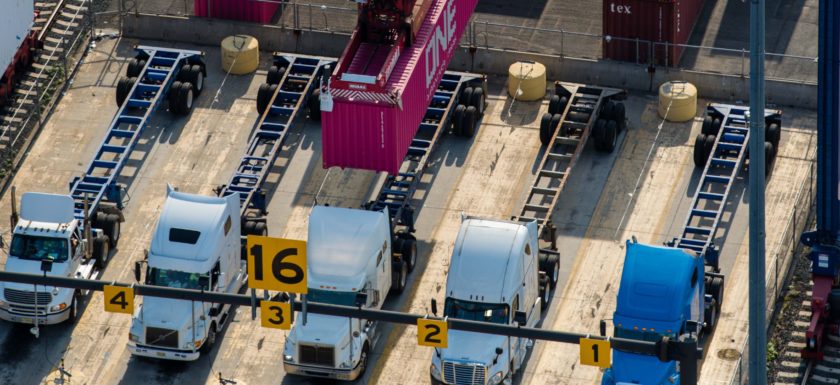
Lean services is a process that applies lean manufacturing production techniques to the service sector. This approach has been adopted by companies such as HMRC in the UK and US health care providers. Lean services aim to reduce waste, improve customer satisfaction and lower costs. No matter if you're a small business or a large corporation, lean services will help to improve your company.
Lean manufacturing
Lean manufacturing is an approach to eliminating waste. Lean manufacturing helps companies increase their productivity, decrease operating costs, and improve employee satisfaction. It can also increase profits. It can help increase profits and speed up product development. Companies can increase their customer base, and their revenue streams by using lean manufacturing services.
Lean manufacturing requires a team approach and a lot of talent. It is important that everyone on the team understands the process and how it works. Additionally, they must be able adapt the practices to suit the company's needs. The first step to lean manufacturing is to simplify manufacturing processes. Complex manufacturing processes make it hard to spot waste or inefficiencies. Simpler processes allow for better visibility and encourage continuous improvement. This will allow your employees the freedom to search for inefficiencies.
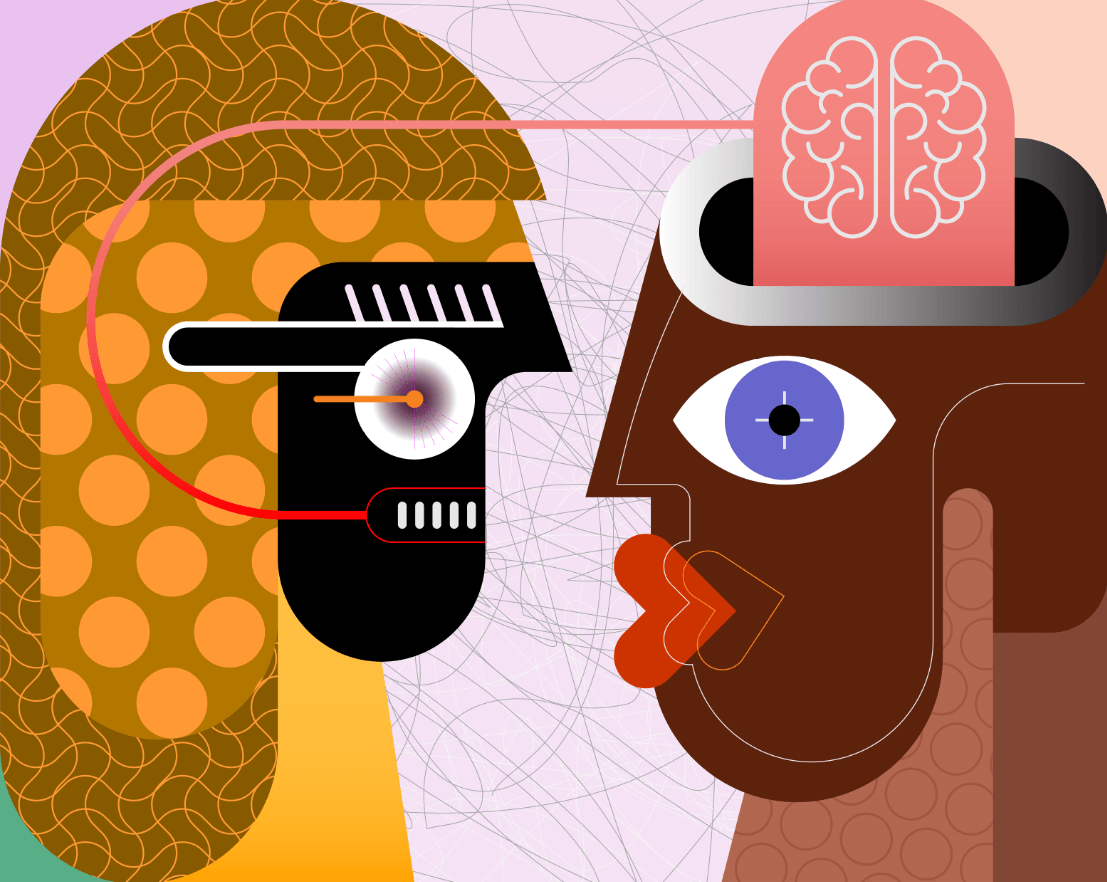
Lean manufacturing services can help companies improve their efficiency by reducing their lead time. MXGlobal, one of these companies that offers lean implementation has successfully consulted Japanese firms with a U.S. present. The firm's lean manufacturing services are aimed at helping businesses grow internationally and achieve their business goals.
