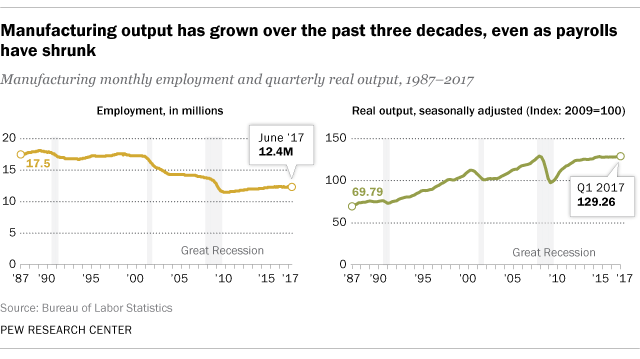
Manufacturing Extension Partnership (MEP) Centers provide a broad range of services to help small and medium-sized manufacturers grow and thrive. MEP Centers are located in every state and Puerto Rico and serve as trusted business advisors, focused on solving manufacturers' challenges and identifying opportunities for growth.
MEP centers recruit subject matter specialists who are familiar with their local industries and have experience working with small and mid-sized manufacturers. The centers can assist in several areas including cybersecurity protection, productivity, quality and business growth. They also create tools that SMMs can use internally or develop with their suppliers, according to Sharon Ohman, senior services manager for Purdue University's MEP center in Fort Wayne.
Centers are funded by federal funds, which pay half to each one. The other half is provided by the state and local governments or private entities. In January 2017, the American Innovation and Competitiveness Act adjusted the cost share ratio for MEP centers, allowing them to retain more of their nonfederal funding.
Many MEP centers are nonprofit organizations or are affiliated with universities. Other MEP centers are operated by the state government or an agency within the same state as the center.
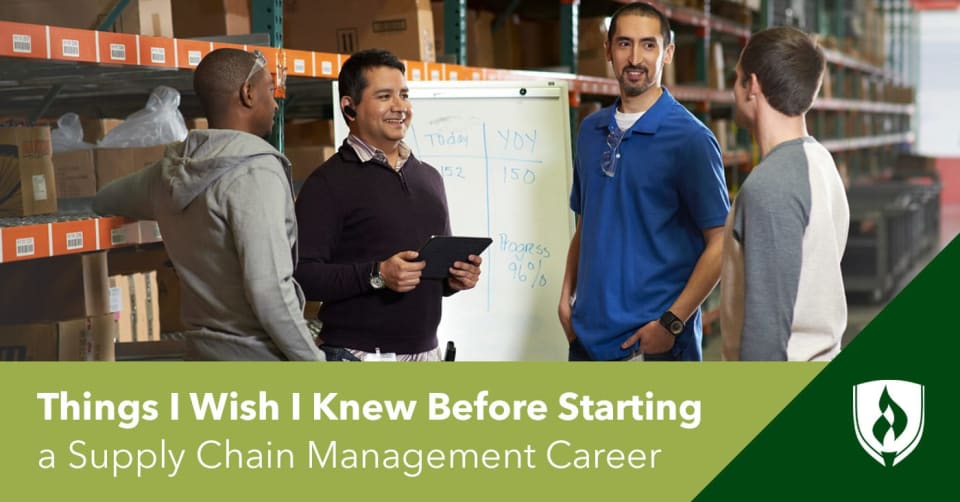
These centers may be staffed by professional technicians, managers or consultants. Some centers have more advanced technology and include laboratories or a center for research.
Some centers provide training and consulting to other companies. For example, the Nebraska MEP provides support to manufacturers on implementing new technology.
MEP services can be delivered to a manufacturer's employees or even to the company itself. Some centers send specialists to manufacturing sites to work with the manufacturer's management team on specific goals.
MEP centers have connected with over 3,000 manufacturers in the last year. It helped them to generate $14.4B in sales and $1.5B in cost-savings, $5.2B in new investments from clients, and 125,746 job creations across the U.S.
The MEP National Network is comprised of the NIST MEP Programme Office, 51 MEP Centers, and an MEP advisory board. The MEP National Network includes the NIST MEP Program Office, 51 MEP Centers and an MEP Advisory Board.
