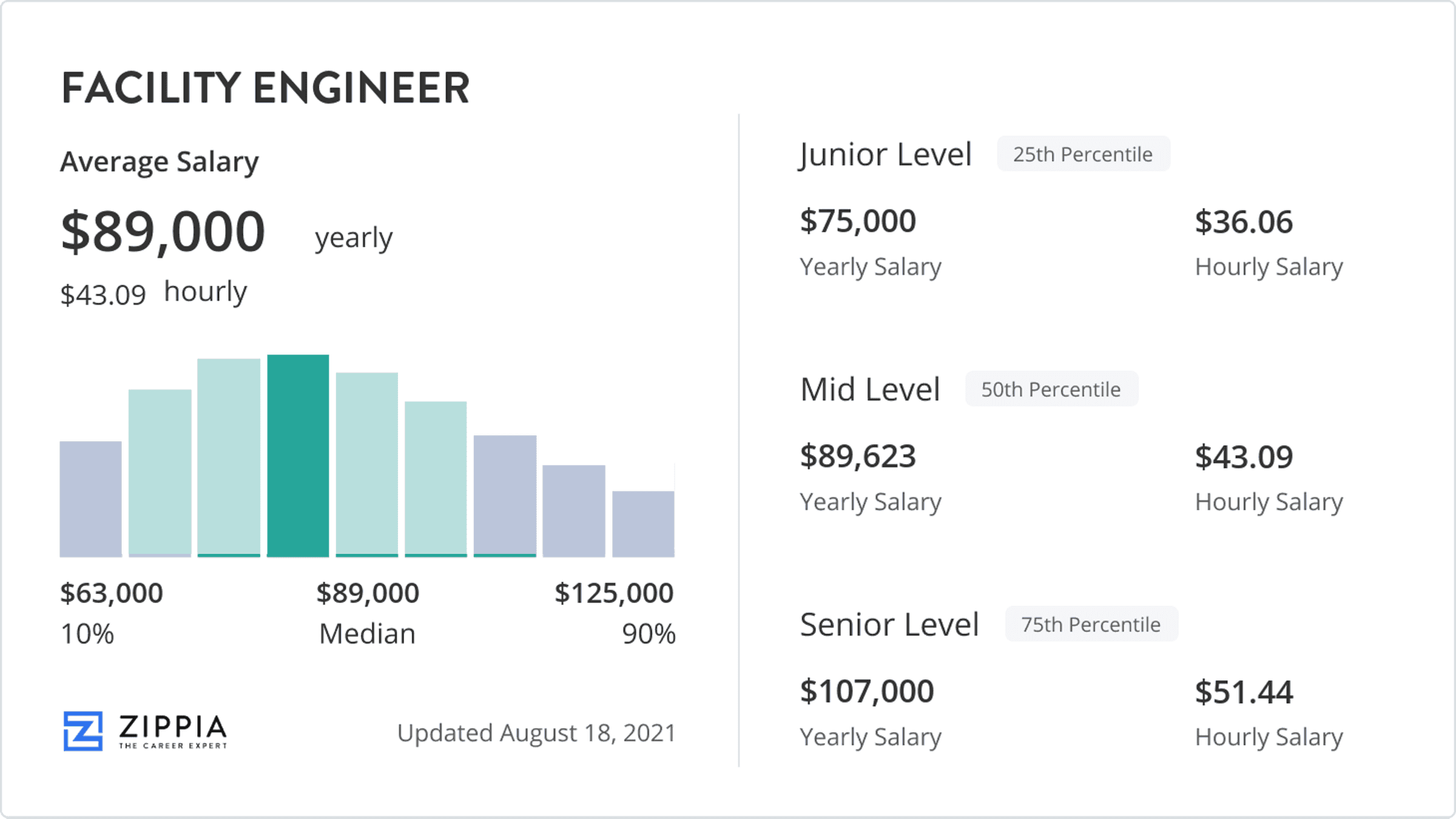
Industrial engineers are responsible for designing and implementing processes that minimize wastefulness and maximize the use of resources. These engineers are employed in many industries to create processes that will benefit their clients in many ways. They look at production schedules, design specifications, as well as workflows to help create more efficient processes. Moreover, industrial engineers are responsible for analyzing the efficiency of production processes to make the company more profitable. They are also responsible for improving the quality of products or services.
Industrial engineer job requirements
The Industrial Engineer is a key role in any manufacturing company. They use innovative design systems to streamline operations for organic and natural food industries. The Industrial Engineer works closely with customers to develop innovative solutions and lead dynamic projects to improve the manufacturing industry. To qualify for this job, an individual must be qualified and able to perform all essential duties satisfactorily. Industrial engineers must be skilled in AutoCAD and Pro-E.
