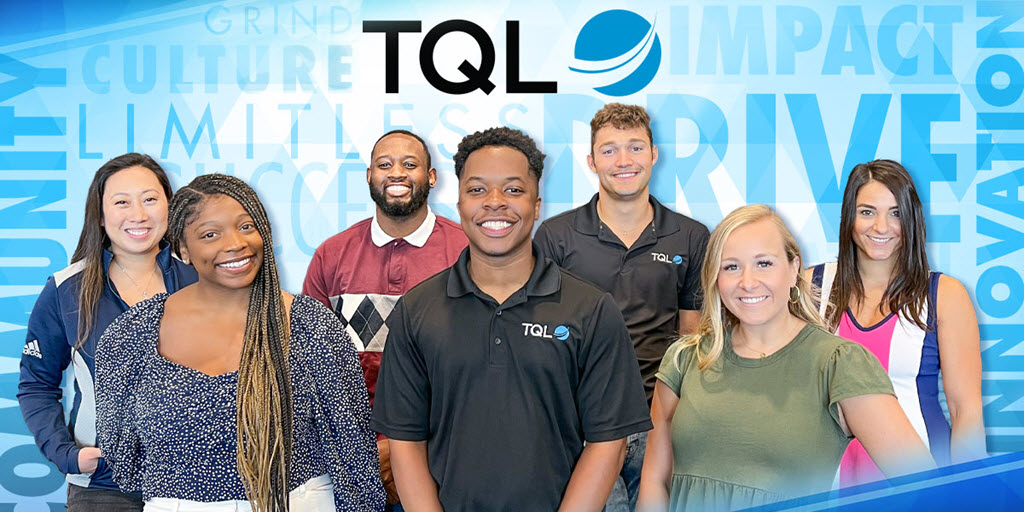
Industrial engineering technicians use their knowledge of mathematics and engineering to determine and improve the way a business runs. This includes the development of blueprints for machinery and the analysis of statistical data. A skilled industrial engineering engineer will be able help management make informed decisions to improve efficiency.
Typical tasks of an industrial engineering technician include: performing time and motion studies to enhance productivity, evaluating performance and implementing changes. They might also be asked to analyze data related to an industrial safety and health program.
Additionally, they are responsible for technical tasks like preparing diagrams and graphs to show the flow of a process. They also perform numerous quality tests on products to ensure they conform to standards.
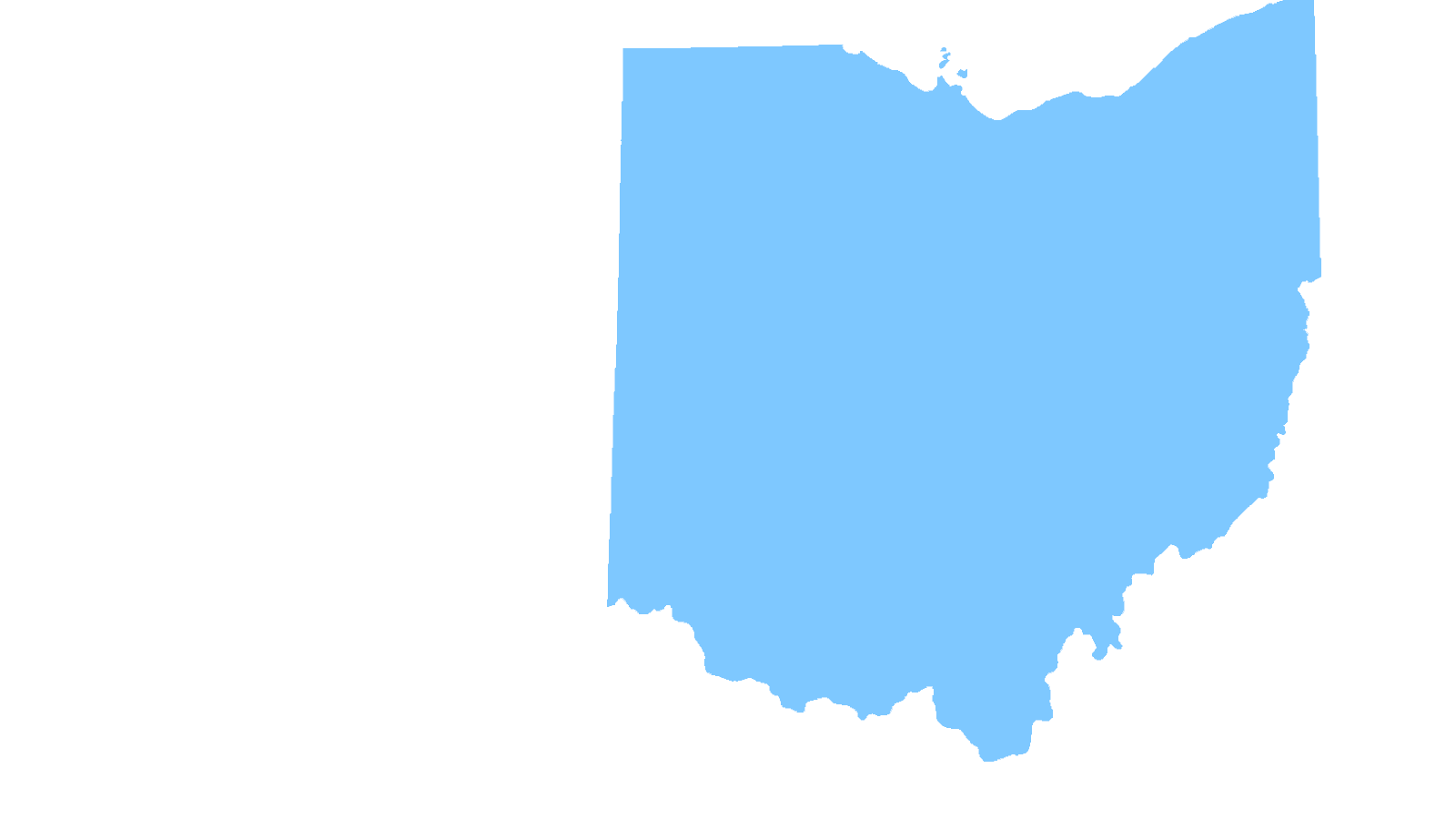
An industrial engineer's most common job duties include planning workflow, analyzing production costs and gauging prototypes. They also assess equipment capacities and develop efficient operating procedures. They can be found in a variety of industries, including aerospace, pharmaceuticals, electronics, food, and automotive. Most work full-time. The average annual salary for these workers is $53,000, although those with more education and experience might be able to make a better living.