Lean manufacturing services can help businesses create a working environment that maximizes profit. They work to reduce waste and increase productivity. Lean manufacturing has eight types. They include excess production, inventory, and transport. These wastes could increase costs or decrease customer satisfaction.
Lean operations management
Organizations must first identify what they want to achieve in order to implement lean operations management. This systematic approach focuses on creating value to the customer. Customers expect value from products and services. It is what drives sales. To get started, consider mapping all steps in the creation of a product or service and ask, "What adds value to the customer?"
Continuous improvement is the goal of lean management systems. This is the most important part of lean management. This ensures your team delivers work assignments consistently in a shorter amount of time and with less effort. It reduces production waste and optimizes overheads. Lean management's four principles include continuous improvement, minimizing waste and reducing cycle times. They also ensure continuous workflows.
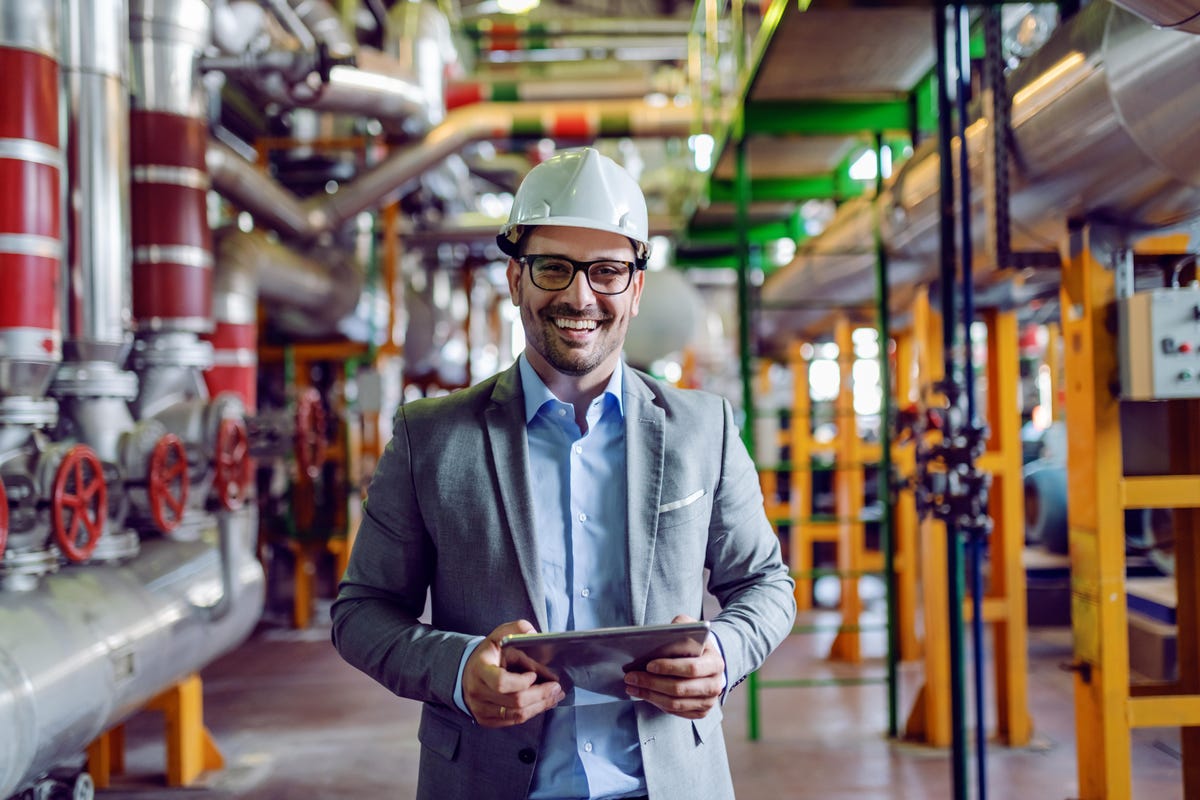
Lean operations management for services is about creating more value to customers with less resources. Intangible wastes are harder to identify in a service environment, but lean principles work to reduce and eliminate them. Companies can increase their customer value and maximize profits by eliminating waste.
FAQ
What is the distinction between Production Planning or Scheduling?
Production Planning (PP) refers to the process of determining how much production is needed at any given moment. This is done through forecasting demand and identifying production capacities.
