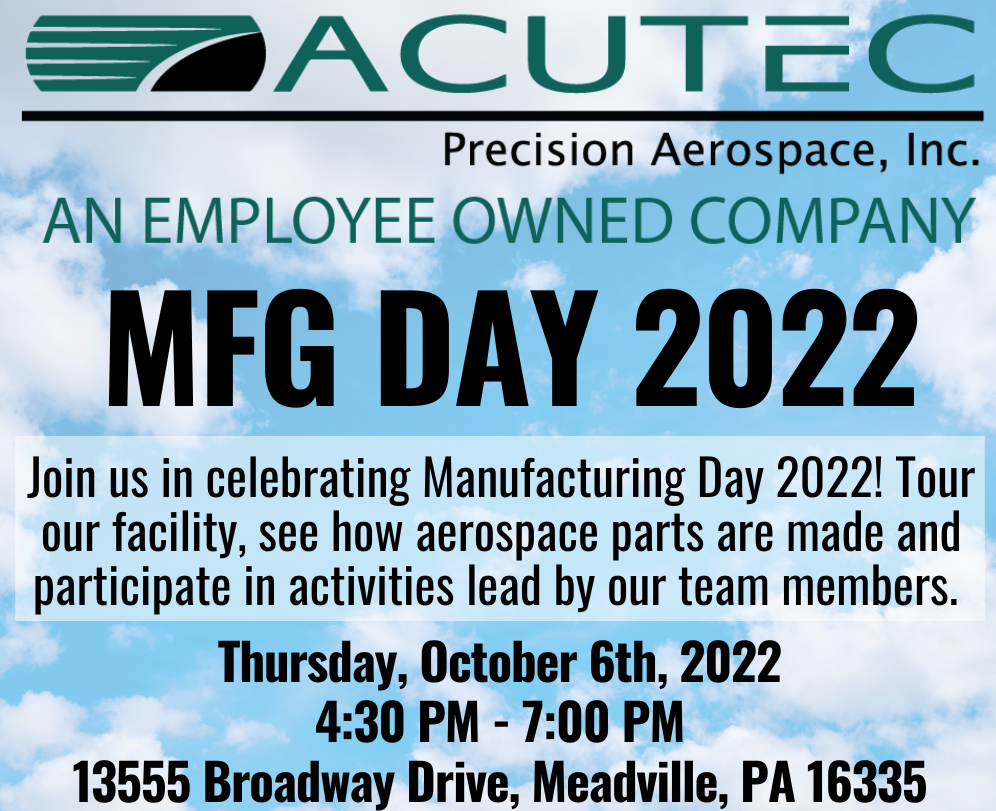
Food manufacturing is a broad industry that employs many managers and professionals. Top executives are responsible for making policy decisions and organizing production operations. Industrial production managers oversee the day-today operations of a manufacturing factory. Marketing, community relations, sales, marketing and public relations managers direct the sales and promotional programs.
The food manufacturing industry has many jobs
New York state is home many food manufacturing jobs. Bakers, food batchmakers, packaging and filling machine operator are the top three most common occupations. These occupations are responsible for less than half the state's food processing employment. Throughout the state, food manufacturing employment increased in seven out of 10 labor market regions.
There has been an improvement in the job market, which coincides well with the rise in food manufacturing jobs. In February, unemployment was at 3.8%. It was the lowest level in more that a decade. Nondurable goods industries saw the largest increase in employment in food manufacturing, with 16,000 additional workers.

Workers in the industry make an average salary
The average wages for workers in food manufacturing range from $26,000 to $52,000 per year, with the highest paid earning an average of $52,000 per year. The range is higher for those with more years of experience, but the bottom 10 percent of earners earn less than $26,000 per year. Food Factory Workers have a wide range of salaries, but it is within the range of other manufacturing occupations.
Average wages in this industry have increased over the last few years. While the manufacturing industry is important to our economy, it isn't an independent sector. Understanding how other economic sectors impact workers' lives is crucial.
These are the locations with the highest number of workers in the industry
2013 saw three New York State labor markets containing food manufacturing companies: the Finger Lakes region, the Southern Tier and Western New York. These three regions together employed almost half of the total food manufacturing workforce. These regions saw high concentrations of food production. The highest average wages were found in the Hudson Valley Southern Tier, Western New York and Western New York.
Food processing is an industry that requires skilled labor. Lack of skilled labor in certain areas makes it difficult for food manufacturers to find the right workers. Not only is it hard to find people to work in distribution trucks and other lower-level positions, but it's also becoming increasingly difficult to fill more senior positions. Career site CareersInFood.com reports that food manufacturing job openings have increased by 12% in the last year. There has been a 37% increase in the 24 months.
