experience
-
Improves employee satisfaction
-
Reducing downtime and increasing uptime
-
Ensures quality products are delivered on time
-
Removes human error
-
This helps to ensure compliance with regulations
What skills does a production planner need?
You must be flexible and organized to become a productive production planner. You must also be able to communicate effectively with clients and colleagues.
What are the 7 Rs of logistics?
The acronym 7R's of Logistic is an acronym that stands for seven fundamental principles of logistics management. It was developed by International Association of Business Logisticians (IABL), and published as part of their "Seven Principles of Logistics Management Series" in 2004.
The acronym is composed of the following letters.
-
Responsive - ensure all actions are legal and not harmful to others.
-
Reliable – have faith in your ability and capability to keep promises.
-
Be responsible - Use resources efficiently and avoid wasting them.
-
Realistic - consider all aspects of operations, including cost-effectiveness and environmental impact.
-
Respectful - Treat people fairly and equitably
-
Reliable - Find ways to save money and increase your productivity.
-
Recognizable - provide customers with value-added services.
What is the difference between manufacturing and logistics
Manufacturing refers the process of producing goods from raw materials through machines and processes. Logistics covers all aspects involved in managing supply chains, including procurement and production planning. As a broad term, manufacturing and logistics often refer to both the creation and delivery of products.
How can manufacturing prevent production bottlenecks?
The key to avoiding bottlenecks in production is to keep all processes running smoothly throughout the entire production cycle, from the time you receive an order until the time when the product ships.
This includes planning for capacity requirements as well as quality control measures.
Continuous improvement techniques such Six Sigma can help you achieve this.
Six Sigma is a management system used to improve quality and reduce waste in every aspect of your organization.
It emphasizes consistency and eliminating variance in your work.
What are the responsibilities for a manufacturing manager
A manufacturing manager has to ensure that all manufacturing processes work efficiently and effectively. They should also be aware and responsive to any company problems.
They should also know how to communicate with other departments such as sales and marketing.
They should also be knowledgeable about the latest trends in the industry so they can use this information for productivity and efficiency improvements.
What are the products of logistics?
Logistics are the activities involved in moving goods from point A to point B.
They include all aspects of transport, including packaging, loading, transporting, unloading, storing, warehousing, inventory management, customer service, distribution, returns, and recycling.
Logisticians ensure that the product is delivered to the correct place, at the right time, and under safe conditions. They assist companies with their supply chain efficiency through information on demand forecasts. Stock levels, production times, and availability.
They keep track and monitor the transit of shipments, maintain quality standards, order replenishment and inventories, coordinate with suppliers, vendors, and provide support for sales and marketing.
Statistics
- Job #1 is delivering the ordered product according to specifications: color, size, brand, and quantity. (netsuite.com)
- In 2021, an estimated 12.1 million Americans work in the manufacturing sector.6 (investopedia.com)
- In the United States, for example, manufacturing makes up 15% of the economic output. (twi-global.com)
- You can multiply the result by 100 to get the total percent of monthly overhead. (investopedia.com)
- (2:04) MTO is a production technique wherein products are customized according to customer specifications, and production only starts after an order is received. (oracle.com)
External Links
How To
How to use 5S to increase Productivity in Manufacturing
5S stands in for "Sort", the "Set In Order", "Standardize", or "Separate". Toyota Motor Corporation created the 5S methodology in 1954. It improves the work environment and helps companies to achieve greater efficiency.
The idea behind standardizing production processes is to make them repeatable and measurable. This means that daily tasks such as cleaning and sorting, storage, packing, labeling, and packaging are possible. This knowledge allows workers to be more efficient in their work because they are aware of what to expect.
Implementing 5S involves five steps: Sort, Set in Order, Standardize Separate, Store, and Each step requires a different action, which increases efficiency. By sorting, for example, you make it easy to find the items later. When you set items in an order, you put items together. Next, organize your inventory into categories and store them in containers that are easily accessible. Finally, label all containers correctly.
Employees will need to be more critical about their work. Employees need to understand the reasons they do certain jobs and determine if there is a better way. To be successful in the 5S system, employees will need to acquire new skills and techniques.
The 5S Method not only improves efficiency, but it also helps employees to be more productive and happier. As they begin to see improvements, they feel motivated to continue working towards the goal of achieving higher levels of efficiency.