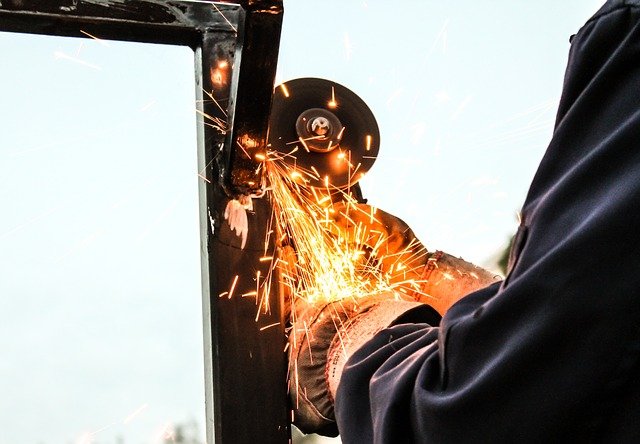
You're here because you are interested in a salary in biochemistry. This article will describe biochemical salaries at BOTHELL WA and San Mateo CA. You can explore the many biochemical salary options to help you get started with your career. Find out more about the requirements for salary and job descriptions at Worthington Biochemical as well as Youtell Biochemical. Both companies have BOTHELL, WA headquarters and offer competitive benefits.
Youtell Biochemical pay is $29 an Hour
Youtell Biochemical's average salary is $99,854. Salaries can range anywhere from $88,159 to $114,509. Salaries can range from $88,159 to $114,509 depending on the job, education and skills. Below are some examples of the types of jobs and salaries at Youtell Biochemical. Also, the salary ranges depend on education and previous experience.
Youtell Biochemical headquarters are located in BOTHELL WA
Youtell Biochemical, located in BOTHELL WA focuses its enzyme products business. They have a state of the art biotechnology research centre in Bothell and two downstream processing or fermentation factories in China. Those companies use patented technologies to produce enzyme products. Youtell Biochemical's main campus is located in BOTHELL WA and produces more than 80,000 tons of enzymes per year.
Worthington Biochemical, located in San Mateo CA
Worthington Biochemical was established in 1947. Charles Worthington was a Rockefeller Institute research assistant who had prepared crystalline enzymes for biochemical research. He soon realized that biochemical researchers needed reliable, high-purity proteins and that they would need to be purified by scientists. Worthington created its own company, Freehold, New Jersey in 1947, to provide these enzymes.
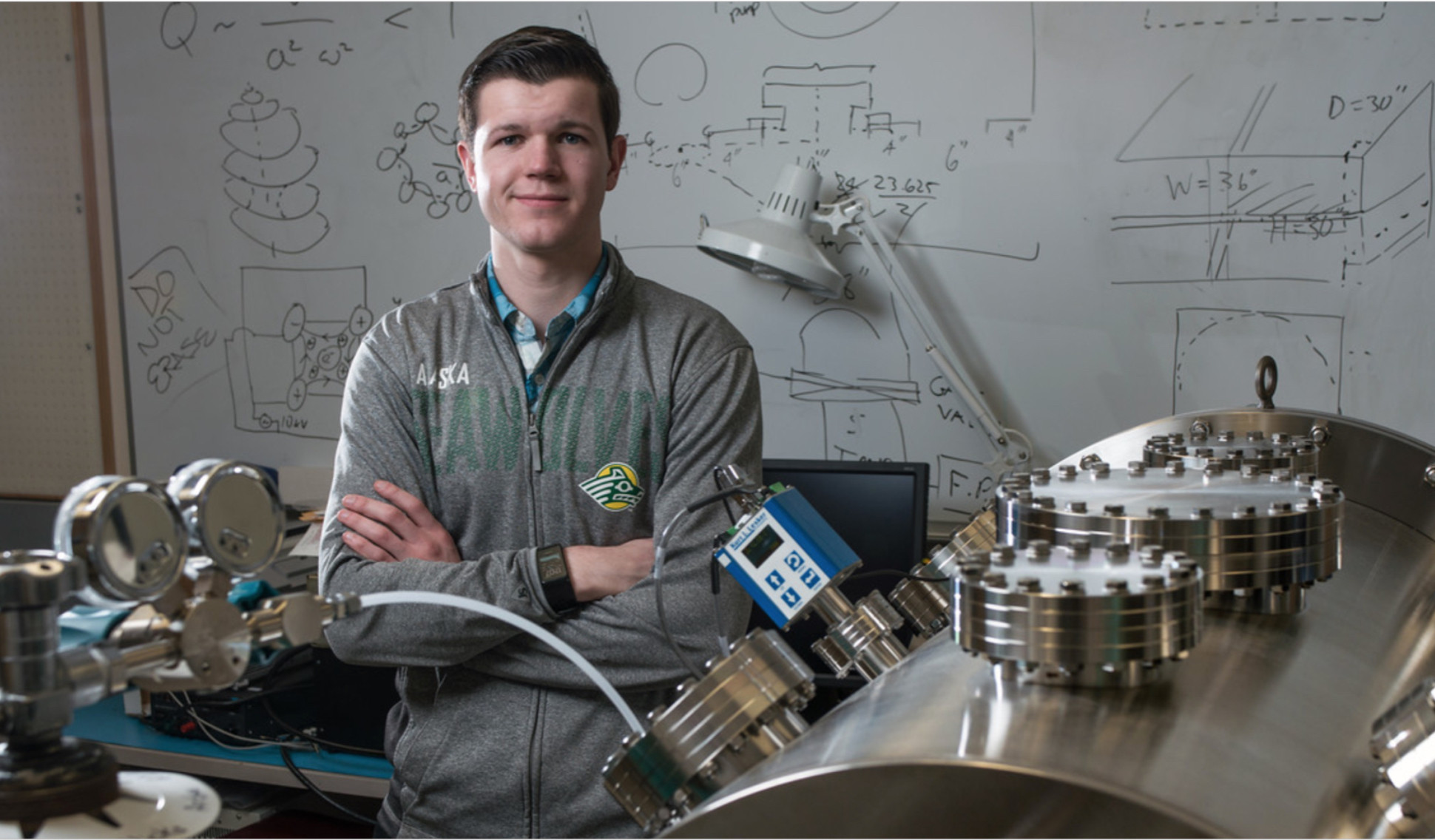
Worthington bought Cooper's Clinical Division in 1985. This was a biotech company based in New Jersey. Worthington's acquisition of the Clinical Division of Cooper, a biotech firm based in New Jersey, allowed it to expand its operations and allow it to concentrate more on the lucrative clinic market. The company failed to venture into the areas of molecular and immunology. Instead, it expanded its diagnostic kit manufacturing facility while investing less in enzyme production.
