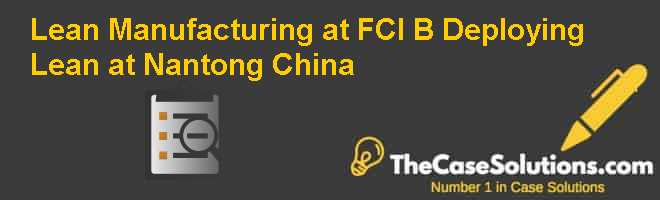
Art Byrne's tenure as CEO at Wiremold saw a number of innovations that were instrumental in achieving the company's goals of reducing expenses and increasing production. Byrne displayed a keen understanding and ability to motivate the entire team through this case study in lean manufacturing. While implementing the improvements, Byrne encouraged his team to learn by doing and enlisted everyone in the kaizen process.
He created a lean manufacturing program that tracked parts flow through the production process. He introduced many tools to decrease waste and increase productivity. He also introduced a laser-cutting machine that made it possible to produce small batches and save on tooling. His success was due in large part to his lean strategy which consisted of just a few easy steps.
He also used a JIT manufacturing process. The company could deliver vehicles in a very short time frame thanks to this manufacturing method. It also allowed for harmony through the manufacturing process, which was the key to reducing waste.
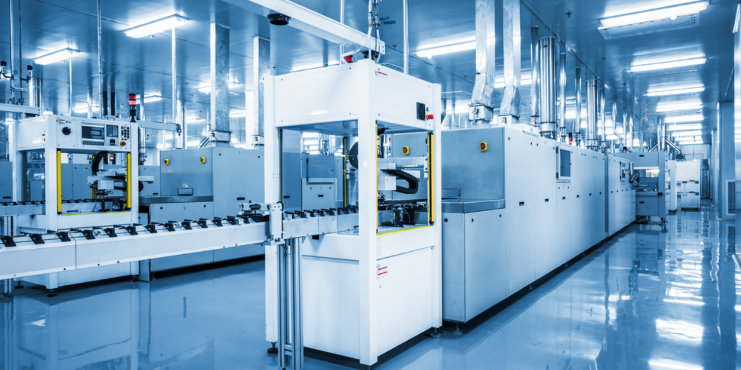
He was a problem solver during the recession. His tool maintenance strategy saved $2 million. He also implemented an early retirement plan for unionized workers. These actions helped transform Wiremold into a Lean-oriented company from an inefficient, haphazard organization.
He introduced a system to track the flow of raw material throughout the manufacturing process. He also implemented an ERP system. He also ensured that his team understood respect for employees. His lean strategy was simple and effective. This allowed him make sure all employees understood the concept. His management style encouraged respect for people and a hands-on approach.
His greatest asset was his understanding of the kaizen process. Danaher Corporation had been his employer for a while, and he was familiar with the three Ps of a good kaizen: process, product, and people. He also took small steps to lay off salaried employees. His kaizen approach helped him ensure his team achieved their goals.
He also introduced value stream mapping. This diagram shows how manufacturing resources affect the overall efficiency and effectiveness of the company. He also introduced Kaizen events worksheets, which can help track key improvement efforts. A chart that shows overall achievements displays the results.
