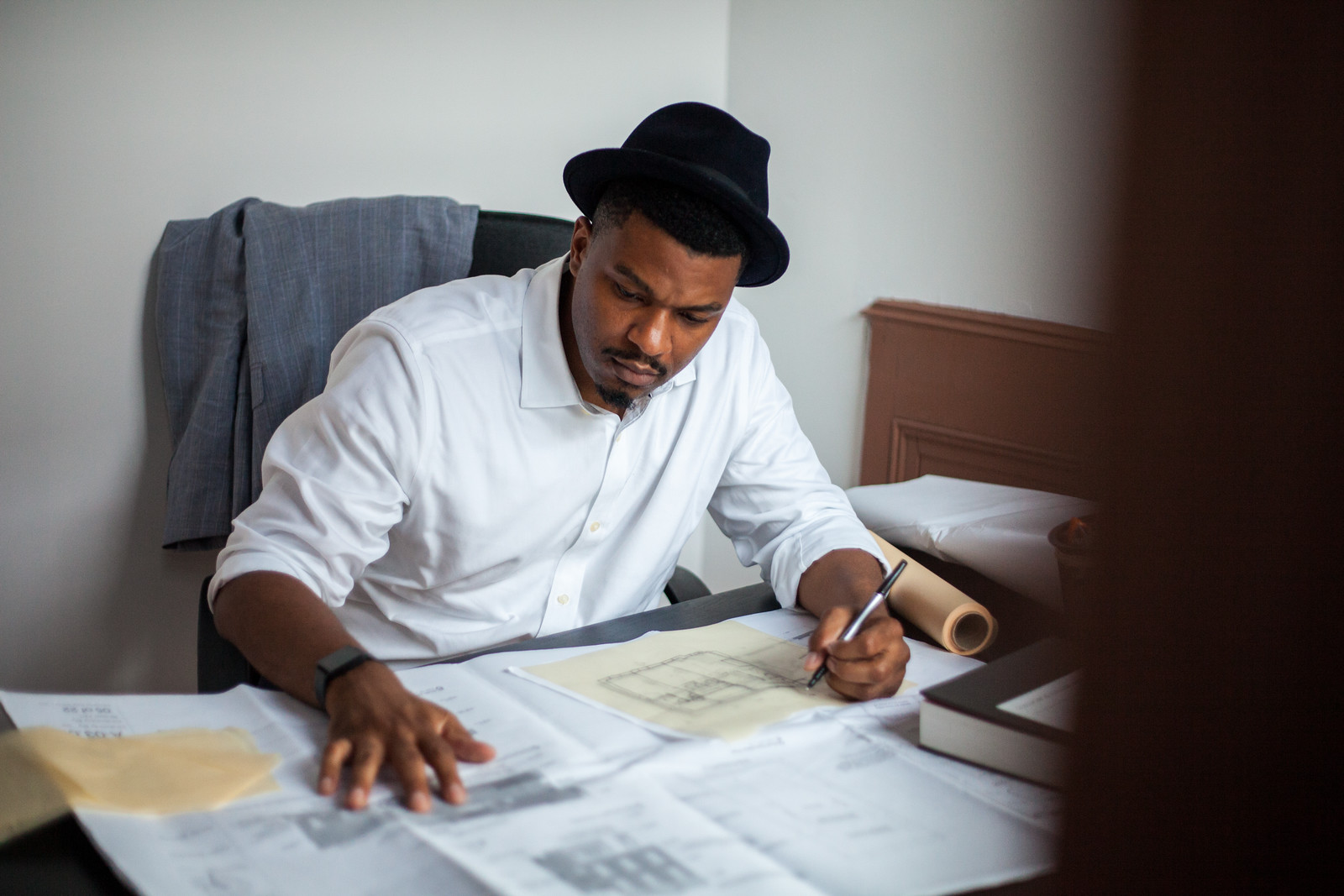
Visual management is the act of using visual signals to convey information. This method increases efficiency and clarity by recognizing information immediately. There are several types of visual control, including: process control charts, FIFO lane, and Lean daily management board. These are just a few of the most commonly used examples. Also, you can read more about visual control in Lean manufacturing. Continue reading to find out more. This is a great way for your company to adopt lean manufacturing.