Scheduling refers the process by which tasks are assigned dates so that they can all be completed within the given timeframe.
What is production plan?
Production Planning is the creation of a plan to cover all aspects, such as scheduling, budgeting. Location, crew, equipment, props and other details. This document ensures that everything is prepared and available when you are ready for shooting. You should also have information to ensure the best possible results on set. This includes information on shooting times, locations, cast lists and crew details.
First, you need to plan what you want to film. You might have an idea of where you want to film, or you may have specific locations or sets in mind. Once you have identified your locations and scenes it's time to begin figuring out what elements you will need for each one. Perhaps you have decided that you need to buy a car but aren't sure which model. To narrow your options, you can search online for available models.
After you have chosen the right car, you will be able to begin thinking about accessories. Are you looking for people to sit in the front seats? Or maybe you just need someone to push the car around. Maybe you'd like to change the interior from black to a white color. These questions will help to determine the style and feel of your car. Also, think about what kind of shots you would like to capture. What type of shots will you choose? Perhaps you want to show the engine or the steering wheel? These details will help identify the exact car you wish to film.
Once you have made all the necessary decisions, you can start to create a schedule. You can create a schedule that will outline when you must start and finish your shoots. Each day will include the time when you need to arrive at the location, when you need to leave and when you need to return home. Everyone will know what they need and when. It is possible to make arrangements in advance for additional staff if you are looking to hire. You don't want to hire someone who won't show up because he didn't know.
When creating your schedule, you will also need to consider the number of days you need to film. Some projects only take one or two days, while others may last weeks. It is important to consider whether you require more than one photo per day when you create your schedule. Multiple takes at the same place will result in higher costs and longer completion times. It is better to be cautious and take fewer shots than you risk losing money if you are not sure if multiple takes are necessary.
Another important aspect of production planning is setting budgets. As it will allow you and your team to work within your financial means, setting a realistic budget is crucial. Remember that you can always reduce the budget later on if you run into unforeseen problems. But, don't underestimate how much money you'll spend. If you underestimate the cost of something, you will have less money left after paying for other items.
Production planning is a complicated process. But once you understand how everything works together, it becomes much easier to plan future project.
What is the role of a production manager?
Production planners make sure that every aspect of the project is delivered on-time, within budget, and within schedule. They also ensure that the product/service meets the client’s needs.
What is the job of a logistics manger?
Logistics managers make sure all goods are delivered on schedule and without damage. This is achieved by using their knowledge and experience with the products of the company. He/she should make sure that enough stock is on hand to meet the demands.
How can manufacturing efficiency be improved?
First, we need to identify which factors are most critical in affecting production times. We then need to figure out how to improve these variables. If you aren't sure where to begin, think about the factors that have the greatest impact on production time. Once you've identified them all, find solutions to each one.
Is automation necessary in manufacturing?
Not only is automation important for manufacturers, but it's also vital for service providers. It allows them provide faster and more efficient services. It reduces human errors and improves productivity, which in turn helps them lower their costs.
How does a Production Planner differ from a Project Manager?
The primary difference between a producer planner and a manager of a project is that the manager usually plans and organizes the whole project, while a production planner is only involved in the planning stage.
Statistics
- Job #1 is delivering the ordered product according to specifications: color, size, brand, and quantity. (netsuite.com)
- [54][55] These are the top 50 countries by the total value of manufacturing output in US dollars for its noted year according to World Bank.[56] (en.wikipedia.org)
- It's estimated that 10.8% of the U.S. GDP in 2020 was contributed to manufacturing. (investopedia.com)
- (2:04) MTO is a production technique wherein products are customized according to customer specifications, and production only starts after an order is received. (oracle.com)
- In 2021, an estimated 12.1 million Americans work in the manufacturing sector.6 (investopedia.com)
External Links
How To
Six Sigma: How to Use it in Manufacturing
Six Sigma can be described as "the use of statistical process control (SPC), techniques to achieve continuous improvement." Motorola's Quality Improvement Department developed it at their Tokyo plant in Japan in 1986. Six Sigma is a method to improve quality through standardization and elimination of defects. Since there are no perfect products, or services, this approach has been adopted by many companies over the years. Six Sigma's primary goal is to reduce variation from the average value of production. If you take a sample and compare it with the average, you will be able to determine how much of the production process is different from the norm. If it is too large, it means that there are problems.
Understanding how variability works in your company is the first step to Six Sigma. Once you've understood that, you'll want to identify sources of variation. It is important to identify whether the variations are random or systemic. Random variations happen when people make errors; systematic variations are caused externally. For example, if you're making widgets, and some of them fall off the assembly line, those would be considered random variations. You might notice that your widgets always fall apart at the same place every time you put them together.
After identifying the problem areas, you will need to devise solutions. That solution might involve changing the way you do things or redesigning the process altogether. After implementing the new changes, you should test them again to see if they worked. If they don't work you need to rework them and come up a better plan.