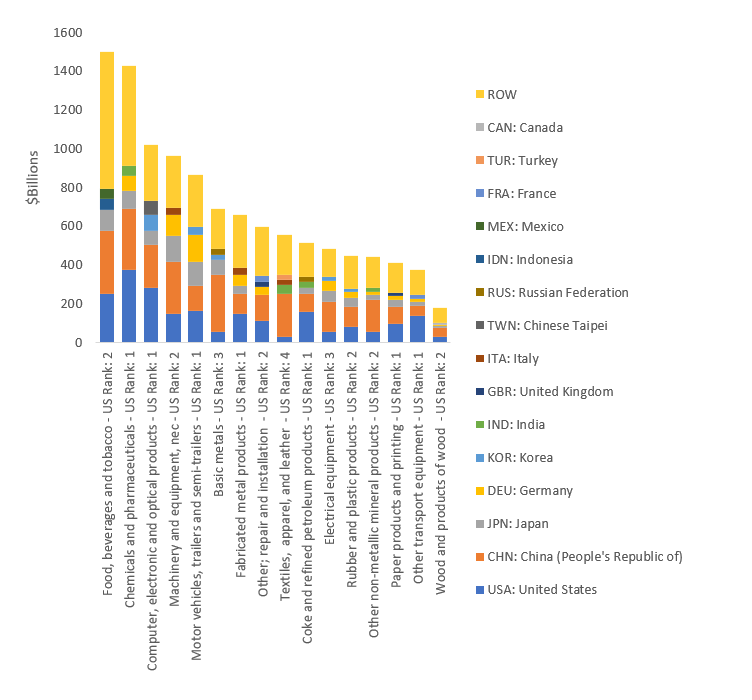
There are three main sectors in classical economics. These categories can be broken down into manufacturing, services, or financial activities. Business classifications are based on the characteristics and risks of each business. Each of these three sectors is described below. Below is a brief overview about the types of businesses found in each sector. If you are interested, you can explore the information further. But, these categories should not be viewed as mutually exclusive.
Economic activity
Factors that are used to produce, inputs, or outputs affect the country's economic activity. The demand for particular goods or services is often the determinant of a region’s economic activity. There are two types if economic activity. Primary economic activities offer goods and services that meet human needs. Secondary economic activities add value to raw materials to create a more valuable product. Some examples of secondary economic activities include manufacturing and processing industries.
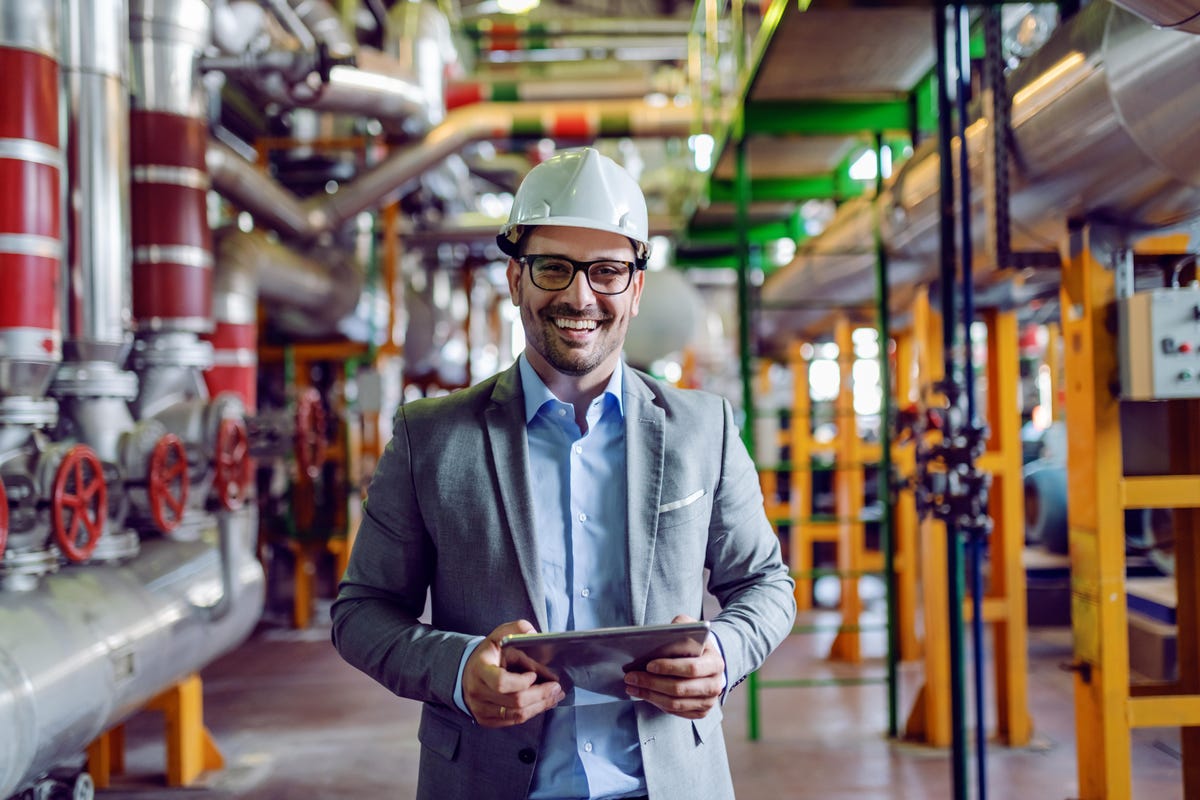
Classification
The process of classifying businesses is to divide them into groups according to the activities they do. There are two major categories: primary and second. Primary businesses are those which extract or exchange natural resources. The second type of business processes and transforms raw materials into products that are ready for consumption. These two types of businesses have many differences. Here are some major differences between both types. You can use the information from this article to help you decide which type of business is best for your company.