There are no specific degrees required to become an industrial engineer. However, a strong math skills, critical thinking, and an eye for detail are vital. They should also be able communicate with and work with employees and observe the workplace processes.
A skilled industrial engineering technician will know how to identify the critical factors that affect the success of a workflow. For instance, they must be able to see the importance of reducing wasted materials and wasteful practices. This allows them to see the value of implementing improvements at work and can save money for the company.
They are likely to be the first to test new ideas in their company. This is possible by using a strategic outline. It's like fitting together the pieces of a giant puzzle.
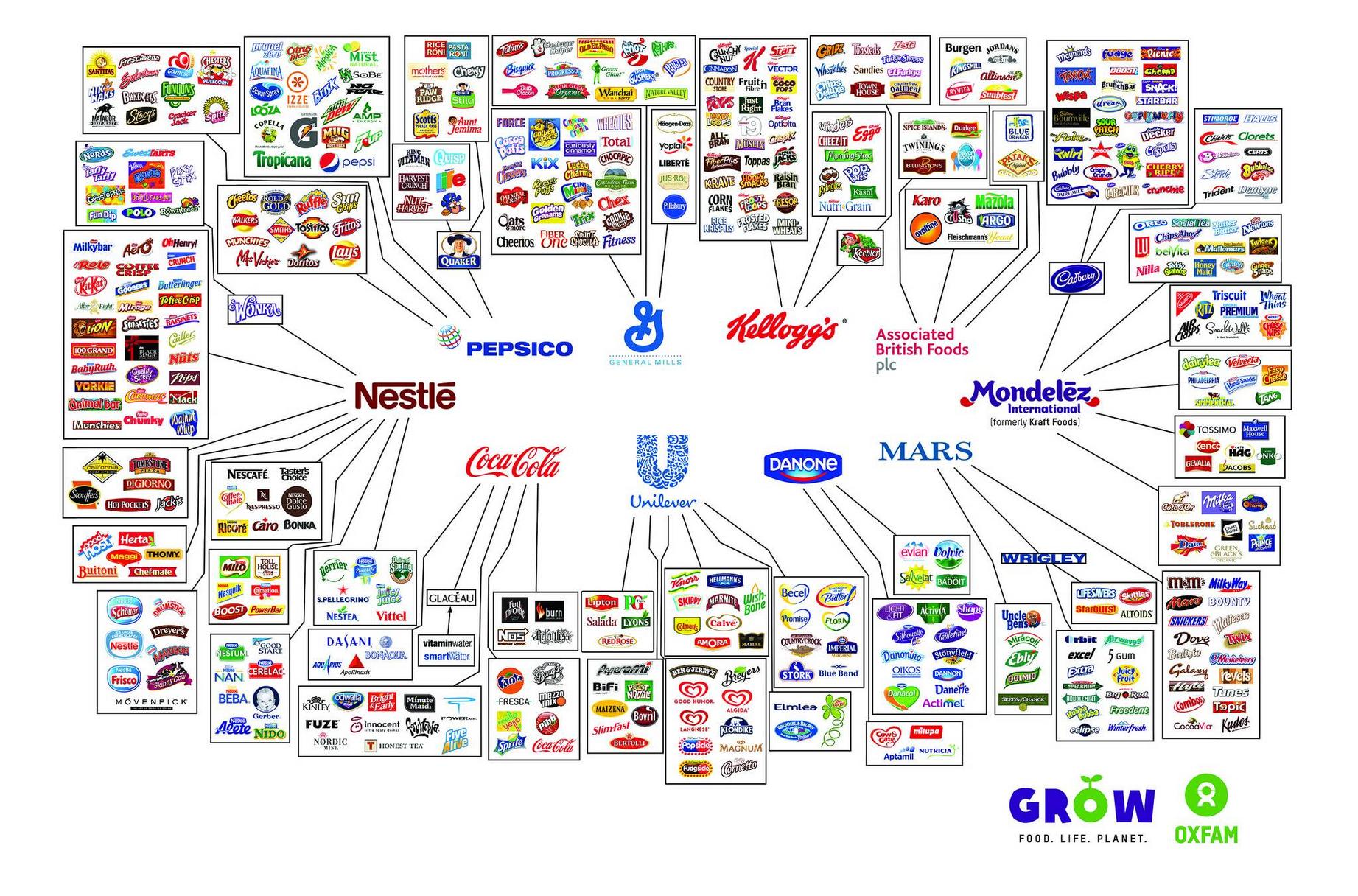
An industrial engineer can also improve the quality of output. This is another interesting job. While the number of jobs will be decreased by the increasing automation of industries, the role of industrial engineering technicians will be bolstered by a growing focus on cost control.
