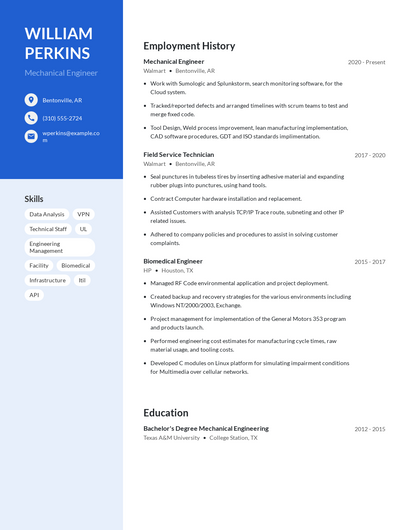
Both individuals and businesses can find a wide range of employment opportunities in the industry. It is expected that the employment industry will continue to grow because many employers prefer to use external agencies to screen potential employees. Many of these agencies operate online, which allows them to lower their administrative costs as well as staff. They are also vulnerable to competition from job postings found on employer Web pages and job-matching websites run by educational institutions and professional associations.
Jobs in the employment service industry
Many occupations are represented in the employment service industry. These professionals have specialized knowledge in many areas, including executive search, placement, recruiting, and placement. These professionals can also offer temporary workers to clients. These professionals also offer human resources services. Companies located in different parts the world dominate the industry of employment services.
This industry employs millions, with a wide range of education, experience, as well as skills. There are many occupations, from secretary to computer systems analyst and general laborer to nurse. Some of these jobs, like employment interviewers, sales representatives, or office managers, are permanent.
Labor market
The labor market is a place where the supply and demand of jobs meet. The employer pays employees to provide services for employers. The worker could be an individual, or an organization. The employer could be anyone looking for a worker. This is similar to selling and buying in that a worker can be an employer and a buyer can be an employee.
The federal government has several statistical agencies that collect data on the labor market. The Bureau of Labor Statistics, for example, collects and analyzes data on unemployment, employment, and wages. It also analyzes data about industrial relations, occupational safety and family spending. These data can help economists identify trends in labour market.
Industry size
The size of an employment industry is the number of workers employed by the industry. In the United States there are 6.1 Million employers. Large companies are the most important employers. Employing fewer workers is the case for smaller businesses. According to the U.S. Census Bureau, businesses with less than 500 employees comprise 99.7% of the total. Although smaller industries might not have many employees, they can create new jobs.
Recession and its impact on the industry
If the economy is experiencing recession, the workforce will suffer. The unemployment rate will rise as a result. The length of unemployment increases, as well. Each sector of the employment industry will suffer a loss in jobs, but this loss will be different in scale. While every sector experienced job losses during the Great Recession all sectors suffered different levels of job loss.
Premiums will reflect the reductions in payroll. This will cause a 1% rise in premiums in the Mild recession scenario. In the event of a severe recession, this increase will be much greater. The decrease in payrolls of Goods & Services is approximately half the size as other industries. As a result, the premiums on Goods & Services may rise.
Influence of COVID-19, coronavirus, pandemic on the industry
Industries that have a high proportion of older workers were most affected by the COVID-19 (coronavirus epidemic) on the employment industry. Professional and business service were the most affected, followed by social assistance and health care. Although job losses were greater among younger workers, they weren't disproportionately high. Worker younger than 35 years old were more likely to work in jobs that require face-to–face contact.
Both high-paying and lower-paying jobs were affected by this pandemic. While most workers lost their jobs because of the virus, the number of people in these sectors was smaller than in other sectors. Many information and management workers were able to work remotely, which allowed them to recover the majority of their jobs. The worst impact on employment was felt in higher-paying industries. In the second quarter of 2019, the number of people working in those sectors was 15% lower than in the same period in 2018.
FAQ
What is the job of a production plan?
Production planners make sure that every aspect of the project is delivered on-time, within budget, and within schedule. A production planner ensures that the service and product meet the client's expectations.
How can manufacturing efficiency be improved?
The first step is to determine the key factors that impact production time. We must then find ways that we can improve these factors. If you don't know where to start, then think about which factor(s) have the biggest impact on production time. Once you have identified them, it is time to identify solutions.
Is automation necessary in manufacturing?
Automation is essential for both manufacturers and service providers. It allows them provide faster and more efficient services. It reduces human errors and improves productivity, which in turn helps them lower their costs.
How does manufacturing avoid bottlenecks in production?
