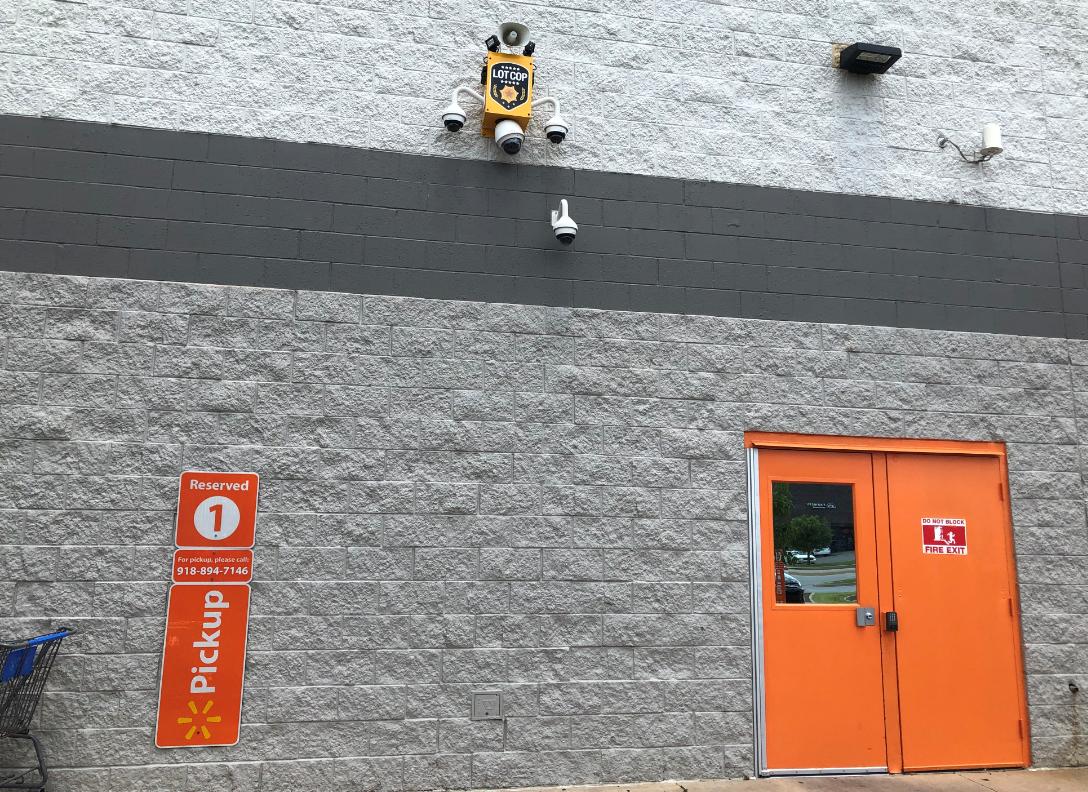
Denver in Colorado offers many different jobs. It also has several logistics companies which offer a variety of logistics services. These include trucking, freight forwarding and logistics & Supply Chain Consulting.
If you're interested in a career in logistics, you may want to consider a number of different positions, such as dispatcher, transportation director and warehouse assistant. All of these positions have the responsibility of ensuring that logistics are run smoothly in an organization.
Dispatch Manager
A dispatcher's main responsibility is to direct and coordinate the work of a group that operates in a contact center or warehouse. This includes evaluating productivity, training new employees, delegating work, and coordinating workloads of team members. Dispatch managers usually have a bachelor's degree in business management or logistics and experience with workflow organization.
Transportation Director
Transportation directors are responsible for the logistics of a school, governmental department or company. This includes setting up distribution channels and arranging for transport methods such as trucks or buses to move products from one location.
