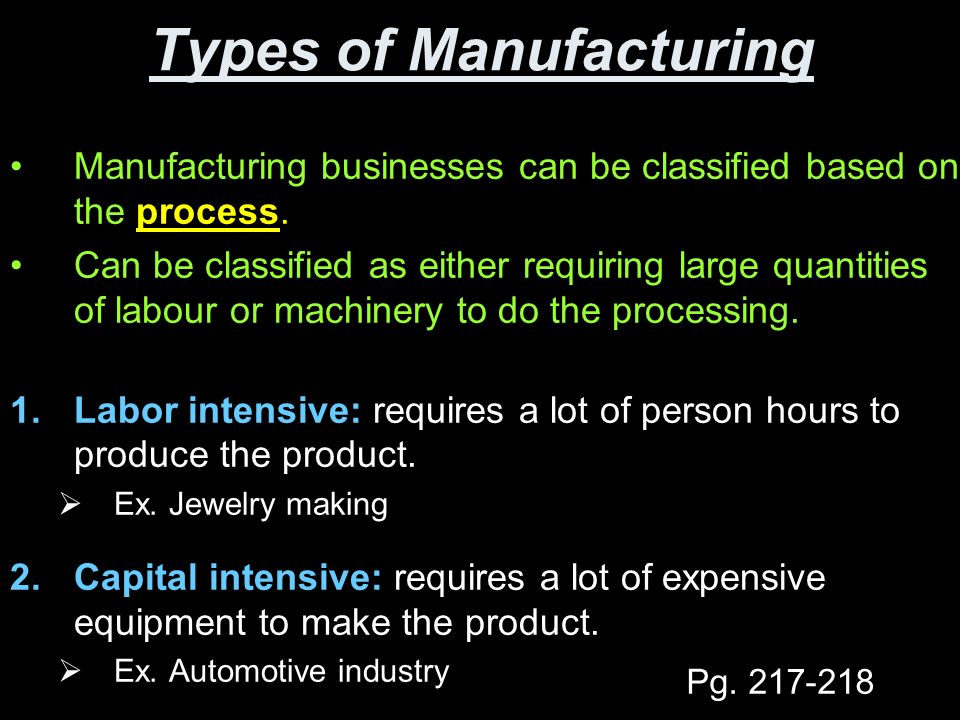
The director of manufacturing oversees the company's production process. They are responsible for overseeing all aspects of manufacturing, from design through to production. For this position to be successful, candidates must have experience in manufacturing and familiarity with new technologies. These technologies include 3D printing and robotics. These technologies are an asset for any director. As the manufacturing sector continues to develop, the director will find his or her role more complicated as he/she must coordinate with both engineering and operations. Quality control will also be a key focus.
Director of manufacturing: Salary
The salary of a Director of Manufacturing can vary depending on where they are located. Many directors are compensated in the low six-figure range, and some earn significantly more than others. The experience and education of a Director Manufacturing might also impact the salary. In order to determine how much you'll earn in your area, consider a few factors that may influence your salary:
The salary for a director of manufacturing varies but it's generally higher if you have more work experience. Like many other positions, salary can be affected by the cost of living or where you live. You will earn a higher salary if you live in a large city. However, your salary may not be sufficient to cover the cost of living. It is important that you are always willing to negotiate a higher salary when the opportunity arises.
The annual salary of a Director of Manufacturing Operations is between $181,500 to $66,000. The salary for a Director of Manufacturing Operations is highly variable and can vary by up to 8% between different cities. Fremont's director manufacturing operations can expect to earn $128.493 to $164.500. This makes Fremont, CA a significantly better place than the national average. However, salaries for Director of Manufacturing Operations vary depending on location, experience, and company.
Education Required
The director of manufacturing oversees the management and production of a facility. The director of manufacturing is responsible for hiring new workers, overseeing quality control, working with designers, as well as meeting operational standards. A director in manufacturing typically reports directly to the senior management team. This person executes policies and sales initiatives. Candidates must have experience in manufacturing and communicate well. Different companies have different requirements for directors of manufacturing.
