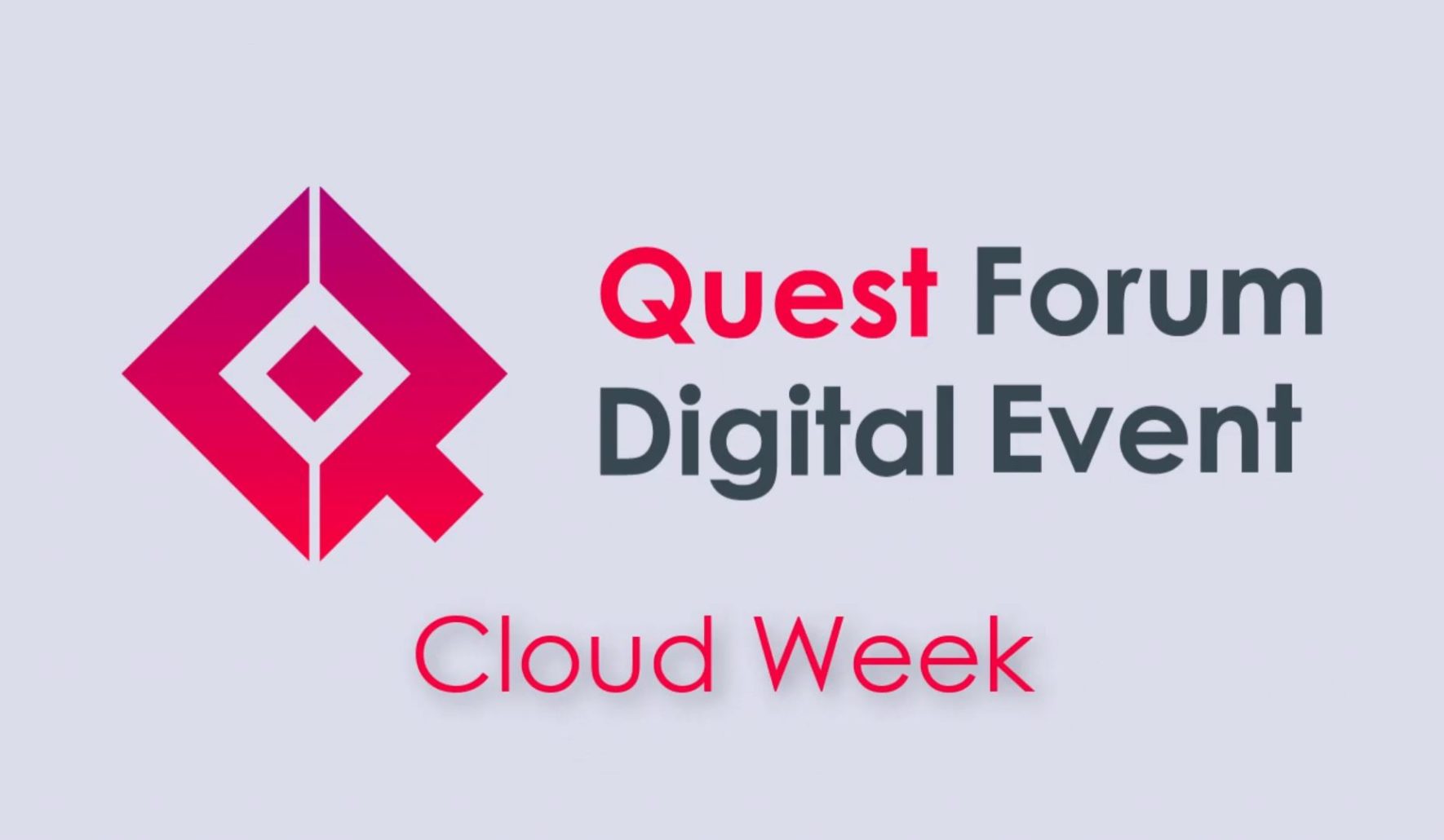
The demand for logistics jobs is increasing, with an expected 5% growth between 2018 and 2028. Learn more about the job requirements of logistics professionals and what education you will need to get started. These are just a few of the questions that need to be answered before applying for a logistics job. Once you have read this information, you will be ready to begin your career. Here are some examples and information about the salaries of logistics professionals. Want to become a logistics professional yourself?
Logistics careers will see a 5% increase between 2018-2028
Globalization is increasing in importance, which means that logisticians worldwide are increasingly needed. Companies need the right products at the right time and at the right price, and logistics professionals help them get there. All types of businesses need specialists, managers, coordinators and specialists in logistics. The Kangan Institute lists five reasons why a job in logistics might be the right fit for you. The logistics industry offers high stability and offers high levels of security.
Logistics professionals oversee the entire product lifecycle and work closely with multiple stakeholders. Software is used to plan the movement and distribution of products, from purchase to final distribution. According to Bureau of Labor Statistics, the demand in logistics professionals will rise by 5% within the next decade. In the meantime purchasing managers manage more difficult procurement tasks. Logistics careers are highly sought after.
