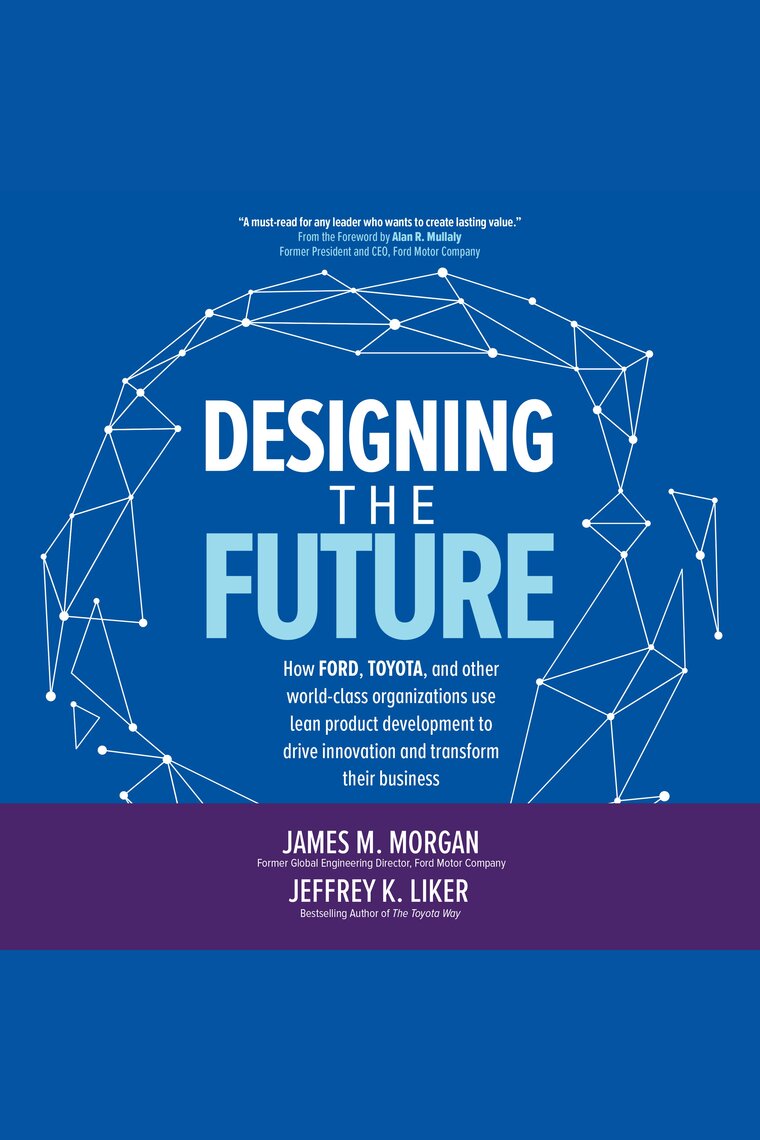
Despite the economic rebound, the US's manufacturing sector continues to be a significant contributor to the US economy. It supports 12.8million jobs, accounts for one percent of private-sector work, and employs more people than the average American. However, its share of national output has declined since the Great Recession, and its share of employment has fallen to below 12 percent. The manufacturing industry is facing structural problems. These include trade deficits as well as low productivity and output. These issues are being slowly addressed but it remains to be seen what long-term implications they will have. The US manufacturing sector is in a good place to rebound. However, the United States must decide whether it will make a comeback.
Manufacturing is a capital intensive industry. The sector is changing as new technologies become available. Firms are investing in new technologies to enhance their productivity and enhance the skills of their workers. They also create a pipeline for future workers. In addition, manufacturers are investing in upskilling their existing workforce. These investments are helping to increase their competitiveness in the market. In order to avoid future disruptions, the firms also work to strengthen their supply networks.
