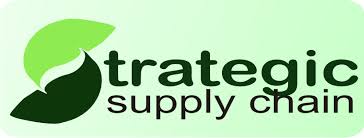
Medical equipment manufacturers manufacture products used by doctors and nurses as well hospital staff. These companies provide a variety of equipment such as medical beds, wheelchairs and oxygen tanks. They also offer monitors, ventilators and other devices. The medical sector is expected to grow from $135 billion in 2014 to $135 trillion by 2024.
Transport Equipment
Some medical devices are transported via truck or airplane. Some medical equipments may have to travel across the nation or even overseas. Manufacturers that produce this type of equipment also need to ensure that they have a reliable and trustworthy transportation system in place.
Manufacturing:
Some of the most popular processes that are involved in manufacturing medical devices include micromachining and injection molding. These processes demand specialized equipment, high quality materials and sterile manufacturing environments.
Get the right certification:
FDA regulations apply to a large number of products manufactured in this sector. Medical device manufacturers must be ISO 13485 Certified to remain in compliance. This non-government organisation inspects and certifies manufacturing companies based on their quality and consistency.
Usability:
The user-friendliness of a device should be one of the main factors in its design. This means it should be easy to operate and use, for both those using the product as well as those manufacturing it. This can include many factors, such as the size and form of the product and its ease in handling and moving.
The Product Design:
When designing a medical device, it is important to consider all of the components that will make up the final product. The shape, the materials, and any other features that make it special are all considered. It is also important to ensure that the product is safe.
Best Medical Equipment:
Some of the most effective medical equipments were designed to be easy-to-use and perform their intended function. This will increase their success and longevity in the market.
The medical device must also be constructed from a material easy to clean and disinfect. This can reduce the risk of cross-contamination and infection in hospitals or other care settings.
It is important to keep in mind that medical devices have specific applications. Their design should therefore be tailored for that particular application. It is important to remember that medical devices are designed to be used in specific applications and should therefore be tailored to suit that application.
It is also well-known for its large variety of products, which can be tailored to meet a wide range of medical preferences and needs. For instance, it offers a number of wheelchairs and other equipment that can be adjusted to the patient's height.
Merit Medical, a leading manufacturer of medical equipments, strives to provide innovative and life-changing devices to healthcare providers and patients around the globe. The company's dedication to providing excellent customer service and innovative products has allowed it to grow into a major supplier of disposable medical devices.
FAQ
What is the role of a production manager?
A production planner ensures all aspects of the project are delivered on time, within budget, and within scope. They make sure that the product and services meet client expectations.
What are the 4 types manufacturing?
Manufacturing is the process that transforms raw materials into useful products. Manufacturing can include many activities such as designing and building, testing, packaging shipping, selling, servicing, and other related activities.
Why automate your factory?
Automation has become increasingly important in modern warehousing. Increased demand for efficient and faster delivery has resulted in a rise in e-commerce.
Warehouses should be able adapt quickly to new needs. To do so, they must invest heavily in technology. Automation of warehouses offers many benefits. These are just a few reasons to invest in automation.
-
Increases throughput/productivity
-
Reduces errors
-
Improves accuracy
-
Safety Boosts
-
Eliminates bottlenecks
-
This allows companies to scale easily
-
Increases efficiency of workers
-
This gives you visibility into what happens in the warehouse
-
Enhances customer experience
-
Improves employee satisfaction
-
Minimizes downtime and increases uptime
-
High quality products delivered on-time
-
Removing human error
-
Assure compliance with regulations
How is a production manager different from a producer planner?
The primary difference between a producer planner and a manager of a project is that the manager usually plans and organizes the whole project, while a production planner is only involved in the planning stage.
What are the jobs in logistics?
There are many kinds of jobs available within logistics. Some of them are:
-
Warehouse workers – They load, unload and transport pallets and trucks.
-
Transportation drivers - They drive trucks and trailers to deliver goods and carry out pick-ups.
-
Freight handlers are people who sort and pack freight into warehouses.
-
Inventory managers - These are responsible for overseeing the stock of goods in warehouses.
-
Sales reps are people who sell products to customers.
-
Logistics coordinators - They organize and plan logistics operations.
-
Purchasing agents - They purchase goods and services needed for company operations.
-
Customer service representatives are available to answer customer calls and emails.
-
Shippers clerks - They process shipping order and issue bills.
-
Order fillers – They fill orders based upon what was ordered and shipped.
-
Quality control inspectors - They check incoming and outgoing products for defects.
-
Others - There are many types of jobs in logistics such as transport supervisors and cargo specialists.
What are the requirements to start a logistics business?
It takes a lot of skills and knowledge to run a successful logistics business. Effective communication skills are necessary to work with suppliers and clients. You will need to know how to interpret data and draw conclusions. You need to be able work under pressure and manage stressful situations. To improve efficiency, you must be innovative and creative. You need to have strong leadership qualities to motivate team members and direct them towards achieving organizational goals.
It is also important to be efficient and well organized in order meet deadlines.
How can manufacturing efficiency be improved?
First, identify the factors that affect production time. Next, we must find ways to improve those factors. If you don't know where to start, then think about which factor(s) have the biggest impact on production time. Once you've identified them all, find solutions to each one.
Statistics
- In the United States, for example, manufacturing makes up 15% of the economic output. (twi-global.com)
- You can multiply the result by 100 to get the total percent of monthly overhead. (investopedia.com)
- According to the United Nations Industrial Development Organization (UNIDO), China is the top manufacturer worldwide by 2019 output, producing 28.7% of the total global manufacturing output, followed by the United States, Japan, Germany, and India.[52][53] (en.wikipedia.org)
- In 2021, an estimated 12.1 million Americans work in the manufacturing sector.6 (investopedia.com)
- (2:04) MTO is a production technique wherein products are customized according to customer specifications, and production only starts after an order is received. (oracle.com)
External Links
How To
Six Sigma and Manufacturing
Six Sigma can be described as "the use of statistical process control (SPC), techniques to achieve continuous improvement." Motorola's Quality Improvement Department in Tokyo, Japan developed Six Sigma in 1986. Six Sigma's basic concept is to improve quality and eliminate defects through standardization. Many companies have adopted this method in recent years. They believe there is no such thing a perfect product or service. Six Sigma's primary goal is to reduce variation from the average value of production. You can calculate the percentage of deviation from the norm by taking a sample of your product and comparing it to the average. If you notice a large deviation, then it is time to fix it.
Understanding how your business' variability is a key step towards Six Sigma implementation is the first. Once you understand this, you can then identify the causes of variation. This will allow you to decide if these variations are random and systematic. Random variations happen when people make errors; systematic variations are caused externally. For example, if you're making widgets, and some of them fall off the assembly line, those would be considered random variations. It would be considered a systematic problem if every widget that you build falls apart at the same location each time.
Once you've identified where the problems lie, you'll want to design solutions to eliminate those problems. That solution might involve changing the way you do things or redesigning the process altogether. You should then test the changes again after they have been implemented. If they don't work you need to rework them and come up a better plan.