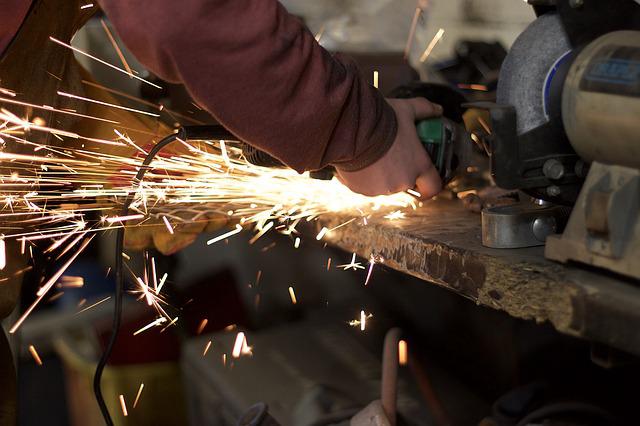
Industrial Engineers are responsible for designing and testing efficient integrated systems. This job is not limited to this. It also includes studying human work factors to increase product quality and efficiency. Other responsibilities include guest coordination and cost analysis. Additionally, the person must have advanced technical skills like Microsoft Office. Experience in manufacturing, logistics, and systems design is also needed. It is essential that you have the technical skills required to perform well in Orlando.
Industrial engineer's salary
You should look at the salaries for Industrial & Manufacturing Engineers here in Orlando, FL if you are considering a career in this field. Orlando is a great place to live with an average salary $80 325 per year. This is 6% less than the national average and 9% below the New York, NY average. Orlando's salary range is $64,260 to $96,390. The middle 67% earn $85,000 annually, while the top 10% earn $102,000.
Industrial engineers in Orlando have salaries that range from $89 700 USD to $114 300 USD. Industrial engineers' salaries can vary, as with all careers. The salary figures listed above are based on the average salary for an Industrial Engineer with five to ten years of experience. However, the average salary for an Industrial Engineer with five to ten years of experience is almost double that of someone with less experience. However, the exact pay scales vary for different industrial engineers.
Responsibilities for industrial engineers
As a process designer and manager, you will determine the best ways to improve process performance. You will be required to design and implement efficient, effective and flexible processes to meet customer demands and business goals. You will be responsible for a wide range of tasks including process improvement, capacity planning and reporting. Additionally, you will be required to perform time studies and observations as well as assist in the development of cross-functional improvement initiatives.
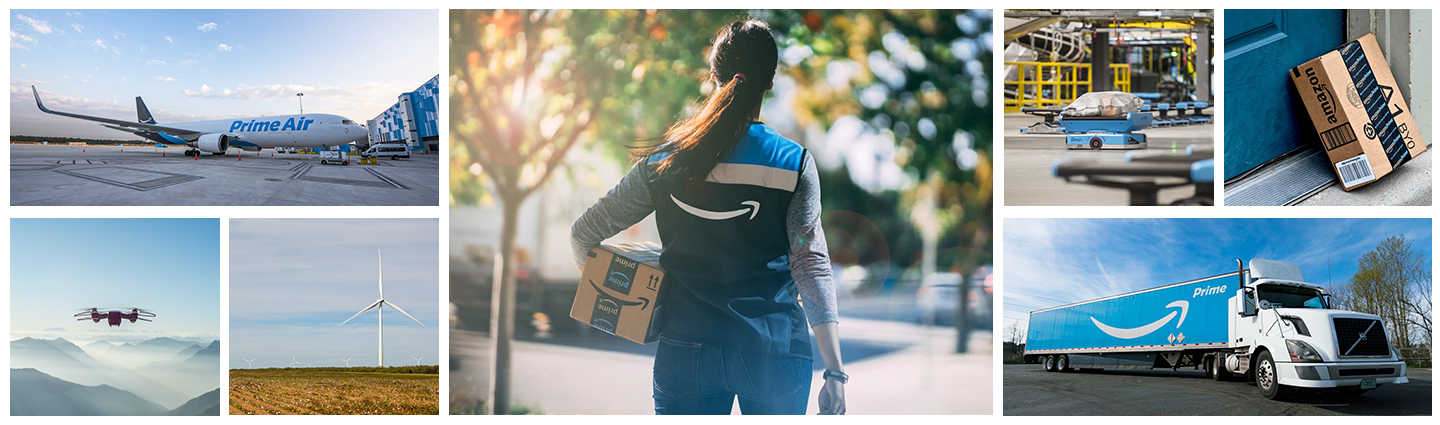
Strong communication skills are required, as well as engineering experience and a strong grasp of statistical analysis, to be able do this job. They will collaborate closely with managers to establish design standards and oversee moderately complex industrial engineering project. They will analyse data and produce statistical reports to improve quality, process flow, and standard times. They will coordinate key research and produce key metrics reports.
