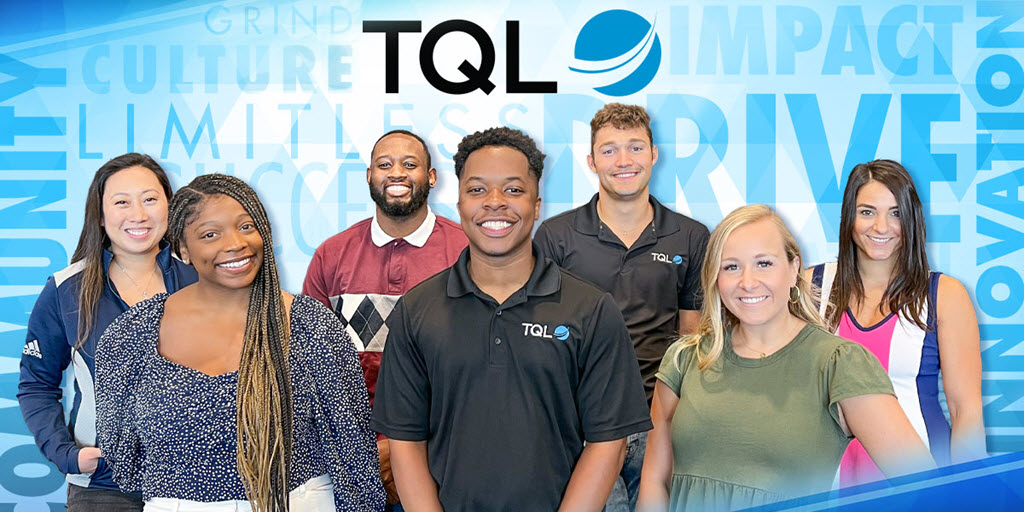
Many factors have contributed to a large chip shortage in recent times. These include manufacturing and transportation problems. In addition, there have been numerous disasters that have led to the shutdown of some chip plants. This has affected consumer devices such as gaming consoles, healthcare devices, and data centers. The Chinese government has made several efforts to support semiconductor manufacturing in China. A fund for investment has been created by the Chinese government to support chip makers.
China's chip production has experienced remarkable growth over the past few year as a direct result of this effort. According to IC Insights the growth in chip production in China is expected to be 19.4% by 2025. But the industry has a long way ahead of it before it reaches its former status. Despite these achievements, the number domestic chip companies remains small. Many of these companies aren't yet independent.
Huawei, Oppo, Midea and Xiaomi are some of China's top chip makers. Chinese companies also have a significant market share of the mobile processor sector. They are also creating their own chips, which allows them to increase their chip making capabilities. This has helped to make them more competitive in the industry.
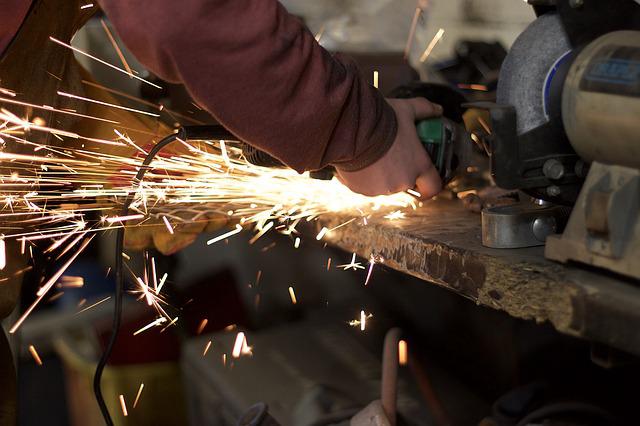
China is fast becoming a global hub for chip manufacturing. But there are still challenges. Chinese companies have limited resources and are not able to mass-produce high end microchips. These chips are used in smartphones and other wearable devices as well as servers. The country is also not yet able to produce the raw materials necessary for chip manufacturing. These include enriched isotopes, tantalum, and neon. These raw materials are refined through chemical processes.
The Chinese government is also keen to decrease its dependence upon imported chips. China hopes to have 70% of its chip production in China by 2025. But this will take many years. China has 32 chip companies currently registered, with many more awaiting IPOs. The government is also marketing its industrial policy. It hopes to encourage companies to produce more chips in the country, which is a significant challenge given the limited resources available.
The US semiconductor market is experiencing an unprecedented shortage. Washington also recently adopted new rules to limit the US's ability to support chip production.
