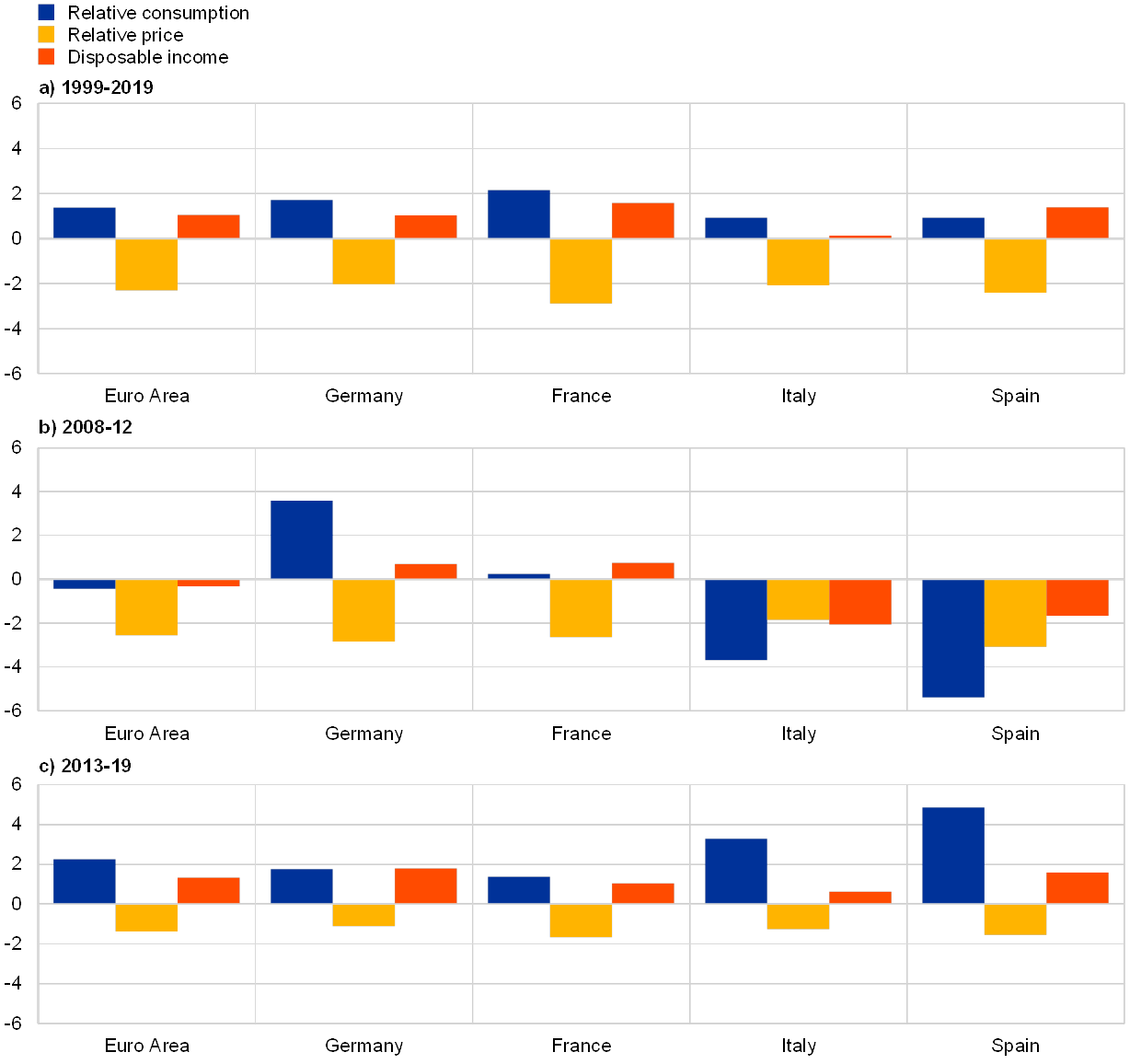
The manufacture of car is a long and complex process that takes a lot of time and effort. It can take a car two or more years to be produced from design to completion and testing before it is sold to consumers. During this time, the vehicle’s electrical systems, programming, as well as safety systems, will be checked to ensure a smooth, safe driving experience.
In the USA, the automobile manufacturing industry is a huge and profitable industry. The industry has also created many jobs and boosted the economy. The United States ranks as one of world's top markets for automotive production.
There are many companies in the automotive industry, including the major names such as General Motors and Ford. This includes suppliers and vendors that provide the materials, parts and components for car production. These companies are present in all 50 states and provide economic benefits for the country.
Major auto manufacturers in USA
The biggest car makers in the United States are GM, Toyota, BMW, Honda, Ford, and Fiat Chrysler Automobiles (FCA). Chevrolet, Hyundai Nissan Kia Subaru Volkswagen and Volkswagen are other major brands sold in the USA.
About half of the best-selling car models in America are manufactured by GM. These companies are known for their excellent customer service, and have an extensive network of dealerships.
Some high-end vehicles are still built by hand. This includes luxury cars from companies such as Aston Martin and Ferrari.
Modern car factories can be bright and very clean. The new production lines are designed so that everyone in the factory can see what is going on. The new factories are a far cry from the old ones where the walls and workers were covered in grease, oil or even sweat.