FAQ
What is the difference between manufacturing and logistics
Manufacturing refers the process of producing goods from raw materials through machines and processes. Logistics is the management of all aspects of supply chain activities, including procurement, production planning, distribution, warehousing, inventory control, transportation, and customer service. As a broad term, manufacturing and logistics often refer to both the creation and delivery of products.
What are the main products of logistics?
Logistics are the activities involved in moving goods from point A to point B.
They cover all aspects of transportation, such as packing, loading, transporting and unloading.
Logisticians make sure that the right product arrives at the right place at the correct time and in safe conditions. They assist companies with their supply chain efficiency through information on demand forecasts. Stock levels, production times, and availability.
They can also track shipments in transit and monitor quality standards.
What are the 7 Rs of logistics?
The acronym "7R's" of Logistics stands for seven principles that underpin logistics management. It was developed by International Association of Business Logisticians (IABL), and published as part of their "Seven Principles of Logistics Management Series" in 2004.
The acronym is made up of the following letters:
-
Responsible - ensure that actions are in compliance with legal requirements and do not cause harm to others.
-
Reliable: Have faith in your ability or the ability to honor any promises made.
-
Be responsible - Use resources efficiently and avoid wasting them.
-
Realistic - consider all aspects of operations, including cost-effectiveness and environmental impact.
-
Respectful: Treat others with fairness and equity
-
Reliable - Find ways to save money and increase your productivity.
-
Recognizable provides value-added products and services to customers
Is automation important in manufacturing?
Automation is important not only for manufacturers but also for service providers. It allows them provide faster and more efficient services. They can also reduce their costs by reducing human error and improving productivity.
Statistics
- (2:04) MTO is a production technique wherein products are customized according to customer specifications, and production only starts after an order is received. (oracle.com)
- In the United States, for example, manufacturing makes up 15% of the economic output. (twi-global.com)
- It's estimated that 10.8% of the U.S. GDP in 2020 was contributed to manufacturing. (investopedia.com)
- Job #1 is delivering the ordered product according to specifications: color, size, brand, and quantity. (netsuite.com)
- You can multiply the result by 100 to get the total percent of monthly overhead. (investopedia.com)
External Links
How To
How to Use the Just In Time Method in Production
Just-intime (JIT), a method used to lower costs and improve efficiency in business processes, is called just-in-time. It's a way to ensure that you get the right resources at just the right time. This means you only pay what you use. Frederick Taylor developed the concept while working as foreman in early 1900s. He observed how workers were paid overtime if there were delays in their work. He decided to ensure workers have enough time to do their jobs before starting work to improve productivity.
JIT is an acronym that means you need to plan ahead so you don’t waste your money. Also, you should look at the whole project from start-to-finish and make sure you have the resources necessary to address any issues. If you anticipate that there might be problems, you'll have enough people and equipment to fix them. You won't have to pay more for unnecessary items.
There are several types of JIT techniques:
-
Demand-driven: This is a type of JIT where you order the parts/materials needed for your project regularly. This will let you track the amount of material left over after you've used it. This will allow you to calculate how long it will take to make more.
-
Inventory-based: This allows you to store the materials necessary for your projects in advance. This allows you to forecast how much you will sell.
-
Project-driven: This method allows you to set aside enough funds for your project. You will be able to purchase the right amount of materials if you know what you need.
-
Resource-based: This is the most common form of JIT. Here you can allocate certain resources based purely on demand. You will, for example, assign more staff to deal with large orders. If you don't receive many orders, then you'll assign fewer employees to handle the load.
-
Cost-based: This is the same as resource-based except that you don't care how many people there are but how much each one of them costs.
-
Price-based: This is very similar to cost-based, except that instead of looking at how much each individual worker costs, you look at the overall price of the company.
-
Material-based is an alternative to cost-based. Instead of looking at the total cost in the company, this method focuses on the average amount of raw materials that you consume.
-
Time-based JIT: This is another variant of resource-based JIT. Instead of focusing only on how much each employee is costing, you should focus on how long it takes to complete your project.
-
Quality-based JIT: This is another variation of resource based JIT. Instead of focusing on the cost of each worker or how long it takes, think about how high quality your product is.
-
Value-based JIT: This is the latest form of JIT. This is where you don't care about how the products perform or whether they meet customers' expectations. Instead, you're focused on how much value you add to the market.
-
Stock-based: This inventory-based approach focuses on how many items are being produced at any one time. This method is useful when you want to increase production while decreasing inventory.
-
Just-in-time (JIT) planning: This is a combination of JIT and supply chain management. It's the process of scheduling delivery of components immediately after they are ordered. It's important because it reduces lead times and increases throughput.