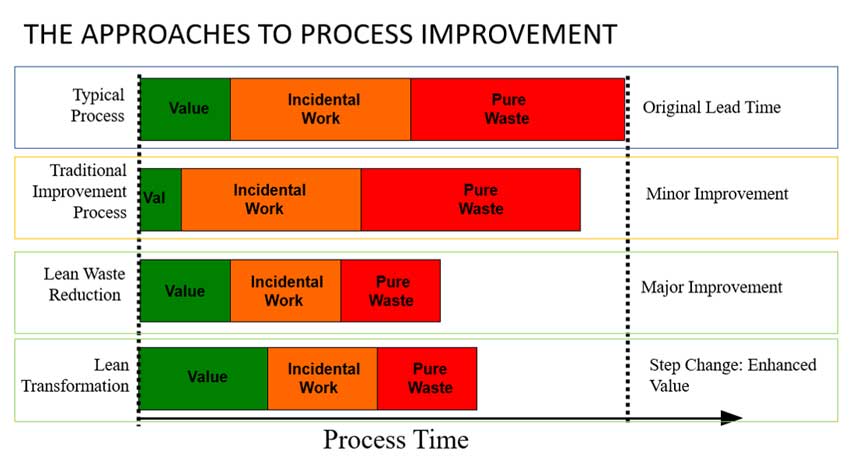
Duties of a logistics professional
You will need a degree and at least two years of experience to be a logistics manger. This job requires extensive knowledge in inventory management software and analytical skills. The ideal candidate should be organized, have strong communication skills and verbal and/or written communication skills. Logistics managers may be responsible for tracking and evaluating metrics. A logistics professional might also interact with employees from other departments.
In some organizations, a logistics manager manages the entire supply chain, including purchasing services, warehousing, transportation, distribution, and customer service. They are responsible for the planning and implementation of the logistics system, as well as overseeing the daily operations and goals for accuracy, productivity, and costs. Additionally, they are responsible for establishing supply chain-based performance measurement systems and training shipping department personnel. They might also assist in the selection of carriers and take part in negotiations concerning sustainability or efficiency in supply chain management.
Salary for logistics professionals
If you love helping organizations get products to market quickly, a career as a logistics professional is an excellent choice. The logistics field includes managing all aspects of a product's life cycle, including design, production, marketing, distribution, and transport plans. According to BLS, the median annual salary for logistics professionals is $76,270 in May 2020. The career outlook for logistics professionals is excellent; according to the BLS, the number of jobs in this field will increase by 30 percent by the end of the decade.
Although the first paycheck may not be a reason to celebrate, your salary will rise as you gain more experience and skills. Many logistics managers are responsible to plan, direct and monitor the distribution and financial transactions. According to a recent survey, the salary for logistics managers in the District of Columbia is the highest in the nation. Salary information is available by state, zip code, and even by company.
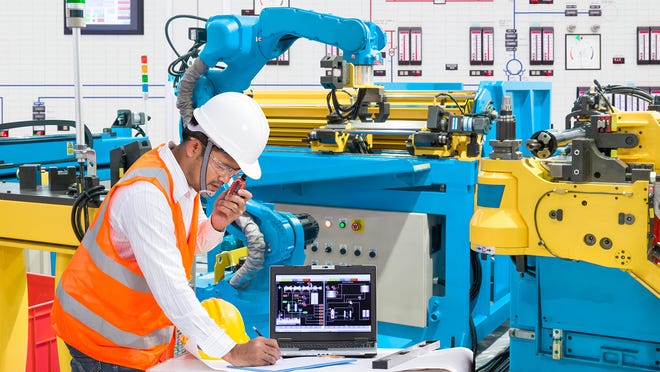
You need to be educated in order to become a logistics professional
There are several reasons why you would want to pursue a career as a logistics professional. These professionals ensure the smooth operation and success of organizations and companies. As Baby Boomers enter retirement, it is becoming less visible in the logistics industry. This might actually be beneficial for this field. Although most people are aware about opportunities in the fields of accounting, law and nursing, very few are aware of the logistics industry.
An associate's in logistics degree, also called a "two year degree", requires 60 credits. The program can be completed in two years of full-time study. This program covers logistics, supply chain management, transport systems, management information system, and production methods. After graduation, you may work in a logistics company.
FAQ
What are manufacturing and logistics?
Manufacturing is the process of creating goods from raw materials by using machines and processes. Logistics is the management of all aspects of supply chain activities, including procurement, production planning, distribution, warehousing, inventory control, transportation, and customer service. Logistics and manufacturing are often referred to as one thing. It encompasses both the creation of products and their delivery to customers.
What type of jobs is there in logistics
There are many jobs available in logistics. Here are some:
-
Warehouse workers: They load and unload trucks, pallets, and other cargo.
-
Transport drivers - These are people who drive trucks and trailers to transport goods or perform pick-ups.
-
Freight handlers - They sort and pack freight in warehouses.
-
Inventory managers – They manage the inventory in warehouses.
-
Sales reps are people who sell products to customers.
-
Logistics coordinators - They plan and organize logistics operations.
