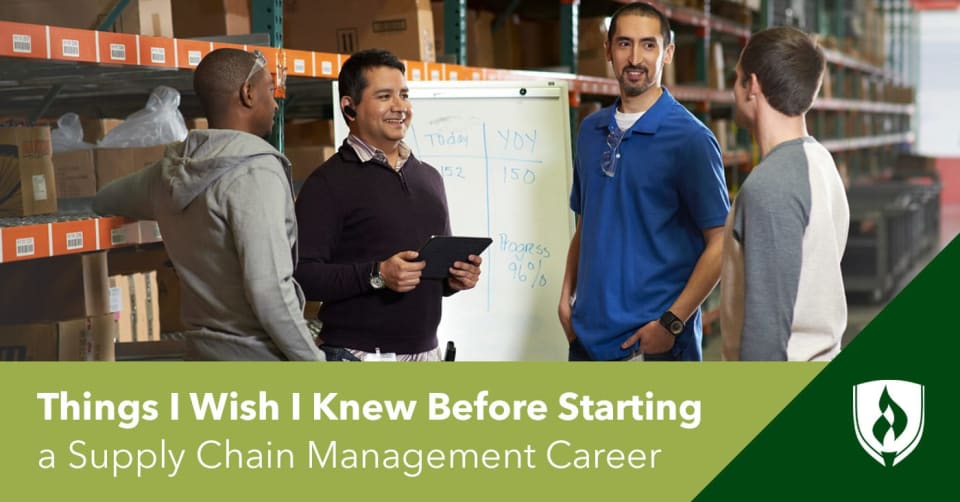
Flow is the state in which all the steps of a production line follow each other seamlessly without interruption. Each step adds to the product's value, and goods move smoothly through the manufacturing process without being stopped. Many companies plan out the production of a certain quantity of stock to ensure that production orders are fulfilled as efficiently and effectively as possible. This is Lean Manufacturing's term for "push" production. Here are the essential elements of flow.
Manufacturing in real-time
The dominant paradigm of "just in time" manufacturing was prevalent when lean manufacturing was introduced to the U.S. late 1970s. This concept is not practical, and it does not have the greatest benefits. The process of reducing costs and increasing efficiency requires many new skills and mindsets. It is worth the effort if you are to reap all of its benefits.
Standardization and the ability to work with smaller lots are some of the key elements of just-in–time manufacturing. In order to encourage a just in time mindset, it is important to plan your facility layout. Cellular manufacturing, for instance, can facilitate production flow. Cellular organization can make it easier to move materials around. For just-intime manufacturing, it is important to avoid long changeovers.
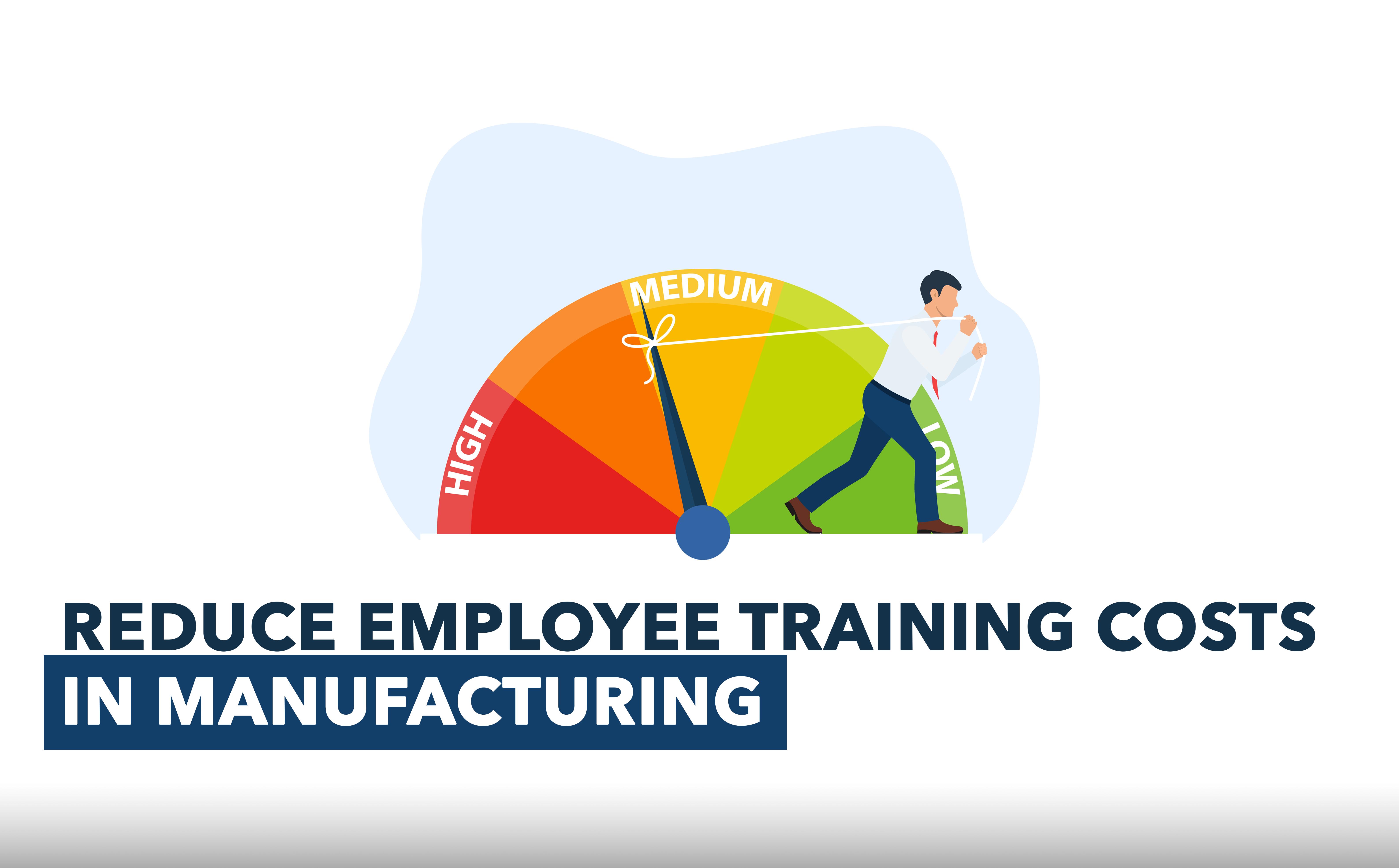
Standardized work
Standardized work is essential in applying lean manufacturing to manufacturing processes. This system of work places emphasis on the workers involved in the production process. It also refers to the process of continuously improving the system through kaizen. The cell leader is responsible to update standardized work documents as soon as takt time changes. Standardized work documentation is a foundation for improvement activities.
Organizations can improve their productivity as well as service quality by having standard work processes. They can reduce the time it takes to develop products and help reduce human error. It also enables the organization to fix problems faster, as people understand the process better. This enables the organization to implement continuous improvement and increase its customer satisfaction. These processes can then be implemented easily in companies once they are standardized. A mission statement is a great idea.
