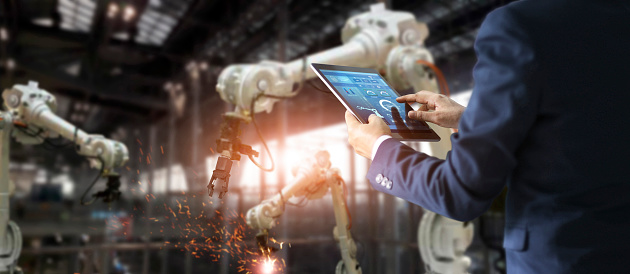
Materials engineers design and develop new materials to enable the technology of tomorrow. They use metals, composites, ceramics, and plastics to create materials which meet specific chemical, mechanical, and electrical requirements.
What is a Materials Engineer?
A material engineer tests, processes and develops raw materials, which are then used to create a range of products including aircraft wings or computer chips. They can also be involved in the development of biomedical devices or golf clubs. They study and evaluate metals, ceramics and plastics as well as nanomaterials and other substances to develop new materials that can meet specific chemical, electrical and mechanical requirements.
The responsibilities of a materials engineer vary according to the specific type of materials that they are working with and the industry in which they are employed. But they are also responsible for creating budgets, assessing production cost, and supervising technicans.
What is the role of a materials scientist engineer?
A materials science engineer can work with metals as well as ceramics and composites. They also improve the durability, strength, and weight of these materials. They can develop new materials and improve existing ones.
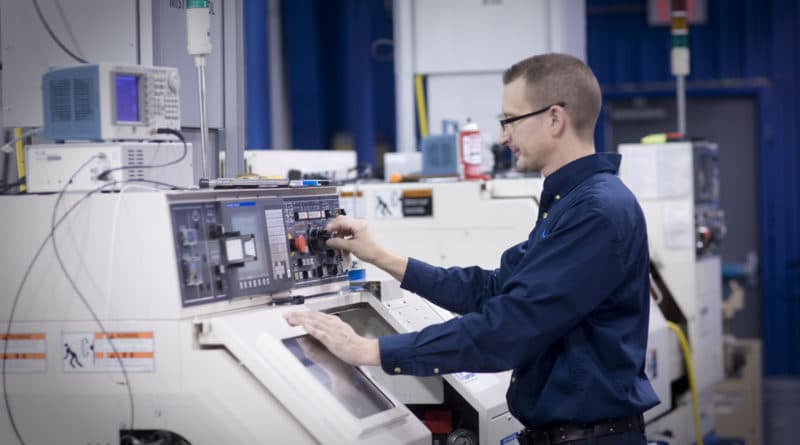
What do materials engineers need?
For a career as a materials engineer you will need to have a bachelor’s degree in an engineering or materials science field. The degree program should emphasize engineering principles in the classroom and lab. This program may take a couple of years to complete.
After graduation, you can look for a job in materials engineering and earn around PS25,000 per year. With experience, the salary you earn will increase.
How to become materials engineer
Qualifications for materials engineers vary depending on the industry and employer. The majority of materials engineers require a degree in materials engineering or material science. This includes chemistry, mathematics, and physics.
As a materials scientist engineer, you'll need to have a bachelor's in a relevant subject such as engineering, chemistry, or physics. A master's or doctoral degree is usually required for higher-level research positions.
How much money can I make as a materials engineer?
The salaries of materials engineers can vary depending on their level of expertise, the industry in which they work and the size of the company. You can also expect bonuses and other benefits for your work.