Lean manufacturing
Andon, which refers to status-display visualization in Japanese, is one of the many methods that can be used for visual management. This helps supervisors and workers to see the status of their work, process flow, and any other relevant information. Visual management also allows you to label workspaces, materials and parts. It helps to identify inefficiencies and streamline processes. Listed below are some of the benefits of visual management in lean manufacturing.
Lean's core principle is to use visible tools for visual management. Supervisors and operators can use visual signals to identify waste, improve process flow and avoid errors. Additionally, it can reduce safety concerns. Floor markings and other visual indicators can help forklift drivers stay in the right places. Workers can work more efficiently by using visual management when lean manufacturing is used. Safety risks can be minimized by visual management.
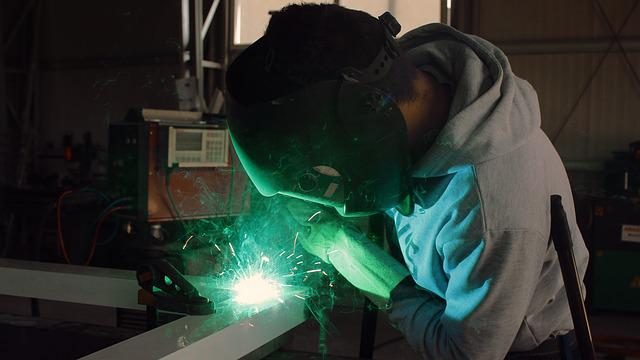
Process control charts
Process control charts can be an effective tool to visualize performance metrics, set a baseline for future improvements, and improve output. They are a way for managers, operators, and all other stakeholders to communicate and agree on common causes and the best path forward. These charts are particularly helpful for processes that exhibit unusual patterns or variation. These process control charts are useful for visual management. They are easy to create, and can be used as visual indicators to see the status of any process.
A control chart's primary purpose is to monitor the process' performance over time. These charts display the sequence of samples and measurements that allow managers to determine whether or not the process is stable. These charts can also be used for analytic purposes to identify and propose solutions. A line segment is a segment that connects the centerline of a control chart. This allows an operator to easily compare the process's performance to its baseline. The control limits usually have three standard deviations from the centerline.
FIFO Lane
FIFO lanes may increase throughput or utilization of a system. Take a look at a production line or counter that sells fast food. It is likely that you have felt the frustration of having to wait in long lines for something. FiFo helps you manage your work flow by setting priority in the queues through visual management. You can define these lanes by placing painted lines on the floor, markings on roller conveyors, and clearly marked shelf spaces. Process A's first job would be moved into the first FIFO lane open. The next job would go into the open position.
Implementing time registration can be a great way to improve FIFO lane visual organization. Employees can track the date and time that carts are placed in a FIFO lane by recording the time and date. Some employees use digital counters to count how many products are in each FIFO lane. You can also install whiteboard stickers to write down times on carts. This way, downstream employees can refer to these times to determine which order to take next.
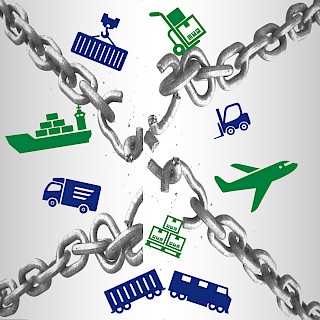
Lean daily management board
The Lean Daily Management Board was established by a multidisciplinary team that was based upon five predetermined metrics. They were: patient outcomes and documentation adherence, employee engagement, productivity, and employee engagement. This team met every day to review progress in each area. To verify every daily activity, the team used a checklist. To address any problems, they also used a problem-solving tool. The initial data collected in January 2014 noted a medication scan rate of 75% and a fall rate of 1.32/1000 patient days. These initial data weren't specific to patient care nor continuing education.
Daily management allows for a more visible view of the process and allows for managers to address problems as they arise. Poor performers stretch out work to avoid being asked to do more. The poor performers need to be aware of the extra effort and time they spend on their work by making stretching work visible. Even though daily management doesn't have to be harsh, it does help highlight inefficient and ineffective processes. People should be able to point out the failure of a process.
FAQ
How is a production manager different from a producer planner?
The difference between a product planner and project manager is that a planer is typically the one who organizes and plans the entire project. A production planner, however, is mostly involved in the planning stages.