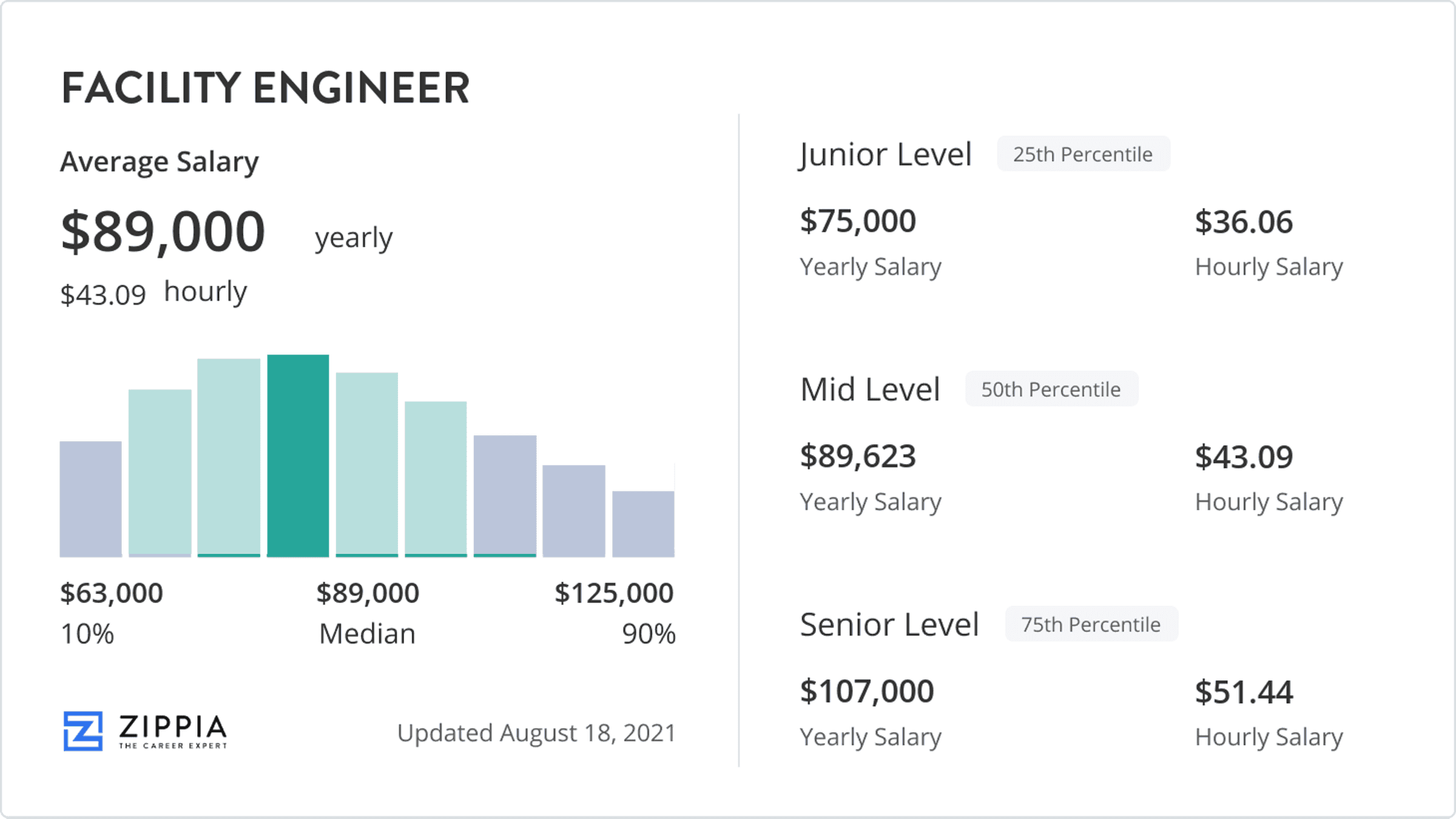
Through its information infrastructure services and pilots, the MEP Network is assisting MEP centers and smaller manufacturers in accessing the technical information they need to operate their businesses. These projects will accelerate the adoption and use of electronic commerce among MEP centers, smaller manufacturers and other businesses.
MEP National Network, in addition to being a critical component of the larger national strategy for increasing the ability of small and mid-sized manufacturers to adopt new technology to support business growth and economic development. The MEP National Network works with over 7,000 manufacturers each year and helps to boost innovation, economic growth and job creation in the United States.
FAQ
What skills should a production planner have?
You must be flexible and organized to become a productive production planner. Effective communication with clients and colleagues is essential.
How can we improve manufacturing efficiency?
First, we need to identify which factors are most critical in affecting production times. We then need to figure out how to improve these variables. If you aren't sure where to begin, think about the factors that have the greatest impact on production time. Once you've identified them, try to find solutions for each of those factors.
How does a Production Planner differ from a Project Manager?
The main difference between a production planner and a project manager is that a project manager is usually the person who plans and organizes the entire project, whereas a production planner is mainly involved in the planning stage of the project.
What is the job of a logistics manger?
Logistics managers ensure that goods arrive on time and are unharmed. This is done through his/her expertise and knowledge about the company's product range. He/she should also ensure enough stock is available to meet demand.
Statistics
- [54][55] These are the top 50 countries by the total value of manufacturing output in US dollars for its noted year according to World Bank.[56] (en.wikipedia.org)
- It's estimated that 10.8% of the U.S. GDP in 2020 was contributed to manufacturing. (investopedia.com)
- Many factories witnessed a 30% increase in output due to the shift to electric motors. (en.wikipedia.org)
- According to a Statista study, U.S. businesses spent $1.63 trillion on logistics in 2019, moving goods from origin to end user through various supply chain network segments. (netsuite.com)
- According to the United Nations Industrial Development Organization (UNIDO), China is the top manufacturer worldwide by 2019 output, producing 28.7% of the total global manufacturing output, followed by the United States, Japan, Germany, and India.[52][53] (en.wikipedia.org)
External Links
How To
Six Sigma: How to Use it in Manufacturing
Six Sigma refers to "the application and control of statistical processes (SPC) techniques in order to achieve continuous improvement." Motorola's Quality Improvement Department created Six Sigma at their Tokyo plant, Japan in 1986. The basic idea behind Six Sigma is to improve quality by improving processes through standardization and eliminating defects. In recent years, many companies have adopted this method because they believe there is no such thing as perfect products or services. The main goal of Six Sigma is to reduce variation from the mean value of production. This means that if you take a sample of your product, then measure its performance against the average, you can find out what percentage of the time the process deviates from the norm. If it is too large, it means that there are problems.
The first step toward implementing Six Sigma is understanding how variability works in your business. Once you've understood that, you'll want to identify sources of variation. You'll also want to determine whether these variations are random or systematic. Random variations are caused by human errors. Systematic variations can be caused by outside factors. If you make widgets and some of them end up on the assembly line, then those are considered random variations. It would be considered a systematic problem if every widget that you build falls apart at the same location each time.
Once you have identified the problem, you can design solutions. You might need to change the way you work or completely redesign the process. Once you have implemented the changes, it is important to test them again to ensure they work. If they fail, you can go back to the drawing board to come up with a different plan.