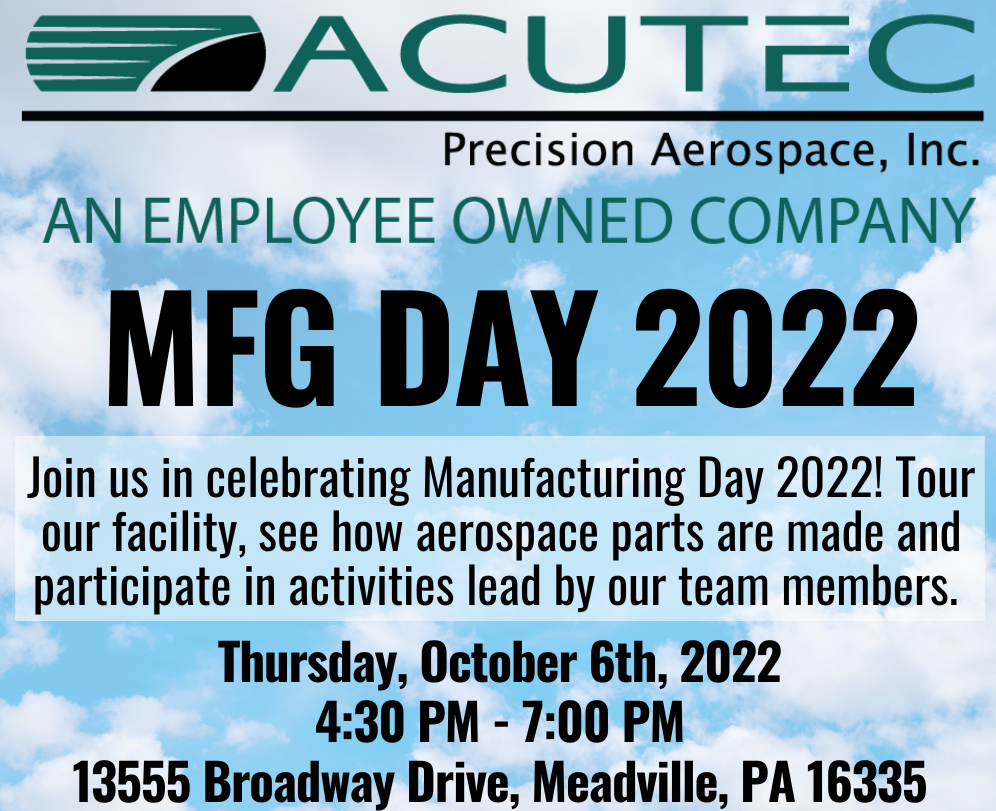
Manufacturers are now facing increasing supply chain costs and are being challenged. The US can solve these problems by strengthening the innovation system. The US will need avoid tariff wars from countries that want to import to the US and will need to maintain open-trade policies to keep its manufacturer competitive.
The United States is a world leader with a growing presence over the past century. As a result, the United States has a large share of the world's oil and gas demand. Nevertheless, it is in danger of losing its position as the world's leading manufacturing economy. Its aging population and low international immigration are two reasons for this. It can also become more competitive by investing into new technologies that will improve production efficiency, and make it more sustainably.
US manufacturing is responsible for $2.3 trillion in US GDP. This figure is 20 percent of the nation’s capital investment, and 35 percent productivity growth. In Q1 2018, manufacturing output reached a record $2.00 trillion. This is the highest level of manufacturing output in the United States since the Great Recession. It is also higher than the recovery in the labor market.
The United States is second in the world in manufacturing, only behind China. 60 percent of exports to the United States are manufactured. Manufacturing also accounts for significant business R&D expenditures. However, manufacturing output has declined between the fourth quarter of 2007, and the first quarter 2009. The share of manufacturing output increased in only a few States. Manufacturing has a greater presence in the Eighth District states, and manufacturing output shares have increased in many of these states.
