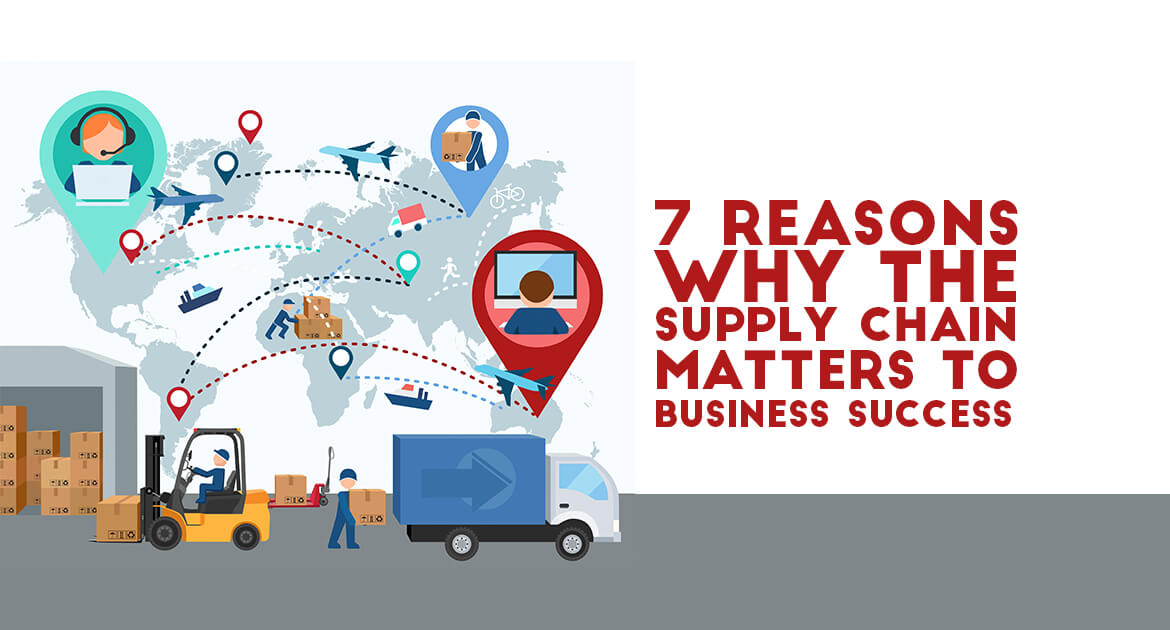
Six-Sigma and lean are complementary approaches to improving processes. Although they both have the same tools for problem solving, each has its strengths and weaknesses. Six-Sigma is a statistical process control technique, and Lean starts with the premise that a product must add value, not just produce it. The key to Lean is to eliminate waste and improve the quality of the product as it is being produced.
Problem solving regarding PDCA
Although there are differences in DMAIC problem solving and PDCA, they both use the DMAIC approach. The PDCA cycle is more complex and requires more analysis. Unlike DMAIC, PDCA is not effective for solving urgent problems. This approach requires technical skills and a lead problem-solver. Six Sigma's problem-solving leader will need to be a Six Sigma "green belt" practitioner.
In Six Sigma, problem-solving follows a cycle that was first introduced in the 1950s by W. Edwards Deming. Its creators intended to use it in conjunction with continuous improvement methods to help rebuild Japan's industries. Real data must be collected and a clear mission statement must created in the P (Plan). After the PDCA, the team should decide on a suggested solution.