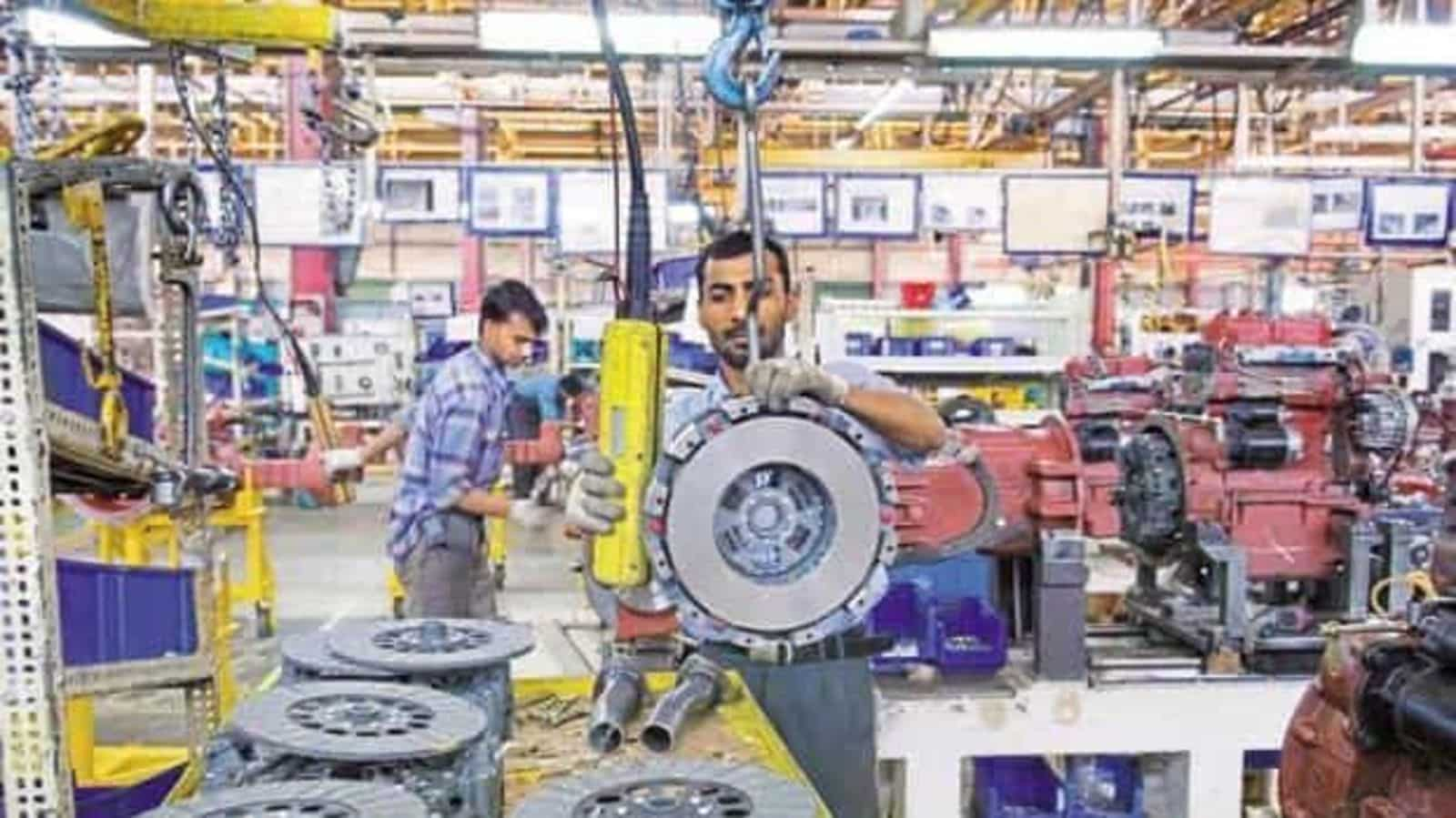
There are approximately 12,000 workers in this industry.
According to the Bureau of Labor Statistics the number of food industry workers increased by 7.200 in February. This is a more than 1% increase from January. This is the third consecutive month of job gains for this industry, which is slowly recovering from several headwinds. The COVID-19 pandemic, a labor shortage, and the global recession have all affected the industry's employment. According to Bureau of Labor Statistics, there were 40,700 workers in the industry in February.
New York State's number of food processing firms grew by 8.8% between 2003-2013. The employment rate increased in four of 10 labor market regions. The largest increase was in the Southern Tier, Hudson Valley and Hudson Valley.
FAQ
What are the products of logistics?
Logistics is the process of moving goods from one point to another.
They include all aspects of transport, including packaging, loading, transporting, unloading, storing, warehousing, inventory management, customer service, distribution, returns, and recycling.
Logisticians ensure that the right product reaches the right place at the right time and under safe conditions. Logisticians assist companies in managing their supply chains by providing information such as demand forecasts, stock levels and production schedules.
They can also track shipments in transit and monitor quality standards.
What is production management?