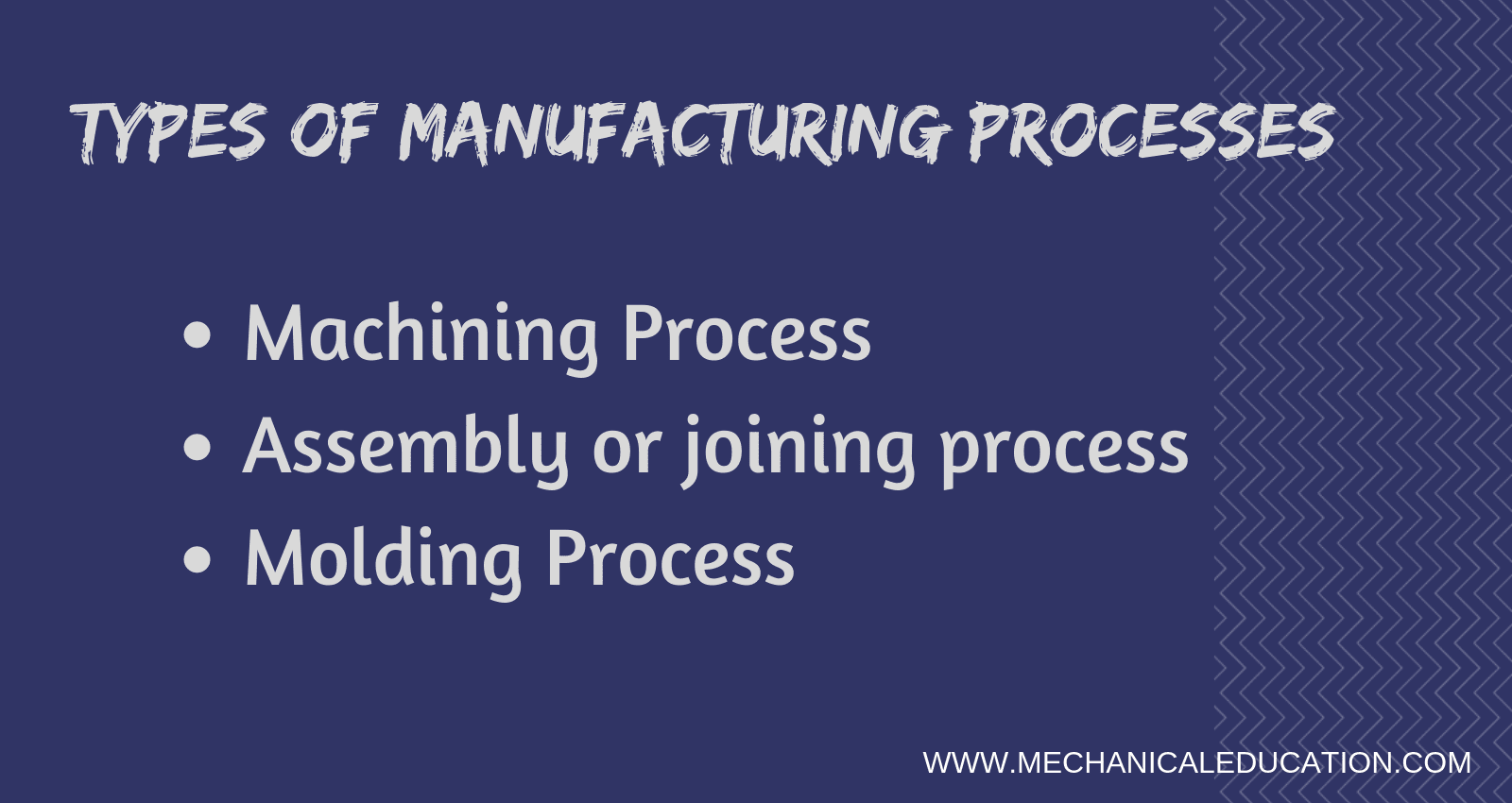
This career suits those who would like to work for an organization or government agency. This is a highly competitive career, so you must have good organizational skills and be willing work long hours.
Warehouse Associate
A warehouse associate may be the right job for you if your schedule is flexible and you don't want to compete with other candidates. A warehouse associate typically handles smaller projects such as picking shipments, packing products, and moving merchandise to other locations.
The best way to start your search for a job in the logistics industry is to set up a profile on Monster. This will let you be notified when there are new logistics jobs available near you.
In addition, you will be able to receive expert advice about how to make the most of your job application, how to negotiate your salary, and more.
Logistics Manager
A bachelor's in supply management or business administration is required to become a manager of logistics. It is necessary to have a minimum of a year's professional experience in warehouse environments, and strong organization skills. You can also earn a master's degree in supply chain management or another related field to become a senior logistics manager.