-
Purchasing agents are those who purchase goods and services for the company.
-
Customer service representatives are available to answer customer calls and emails.
-
Shipping clerks – They process shipping orders, and issue bills.
-
Order fillers - These people fill orders based on what has been ordered.
-
Quality control inspectors: They inspect outgoing and incoming products for any defects.
-
Others - There are many other types of jobs available in logistics, such as transportation supervisors, cargo specialists, etc.
What are the 4 types manufacturing?
Manufacturing refers the process of turning raw materials into useful products with machines and processes. Manufacturing involves many activities, including designing, building, testing and packaging, shipping, selling, service, and so on.
What are the 7 Rs of logistics?
The acronym 7R's for Logistics stands to represent the seven basic principles in logistics management. It was created by the International Association of Business Logisticians and published in 2004 under its "Seven Principles of Logistics Management".
The acronym consists of the following letters:
-
Responsible – ensure that all actions are legal and don't cause harm to anyone else.
-
Reliable: Have faith in your ability or the ability to honor any promises made.
-
It is reasonable to use resources efficiently and not waste them.
-
Realistic – Consider all aspects, including cost-effectiveness as well as environmental impact.
-
Respectful - Treat people fairly and equitably
-
You are resourceful and look for ways to save money while increasing productivity.
-
Recognizable provides value-added products and services to customers
What can I do to learn more about manufacturing?
Experience is the best way for you to learn about manufacturing. However, if that's not possible, you can always read books or watch educational videos.
Do we need to know about Manufacturing Processes before learning about Logistics?
No. No. It is important to know about the manufacturing processes in order to understand how logistics works.
How can we increase manufacturing efficiency?
First, determine which factors have the greatest impact on production time. We must then find ways that we can improve these factors. If you don’t know where to begin, consider which factors have the largest impact on production times. Once you identify them, look for solutions.
Statistics
- According to a Statista study, U.S. businesses spent $1.63 trillion on logistics in 2019, moving goods from origin to end user through various supply chain network segments. (netsuite.com)
- (2:04) MTO is a production technique wherein products are customized according to customer specifications, and production only starts after an order is received. (oracle.com)
- According to the United Nations Industrial Development Organization (UNIDO), China is the top manufacturer worldwide by 2019 output, producing 28.7% of the total global manufacturing output, followed by the United States, Japan, Germany, and India.[52][53] (en.wikipedia.org)
- In 2021, an estimated 12.1 million Americans work in the manufacturing sector.6 (investopedia.com)
- You can multiply the result by 100 to get the total percent of monthly overhead. (investopedia.com)
External Links
How To
How to use the Just In-Time Production Method
Just-in time (JIT), is a process that reduces costs and increases efficiency in business operations. It's a way to ensure that you get the right resources at just the right time. This means that you only pay the amount you actually use. Frederick Taylor was the first to coin this term. He developed it while working as a foreman during the early 1900s. He saw how overtime was paid to workers for work that was delayed. He realized that workers should have enough time to complete their jobs before they begin work. This would help increase productivity.
JIT teaches you to plan ahead and prepare everything so you don’t waste time. Look at your entire project, from start to end. Make sure you have enough resources in place to deal with any unexpected problems. If you anticipate that there might be problems, you'll have enough people and equipment to fix them. You won't have to pay more for unnecessary items.
There are many JIT methods.
-
Demand-driven JIT: You order the parts and materials you need for your project every other day. This will allow for you to track the material that you have left after using it. This will let you know how long it will be to produce more.
-
Inventory-based: You stock materials in advance to make your projects easier. This allows for you to anticipate how much you can sell.
-
Project-driven : This is a method where you make sure that enough money is set aside to pay the project's cost. When you know how much you need, you'll purchase the appropriate amount of materials.
-
Resource-based: This is the most common form of JIT. You assign certain resources based off demand. You will, for example, assign more staff to deal with large orders. You'll have fewer orders if you have fewer.
-
Cost-based: This is a similar approach to resource-based but you are not only concerned with how many people you have, but also how much each one costs.
-
Price-based: This is a variant of cost-based. However, instead of focusing on the individual workers' costs, this looks at the total price of the company.
-
Material-based: This approach is similar to cost-based. However, instead of looking at the total cost for the company, you look at how much you spend on average on raw materials.
-
Time-based JIT: This is another variant of resource-based JIT. Instead of focusing on how much each employee costs, you focus on how long it takes to complete the project.
-
Quality-based: This is yet another variation of resource-based JIT. Instead of looking at the labor costs and time it takes to make a product, think about its quality.
-
Value-based JIT is the newest form of JIT. In this case, you're not concerned with how well the products perform or whether they meet customer expectations. Instead, you focus on the added value that you provide to your market.
-
Stock-based: This stock-based method focuses on the actual quantity of products being made at any given time. This is used to increase production and minimize inventory.
-
Just-in-time planning (JIT): This is a combination JIT and supply-chain management. It refers to the process of scheduling the delivery of components as soon as they are ordered. It's important because it reduces lead times and increases throughput.