When it comes to the best way to measure the performance of a system, an engineer might choose to conduct a time and motion study to determine how long it takes to complete a task. This study could be used by engineers to establish a standard production level. These results can then be used for improvements in the operation's running.
Many universities offer an industrial engineering technology program, including Liberty University. This program offers a variety of courses that range from motor controls and hydraulics to self-management skills. The program helps students learn how to work together and problem solve.
FAQ
What are the responsibilities of a production planner
A production planner ensures all aspects of the project are delivered on time, within budget, and within scope. They also ensure that the product/service meets the client’s needs.
What is the role of a manager in manufacturing?
A manufacturing manager has to ensure that all manufacturing processes work efficiently and effectively. They must also be alert to any potential problems and take appropriate action.
They should also be able communicate with other departments, such as sales or marketing.
They must also keep up-to-date with the latest trends in their field and be able use this information to improve productivity and efficiency.
What do you mean by warehouse?
A warehouse or storage facility is where goods are stored before they are sold. It can be indoors or out. In some cases it could be both indoors and outdoors.
How can I find out more about manufacturing?
You can learn the most about manufacturing by getting involved in it. If that is not possible, you could always read books or view educational videos.
What are the 7 Rs of logistics.
The acronym 7R's for Logistics stands to represent the seven basic principles in logistics management. It was created by the International Association of Business Logisticians and published in 2004 under its "Seven Principles of Logistics Management".
The acronym consists of the following letters:
-
Responsive - ensure all actions are legal and not harmful to others.
-
Reliable - You can have confidence that you will fulfill your promises.
-
It is reasonable to use resources efficiently and not waste them.
-
Realistic – consider all aspects of operations, from cost-effectiveness to environmental impact.
-
Respectful - treat people fairly and equitably.
-
Responsive - Look for ways to save time and increase productivity.
-
Recognizable - provide customers with value-added services.
Is automation important for manufacturing?
Not only are service providers and manufacturers important, but so is automation. They can provide services more quickly and efficiently thanks to automation. It reduces human errors and improves productivity, which in turn helps them lower their costs.
Statistics
- Many factories witnessed a 30% increase in output due to the shift to electric motors. (en.wikipedia.org)
- It's estimated that 10.8% of the U.S. GDP in 2020 was contributed to manufacturing. (investopedia.com)
- [54][55] These are the top 50 countries by the total value of manufacturing output in US dollars for its noted year according to World Bank.[56] (en.wikipedia.org)
- Job #1 is delivering the ordered product according to specifications: color, size, brand, and quantity. (netsuite.com)
- In 2021, an estimated 12.1 million Americans work in the manufacturing sector.6 (investopedia.com)
External Links
How To
Six Sigma and Manufacturing
Six Sigma is defined by "the application SPC (statistical process control) techniques to achieve continuous improvements." It was developed by Motorola's Quality Improvement Department at their plant in Tokyo, Japan, in 1986. Six Sigma's basic concept is to improve quality and eliminate defects through standardization. This method has been adopted by many companies in recent years as they believe there are no perfect products or services. The main goal of Six Sigma is to reduce variation from the mean value of production. If you take a sample and compare it with the average, you will be able to determine how much of the production process is different from the norm. If the deviation is excessive, it's likely that something needs to be fixed.
Understanding the nature of variability in your business is the first step to Six Sigma. Once you have this understanding, you will need to identify sources and causes of variation. This will allow you to decide if these variations are random and systematic. Random variations occur when people make mistakes; systematic ones are caused by factors outside the process itself. For example, if you're making widgets, and some of them fall off the assembly line, those would be considered random variations. However, if you notice that every time you assemble a widget, it always falls apart at exactly the same place, then that would be a systematic problem.
Once you have identified the problem, you can design solutions. The solution could involve changing how you do things, or redesigning your entire process. You should then test the changes again after they have been implemented. If they don’t work, you’ll need to go back and rework the plan.