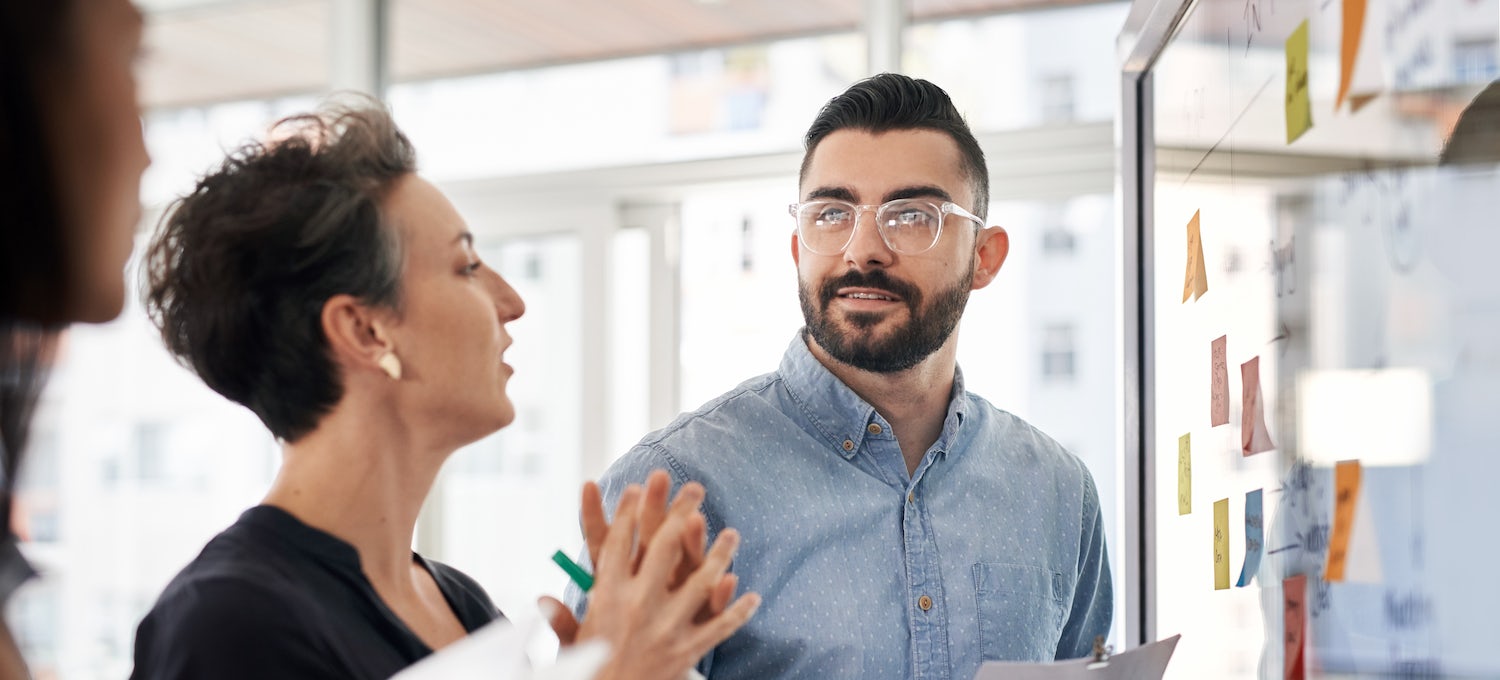
He also devised a process to decrease lead time, which is critical for the manufacturing business. The fine blank machine was capable of producing 600 to 800 blades per hour. It also eliminated the need for a lot of manual work. Another tool was the Kanban card, which can be used to reduce lead times.
Wiremold was a leading manufacturer of conduit casing. After a major overhaul by Art Byrne, the company saw its sales rise from 100 million to over 450 million dollars in ten short years. In 2001, French competitor Legrand bought the company. Wiremold was not always a success. Its biggest problem, however, was queue processing. This caused stations to have too many or too few jobs.
FAQ
How can I find out more about manufacturing?
You can learn the most about manufacturing by getting involved in it. However, if that's not possible, you can always read books or watch educational videos.
Can we automate some parts of manufacturing?
Yes! Yes! Automation has existed since ancient times. The Egyptians invent the wheel thousands of year ago. Today, robots assist in the assembly of lines.
There are many uses of robotics today in manufacturing. These include:
-
Automated assembly line robots
-
Robot welding
-
Robot painting
-
Robotics inspection
-
Robots that make products
Automation could also be used to improve manufacturing. For example, 3D printing allows us to make custom products without having to wait for weeks or months to get them manufactured.
What is the role of a manager in manufacturing?
Manufacturing managers must ensure that manufacturing processes are efficient, effective, and cost-effective. They must also be alert to any potential problems and take appropriate action.
They must also be able to communicate with sales and marketing departments.
They should be up to date on the latest trends and be able apply this knowledge to increase productivity and efficiency.
How can manufacturing efficiency be improved?
The first step is to identify the most important factors affecting production time. Then we need to find ways to improve these factors. If you don’t know how to start, look at which factors have the greatest impact upon production time. Once you've identified them all, find solutions to each one.
What are the logistics products?
Logistics involves the transportation of goods from point A and point B.