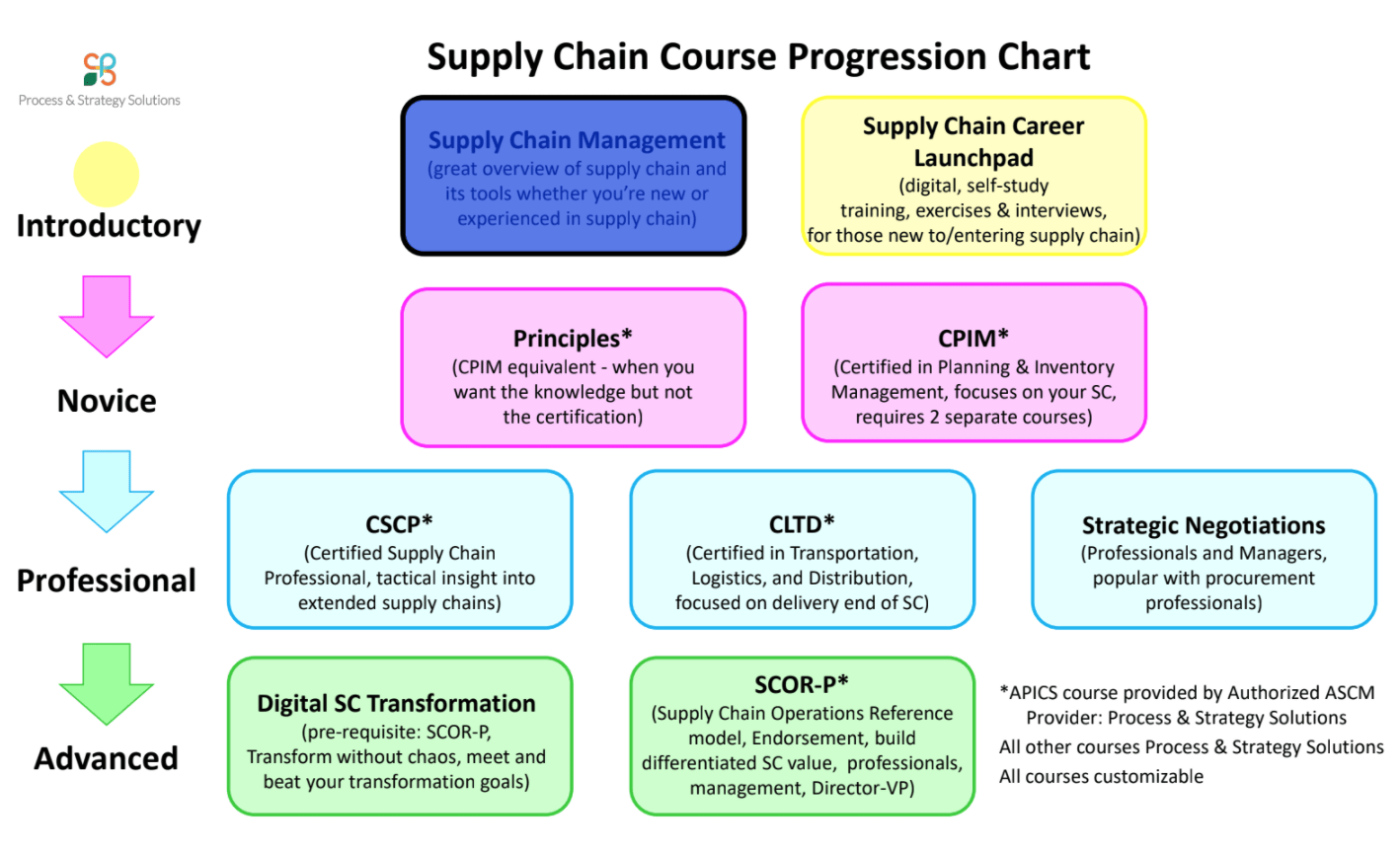
Process maps
The way that each approach describes the process is a key difference between Six Sigma and Lean processes maps. Both methods focus on defining the process in detail but each approach focuses more on different aspects. For example, Lean involves mapping actual processes instead of standard operating procedures. Make sure to include major activities, decisions, approvals, and other sources of approval when creating process maps. Include areas where you use multiple methods and factors that may obstruct members. Match roles carefully and examine the flow of the process.
A process map should have steps, symbols and arrows that show the flow of a particular process. To ensure that each process accurately depicts the actual process, several people should review it. Also, a process map should include the date it was created and who to contact if there are any questions. Process maps can be a great way to improve any process. They may also be complex.
Analyse of cause and effect
Six Sigma, lean project management techniques are based on statistical analysis. The Cause and Effect Matrix or CAE is a method that links the outputs and inputs of a process. The customer's requirements are listed according to their importance. Outputs and inputs are ranked according the effect on the outcome. Key process input variables and their ranking should be determined.
While each technique brings unique benefits, they are all not the same. Lean Six Sigma is based on Frederick Winslow Taylor’s Principles of Scientific Management. Taylor saw business as interconnected workflows and processes. He recommended reducing variability as well. Six-Sigma and Lean complement each other in the reduction of waste.