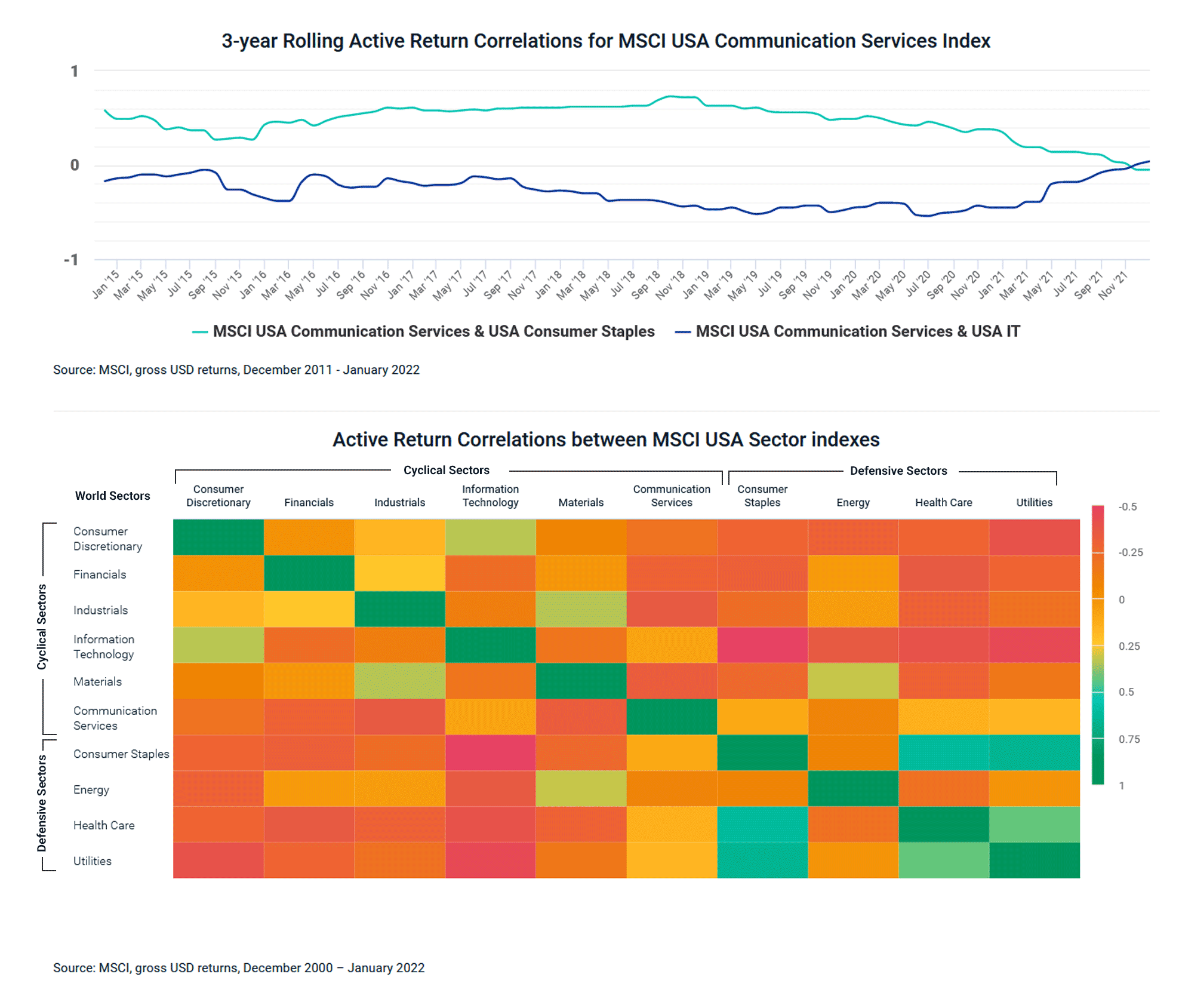
Manufacturing output fell by 15.2 % from 2007's fourth quarter. Manufacturing output decreased by 6.4% in the first three quarters of 2009. However, manufacturing production increased in Illinois (Indiana), Kentucky, and Ohio.
FAQ
How can manufacturing avoid production bottlenecks
The key to avoiding bottlenecks in production is to keep all processes running smoothly throughout the entire production cycle, from the time you receive an order until the time when the product ships.
This includes both planning for capacity and quality control.
This can be done by using continuous improvement techniques, such as Six Sigma.
Six Sigma is a management system used to improve quality and reduce waste in every aspect of your organization.
It emphasizes consistency and eliminating variance in your work.
How can manufacturing overproduction be reduced?
The key to reducing overproduction lies in developing better ways to manage inventory. This would decrease the time that is spent on inefficient activities like purchasing, storing, or maintaining excess stock. This would allow us to use our resources for more productive tasks.