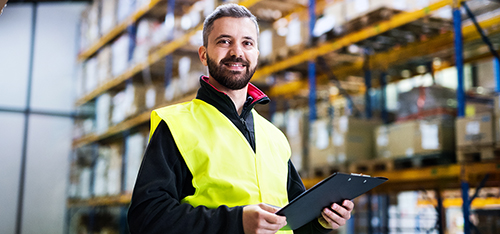
Logistik Analyst
A logistic analyst monitors the logistics of a company and works to make changes that will help the company better meet its goals. This includes evaluating the inventory levels, scheduling deliveries, and determining budget restrictions. A logistics analyst needs to have a bachelor's degree in business or engineering and must have experience with the logistics of a specific industry.
Logistics is a growing industry and there are a lot of jobs available. You can create a free Monster account to get started in this career. You will have a better chance to find the perfect logistics job.
FAQ
What is the role of a manager in manufacturing?
The manufacturing manager should ensure that every manufacturing process is efficient and effective. They should be aware of any issues within the company and respond accordingly.
They should also be able and comfortable communicating with other departments like sales and marketing.
They should also be knowledgeable about the latest trends in the industry so they can use this information for productivity and efficiency improvements.
Is it necessary to be familiar with Manufacturing Processes before we learn about Logistics.
No. No. But, being familiar with manufacturing processes will give you a better understanding about how logistics works.
What does it mean to be a manufacturer?
Manufacturing Industries are companies that manufacture products. Consumers are the people who purchase these products. These companies use various processes such as production, distribution, retailing, management, etc., to fulfill this purpose. These companies produce goods using raw materials and other equipment. This includes all types of manufactured goods, including food items, clothing, building supplies, furniture, toys, electronics, tools, machinery, vehicles, pharmaceuticals, medical devices, chemicals, and many others.
What are the main products of logistics?
Logistics is the process of moving goods from one point to another.
They include all aspects associated with transport including packaging, loading transporting, unloading storage, warehousing inventory management customer service, distribution returns and recycling.
Logisticians ensure the product reaches its destination in the most efficient manner. They help companies manage their supply chain efficiency by providing information on demand forecasts, stock levels, production schedules, and availability of raw materials.
They also keep track of shipments in transit, monitor quality standards, perform inventories and order replenishment, coordinate with suppliers and vendors, and provide support services for sales and marketing.
Statistics
- Job #1 is delivering the ordered product according to specifications: color, size, brand, and quantity. (netsuite.com)
- According to a Statista study, U.S. businesses spent $1.63 trillion on logistics in 2019, moving goods from origin to end user through various supply chain network segments. (netsuite.com)
- Many factories witnessed a 30% increase in output due to the shift to electric motors. (en.wikipedia.org)
- You can multiply the result by 100 to get the total percent of monthly overhead. (investopedia.com)
- [54][55] These are the top 50 countries by the total value of manufacturing output in US dollars for its noted year according to World Bank.[56] (en.wikipedia.org)
External Links
How To
How to Use Six Sigma in Manufacturing
Six Sigma refers to "the application and control of statistical processes (SPC) techniques in order to achieve continuous improvement." Motorola's Quality Improvement Department developed it at their Tokyo plant in Japan in 1986. Six Sigma's core idea is to improve the quality of processes by standardizing and eliminating defects. Many companies have adopted this method in recent years. They believe there is no such thing a perfect product or service. The main goal of Six Sigma is to reduce variation from the mean value of production. This means that if you take a sample of your product, then measure its performance against the average, you can find out what percentage of the time the process deviates from the norm. If you notice a large deviation, then it is time to fix it.
The first step toward implementing Six Sigma is understanding how variability works in your business. Once you've understood that, you'll want to identify sources of variation. You'll also want to determine whether these variations are random or systematic. Random variations are caused when people make mistakes. While systematic variations are caused outside of the process, they can occur. For example, if you're making widgets, and some of them fall off the assembly line, those would be considered random variations. If however, you notice that each time you assemble a widget it falls apart in exactly the same spot, that is a problem.
After identifying the problem areas, you will need to devise solutions. It might mean changing the way you do business or redesigning it entirely. To verify that the changes have worked, you need to test them again. If they don't work, you will need to go back to the drawing boards and create a new plan.