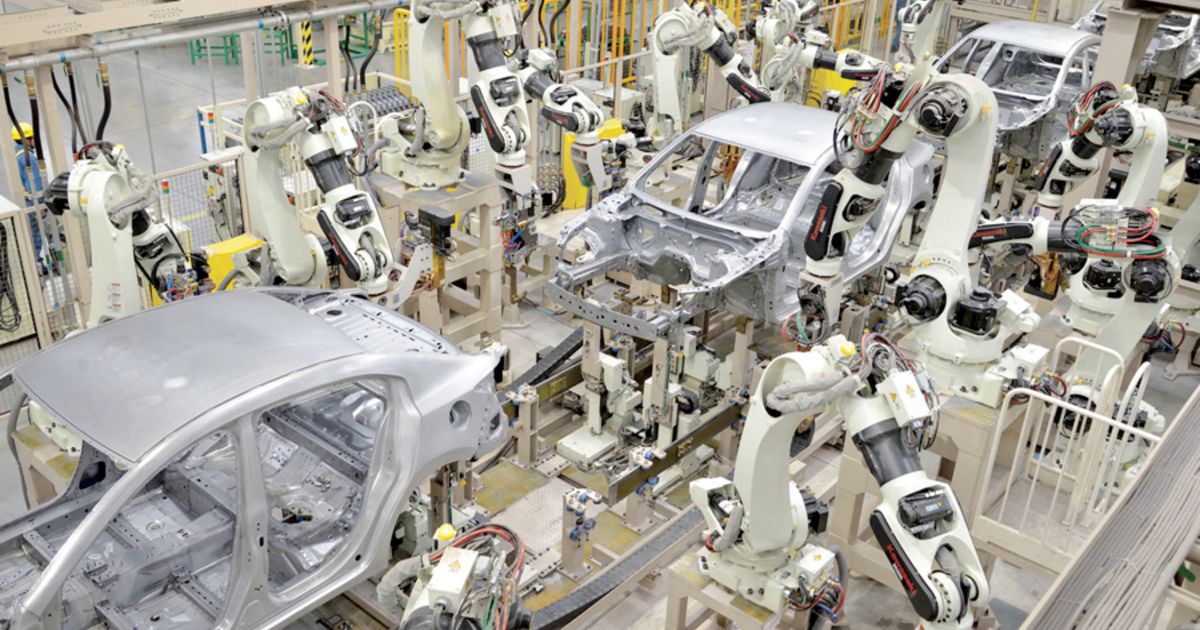
Industrial engineering jobs in Colorado offer many opportunities for developing new products to meet the needs of businesses around the globe. These professionals are dedicated to making their employers successful, from reducing costs to ensuring products and services meet high quality standards.
Get a Job as a Packaging Engineer at Denver
As a packaging engineering, you will be responsible for the testing and design of packaging so that different products can be safely transported. You'll be paired with product designers and logisticians to oversee one of the final stages in product development. As this profession is expected to grow at 10% over the coming decade, you should expect a competitive salary.
Direct Hire Mechanical Engineer for Power Plants Centennial, CO
As a mechanical engineer for power plants, you'll provide technical engineering and cost information to ensure your work meets all engineering standards on heavy industrial or power projects. As a mechanical engineer for power plants, you'll work with your team members to develop project schedules and specifications, track submissions and evaluate bids from general contractors and equipment suppliers. You'll need a bachelor's degree in engineering or a related field and at least eight years of experience performing design and construction oversight for power plant projects. You should have some CAD knowledge and be familiar with electromechanical engineering principles.
FAQ
What are manufacturing and logistic?
Manufacturing is the production of goods using raw materials. Logistics manages all aspects of the supply chain, including procurement, production planning and distribution, inventory control, transportation, customer service, and transport. Logistics and manufacturing are often referred to as one thing. It encompasses both the creation of products and their delivery to customers.
What are the responsibilities of a production planner
A production planner makes sure all project elements are delivered on schedule, within budget, as well as within the agreed scope. They ensure that the product or service is of high quality and meets client requirements.
What is the responsibility of a logistics manager?
A logistics manager ensures that all goods are delivered on time and without damage. This is done using his/her knowledge of the company's products. He/she should also ensure enough stock is available to meet demand.
Statistics
- (2:04) MTO is a production technique wherein products are customized according to customer specifications, and production only starts after an order is received. (oracle.com)
- You can multiply the result by 100 to get the total percent of monthly overhead. (investopedia.com)
- It's estimated that 10.8% of the U.S. GDP in 2020 was contributed to manufacturing. (investopedia.com)
- According to a Statista study, U.S. businesses spent $1.63 trillion on logistics in 2019, moving goods from origin to end user through various supply chain network segments. (netsuite.com)
- In 2021, an estimated 12.1 million Americans work in the manufacturing sector.6 (investopedia.com)
External Links
How To
How to Use Six Sigma in Manufacturing
Six Sigma is defined as "the application of statistical process control (SPC) techniques to achieve continuous improvement." Motorola's Quality Improvement Department in Tokyo, Japan developed Six Sigma in 1986. The basic idea behind Six Sigma is to improve quality by improving processes through standardization and eliminating defects. This method has been adopted by many companies in recent years as they believe there are no perfect products or services. Six Sigma seeks to reduce variation between the mean production value. This means that if you take a sample of your product, then measure its performance against the average, you can find out what percentage of the time the process deviates from the norm. If you notice a large deviation, then it is time to fix it.
The first step toward implementing Six Sigma is understanding how variability works in your business. Once you've understood that, you'll want to identify sources of variation. You'll also want to determine whether these variations are random or systematic. Random variations occur when people do mistakes. Symmetrical variations are caused due to factors beyond the process. You could consider random variations if some widgets fall off the assembly lines. If however, you notice that each time you assemble a widget it falls apart in exactly the same spot, that is a problem.
Once you identify the problem areas, it is time to create solutions. It might mean changing the way you do business or redesigning it entirely. To verify that the changes have worked, you need to test them again. If they fail, you can go back to the drawing board to come up with a different plan.