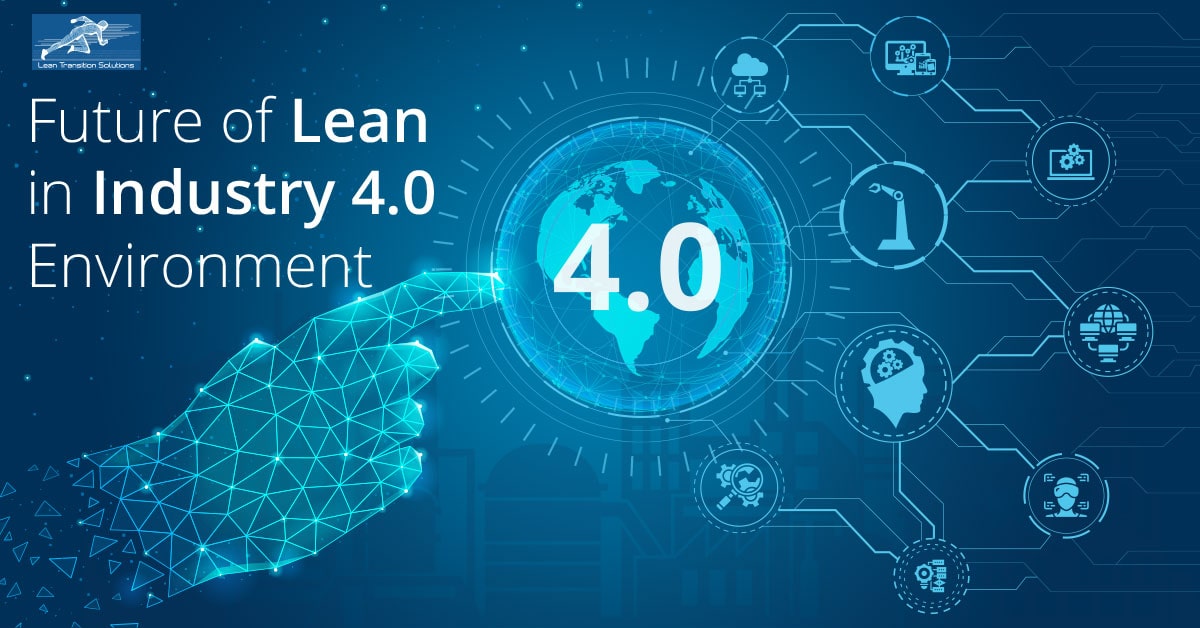
If you're looking for news about manufacturing, you've come to the right place. Fusion 360 community members recap the week's events and share news about manufacturing innovation. Fusion 360 covers all aspects of the industry, including Alexandria Industries and Festo's expansion plans. Fusion 360 covers everything from the latest product launches, to news about additive production. Here are some recent articles regarding manufacturing innovation. Read on to learn more.
Alexandria Industries
Alexandria Industries recently announced that they are expanding their operations in Douglas County. They have 480 employees and are currently investing several million in new facilities to grow. Although Alexandria Industries has long outpaced employment and revenue levels prior to the recession, they still struggle to find qualified applicants for 50 new jobs. These positions pay $15-30 an hour, plus benefits. Alexandria Industries is looking for a new career.
Alexandria Industries recently hired new management to help them grow. Jonathan D. Olson, Alexandria Industries' CFO, was previously employed. He will now be its CFO. He is determined to make investments in the company, and the people who work there. He also joined the company as its new CFO, and is planning to improve the working conditions of employees and invest in training programs. The new acquisition will expand the company's capabilities by integrating the operations of Alexandria Plastics, Inc., a manufacturer of plastic injection and foam-molded components.
Festo U.S. expansion plans
Festo Corp. has announced plans to expand its North American manufacturing operations. The company will expand its Mason operations by doubling the size and creating 350 jobs. The expansion will be $90 million in cost and create 350 new jobs over the next five year. Festo will also provide support services and industrial training solutions. A new Didactic Learning Centre will be added to the expansion, which will serve colleges and manufacturing companies throughout the Tristate region.
The new Mason facility will be used to produce automation components. The new facility will be home to both a Research and Development Center and Global Production Center. Upon completion, both will employ more than 1,000 people. The company will create new jobs as well as a new research center to develop automation systems. This expansion is part the company's larger plan to target the U.S. market.
Additive Manufacturing
Manufacturers are beginning to recognize the advantages of additive manufacturing in their manufacturing processes, thanks to technological advancements. Recently, a number of companies have announced partnerships with one another to help them reach the global market. Voxeljet has partnered with AGC Ceramic, which is a ceramic and glass company. Voxeljet will introduce Brightorb ceramic material and the VX1000 to be used for 3D printing ceramic powder. AGC Ceramic also plans to partner with Voxeljet. Other partnerships include Stratasys, which has partnered with Tata Technologies to promote additive manufacturing technologies in India.
New technologies are being developed to aid in the additive manufacturing process. Optimus 3D recently acquired a fourth Renishaw Metal additive manufacturing system. The company has also expanded the range of 3D printers to include metal powder. This development will ensure that additive manufacturing becomes an integral part advanced PLM. Advanced PLM will be more IoT-oriented, integrated, and flexible. These innovations will facilitate the rapid growth and diversification of many industries.
