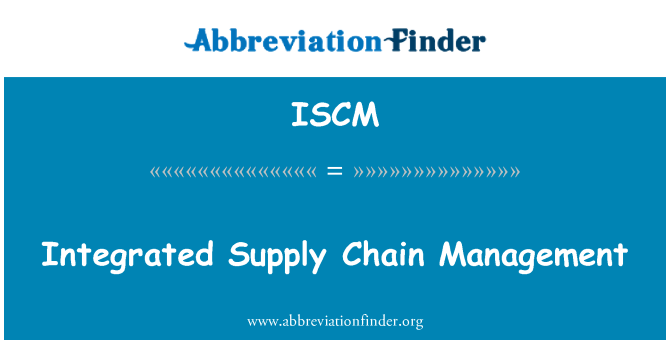
Michigan's unemployment rates are among the highest across the country, and in the Midwest. The Unemployment insurance system was created to aid families in economic downturns. However, the system was not updated to meet today's workforce. Many of the state's policies are outdated, especially when it comes to protecting women and Black and Latinx workers.
Michigan's maximum weekly benefit has only been raised once since 1995. It is also one of only six states to provide fewer than the standard 26 weeks of unemployment benefits. In reality, the minimum number of weeks provided is less than 10. A family might find themselves in poverty if they lose their job before the maximum number. Michigan isn't doing enough to make sure that every worker is eligible for unemployment insurance.
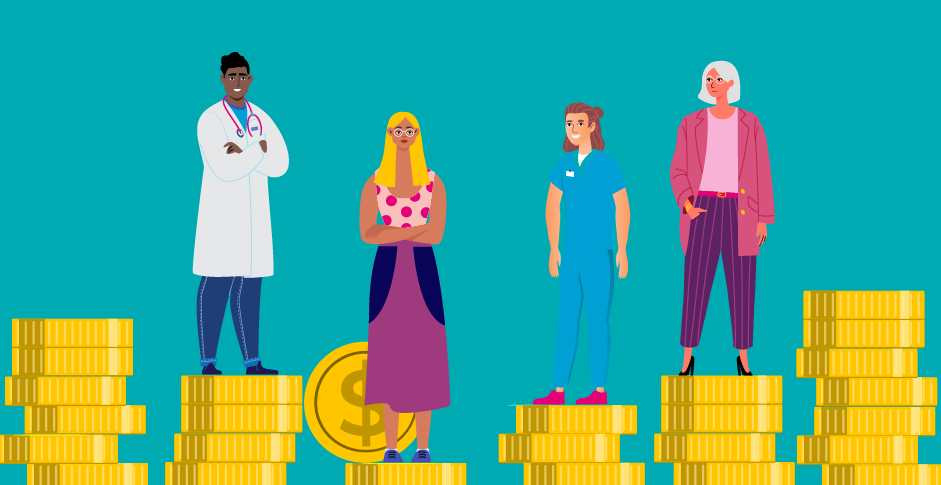
Michigan's minimum wage is another example. A worker must make at least $5,667 per weekly to be eligible for UI. This is more than the average wage in other Midwestern states. This is not a bad thing. However, Michigan's minimum wage requirement of more than $100 per week makes it a far behind other states.
According to the Advisory Council's "two-thirds rule," Michigan's unemployment benefits should be more than 50% of average weekly wages. Instead, the state's maximum benefit is just 34%. Michigan is far behind other States in terms of Unemployment Insurance, which means it should be increasing its game. Wisconsin, Iowa, Pennsylvania and other states offer maximum benefits that are at or below 50% of the average wage.
The Michigan Legislature should look to improve the state's Unemployment Insurance program. This is an important step that will help to reduce racial inequalities and improve the safety net. Additionally, the state should look to expand the base period in which workers can apply for benefits. An expanded base period is a great way to increase federal funding for skills training and employment search costs. As an added bonus, it would improve the likelihood that more unemployed workers would get the assistance they need.
Michigan's unemployment rate is higher than many other states but has been decreasing since 2009. New figures from the state show that the unemployment rate is now at 6.1 percent as of January 2021. Since then, the rate has remained relatively stable. During the recession, the State of Michigan had the worst unemployment rates in the country. With a strong investment in the Unemployment Insurance system, however, more workers will be able to find jobs before the 26-week standard is reached.
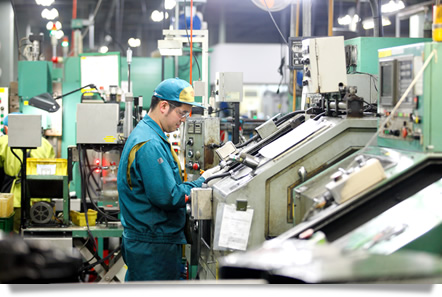
The minimum wage necessary to qualify for unemployment benefit is highest in the midwest. In the same year, Michigan's maximum UI benefit is the lowest in the nation.
FAQ
What are the responsibilities of a production planner
Production planners ensure all aspects of the project are delivered within time and budget. A production planner ensures that the service and product meet the client's expectations.
What's the difference between Production Planning & Scheduling?
Production Planning (PP) is the process of determining what needs to be produced at any given point in time. Forecasting and identifying production capacity are two key elements to this process.
Scheduling is the process of assigning specific dates to tasks so they can be completed within the specified timeframe.
Is automation important in manufacturing?
Automating is not just important for manufacturers, but also for service providers. They can provide services more quickly and efficiently thanks to automation. It also helps to reduce costs and improve productivity.
What is the job of a manufacturer manager?
A manufacturing manager has to ensure that all manufacturing processes work efficiently and effectively. They should also be aware of any problems within the company and act accordingly.
They should also be able and comfortable communicating with other departments like sales and marketing.
They should be informed about industry trends and be able make use of this information to improve their productivity and efficiency.
Statistics
- Many factories witnessed a 30% increase in output due to the shift to electric motors. (en.wikipedia.org)
- In 2021, an estimated 12.1 million Americans work in the manufacturing sector.6 (investopedia.com)
- Job #1 is delivering the ordered product according to specifications: color, size, brand, and quantity. (netsuite.com)
- (2:04) MTO is a production technique wherein products are customized according to customer specifications, and production only starts after an order is received. (oracle.com)
- According to the United Nations Industrial Development Organization (UNIDO), China is the top manufacturer worldwide by 2019 output, producing 28.7% of the total global manufacturing output, followed by the United States, Japan, Germany, and India.[52][53] (en.wikipedia.org)
External Links
How To
Six Sigma in Manufacturing
Six Sigma is "the application statistical process control (SPC), techniques for continuous improvement." Motorola's Quality Improvement Department developed it at their Tokyo plant in Japan in 1986. Six Sigma is a method to improve quality through standardization and elimination of defects. Many companies have adopted this method in recent years. They believe there is no such thing a perfect product or service. The main goal of Six Sigma is to reduce variation from the mean value of production. This means that you can take a sample from your product and then compare its performance to the average to find out how often the process differs from the norm. If this deviation is too big, you know something needs fixing.
Understanding how your business' variability is a key step towards Six Sigma implementation is the first. Once you have a good understanding of the basics, you can identify potential sources of variation. These variations can also be classified as random or systematic. Random variations happen when people make errors; systematic variations are caused externally. You could consider random variations if some widgets fall off the assembly lines. However, if you notice that every time you assemble a widget, it always falls apart at exactly the same place, then that would be a systematic problem.
Once you've identified the problem areas you need to find solutions. The solution could involve changing how you do things, or redesigning your entire process. Once you have implemented the changes, it is important to test them again to ensure they work. If they don't work, you will need to go back to the drawing boards and create a new plan.