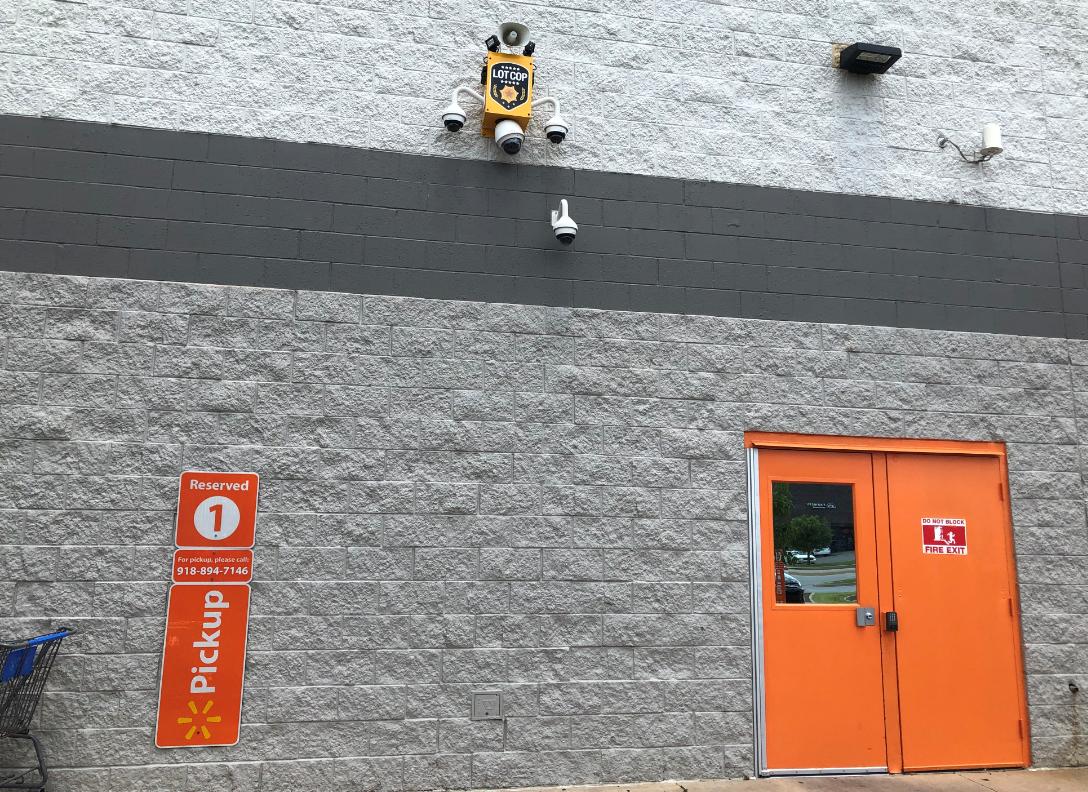
What is the future of the materials engineering career?
It is predicted that the future of materials engineering will be bright, and there are many opportunities available to those who choose to pursue this career. The increasing demand in the fields of medicine, architecture and communications for newer and more advanced materials has led to this.
You can become an engineer in materials by completing a degree program in a discipline such as metallurgy. This will give you the knowledge you need to pursue a career in this industry and may open up more opportunities for you down the line. A degree in a subject such as chemistry will help you with your research and development skills. For more experience, you could work at an engineering company specializing in a particular field of materials.
FAQ
What are the 7 Rs of logistics management?
The acronym 7R's for Logistics stands to represent the seven basic principles in logistics management. It was created by the International Association of Business Logisticians and published in 2004 under its "Seven Principles of Logistics Management".
The acronym consists of the following letters:
-
Responsible - to ensure that all actions are within the legal requirements and are not detrimental to others.
-
Reliable - You can have confidence that you will fulfill your promises.
-
Reasonable - use resources efficiently and don't waste them.
-
Realistic - Take into consideration all aspects of operations including cost-effectiveness, environmental impact, and other factors.
-
Respectful - show respect and treat others fairly and fairly
-
Reliable - Find ways to save money and increase your productivity.
-
Recognizable provides value-added products and services to customers
What is the difference between manufacturing and logistics
Manufacturing refers the process of producing goods from raw materials through machines and processes. Logistics is the management of all aspects of supply chain activities, including procurement, production planning, distribution, warehousing, inventory control, transportation, and customer service. As a broad term, manufacturing and logistics often refer to both the creation and delivery of products.
Is automation necessary in manufacturing?
Automating is not just important for manufacturers, but also for service providers. Automation allows them to deliver services quicker and more efficiently. They can also reduce their costs by reducing human error and improving productivity.