These include all aspects related to transport such as packaging, loading and transporting, storing, transporting, unloading and warehousing inventory management, customer service. Distribution, returns, recycling are some of the options.
Logisticians ensure that the product is delivered to the correct place, at the right time, and under safe conditions. They provide information on demand forecasts as well stock levels, production schedules and availability of raw material.
They monitor shipments in transit, ensure quality standards, manage inventories, replenish orders, coordinate with suppliers and other vendors, and offer support services for sales, marketing, and customer service.
Statistics
- According to a Statista study, U.S. businesses spent $1.63 trillion on logistics in 2019, moving goods from origin to end user through various supply chain network segments. (netsuite.com)
- According to the United Nations Industrial Development Organization (UNIDO), China is the top manufacturer worldwide by 2019 output, producing 28.7% of the total global manufacturing output, followed by the United States, Japan, Germany, and India.[52][53] (en.wikipedia.org)
- [54][55] These are the top 50 countries by the total value of manufacturing output in US dollars for its noted year according to World Bank.[56] (en.wikipedia.org)
- Job #1 is delivering the ordered product according to specifications: color, size, brand, and quantity. (netsuite.com)
- In the United States, for example, manufacturing makes up 15% of the economic output. (twi-global.com)
External Links
How To
How to Use Lean Manufacturing in the Production of Goods
Lean manufacturing refers to a method of managing that seeks to improve efficiency and decrease waste. It was developed in Japan during the 1970s and 1980s by Taiichi Ohno, who received the Toyota Production System (TPS) award from TPS founder Kanji Toyoda. The first book published on lean manufacturing was titled "The Machine That Changed the World" written by Michael L. Watkins and published in 1990.
Lean manufacturing can be described as a set or principles that are used to improve quality, speed and cost of products or services. It emphasizes reducing defects and eliminating waste throughout the value chain. Lean manufacturing can be described as just-in–time (JIT), total productive maintenance, zero defect (TPM), or even 5S. Lean manufacturing seeks to eliminate non-value added activities, such as inspection, work, waiting, and rework.
Lean manufacturing can help companies improve their product quality and reduce costs. Additionally, it helps them achieve their goals more quickly and reduces employee turnover. Lean manufacturing is considered one of the most effective ways to manage the entire value chain, including suppliers, customers, distributors, retailers, and employees. Lean manufacturing practices are widespread in many industries. Toyota's philosophy is the foundation of its success in automotives, electronics and appliances, healthcare, chemical engineers, aerospace, paper and food, among other industries.
Lean manufacturing includes five basic principles:
-
Define Value - Determine the value that your business brings to society. Also, identify what sets you apart from your competitors.
-
Reduce Waste – Eliminate all activities that don't add value throughout the supply chain.
-
Create Flow: Ensure that the work process flows without interruptions.
-
Standardize & simplify - Make processes consistent and repeatable.
-
Build Relationships - Establish personal relationships with both internal and external stakeholders.
Lean manufacturing, although not new, has seen renewed interest in the economic sector since 2008. Many companies have adopted lean manufacturing methods to increase their marketability. Many economists believe lean manufacturing will play a major role in economic recovery.
With many benefits, lean manufacturing is becoming more common in the automotive industry. These include higher customer satisfaction, lower inventory levels, lower operating expenses, greater productivity, and improved overall safety.
Any aspect of an enterprise can benefit from Lean manufacturing. This is because it ensures efficiency and effectiveness in all stages of the value chain.
There are three types of lean manufacturing.
-
Just-in-Time Manufacturing (JIT): This type of lean manufacturing is commonly referred to as "pull systems." JIT is a method in which components are assembled right at the moment of use, rather than being manufactured ahead of time. This strategy aims to decrease lead times, increase availability of parts and reduce inventory.
-
Zero Defects Manufacturing (ZDM),: ZDM is a system that ensures no defective units are left the manufacturing facility. If a part needs to be fixed during the assembly line, it should be repaired rather than scrapped. This applies to finished goods that may require minor repairs before shipment.
-
Continuous Improvement (CI): CI aims to improve the efficiency of operations by continuously identifying problems and making changes in order to eliminate or minimize waste. Continuous Improvement involves continuous improvement of processes.