TSMC, the largest chipmaker in the world, has yet to make any announcements regarding a European plant. But it has not ruled out building an older-generation chip plant there. The company has also partnered with European automakers to purchase less-advanced chips. The idea has been resisted by most European auto companies. The addition of a European plant to the supply chain would increase its complexity. This would mean that chips would need to be shipped back from Asia for processing. This could add several years to the chip's lifespan.
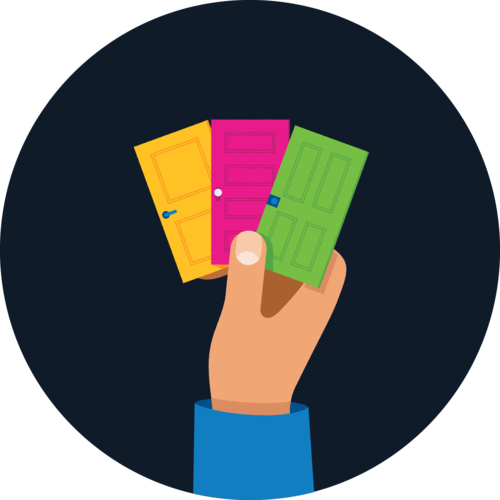
According to a report by the US Commerce Department, the chip shortage will become bad in 2021. This has caused long delays for consumers. The shortage has also had a negative impact on transportation, healthcare, as well as gaming consoles. The US government will invest in reshoring chips production to create thousands of jobs and ensure a more resilient chip supply.
FAQ
How does manufacturing avoid bottlenecks in production?
Production bottlenecks can be avoided by ensuring that processes are running smoothly during the entire production process, starting with the receipt of an order and ending when the product ships.
This includes both quality control and capacity planning.
The best way to do this is to use continuous improvement techniques such as Six Sigma.
Six Sigma management is a system that improves quality and reduces waste within your organization.
It's all about eliminating variation and creating consistency in work.
Why automate your factory?
Modern warehouses have become more dependent on automation. Increased demand for efficient and faster delivery has resulted in a rise in e-commerce.
Warehouses have to be flexible to meet changing requirements. To do so, they must invest heavily in technology. Automation warehouses can bring many benefits. These are some of the benefits that automation can bring to warehouses:
-
Increases throughput/productivity
-
Reduces errors
-
Increases accuracy
-
Boosts safety
-
Eliminates bottlenecks
-
This allows companies to scale easily
-
Makes workers more efficient
-
This gives you visibility into what happens in the warehouse
-
Enhances customer experience
-
Improves employee satisfaction
-
Reduces downtime and improves uptime
-
You can be sure that high-quality products will arrive on time
-
Removes human error
-
Assure compliance with regulations
How does a Production Planner differ from a Project Manager?
A production planner is more involved in the planning phase of the project than a project manger.
Statistics
- You can multiply the result by 100 to get the total percent of monthly overhead. (investopedia.com)
- In the United States, for example, manufacturing makes up 15% of the economic output. (twi-global.com)
- In 2021, an estimated 12.1 million Americans work in the manufacturing sector.6 (investopedia.com)
- [54][55] These are the top 50 countries by the total value of manufacturing output in US dollars for its noted year according to World Bank.[56] (en.wikipedia.org)
- According to the United Nations Industrial Development Organization (UNIDO), China is the top manufacturer worldwide by 2019 output, producing 28.7% of the total global manufacturing output, followed by the United States, Japan, Germany, and India.[52][53] (en.wikipedia.org)
External Links
How To
How to Use the 5S to Increase Productivity In Manufacturing
5S stands in for "Sort", the "Set In Order", "Standardize", or "Separate". The 5S methodology was developed at Toyota Motor Corporation in 1954. It improves the work environment and helps companies to achieve greater efficiency.
This approach aims to standardize production procedures, making them predictable, repeatable, and easily measurable. This means that tasks such as cleaning, sorting, storing, packing, and labeling are performed daily. Because workers know what they can expect, this helps them perform their jobs more efficiently.
Implementing 5S requires five steps. These are Sort, Set In Order, Standardize. Separate. And Store. Each step has a different action and leads to higher efficiency. You can make it easy for people to find things later by sorting them. When items are ordered, they are put together. Next, organize your inventory into categories and store them in containers that are easily accessible. You can also label your containers to ensure everything is properly labeled.
This requires employees to critically evaluate how they work. Employees need to be able understand their motivations and discover alternative ways to do them. In order to use the 5S system effectively, they must be able to learn new skills.
In addition to increasing efficiency, the 5S method also improves morale and teamwork among employees. They feel more motivated to work towards achieving greater efficiency as they see the results.