What skills should a production planner have?
Being a production planner is not easy. You need to be organized and flexible. Effective communication with clients and colleagues is essential.
How does manufacturing avoid bottlenecks in production?
Avoiding production bottlenecks is as simple as keeping all processes running smoothly, from the time an order is received until the product ships.
This includes planning for both capacity requirements and quality control measures.
Continuous improvement techniques like Six Sigma are the best way to achieve this.
Six Sigma can be used to improve the quality and decrease waste in all areas of your company.
It focuses on eliminating variation and creating consistency in your work.
What are the goods of logistics?
Logistics is the process of moving goods from one point to another.
They include all aspects associated with transport including packaging, loading transporting, unloading storage, warehousing inventory management customer service, distribution returns and recycling.
Logisticians ensure the product reaches its destination in the most efficient manner. They provide information on demand forecasts as well stock levels, production schedules and availability of raw material.
They can also track shipments in transit and monitor quality standards.
What is the best way to learn about manufacturing?
You can learn the most about manufacturing by getting involved in it. However, if that's not possible, you can always read books or watch educational videos.
Statistics
- In 2021, an estimated 12.1 million Americans work in the manufacturing sector.6 (investopedia.com)
- In the United States, for example, manufacturing makes up 15% of the economic output. (twi-global.com)
- It's estimated that 10.8% of the U.S. GDP in 2020 was contributed to manufacturing. (investopedia.com)
- Job #1 is delivering the ordered product according to specifications: color, size, brand, and quantity. (netsuite.com)
- According to a Statista study, U.S. businesses spent $1.63 trillion on logistics in 2019, moving goods from origin to end user through various supply chain network segments. (netsuite.com)
External Links
How To
How to Use the Just In Time Method in Production
Just-in time (JIT), is a process that reduces costs and increases efficiency in business operations. It is a process where you get the right amount of resources at the right moment when they are needed. This means that you only pay for what you actually use. The term was first coined by Frederick Taylor, who developed his theory while working as a foreman in the early 1900s. He noticed that workers were often paid overtime when they had to work late. He decided that workers would be more productive if they had enough time to complete their work before they started to work.
JIT is a way to plan ahead and make sure you don't waste any money. Look at your entire project, from start to end. Make sure you have enough resources in place to deal with any unexpected problems. If you expect problems to arise, you will be able to provide the necessary equipment and personnel to address them. This will prevent you from spending extra money on unnecessary things.
There are different types of JIT methods:
-
Demand-driven: This JIT is where you place regular orders for the parts/materials that are needed for your project. This will allow for you to track the material that you have left after using it. It will also allow you to predict how long it takes to produce more.
-
Inventory-based: This type allows you to stock the materials needed for your projects ahead of time. This allows you predict the amount you can expect to sell.
-
Project-driven: This approach involves setting aside sufficient funds to cover your project's costs. Knowing how much money you have available will help you purchase the correct amount of materials.
-
Resource-based JIT: This is the most popular form of JIT. Here, you allocate certain resources based on demand. You will, for example, assign more staff to deal with large orders. If you don't have many orders, you'll assign fewer people to handle the workload.
-
Cost-based: This is the same as resource-based except that you don't care how many people there are but how much each one of them costs.
-
Price-based: This is very similar to cost-based, except that instead of looking at how much each individual worker costs, you look at the overall price of the company.
-
Material-based - This is a variant of cost-based. But instead of looking at the total company cost, you focus on how much raw material you spend per year.
-
Time-based: This is another variation of resource-based JIT. Instead of focusing on how much each employee costs, you focus on how long it takes to complete the project.
-
Quality-based JIT: Another variation on resource-based JIT. Instead of focusing on the cost of each worker or how long it takes, think about how high quality your product is.
-
Value-based: This is one of the newest forms of JIT. In this case, you're not concerned with how well the products perform or whether they meet customer expectations. Instead, your goal is to add value to the market.
-
Stock-based: This is an inventory-based method that focuses on the actual number of items being produced at any given time. It's used when you want to maximize production while minimizing inventory.
-
Just-in-time (JIT) planning: This is a combination of JIT and supply chain management. It refers to the process of scheduling the delivery of components as soon as they are ordered. It's important as it reduces leadtimes and increases throughput.