Continuous improvement
Lean principles promote continuous improvement. They result in a wide range of benefits. These benefits are usually additive, but one thread links them all: increased productivity, lower costs, and shorter lead times. Lean continuous improvement is about increasing value creation. But how does continuous improving work? This article will provide an overview of the common benefits of continuous improvements. It's very simple: continuous improvement helps companies save money.
In continuous improvement, a company focuses on incremental improvements rather than sweeping changes. Even though individual improvements might seem insignificant or small, the overall effect of continuous improvement is significant. Slow improvements are more effective than large leaps. In a lean manufacturing environment, continuous improvement focuses on alignment of goals, allowing the business to maximize productivity and profitability. Continuous improvement can make the entire production process more efficient and enable all processes to work together toward a common goal.
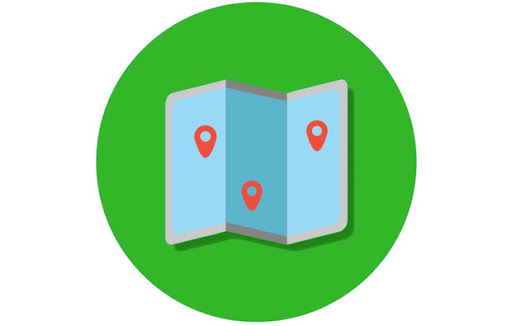
Kaizen
Kaizen is a lean manufacturing method that focuses on eliminating waste. In some cases, it is used to improve production yield, decrease lead time, and improve quality. A team of employees is assigned a specific role to study the problem and propose solutions. The process of creating a value stream map for kaizen usually begins with the creation. The team then conducts time studies on the relevant operations. This is repeated until the process is more efficient and leaner.
An example is a manufacturing plant that has identified inefficiencies and may buy a new lift truck. Its operator could move inventory around to make loading/unloading more efficient. The value stream, which is a map that shows the processes involved in creating products and services, can be used similarly. Five S's are used in the mapping process to increase employee productivity, workplace practices, and workplace efficiency. There are seven types. Each of these types focuses on a different aspect of a manufacturing process.