What are the responsibilities of a manufacturing manager
Manufacturing managers must ensure that manufacturing processes are efficient, effective, and cost-effective. They must also be alert to any potential problems and take appropriate action.
They should also be able communicate with other departments, such as sales or marketing.
They must also keep up-to-date with the latest trends in their field and be able use this information to improve productivity and efficiency.
What do you mean by warehouse?
Warehouses and storage facilities are where goods are kept before being sold. It can be indoors or out. It may also be an indoor space or an outdoor area.
What is the responsibility of a production planner?
A production planner ensures all aspects of the project are delivered on time, within budget, and within scope. They ensure that the product or service is of high quality and meets client requirements.
Statistics
- According to a Statista study, U.S. businesses spent $1.63 trillion on logistics in 2019, moving goods from origin to end user through various supply chain network segments. (netsuite.com)
- (2:04) MTO is a production technique wherein products are customized according to customer specifications, and production only starts after an order is received. (oracle.com)
- In 2021, an estimated 12.1 million Americans work in the manufacturing sector.6 (investopedia.com)
- Job #1 is delivering the ordered product according to specifications: color, size, brand, and quantity. (netsuite.com)
- You can multiply the result by 100 to get the total percent of monthly overhead. (investopedia.com)
External Links
How To
How to Use lean manufacturing in the Production of Goods
Lean manufacturing (or lean manufacturing) is a style of management that aims to increase efficiency, reduce waste and improve performance through continuous improvement. It was created in Japan by Taiichi Ohno during the 1970s and 80s. He received the Toyota Production System award (TPS), from Kanji Toyoda, founder of TPS. Michael L. Watkins published the "The Machine That Changed the World", the first book about lean manufacturing. It was published in 1990.
Lean manufacturing is often defined as a set of principles used to improve the quality, speed, and cost of products and services. It emphasizes reducing defects and eliminating waste throughout the value chain. Lean manufacturing is also known as just in time (JIT), zero defect total productive maintenance(TPM), and five-star (S). Lean manufacturing eliminates non-value-added tasks like inspection, rework, waiting.
In addition to improving product quality and reducing costs, lean manufacturing helps companies achieve their goals faster and reduces employee turnover. Lean manufacturing has been deemed one of the best ways to manage the entire value-chain, including customers, distributors as well retailers and employees. Lean manufacturing can be found in many industries. Toyota's philosophy is a great example of this. It has helped to create success in automobiles as well electronics, appliances and healthcare.
Five basic principles of Lean Manufacturing are included in lean manufacturing
-
Define Value: Identify the social value of your business and what sets you apart.
-
Reduce Waste - Eliminate any activity that doesn't add value along the supply chain.
-
Create Flow. Ensure that your work is uninterrupted and flows seamlessly.
-
Standardize & Simplify - Make processes as consistent and repeatable as possible.
-
Build Relationships- Develop personal relationships with both internal as well as external stakeholders.
Lean manufacturing, although not new, has seen renewed interest in the economic sector since 2008. To increase their competitiveness, many businesses have turned to lean manufacturing. Some economists even believe that lean manufacturing can be a key factor in economic recovery.
Lean manufacturing has many benefits in the automotive sector. These include better customer satisfaction and lower inventory levels. They also result in lower operating costs.
It can be applied to any aspect of an organisation. However, it is particularly useful when applied to the production side of an organization because it ensures that all steps in the value chain are efficient and effective.
There are three main types in lean manufacturing
-
Just-in-Time Manufacturing: Also known as "pull systems", this type of lean manufacturing uses just-in-time manufacturing (JIT). JIT refers to a system in which components are assembled at the point of use instead of being produced ahead of time. This approach is designed to reduce lead times and increase the availability of components. It also reduces inventory.
-
Zero Defects Manufacturing (ZDM),: ZDM is a system that ensures no defective units are left the manufacturing facility. If a part is required to be repaired on the assembly line, it should not be scrapped. This applies to finished products, which may need minor repairs before they are shipped.
-
Continuous Improvement (CI): CI aims to improve the efficiency of operations by continuously identifying problems and making changes in order to eliminate or minimize waste. Continuous improvement involves continuous improvement of processes and people as well as tools.