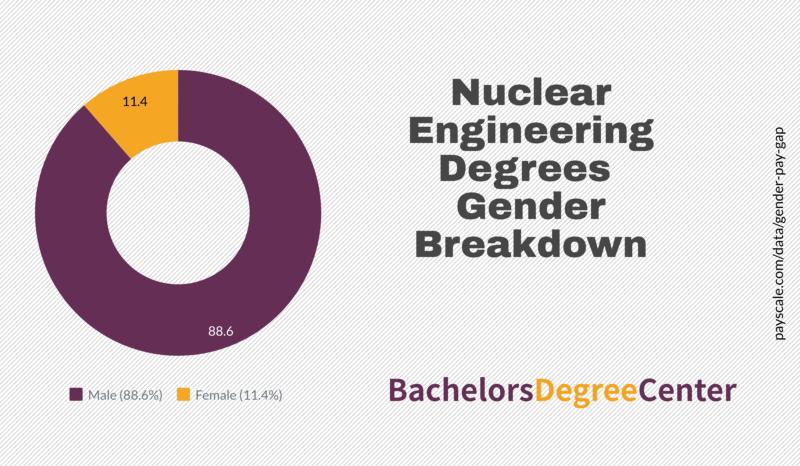
Although a graduate degree in engineering is not always required for director of manufacturing jobs, a post-secondary education in a related field will greatly enhance your skill set and knowledge base. A MBA in industrial management or business administration would be a great option for this job. It teaches candidates about economics, management, and organizational behavior. You will ultimately be responsible for managing diverse groups of people.
As a director manufacturing, you will closely work with designers and engineers in the product development phase. This stage will see you actively evaluate the feasibility of new processes, and ensure quality standards before committing resources for larger productions. In addition to overseeing the production process, successful directors serve as coaches for employees. They mentor their employees in risk mitigation and best practices. A manufacturing director must not only oversee the production process but also be able to solve problems.
Experience required
A bachelor's degree in a relevant field and five to 10 years of progressive work experience are often necessary for this position. Generally, manufacturing companies prefer to hire internal employees for this role. A strong understanding of the manufacturing process is essential. Employers may require a graduate degree. Candidates may also need additional training in the chosen industry or field.
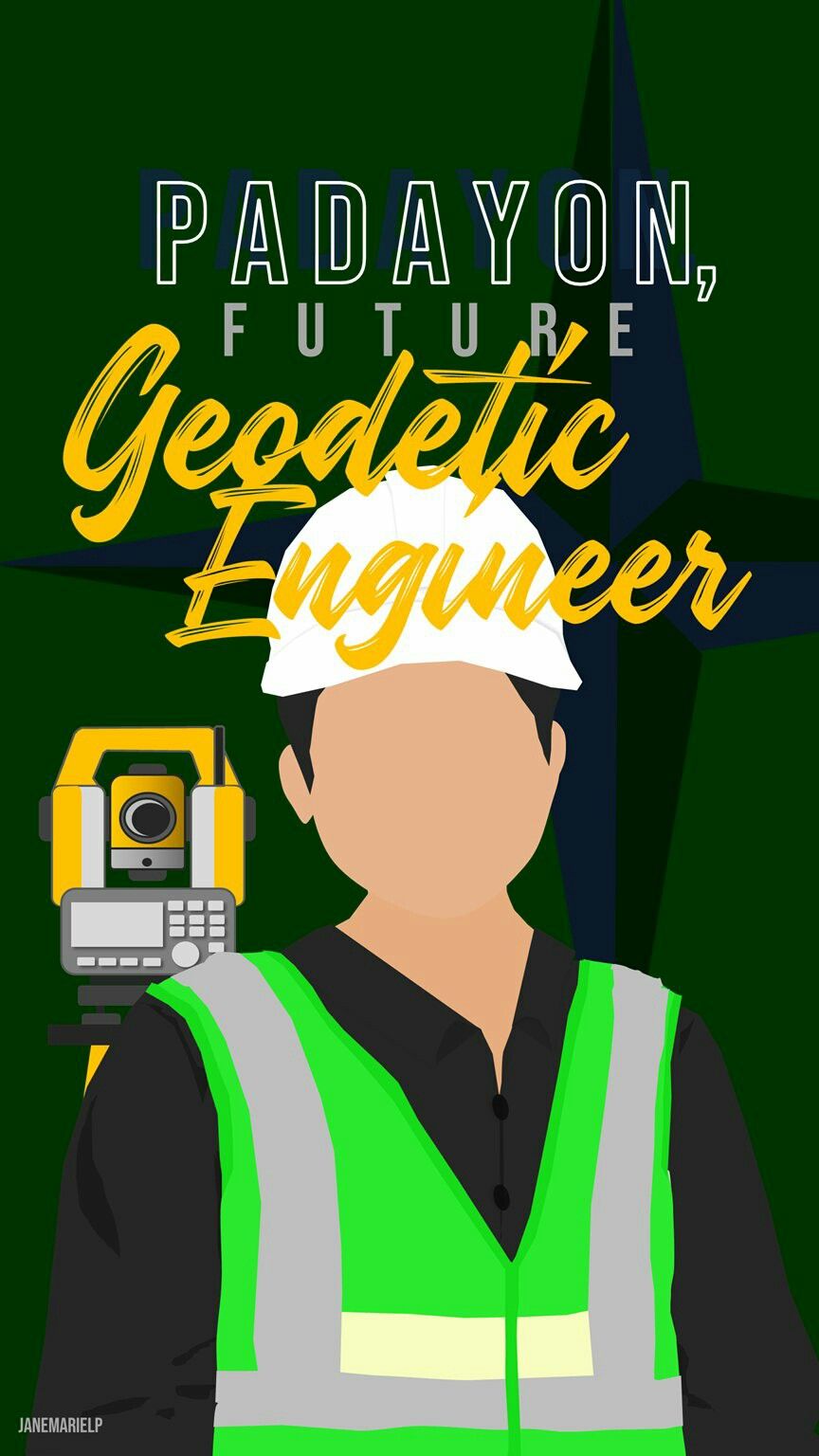
The production process is overseen by a director of manufacturing, which includes engineers, supervisors, workers, and other personnel. They could be responsible to solve problems and develop solutions. A director of manufacturing may not only oversee production but also develop and implement quality-control programs. The manufacturing director reports directly to the chief executive of the organization. Experience in manufacturing is essential. Experience in manufacturing management can help you succeed in this position.