Kanban systems are one way to achieve this. A Kanbanboard is a visual tool that allows you to keep track of the work being done. Kanban systems are where work items travel through a series of states until reaching their final destination. Each state represents a different priority.
As an example, if work is progressing from one stage of the process to another, then the current task is complete and can be transferred to the next. But if a task remains in the beginning stages it will stay that way until it reaches its end.
This helps to keep work moving forward while ensuring that no work is left behind. Managers can view the Kanban board to see how much work they have done. This allows them the ability to adjust their workflow using real-time data.
Lean manufacturing is another way to manage inventory levels. Lean manufacturing focuses on eliminating waste throughout the entire production chain. Waste includes anything that does not add value to the product. Here are some examples of common types.
-
Overproduction
-
Inventory
-
Unnecessary packaging
-
Material surplus
By implementing these ideas, manufacturers can improve efficiency and cut costs.
What are the 7 Rs of logistics?
The 7R's of Logistics is an acronym for the seven basic principles of logistics management. It was developed by International Association of Business Logisticians (IABL), and published as part of their "Seven Principles of Logistics Management Series" in 2004.
The acronym consists of the following letters:
-
Responsible - ensure that all actions taken are within legal requirements and are not harmful to others.
-
Reliable - You can have confidence that you will fulfill your promises.
-
Be responsible - Use resources efficiently and avoid wasting them.
-
Realistic - Consider all aspects of operations, including environmental impact and cost effectiveness.
-
Respectful - treat people fairly and equitably.
-
Reliable - Find ways to save money and increase your productivity.
-
Recognizable is a company that provides customers with value-added solutions.
What does it mean to be a manufacturer?
Manufacturing Industries are businesses that produce products for sale. Consumers are the people who purchase these products. These companies use various processes such as production, distribution, retailing, management, etc., to fulfill this purpose. They create goods from raw materials, using machines and various other equipment. This includes all types if manufactured goods.
What are the products of logistics?
Logistics involves the transportation of goods from point A and point B.
They encompass all aspects transport, including packaging and loading, transporting, storage, unloading.
Logisticians ensure the product reaches its destination in the most efficient manner. They provide information on demand forecasts as well stock levels, production schedules and availability of raw material.
They keep track and monitor the transit of shipments, maintain quality standards, order replenishment and inventories, coordinate with suppliers, vendors, and provide support for sales and marketing.
Statistics
- Many factories witnessed a 30% increase in output due to the shift to electric motors. (en.wikipedia.org)
- It's estimated that 10.8% of the U.S. GDP in 2020 was contributed to manufacturing. (investopedia.com)
- [54][55] These are the top 50 countries by the total value of manufacturing output in US dollars for its noted year according to World Bank.[56] (en.wikipedia.org)
- In the United States, for example, manufacturing makes up 15% of the economic output. (twi-global.com)
- According to a Statista study, U.S. businesses spent $1.63 trillion on logistics in 2019, moving goods from origin to end user through various supply chain network segments. (netsuite.com)
External Links
How To
How to use 5S to increase Productivity in Manufacturing
5S stands for "Sort", 'Set In Order", 'Standardize', & Separate>. Toyota Motor Corporation invented the 5S strategy in 1954. It assists companies in improving their work environments and achieving higher efficiency.
This method aims to standardize production processes so that they are repeatable, measurable and predictable. Cleaning, sorting and packing are all done daily. Through these actions, workers can perform their jobs more efficiently because they know what to expect from them.
Five steps are required to implement 5S: Sort, Set In Order, Standardize. Separate. Each step requires a different action, which increases efficiency. By sorting, for example, you make it easy to find the items later. When you set items in an order, you put items together. Next, organize your inventory into categories and store them in containers that are easily accessible. Make sure everything is correctly labeled when you label your containers.
Employees need to reflect on how they do their jobs. Employees must understand why they do certain tasks and decide if there's another way to accomplish them without relying on the old ways of doing things. In order to use the 5S system effectively, they must be able to learn new skills.
In addition to improving efficiency, the 5S system also increases morale and teamwork among employees. They are more motivated to achieve higher efficiency levels as they start to see improvement.