Another major advantage of the production lines is that they help to increase productivity. This allows car companies to build more cars in less time than it would take if the workers had to do each task individually.
These new production lines not only helped to lower costs but also improved quality. Quality can be used to increase profits and sales.
Some auto manufacturers have also moved to use more green energy sources, such as wind power, in their factories. This helps to lower the cost of production while reducing pollution.
It provides millions jobs throughout the United States. It contributes to economic development and is an important driver of innovation across many different sectors.
What are the largest car manufacturing facilities in the US?
Michigan is the home of America's largest auto manufacturing plant. The Ford Focus is produced there. It also employs over 34,000 workers and generates about $3 billion in revenue each year.
FAQ
What are manufacturing & logistics?
Manufacturing is the production of goods using raw materials. Logistics covers all aspects involved in managing supply chains, including procurement and production planning. Manufacturing and logistics are often considered together as a broader term that encompasses both the process of creating products and delivering them to customers.
What are the products of logistics?
Logistics involves the transportation of goods from point A and point B.
They encompass all aspects transport, including packaging and loading, transporting, storage, unloading.
Logisticians ensure that the right product reaches the right place at the right time and under safe conditions. They assist companies with their supply chain efficiency through information on demand forecasts. Stock levels, production times, and availability.
They coordinate with vendors and suppliers, keep track of shipments, monitor quality standards and perform inventory and order replenishment.
What are the differences between these four types?
Manufacturing refers to the transformation of raw materials into useful products by using machines and processes. It involves many different activities such as designing, building, testing, packaging, shipping, selling, servicing, etc.
How can I learn about manufacturing?
Hands-on experience is the best way to learn more about manufacturing. You can read books, or watch instructional videos if you don't have the opportunity to do so.
How can we reduce manufacturing overproduction?
In order to reduce excess production, you need to develop better inventory management methods. This would decrease the time that is spent on inefficient activities like purchasing, storing, or maintaining excess stock. By doing this, we could free up resources for other productive tasks.
Kanban systems are one way to achieve this. A Kanban board, a visual display to show the progress of work, is called a Kanban board. Kanban systems allow work items to move through different states until they reach their final destination. Each state represents a different priority.
To illustrate, work can move from one stage or another when it is complete enough for it to be moved to a new stage. If a task is still in its beginning stages, it will continue to be so until it reaches the end.
This allows you to keep work moving along while making sure that no work gets neglected. A Kanban board allows managers to monitor how much work is being completed at any given moment. This allows them the ability to adjust their workflow using real-time data.
Lean manufacturing, another method to control inventory levels, is also an option. Lean manufacturing works to eliminate waste throughout every stage of the production chain. Any product that isn't adding value can be considered waste. These are some of the most common types.
-
Overproduction
-
Inventory
-
Unnecessary packaging
-
Materials in excess
These ideas can help manufacturers improve efficiency and reduce costs.
What does it mean to be a manufacturer?
Manufacturing Industries are those businesses that make products for sale. Consumers are the people who purchase these products. These companies use a variety processes such as distribution, retailing and management to accomplish their purpose. They make goods from raw materials with machines and other equipment. This includes all types if manufactured goods.
What is the job of a production plan?
A production planner ensures all aspects of the project are delivered on time, within budget, and within scope. They make sure that the product and services meet client expectations.
Statistics
- [54][55] These are the top 50 countries by the total value of manufacturing output in US dollars for its noted year according to World Bank.[56] (en.wikipedia.org)
- It's estimated that 10.8% of the U.S. GDP in 2020 was contributed to manufacturing. (investopedia.com)
- (2:04) MTO is a production technique wherein products are customized according to customer specifications, and production only starts after an order is received. (oracle.com)
- Many factories witnessed a 30% increase in output due to the shift to electric motors. (en.wikipedia.org)
- According to a Statista study, U.S. businesses spent $1.63 trillion on logistics in 2019, moving goods from origin to end user through various supply chain network segments. (netsuite.com)
External Links
How To
How to Use Six Sigma in Manufacturing
Six Sigma is defined as "the application of statistical process control (SPC) techniques to achieve continuous improvement." Motorola's Quality Improvement Department, Tokyo, Japan, developed it in 1986. Six Sigma's core idea is to improve the quality of processes by standardizing and eliminating defects. Many companies have adopted this method in recent years. They believe there is no such thing a perfect product or service. Six Sigma's main objective is to reduce variations from the production average. This means that you can take a sample from your product and then compare its performance to the average to find out how often the process differs from the norm. If this deviation is too big, you know something needs fixing.
The first step toward implementing Six Sigma is understanding how variability works in your business. Once you have this understanding, you will need to identify sources and causes of variation. You'll also want to determine whether these variations are random or systematic. Random variations are caused when people make mistakes. While systematic variations are caused outside of the process, they can occur. If you make widgets and some of them end up on the assembly line, then those are considered random variations. If however, you notice that each time you assemble a widget it falls apart in exactly the same spot, that is a problem.
After identifying the problem areas, you will need to devise solutions. That solution might involve changing the way you do things or redesigning the process altogether. To verify that the changes have worked, you need to test them again. If they fail, you can go back to the drawing board to come up with a different plan.