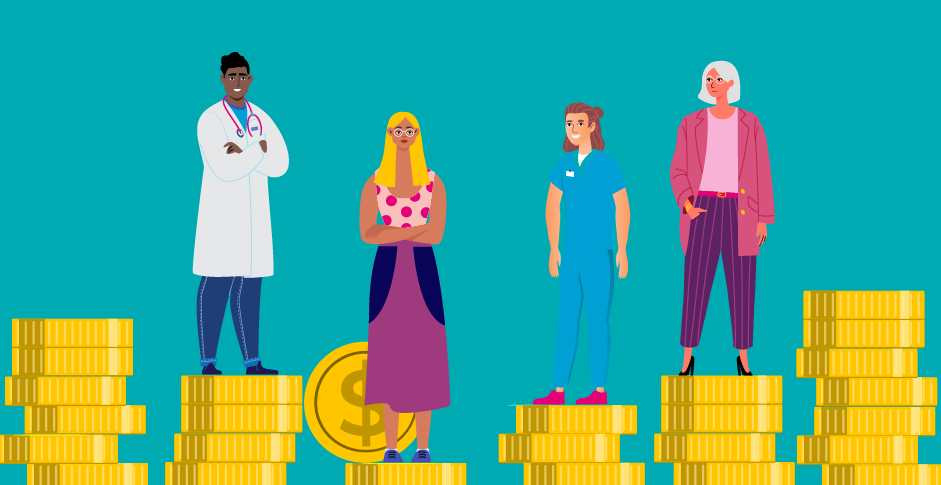
Historically, demand from consumers drove manufacturing. This is changing. The manufacturing industry is also being transformed by technology. This is partly due to the advancements in predictive analytics that allow manufacturers to move production closer towards consumers. Despite these advances, manufacturing faces many risks, including shortages and high demand. Manufacturers that fail to meet customer demand may lose customers. Also, too much production can lead to oversupply in the market. In order to preserve their brand image, manufacturers need to adhere strictly to quality control guidelines.
There are many types of manufacturing processes manufacturers can use, but they all share some common characteristics. Repetitive manufacturing, batch manufacturing and process manufacturing are the most popular. These processes can be used on large scales to allow manufacturers to make products in bulk.
Repetitive Manufacturing is a process where the same or similar items are produced on a dedicated production line all year. Repetitive manufacturing production line require very little setup and changeover. They are ideal for small production runs with minimal capital investment. They can also operate 24 hours a days.
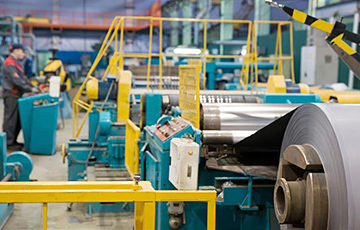
Batch manufacturing works in discrete, small batches and is very similar to repetitive manufacturing. It is generally faster and requires less automation. It is not suitable for every type of production. This is a great option for products that have to be changed frequently. You can also use it to create custom products. It is ideal for making goods from materials that don't easily degrade.
Discrete production is the opposite from process manufacturing. It requires a bill of materials, as well as instructions to produce finished goods. It can include items such as automobiles and toys. This includes the use of computers and software. The main difference is that process manufacturing requires fewer interruptions and higher quality control.
Injection molding is the most widely used process for mass production of plastic parts. In this process, small plastic pellets are melted and then injected into a mold. After cooling, the mold is mechanically ejected. To ensure a uniform coating, the mold must be heated and rotated. This method can be used to create a wide range of products, from pipes and straws to name a few.
A third type of manufacturing process is atomic manufacturing. This process is also known as "bottom-up" manufacturing. This method allows components to interact naturally. It is also possible to produce products from biological materials in this manner. Sometimes, parts can either be added manually or robotically.
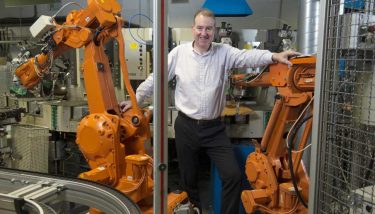
Intermittent Manufacturing is another form. This method produces multiple identical items at once, which is especially beneficial for low-volume production runs. This method is not customizable and may not be suitable for all products.
A process manufacturing includes items that cannot be broken down such as ceramics and glass. Process manufacturing offers the main advantage of producing a wide range of products at high quality. Additionally, process manufacturing is less prone to defects and has fewer interruptions.
FAQ
Why should you automate your warehouse?
Automation has become increasingly important in modern warehousing. Increased demand for efficient and faster delivery has resulted in a rise in e-commerce.
Warehouses must adapt quickly to meet changing customer needs. They must invest heavily in technology to do this. Automation of warehouses offers many benefits. Here are some reasons why it's worth investing in automation:
-
Increases throughput/productivity
-
Reduces errors
-
Increases accuracy
-
Safety is boosted
-
Eliminates bottlenecks
-
Companies can scale more easily
-
Workers are more productive
-
Provides visibility into everything that happens in the warehouse
-
Enhances customer experience
-
Improves employee satisfaction
-
This reduces downtime while increasing uptime
-
You can be sure that high-quality products will arrive on time
-
Human error can be eliminated
-
This helps to ensure compliance with regulations
What is the best way to learn about manufacturing?
The best way to learn about manufacturing is through hands-on experience. You can read books, or watch instructional videos if you don't have the opportunity to do so.
What are the 4 types manufacturing?
Manufacturing is the process of transforming raw materials into useful products using machines and processes. Manufacturing involves many activities, including designing, building, testing and packaging, shipping, selling, service, and so on.
Statistics
- According to the United Nations Industrial Development Organization (UNIDO), China is the top manufacturer worldwide by 2019 output, producing 28.7% of the total global manufacturing output, followed by the United States, Japan, Germany, and India.[52][53] (en.wikipedia.org)
- [54][55] These are the top 50 countries by the total value of manufacturing output in US dollars for its noted year according to World Bank.[56] (en.wikipedia.org)
- In 2021, an estimated 12.1 million Americans work in the manufacturing sector.6 (investopedia.com)
- It's estimated that 10.8% of the U.S. GDP in 2020 was contributed to manufacturing. (investopedia.com)
- (2:04) MTO is a production technique wherein products are customized according to customer specifications, and production only starts after an order is received. (oracle.com)
External Links
How To
How to use 5S to increase Productivity in Manufacturing
5S stands for "Sort", "Set In Order", "Standardize", "Separate" and "Store". The 5S methodology was developed at Toyota Motor Corporation in 1954. It allows companies to improve their work environment, thereby achieving greater efficiency.
This approach aims to standardize production procedures, making them predictable, repeatable, and easily measurable. Cleaning, sorting and packing are all done daily. These actions allow workers to perform their job more efficiently, knowing what to expect.
There are five steps to implementing 5S, including Sort, Set In Order, Standardize, Separate and Store. Each step requires a different action to increase efficiency. By sorting, for example, you make it easy to find the items later. When items are ordered, they are put together. Next, organize your inventory into categories and store them in containers that are easily accessible. Labeling your containers will ensure that everything is correctly labeled.
This process requires employees to think critically about how they do their job. Employees should understand why they do the tasks they do, and then decide if there are better ways to accomplish them. In order to use the 5S system effectively, they must be able to learn new skills.
In addition to increasing efficiency, the 5S method also improves morale and teamwork among employees. They are more motivated to achieve higher efficiency levels as they start to see improvement.