Experience as a manufacturing director is essential. Directors must have at the least 10 years relevant experience working in a manufacturing environment. Some of these people may have started as manufacturing supervisors or technicians. They should also possess strong communication skills. A director of manufacturing should also have a thorough understanding of business strategy. A director of Manufacturing must also be able to communicate effectively with other departments. The director of manufacturing is responsible for overseeing production and ensuring it meets the highest quality standards.
FAQ
What are manufacturing and logistic?
Manufacturing refers the process of producing goods from raw materials through machines and processes. Logistics encompasses the management of all aspects associated with supply chain activities such as procurement, production planning, distribution and inventory control. It also includes customer service. Manufacturing and logistics can often be grouped together to describe a larger term that covers both the creation of products, and the delivery of them to customers.
What is production planning?
Production Planning includes planning for all aspects related to production. This document will ensure everything is in order and ready to go when you need it. This document should include information about how to achieve the best results on-set. This information includes locations, crew details and equipment requirements.
The first step is to outline what you want to film. You may already know where you want the film to be shot, or perhaps you have specific locations and sets you wish to use. Once you have identified your locations and scenes it's time to begin figuring out what elements you will need for each one. One example is if you are unsure of the exact model you want but decide that you require a car. This is where you can look up car models online and narrow down your options by choosing from different makes and models.