FAQ
What does it take for a logistics enterprise to succeed?
A successful logistics business requires a lot more than just knowledge. You must have good communication skills to interact effectively with your clients and suppliers. You need to understand how to analyze data and draw conclusions from it. You must be able manage stress and pressure under pressure. In order to innovate and create new ways to improve efficiency, creativity is essential. To motivate and guide your team towards reaching organizational goals, you must have strong leadership skills.
You should also be organized and efficient to meet tight deadlines.
What does it mean to be a manufacturer?
Manufacturing Industries are those businesses that make products for sale. Consumers are people who purchase these goods. This is accomplished by using a variety of processes, including production, distribution and retailing. They make goods from raw materials with machines and other equipment. This includes all types manufactured goods such as clothing, building materials, furniture, electronics, tools and machinery.
What type of jobs is there in logistics
There are many kinds of jobs available within logistics. Here are some examples:
-
Warehouse workers - They load trucks and pallets.
-
Transportation drivers: They drive trucks and trailers and deliver goods and make pick-ups.
-
Freight handlers: They sort and package freight in warehouses.
-
Inventory managers - These are responsible for overseeing the stock of goods in warehouses.
-
Sales representatives - They sell products.
-
Logistics coordinators are responsible for organizing and planning logistics operations.
-
Purchasing agents are those who purchase goods and services for the company.
-
Customer service agents - They answer phone calls and respond to emails.
-
Shipping clerks: They process shipping requests and issue bills.
-
Order fillers - These people fill orders based on what has been ordered.
-
Quality control inspectors are responsible for inspecting incoming and outgoing products looking for defects.
-
Others - There are many types of jobs in logistics such as transport supervisors and cargo specialists.
What are the main products of logistics?
Logistics are the activities involved in moving goods from point A to point B.
They cover all aspects of transportation, such as packing, loading, transporting and unloading.
Logisticians ensure that the product is delivered to the correct place, at the right time, and under safe conditions. They provide information on demand forecasts as well stock levels, production schedules and availability of raw material.
They coordinate with vendors and suppliers, keep track of shipments, monitor quality standards and perform inventory and order replenishment.
What is the importance of logistics in manufacturing?
Logistics are an essential part of any business. They can help you achieve great success by helping you manage product flow from raw material to finished goods.
Logistics are also important in reducing costs and improving efficiency.
How does a production planner differ from a project manager?
The difference between a product planner and project manager is that a planer is typically the one who organizes and plans the entire project. A production planner, however, is mostly involved in the planning stages.
Statistics
- Many factories witnessed a 30% increase in output due to the shift to electric motors. (en.wikipedia.org)
- According to a Statista study, U.S. businesses spent $1.63 trillion on logistics in 2019, moving goods from origin to end user through various supply chain network segments. (netsuite.com)
- You can multiply the result by 100 to get the total percent of monthly overhead. (investopedia.com)
- (2:04) MTO is a production technique wherein products are customized according to customer specifications, and production only starts after an order is received. (oracle.com)
- In 2021, an estimated 12.1 million Americans work in the manufacturing sector.6 (investopedia.com)
External Links
How To
How to Use 5S for Increasing Productivity in Manufacturing
5S stands in for "Sort", the "Set In Order", "Standardize", or "Separate". Toyota Motor Corporation invented the 5S strategy in 1954. It helps companies achieve higher levels of efficiency by improving their work environment.
This approach aims to standardize production procedures, making them predictable, repeatable, and easily measurable. It means tasks like cleaning, sorting or packing, labeling, and storing are done every day. Through these actions, workers can perform their jobs more efficiently because they know what to expect from them.
There are five steps to implementing 5S, including Sort, Set In Order, Standardize, Separate and Store. Each step has a different action and leads to higher efficiency. Sorting things makes it easier to find them later. When items are ordered, they are put together. Next, organize your inventory into categories and store them in containers that are easily accessible. Labeling your containers will ensure that everything is correctly labeled.
This process requires employees to think critically about how they do their job. Employees should understand why they do the tasks they do, and then decide if there are better ways to accomplish them. They must learn new skills and techniques in order to implement the 5S system.
In addition to increasing efficiency, the 5S method also improves morale and teamwork among employees. They will feel motivated to strive for higher levels of efficiency once they start to see results.