Characteristics
The following discussion explains the differences between the primary, secondary, and tertiary sectors and focuses on how each type of sector affects the economy. First, let's define sectors. Sectors can be considered unique economic entities. They respond differently depending on different factors. These circumstances may be repeated, such as business cycles, or they may be single events, such as improvements in technology. These characteristics are useful in identifying the most profitable sectors and determining their relative importance within an economy.
Risques
Industry risk refers the variation in performance among industries and between companies. It can be measured using the variance in ROE and profitability. This can be adjusted depending on industry to reflect the performance stock markets. A company that makes steel is high-risk because of the possibility for major earthquakes in the area. These risks could help investors to determine which industries are more volatile.
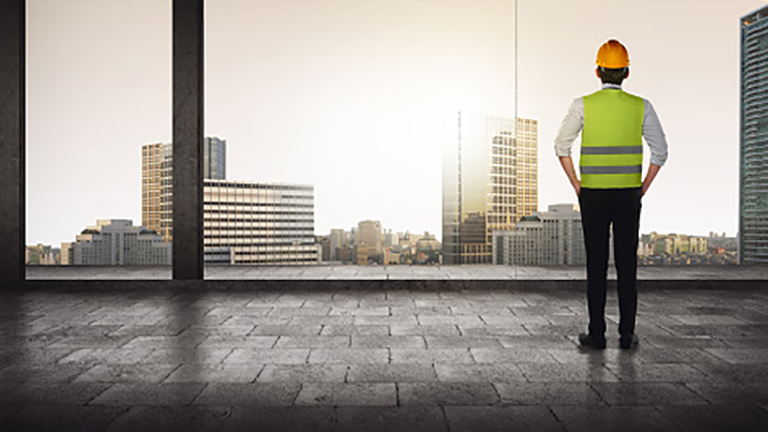
Investments
Although many investors prefer to invest in companies, it is possible to invest in sectors. Sectors are more risk-free and can be found within mutual funds and exchange traded funds. Sector investing is becoming an increasingly popular investment strategy. This article will talk about how sector investment can help you find the best investments. Keep reading to find out more. You can also visit our free resource section for additional information.
FAQ
What are the four types in manufacturing?