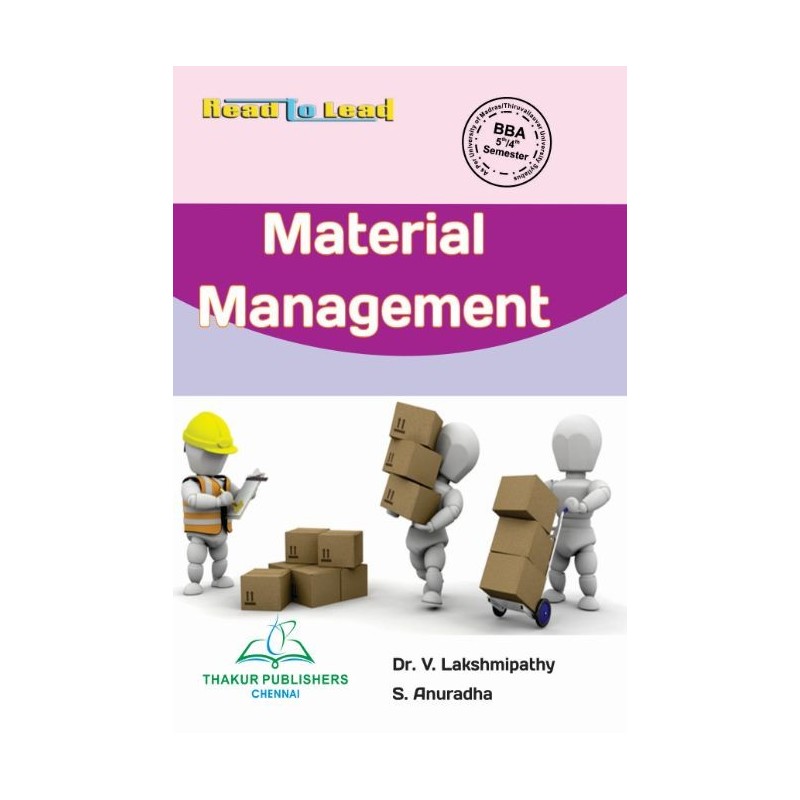
Elimination of variation
Variability is a normal part of any manufacturing process. Variability in manufacturing processes can cause uncertainty regarding the outcome. Consistency is essential to provide professional results. Predictable output is achieved by eliminating variation in Six Sigma and Lean manufacturing processes. Although some variation is normal, excessive variation can lead to problems, rework, or even worse, business consequences. It is best to identify the root causes of variation.
The first place to look for variations is at decision points. Process maps show decision points and are represented by diamonds. Six Sigma teams can start by identifying decision points and start eliminating variations there. This information is obtained directly from the Six Sigma process owner. The Six Sigma team will not be able to focus if the process owner does not follow a standard procedure. In this case, a process map may not be effective unless the Six Sigma team has sufficient technical capacity to make necessary adjustments.
FAQ
How can we reduce manufacturing overproduction?
Improved inventory management is the key to reducing overproduction. This would decrease the time that is spent on inefficient activities like purchasing, storing, or maintaining excess stock. This could help us free up our time for other productive tasks.
This can be done by using a Kanban system. A Kanban board, a visual display to show the progress of work, is called a Kanban board. Kanban systems allow work items to move through different states until they reach their final destination. Each state represents a different priority.
If work is moving from one stage to the other, then the current task can be completed and moved on to the next. It is possible to keep a task in the beginning stages until it gets to the end.
This keeps work moving and ensures no work is lost. Managers can view the Kanban board to see how much work they have done. This allows them to adjust their workflows based on real-time information.
Lean manufacturing is another way to manage inventory levels. Lean manufacturing seeks to eliminate waste from every step of the production cycle. Anything that doesn't add value to the product is considered waste. These are some of the most common types.
-
Overproduction
-
Inventory
-
Packaging that is not necessary
-
Excess materials
These ideas can help manufacturers improve efficiency and reduce costs.
How can manufacturing efficiency improved?
First, identify the factors that affect production time. Then we need to find ways to improve these factors. If you don’t know where to begin, consider which factors have the largest impact on production times. Once you have identified the factors, then try to find solutions.
What jobs are available in logistics?
There are different kinds of jobs available in logistics. Some of them are:
-
Warehouse workers - They load and unload trucks and pallets.
-
Transportation drivers – They drive trucks or trailers to transport goods and perform pick-ups.
-
Freight handlers, - They sort out and pack freight in warehouses.