Collaborative manufacturing
What is collaborative manufacturing? Collaborative manufacture involves input directly from plant floor system. This information is important for the management process. It involves both the design and manufacturing teams working together. Collaborative Manufacturing can improve productivity, quality, and reduce the number required to perform each production process. What are the advantages of collaborative manufacturing? Let's examine a few. How collaborative manufacturing can improve plant performance. Learn more.
Collaboration is a growing trend in many industries. It's used to increase product design, streamline logistics, and help with product development. Collaboration in manufacturing reduces time-to-market, volume, and can speed up manufacturing cycles among suppliers. Recognizing the benefits of collaborative manufacturing for all stakeholders is critical for companies. This isn't for every company. Consider the advantages of collaborative manufacturing before you make the leap to it.
FAQ
Is automation necessary in manufacturing?
Not only are service providers and manufacturers important, but so is automation. Automation allows them to deliver services quicker and more efficiently. In addition, it helps them reduce costs by reducing human errors and improving productivity.
Why is logistics important in manufacturing?
Logistics are an integral part any business. They are essential to any business's success.
Logistics play a key role in reducing expenses and increasing efficiency.
Why automate your warehouse
Modern warehousing has seen automation take center stage. The rise of e-commerce has led to increased demand for faster delivery times and more efficient processes.
Warehouses must adapt quickly to meet changing customer needs. Technology is essential for warehouses to be able to adapt quickly to changing needs. Automating warehouses is a great way to save money. These are some of the benefits that automation can bring to warehouses:
-
Increases throughput/productivity
-
Reduces errors
-
Increases accuracy
-
Safety Boosts
-
Eliminates bottlenecks
-
This allows companies to scale easily
-
It makes workers more efficient
-
This gives you visibility into what happens in the warehouse
-
Enhances customer experience
-
Improves employee satisfaction
-
Reduces downtime and improves uptime
-
This ensures that quality products are delivered promptly
-
Human error can be eliminated
-
Assure compliance with regulations
Statistics
- In 2021, an estimated 12.1 million Americans work in the manufacturing sector.6 (investopedia.com)
- According to a Statista study, U.S. businesses spent $1.63 trillion on logistics in 2019, moving goods from origin to end user through various supply chain network segments. (netsuite.com)
- In the United States, for example, manufacturing makes up 15% of the economic output. (twi-global.com)
- According to the United Nations Industrial Development Organization (UNIDO), China is the top manufacturer worldwide by 2019 output, producing 28.7% of the total global manufacturing output, followed by the United States, Japan, Germany, and India.[52][53] (en.wikipedia.org)
- Many factories witnessed a 30% increase in output due to the shift to electric motors. (en.wikipedia.org)
External Links
How To
How to use the Just In-Time Production Method
Just-intime (JIT), a method used to lower costs and improve efficiency in business processes, is called just-in-time. This is where you have the right resources at the right time. This means you only pay what you use. Frederick Taylor, a 1900s foreman, first coined the term. After observing how workers were paid overtime for late work, he realized that overtime was a common practice. He decided that workers would be more productive if they had enough time to complete their work before they started to work.
JIT is an acronym that means you need to plan ahead so you don’t waste your money. Also, you should look at the whole project from start-to-finish and make sure you have the resources necessary to address any issues. If you anticipate that there might be problems, you'll have enough people and equipment to fix them. This will prevent you from spending extra money on unnecessary things.
There are many JIT methods.
-
Demand-driven JIT: This is a JIT that allows you to regularly order the parts/materials necessary for your project. This will let you track the amount of material left over after you've used it. This will let you know how long it will be to produce more.
-
Inventory-based: This type allows you to stock the materials needed for your projects ahead of time. This allows you to predict how much you can expect to sell.
-
Project-driven : This is a method where you make sure that enough money is set aside to pay the project's cost. You will be able to purchase the right amount of materials if you know what you need.
-
Resource-based JIT: This type of JIT is most commonly used. Here you can allocate certain resources based purely on demand. You might assign more people to help with orders if there are many. You'll have fewer orders if you have fewer.
-
Cost-based: This is the same as resource-based except that you don't care how many people there are but how much each one of them costs.
-
Price-based: This approach is very similar to the cost-based method except that you don't look at individual workers costs but the total cost of the company.
-
Material-based: This approach is similar to cost-based. However, instead of looking at the total cost for the company, you look at how much you spend on average on raw materials.
-
Time-based JIT is another form of resource-based JIT. Instead of focusing only on how much each employee is costing, you should focus on how long it takes to complete your project.
-
Quality-based JIT - This is another form of resource-based JIT. Instead of thinking about the cost of each employee or the time it takes to produce something, you focus on how good your product quality.
-
Value-based JIT: One of the most recent forms of JIT. In this case, you're not concerned with how well the products perform or whether they meet customer expectations. Instead, you focus on the added value that you provide to your market.
-
Stock-based is an inventory-based system that measures the number of items produced at any given moment. It is used when production goals are met while inventory is kept to a minimum.
-
Just-intime planning (JIT), is a combination JIT/sales chain management. It is the process that schedules the delivery of components within a short time of their order. It reduces lead times and improves throughput.