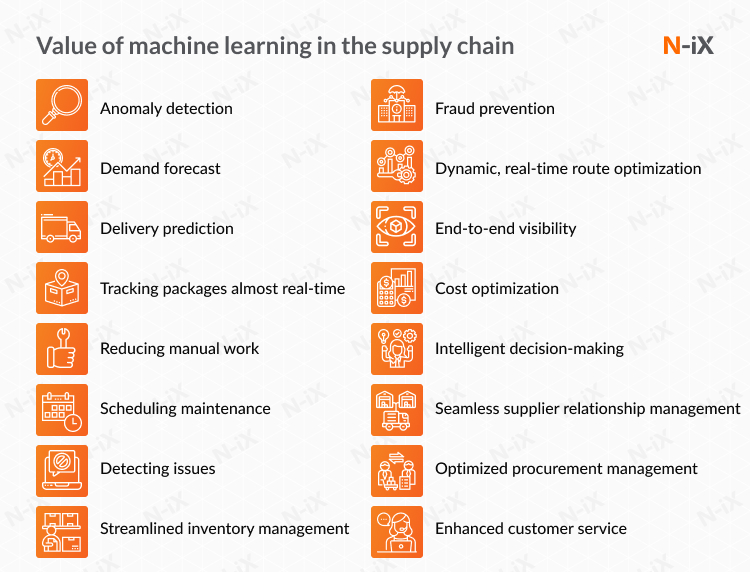
Supply chain disruptions across industries have led to long-term productivity losses and economic losses. Companies' inept risk management is a contributing factor to these disruptions.
In the face of growing internationalization, the defence industry has been affected by this trend. Several technologies, including high-quality carbon fibre and advanced semi-conductors, may run out of supplies. This can lead to increased reliance on foreign capital and oligopolistic behavior. Additionally, dual products are more likely to be used. These products can pose safety and reliability concerns.
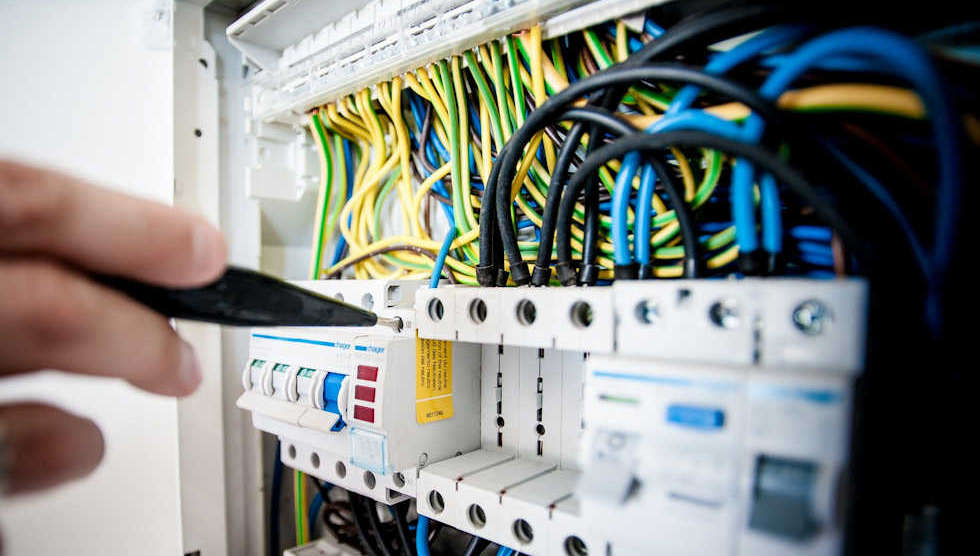
In the face of globalization, the security of critical minerals is critical to the development of modern industrial systems. Some minerals are distributed in economically underdeveloped countries and can be vulnerable to political instability. Under different circumstances, the optimal global allocation for critical minerals can change. China is a pivotal node within the global critical materials value chain. But, the industry relies heavily on other countries. It is important that governments establish a global critical metal allocation network that includes multiple nations, instead of concentrating resources within a single nation.
European Union (EU), is currently engaged in discussions regarding its defense technology, industrial base (DTIB). The European Commission launched the European Defence Agency, (EDA), to create a framework that will allow for a new European defense industry. This new approach will lead to a lot of changes in the EU’s defence industry. For example, certain technologies can only be supplied by a limited number of non-EU companies. There will also be monopoly structures as well as oligopoly structure in the EU's defence industry. Furthermore, it will be much easier to purchase raw materials from non EU firms. This will open the door to a new type, called bundled volume.
An increased emphasis is placed on the creation of a secure supply chain. There are a number of strategies that can be implemented to mitigate the risk of supply chain disruptions. One strategy is the implementation of a formal risk-management approach. Investing in a formal approach to risk management can allow supply chains to flourish, not just survive. It should involve both internal and external key stakeholders, including suppliers, investors and governments. Management of the supply chain should be in line with global supply-chain dynamics.
Security of the 99 Mo/99mtc supply chain is another important policy issue. The policy approach developed by the High-Level Group on Medical Radioisotopes (HLG-MR) ensures the long-term security of the supply of these radioisotopes. This included a review the global 99 M/99 M Tc supply chain, analysis of the economic effects of the supply, as well a policy approach.