FAQ
What are the 7 Rs of logistics.
The acronym 7R's of Logistic is an acronym that stands for seven fundamental principles of logistics management. It was created by the International Association of Business Logisticians and published in 2004 under its "Seven Principles of Logistics Management".
The acronym is made up of the following letters:
-
Responsible - to ensure that all actions are within the legal requirements and are not detrimental to others.
-
Reliable - have confidence in the ability to deliver on commitments made.
-
It is reasonable to use resources efficiently and not waste them.
-
Realistic – Consider all aspects, including cost-effectiveness as well as environmental impact.
-
Respectful - treat people fairly and equitably.
-
Reliable - Find ways to save money and increase your productivity.
-
Recognizable - provide customers with value-added services.
Are there any Manufacturing Processes that we should know before we can learn about Logistics?
No. No. However, knowing about manufacturing processes will definitely give you a better understanding of how logistics works.
What are the requirements to start a logistics business?
To run a successful logistics company, you need a lot knowledge and skills. For clients and suppliers to be successful, you need to have excellent communication skills. You will need to know how to interpret data and draw conclusions. You need to be able work under pressure and manage stressful situations. To improve efficiency, you must be innovative and creative. To motivate and guide your team towards reaching organizational goals, you must have strong leadership skills.
You must be organized to meet tight deadlines.
Statistics
- Job #1 is delivering the ordered product according to specifications: color, size, brand, and quantity. (netsuite.com)
- In 2021, an estimated 12.1 million Americans work in the manufacturing sector.6 (investopedia.com)
- You can multiply the result by 100 to get the total percent of monthly overhead. (investopedia.com)
- (2:04) MTO is a production technique wherein products are customized according to customer specifications, and production only starts after an order is received. (oracle.com)
- Many factories witnessed a 30% increase in output due to the shift to electric motors. (en.wikipedia.org)
External Links
How To
How to use the Just In-Time Production Method
Just-intime (JIT), a method used to lower costs and improve efficiency in business processes, is called just-in-time. This is where you have the right resources at the right time. This means that only what you use is charged to your account. The term was first coined by Frederick Taylor, who developed his theory while working as a foreman in the early 1900s. He observed how workers were paid overtime if there were delays in their work. He decided to ensure workers have enough time to do their jobs before starting work to improve productivity.
JIT is an acronym that means you need to plan ahead so you don’t waste your money. Also, you should look at the whole project from start-to-finish and make sure you have the resources necessary to address any issues. You will have the resources and people to solve any problems you anticipate. This will ensure that you don't spend more money on things that aren't necessary.
There are many JIT methods.
-
Demand-driven JIT: You order the parts and materials you need for your project every other day. This will allow for you to track the material that you have left after using it. This will allow you to calculate how long it will take to make more.
-
Inventory-based: This is a type where you stock the materials required for your projects in advance. This allows you predict the amount you can expect to sell.
-
Project-driven: This method allows you to set aside enough funds for your project. Once you have an idea of how much material you will need, you can purchase the necessary materials.
-
Resource-based JIT is the most widespread form. You allocate resources based on the demand. For example, if there is a lot of work coming in, you will have more people assigned to them. If you don't receive many orders, then you'll assign fewer employees to handle the load.
-
Cost-based: This is the same as resource-based except that you don't care how many people there are but how much each one of them costs.
-
Price-based: This is similar to cost-based but instead of looking at individual workers' salaries, you look at the total company price.
-
Material-based - This is a variant of cost-based. But instead of looking at the total company cost, you focus on how much raw material you spend per year.
-
Time-based JIT: This is another variant of resource-based JIT. Instead of focusing on the cost of each employee, you will focus on the time it takes to complete a project.
-
Quality-based JIT is another variant of resource-based JIT. Instead of thinking about how much each employee costs or how long it takes to manufacture something, you think about how good the quality of your product is.
-
Value-based JIT: One of the most recent forms of JIT. In this scenario, you're not concerned about how products perform or whether customers expect them to meet their expectations. Instead, you're focused on how much value you add to the market.
-
Stock-based: This stock-based method focuses on the actual quantity of products being made at any given time. This method is useful when you want to increase production while decreasing inventory.
-
Just-intime (JIT), planning is a combination JIT management and supply chain management. It is the process of scheduling components' delivery as soon as they have been ordered. This is important as it reduces lead time and increases throughput.