-
Inventory managers – These people oversee inventory at warehouses.
-
Sales reps - They sell products and services to customers.
-
Logistics coordinators - They plan and organize logistics operations.
-
Purchasing agents are those who purchase goods and services for the company.
-
Customer service representatives - They answer calls and emails from customers.
-
Ship clerks - They issue bills and process shipping orders.
-
Order fillers: They fill orders based off what has been ordered and shipped.
-
Quality control inspectors are responsible for inspecting incoming and outgoing products looking for defects.
-
Others - There are many types of jobs in logistics such as transport supervisors and cargo specialists.
What are the responsibilities of a logistic manager?
Logistics managers are responsible for ensuring that all goods arrive in perfect condition and on time. This is accomplished by using the experience and knowledge gained from working with company products. He/she should also ensure enough stock is available to meet demand.
What is the difference between Production Planning and Scheduling?
Production Planning (PP), or production planning, is the process by which you determine what products are needed at any given time. Forecasting demand is one way to do this.
Scheduling involves the assignment of dates and times to tasks in order to complete them within the timeframe.
Statistics
- In the United States, for example, manufacturing makes up 15% of the economic output. (twi-global.com)
- (2:04) MTO is a production technique wherein products are customized according to customer specifications, and production only starts after an order is received. (oracle.com)
- Job #1 is delivering the ordered product according to specifications: color, size, brand, and quantity. (netsuite.com)
- In 2021, an estimated 12.1 million Americans work in the manufacturing sector.6 (investopedia.com)
- [54][55] These are the top 50 countries by the total value of manufacturing output in US dollars for its noted year according to World Bank.[56] (en.wikipedia.org)
External Links
How To
How to Use Lean Manufacturing for the Production of Goods
Lean manufacturing is a management system that aims at increasing efficiency and reducing waste. It was developed in Japan during the 1970s and 1980s by Taiichi Ohno, who received the Toyota Production System (TPS) award from TPS founder Kanji Toyoda. Michael L. Watkins published the first book on lean manufacturing in 1990.
Lean manufacturing can be described as a set or principles that are used to improve quality, speed and cost of products or services. It emphasizes eliminating waste and defects throughout the value stream. Lean manufacturing is called just-in-time (JIT), zero defect, total productive maintenance (TPM), or 5S. Lean manufacturing eliminates non-value-added tasks like inspection, rework, waiting.
Lean manufacturing is a way for companies to achieve their goals faster, improve product quality, and lower costs. Lean manufacturing can be used to manage all aspects of the value chain. Customers, suppliers, distributors, retailers and employees are all included. Lean manufacturing is widely practiced in many industries around the world. Toyota's philosophy has been a key driver of success in many industries, including automobiles and electronics.
Lean manufacturing includes five basic principles:
-
Define Value: Identify the social value of your business and what sets you apart.
-
Reduce waste - Get rid of any activity that does not add value to the supply chain.
-
Create Flow: Ensure that the work process flows without interruptions.
-
Standardize & Simplify - Make processes as consistent and repeatable as possible.
-
Build Relationships - Establish personal relationships with both internal and external stakeholders.
Although lean manufacturing isn't a new concept in business, it has gained popularity due to renewed interest in the economy after the 2008 global financial crisis. Many businesses are now using lean manufacturing to improve their competitiveness. Economists think that lean manufacturing is a crucial factor in economic recovery.
Lean manufacturing is becoming a popular practice in automotive. It has many advantages. These include improved customer satisfaction, reduced inventory levels, lower operating costs, increased productivity, and better overall safety.
Any aspect of an enterprise can benefit from Lean manufacturing. This is because it ensures efficiency and effectiveness in all stages of the value chain.
There are three main types:
-
Just-in Time Manufacturing, (JIT): This kind of lean manufacturing is also commonly known as "pull-systems." JIT is a process in which components can be assembled at the point they are needed, instead of being made ahead of time. This approach reduces lead time, increases availability and reduces inventory.
-
Zero Defects Manufacturing (ZDM),: ZDM is a system that ensures no defective units are left the manufacturing facility. If a part is required to be repaired on the assembly line, it should not be scrapped. This is also true for finished products that require minor repairs before shipping.
-
Continuous Improvement (CI), also known as Continuous Improvement, aims at improving the efficiency of operations through continuous identification and improvement to minimize or eliminate waste. Continuous Improvement involves continuous improvement of processes.