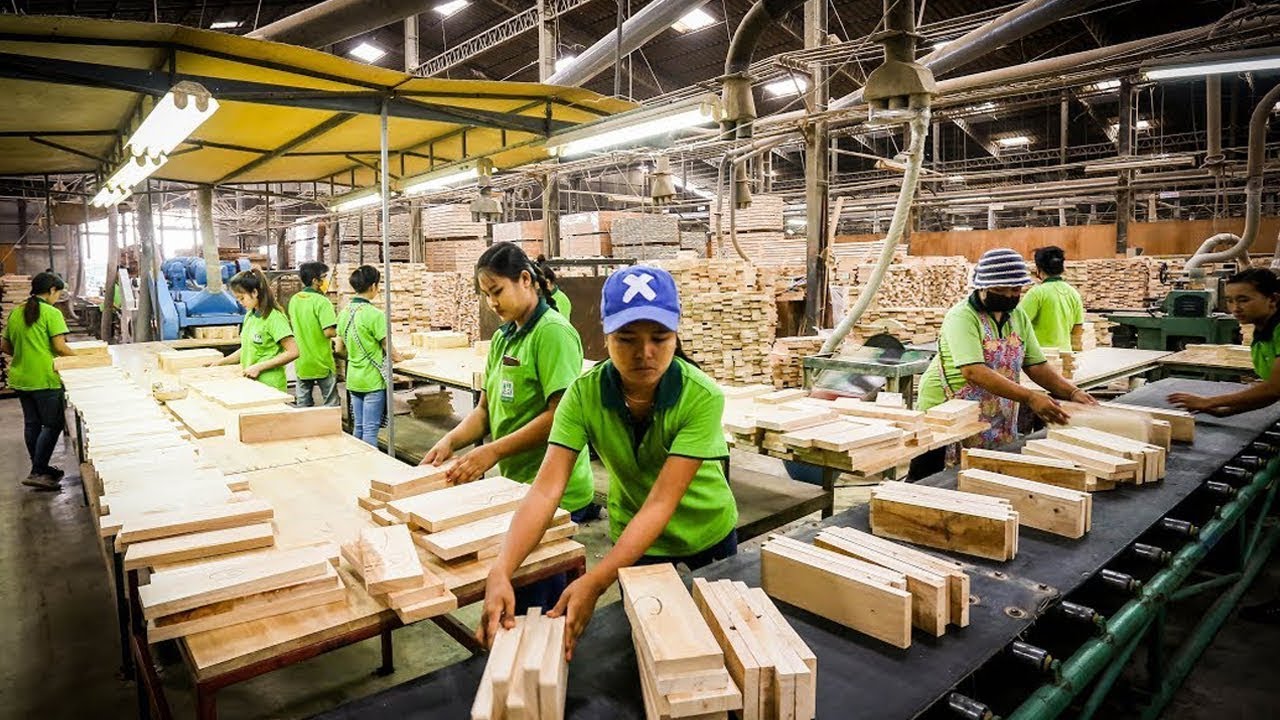
HLG-MR identified 2 main areas of vulnerability which should be addressed to improve the security of the 99m/99m supply chains. These areas include monopolistic behavior as well as foreign capital. These factors can result in significant price increases and risks. HLG-MR's policy approach also identified key steps to address these vulnerabilities.
FAQ
What skills do production planners need?
To become a successful production planner, you need to be organized, flexible, and able to multitask. It is also important to be able communicate with colleagues and clients.
How can we improve manufacturing efficiency?
First, determine which factors have the greatest impact on production time. Then we need to find ways to improve these factors. If you don’t know where to begin, consider which factors have the largest impact on production times. Once you have identified them, it is time to identify solutions.
What is the role of a logistics manager
Logistics managers are responsible for ensuring that all goods arrive in perfect condition and on time. This is accomplished by using the experience and knowledge gained from working with company products. He/she also needs to ensure adequate stock to meet demand.
Statistics
- Many factories witnessed a 30% increase in output due to the shift to electric motors. (en.wikipedia.org)
- Job #1 is delivering the ordered product according to specifications: color, size, brand, and quantity. (netsuite.com)
- According to the United Nations Industrial Development Organization (UNIDO), China is the top manufacturer worldwide by 2019 output, producing 28.7% of the total global manufacturing output, followed by the United States, Japan, Germany, and India.[52][53] (en.wikipedia.org)
- In 2021, an estimated 12.1 million Americans work in the manufacturing sector.6 (investopedia.com)
- According to a Statista study, U.S. businesses spent $1.63 trillion on logistics in 2019, moving goods from origin to end user through various supply chain network segments. (netsuite.com)
External Links
How To
Six Sigma in Manufacturing
Six Sigma refers to "the application and control of statistical processes (SPC) techniques in order to achieve continuous improvement." It was developed by Motorola's Quality Improvement Department at their plant in Tokyo, Japan, in 1986. The basic idea behind Six Sigma is to improve quality by improving processes through standardization and eliminating defects. This method has been adopted by many companies in recent years as they believe there are no perfect products or services. Six Sigma aims to reduce variation in the production's mean value. You can calculate the percentage of deviation from the norm by taking a sample of your product and comparing it to the average. If the deviation is excessive, it's likely that something needs to be fixed.
Understanding how your business' variability is a key step towards Six Sigma implementation is the first. Once you have a good understanding of the basics, you can identify potential sources of variation. These variations can also be classified as random or systematic. Random variations are caused when people make mistakes. While systematic variations are caused outside of the process, they can occur. These are, for instance, random variations that occur when widgets are made and some fall off the production line. You might notice that your widgets always fall apart at the same place every time you put them together.
After identifying the problem areas, you will need to devise solutions. That solution might involve changing the way you do things or redesigning the process altogether. Once you have implemented the changes, it is important to test them again to ensure they work. If they don't work you need to rework them and come up a better plan.