Once you have found the right vehicle, you can think about adding accessories. Are you looking for people to sit in the front seats? Or perhaps you need someone walking around the back of the car? You may want to change the interior's color from black or white. These questions will help guide you in determining the ideal look and feel for your car. You can also think about the type of shots you want to get. Do you want to film close-ups, or wider angles? Maybe you want to show the engine and the steering wheel. These factors will help you determine which car style you want to film.
Once you have established all the details, you can create a schedule. You will know when you should start and when you should finish shooting. The schedule will show you when to get there, what time to leave, and when to return home. Everyone knows exactly what they should do and when. Hire extra staff by booking them ahead of time. You don't want to hire someone who won't show up because he didn't know.
Your schedule will also have to be adjusted to reflect the number of days required to film. Some projects may only take a couple of days, while others could last for weeks. When creating your schedule, be aware of whether you need more shots per day. Multiple takes at the same place will result in higher costs and longer completion times. You can't be certain if you will need multiple takes so it is better not to shoot too many.
Budget setting is another important aspect in production planning. As it will allow you and your team to work within your financial means, setting a realistic budget is crucial. Keep in mind that you can always reduce your budget if you face unexpected difficulties. You shouldn't underestimate the amount you'll spend. You will end up spending less money if you underestimate the cost of something.
Planning production is a tedious process. Once you have a good understanding of how everything works together, planning future projects becomes easy.
Are there any Manufacturing Processes that we should know before we can learn about Logistics?
No. It doesn't matter if you don't know anything about manufacturing before you learn about logistics. Understanding the manufacturing process will allow you to better understand logistics.
Can some manufacturing processes be automated?
Yes! Yes! Automation has existed since ancient times. The Egyptians discovered the wheel thousands and years ago. Today, robots assist in the assembly of lines.
Actually, robotics can be used in manufacturing for many purposes. They include:
-
Line robots
-
Robot welding
-
Robot painting
-
Robotics inspection
-
Robots create products
Manufacturing can also be automated in many other ways. For example, 3D printing allows us to make custom products without having to wait for weeks or months to get them manufactured.
Statistics
- In the United States, for example, manufacturing makes up 15% of the economic output. (twi-global.com)
- According to the United Nations Industrial Development Organization (UNIDO), China is the top manufacturer worldwide by 2019 output, producing 28.7% of the total global manufacturing output, followed by the United States, Japan, Germany, and India.[52][53] (en.wikipedia.org)
- It's estimated that 10.8% of the U.S. GDP in 2020 was contributed to manufacturing. (investopedia.com)
- In 2021, an estimated 12.1 million Americans work in the manufacturing sector.6 (investopedia.com)
- (2:04) MTO is a production technique wherein products are customized according to customer specifications, and production only starts after an order is received. (oracle.com)
External Links
How To
How to use 5S to increase Productivity in Manufacturing
5S stands for "Sort", 'Set In Order", 'Standardize', & Separate>. Toyota Motor Corporation invented the 5S strategy in 1954. It helps companies achieve higher levels of efficiency by improving their work environment.
This method has the basic goal of standardizing production processes to make them repeatable. This means that daily tasks such as cleaning and sorting, storage, packing, labeling, and packaging are possible. Because workers know what they can expect, this helps them perform their jobs more efficiently.
Five steps are required to implement 5S: Sort, Set In Order, Standardize. Separate. Each step has a different action and leads to higher efficiency. By sorting, for example, you make it easy to find the items later. You arrange items by placing them in an order. Once you have separated your inventory into groups and organized them, you will store these groups in easily accessible containers. Finally, when you label your containers, you ensure everything is labeled correctly.
Employees need to reflect on how they do their jobs. Employees need to be able understand their motivations and discover alternative ways to do them. In order to use the 5S system effectively, they must be able to learn new skills.
The 5S method not only increases efficiency but also boosts morale and teamwork. They will feel motivated to strive for higher levels of efficiency once they start to see results.