Production Planning is the creation of a plan to cover all aspects, such as scheduling, budgeting. Location, crew, equipment, props and other details. This document ensures that everything is prepared and available when you are ready for shooting. This document should include information about how to achieve the best results on-set. This includes shooting schedules, locations, cast lists, crew details, and equipment requirements.
First, you need to plan what you want to film. You may have decided where to shoot or even specific locations you want to use. Once you have identified your locations and scenes, you can start working out which elements you require for each scene. You might decide you need a car, but not sure what make or model. If this is the case, you might start searching online for car models and then narrow your options by selecting from different makes.
Once you have found the right car, you can start thinking about extras. What about additional seating? You might also need someone to help you get around the back. Maybe you want to change the interior color from black to white? These questions will help to determine the style and feel of your car. It is also worth considering the types of shots that you wish to take. Are you going to be shooting close-ups? Or wide angles? Maybe you want to show your engine or the steering wheel. These details will help identify the exact car you wish to film.
Once you have all the information, you are ready to create a plan. The schedule will show you when to begin shooting and when to stop. You will need to know when you have to be there, what time you have to leave and when your return home. Everyone will know what they need and when. If you need to hire extra staff, you can make sure you book them in advance. It's not worth paying someone to show up if you haven't told him.
When creating your schedule, you will also need to consider the number of days you need to film. Some projects may only take a couple of days, while others could last for weeks. When you are creating your schedule, you should always keep in mind whether you need more than one shot per day or not. Multiple shots at the same location can increase costs and make it more difficult to complete. You can't be certain if you will need multiple takes so it is better not to shoot too many.
Budgeting is another important aspect of production planning. As it will allow you and your team to work within your financial means, setting a realistic budget is crucial. Remember that you can always reduce the budget later on if you run into unforeseen problems. It is important to not overestimate how much you will spend. You'll end up with less money after paying for other things if the cost is underestimated.
Production planning is a complicated process. But once you understand how everything works together, it becomes much easier to plan future project.
How can manufacturing overproduction be reduced?
It is essential to find better ways to manage inventory to reduce overproduction. This would reduce the time spent on unproductive activities like purchasing, storing and maintaining excess stock. We could use these resources to do other productive tasks.
This can be done by using a Kanban system. A Kanbanboard is a visual tool that allows you to keep track of the work being done. Kanban systems allow work items to move through different states until they reach their final destination. Each state is assigned a different priority.
For instance, when work moves from one stage to another, the current task is complete enough to be moved to the next stage. A task that is still in the initial stages of a process will be considered complete until it moves on to the next stage.
This allows you to keep work moving along while making sure that no work gets neglected. Managers can view the Kanban board to see how much work they have done. This information allows them to adjust their workflow based on real-time data.
Lean manufacturing can also be used to reduce inventory levels. Lean manufacturing works to eliminate waste throughout every stage of the production chain. Anything that doesn't add value to the product is considered waste. There are several types of waste that you might encounter:
-
Overproduction
-
Inventory
-
Unnecessary packaging
-
Exceed materials
By implementing these ideas, manufacturers can improve efficiency and cut costs.
Statistics
- According to the United Nations Industrial Development Organization (UNIDO), China is the top manufacturer worldwide by 2019 output, producing 28.7% of the total global manufacturing output, followed by the United States, Japan, Germany, and India.[52][53] (en.wikipedia.org)
- Many factories witnessed a 30% increase in output due to the shift to electric motors. (en.wikipedia.org)
- According to a Statista study, U.S. businesses spent $1.63 trillion on logistics in 2019, moving goods from origin to end user through various supply chain network segments. (netsuite.com)
- (2:04) MTO is a production technique wherein products are customized according to customer specifications, and production only starts after an order is received. (oracle.com)
- In the United States, for example, manufacturing makes up 15% of the economic output. (twi-global.com)
External Links
How To
How to Use the 5S to Increase Productivity In Manufacturing
5S stands for "Sort", 'Set In Order", 'Standardize', & Separate>. Toyota Motor Corporation created the 5S methodology in 1954. It allows companies to improve their work environment, thereby achieving greater efficiency.
This method aims to standardize production processes so that they are repeatable, measurable and predictable. Cleaning, sorting and packing are all done daily. Because workers know what they can expect, this helps them perform their jobs more efficiently.
There are five steps that you need to follow in order to implement 5S. Each step requires a different action, which increases efficiency. For example, when you sort things, you make them easy to find later. Once you have placed items in an ordered fashion, you will put them together. Once you have separated your inventory into groups and organized them, you will store these groups in easily accessible containers. Finally, label all containers correctly.
This process requires employees to think critically about how they do their job. Employees need to understand the reasons they do certain jobs and determine if there is a better way. In order to use the 5S system effectively, they must be able to learn new skills.
The 5S Method not only improves efficiency, but it also helps employees to be more productive and happier. They are more motivated to achieve higher efficiency levels as they start to see improvement.