Manufacturing refers the process of turning raw materials into useful products with machines and processes. Manufacturing can include many activities such as designing and building, testing, packaging shipping, selling, servicing, and other related activities.
What are the products of logistics?
Logistics refers to the movement of goods from one place to another.
They include all aspects associated with transport including packaging, loading transporting, unloading storage, warehousing inventory management customer service, distribution returns and recycling.
Logisticians ensure that products reach the right destination at the right moment and under safe conditions. They provide information on demand forecasts as well stock levels, production schedules and availability of raw material.
They keep track and monitor the transit of shipments, maintain quality standards, order replenishment and inventories, coordinate with suppliers, vendors, and provide support for sales and marketing.
What is the best way to learn about manufacturing?
The best way to learn about manufacturing is through hands-on experience. If that is not possible, you could always read books or view educational videos.
Statistics
- (2:04) MTO is a production technique wherein products are customized according to customer specifications, and production only starts after an order is received. (oracle.com)
- You can multiply the result by 100 to get the total percent of monthly overhead. (investopedia.com)
- According to the United Nations Industrial Development Organization (UNIDO), China is the top manufacturer worldwide by 2019 output, producing 28.7% of the total global manufacturing output, followed by the United States, Japan, Germany, and India.[52][53] (en.wikipedia.org)
- It's estimated that 10.8% of the U.S. GDP in 2020 was contributed to manufacturing. (investopedia.com)
- In 2021, an estimated 12.1 million Americans work in the manufacturing sector.6 (investopedia.com)
External Links
How To
How to Use the Just In Time Method in Production
Just-intime (JIT), a method used to lower costs and improve efficiency in business processes, is called just-in-time. It allows you to get the right amount resources at the right time. This means that only what you use is charged to your account. Frederick Taylor was the first to coin this term. He developed it while working as a foreman during the early 1900s. After observing how workers were paid overtime for late work, he realized that overtime was a common practice. He then concluded that if he could ensure that workers had enough time to do their job before starting to work, this would improve productivity.
JIT teaches you to plan ahead and prepare everything so you don’t waste time. The entire project should be looked at from start to finish. You need to ensure you have enough resources to tackle any issues that might arise. You'll be prepared to handle any potential problems if you know in advance. This will ensure that you don't spend more money on things that aren't necessary.
There are many JIT methods.
-
Demand-driven: This JIT is where you place regular orders for the parts/materials that are needed for your project. This will allow to track how much material has been used up. This will allow to you estimate the time it will take for more to be produced.
-
Inventory-based: This is a type where you stock the materials required for your projects in advance. This allows you to predict how much you can expect to sell.
-
Project-driven: This is an approach where you set aside enough funds to cover the cost of your project. When you know how much you need, you'll purchase the appropriate amount of materials.
-
Resource-based JIT: This type of JIT is most commonly used. You assign certain resources based off demand. If you have many orders, you will assign more people to manage them. If you don't receive many orders, then you'll assign fewer employees to handle the load.
-
Cost-based: This is similar to resource-based, except that here you're not just concerned about how many people you have but how much each person costs.
-
Price-based: This is a variant of cost-based. However, instead of focusing on the individual workers' costs, this looks at the total price of the company.
-
Material-based - This is a variant of cost-based. But instead of looking at the total company cost, you focus on how much raw material you spend per year.
-
Time-based JIT: A variation on resource-based JIT. Instead of focusing on the cost of each employee, you will focus on the time it takes to complete a project.
-
Quality-based JIT - This is another form of resource-based JIT. Instead of thinking about how much each employee costs or how long it takes to manufacture something, you think about how good the quality of your product is.
-
Value-based JIT: This is the latest form of JIT. In this scenario, you're not concerned about how products perform or whether customers expect them to meet their expectations. Instead, your goal is to add value to the market.
-
Stock-based: This is an inventory-based method that focuses on the actual number of items being produced at any given time. It's useful when you want maximum production and minimal inventory.
-
Just-in-time (JIT) planning: This is a combination of JIT and supply chain management. It is the process of scheduling components' delivery as soon as they have been ordered. It is essential because it reduces lead-times and increases throughput.