Production bottlenecks can be avoided by ensuring that processes are running smoothly during the entire production process, starting with the receipt of an order and ending when the product ships.
This includes planning to meet capacity requirements and quality control.
Continuous improvement techniques like Six Sigma are the best way to achieve this.
Six Sigma is a management method that helps to improve quality and reduce waste.
It seeks to eliminate variation and create consistency in your work.
What does warehouse mean?
A warehouse, or storage facility, is where goods are stored prior to being sold. It can be indoors or out. It may also be an indoor space or an outdoor area.
What are the responsibilities of a manufacturing manager
A manufacturing manager must ensure that all manufacturing processes are efficient and effective. They should be alert for any potential problems in the company and react accordingly.
They should also know how to communicate with other departments such as sales and marketing.
They should also be knowledgeable about the latest trends in the industry so they can use this information for productivity and efficiency improvements.
Statistics
- You can multiply the result by 100 to get the total percent of monthly overhead. (investopedia.com)
- Many factories witnessed a 30% increase in output due to the shift to electric motors. (en.wikipedia.org)
- According to a Statista study, U.S. businesses spent $1.63 trillion on logistics in 2019, moving goods from origin to end user through various supply chain network segments. (netsuite.com)
- In 2021, an estimated 12.1 million Americans work in the manufacturing sector.6 (investopedia.com)
- It's estimated that 10.8% of the U.S. GDP in 2020 was contributed to manufacturing. (investopedia.com)
External Links
How To
How to use lean manufacturing in the production of goods
Lean manufacturing (or lean manufacturing) is a style of management that aims to increase efficiency, reduce waste and improve performance through continuous improvement. It was developed by Taiichi Okono in Japan, during the 1970s & 1980s. TPS founder Kanji Takoda awarded him the Toyota Production System Award (TPS). Michael L. Watkins published the book "The Machine That Changed the World", which was the first to be published about lean manufacturing.
Lean manufacturing, often described as a set and practice of principles, is aimed at improving the quality, speed, cost, and efficiency of products, services, and other activities. It is about eliminating defects and waste from all stages of the value stream. The five-steps of Lean Manufacturing are just-in time (JIT), zero defect and total productive maintenance (TPM), as well as 5S. Lean manufacturing eliminates non-value-added tasks like inspection, rework, waiting.
Lean manufacturing is a way for companies to achieve their goals faster, improve product quality, and lower costs. Lean manufacturing can be used to manage all aspects of the value chain. Customers, suppliers, distributors, retailers and employees are all included. Lean manufacturing is widely used in many industries. For example, Toyota's philosophy underpins its success in automobiles, electronics, appliances, healthcare, chemical engineering, aerospace, paper, food, etc.
Five basic principles of Lean Manufacturing are included in lean manufacturing
-
Define Value - Identify the value your business adds to society and what makes you different from competitors.
-
Reduce waste - Get rid of any activity that does not add value to the supply chain.
-
Create Flow - Ensure work moves smoothly through the process without interruption.
-
Standardize and simplify – Make processes as repeatable and consistent as possible.
-
Develop Relationships: Establish personal relationships both with internal and external stakeholders.
Although lean manufacturing isn't a new concept in business, it has gained popularity due to renewed interest in the economy after the 2008 global financial crisis. Many businesses have adopted lean manufacturing techniques to help them become more competitive. Many economists believe lean manufacturing will play a major role in economic recovery.
Lean manufacturing, which has many benefits, is now a standard practice in the automotive industry. These include higher customer satisfaction levels, reduced inventory levels as well as lower operating costs.
You can apply Lean Manufacturing to virtually any aspect of your organization. Because it makes sure that all value chains are efficient and effectively managed, Lean Manufacturing is particularly helpful for organizations.
There are three types principally of lean manufacturing:
-
Just-in-Time Manufacturing: Also known as "pull systems", this type of lean manufacturing uses just-in-time manufacturing (JIT). JIT refers to a system in which components are assembled at the point of use instead of being produced ahead of time. This method reduces lead times, increases availability, and decreases inventory.
-
Zero Defects Manufacturing (ZDM): ZDM focuses on ensuring that no defective units leave the manufacturing facility. You should repair any part that needs to be repaired during an assembly line. This applies to finished goods that may require minor repairs before shipment.
-
Continuous Improvement (CI: Continuous improvement aims to increase the efficiency of operations by constantly identifying and making improvements to reduce or eliminate waste. Continuous improvement refers to continuous improvement of processes as well people and tools.