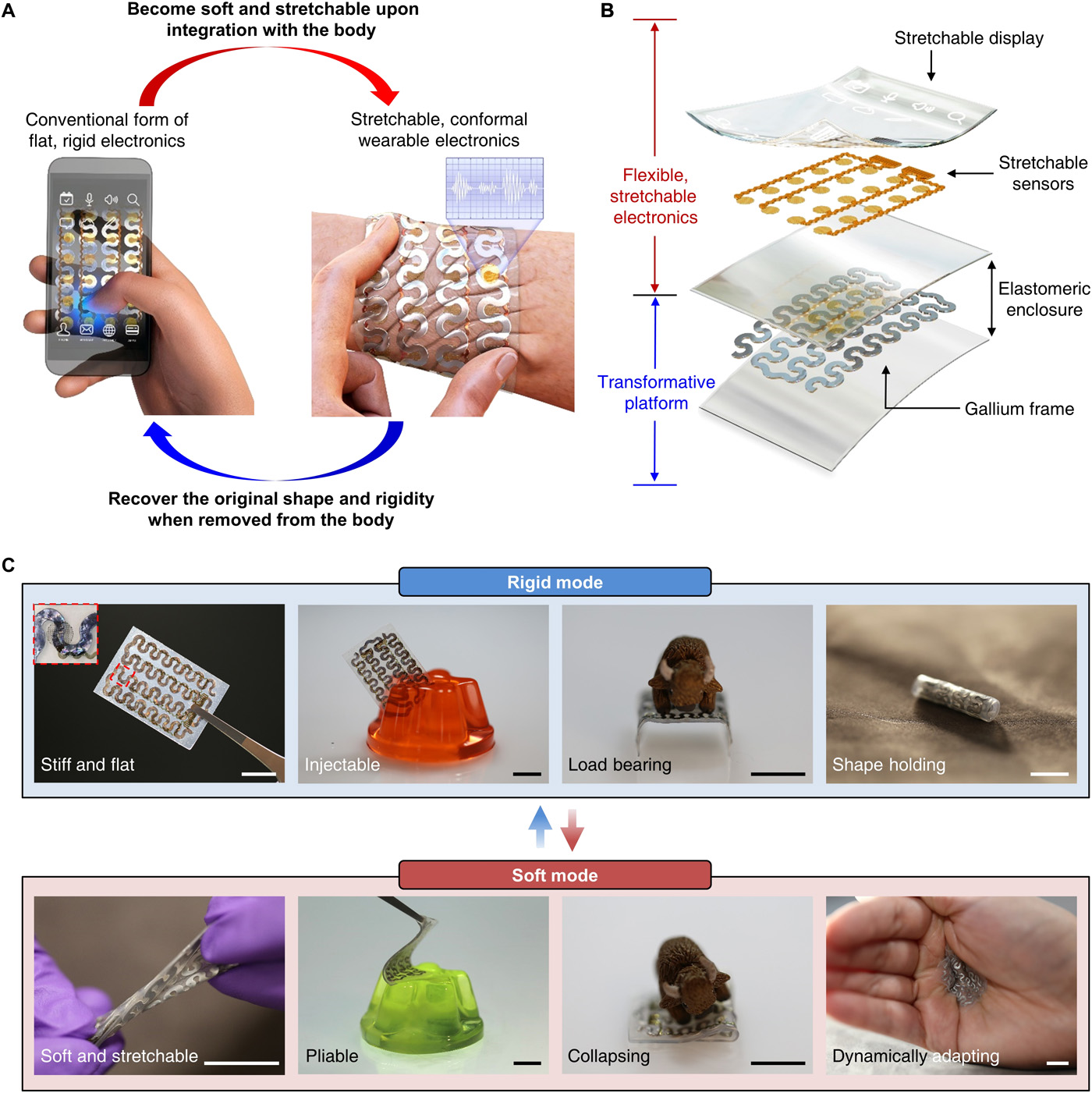
Almost everything that a company does requires an accurate cost estimate. Cost estimators are responsible for this. They are responsible for determining the costs associated with manufacturing and developing new products or services. They are also required to evaluate the cost of building a new structure. This includes the analysis of the labor and material costs.
Most cost estimators are employed by construction companies. They must have a good understanding of construction methods and processes. They also need to be familiar with computer-aided design (CAD) software. This software can improve design and manufacturing efficiency. Also, cost estimators must be able to access data from databases. They can also use Microsoft Excel or other software.
They work closely with other professionals to produce accurate cost estimates. They review the project blueprints and site conditions to determine the cost of each component. Engineers may be involved in determining the dimensions and machining procedures required.
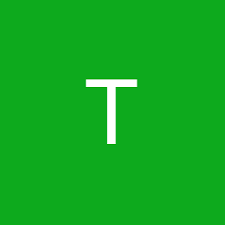
Cost estimators must be detail-oriented, assertive, and dependable. They must be able to analyze information that is difficult to interpret. They must also have the ability to clearly and convincingly present findings. They must be able communicate effectively with clients or professionals.
Cost estimators are usually assigned to the cost or engineering department of a company. They must have a solid background in science and mathematics. They should also be familiar with computer software, including CAD, BIM, and commercial software. You may need to take a certification class. Some certifications include the Certified Cost Estimator/Analyst (CCEA), Professional Cost Estimator/Analyst, and Certified Professional Estimator.
Cost estimators may specialize in particular industries or services. One person may specialize in building costs or construction, while another might be more interested in software development costs. Cost estimators can also find jobs in other areas, including automotive repair and maintenance, building construction, and specialty trade contractors.
These individuals communicate with suppliers, clients, and engineers. They are also proficient in industry terminology. They have extensive knowledge before they can prepare cost estimates. In addition to preparing cost estimates, many individuals in this occupation conduct studies, study the effects of different processes on costs, and find ways to reduce costs.
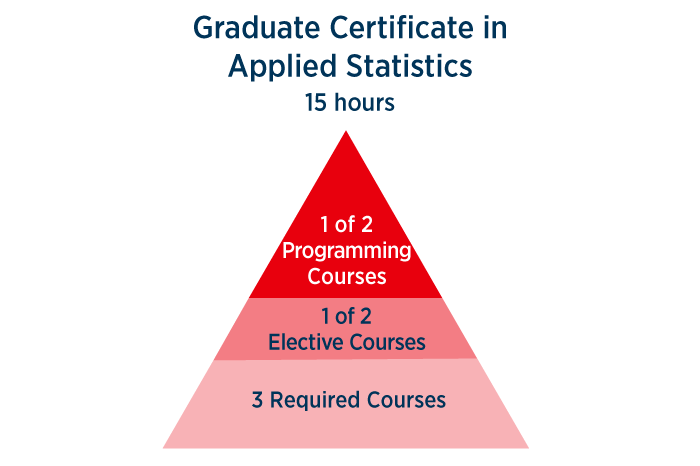
Depending on the industry, job applicants may need to have a bachelor's degree. They may also need to complete an internship. They may also be eligible for cooperative education programs. A degree in building construction, or construction management is also an advantage for construction companies.
Cost estimators can be found in both construction and manufacturing companies. They assist companies in making accurate estimates that will allow them to submit profitable bids. They also analyze data about the supply chain and other factors that impact costs. They can also be cost estimators for government programs. They may also be required to redesign existing products.
Cost estimators must have a strong understanding of computer-aided design (CAD) software. They can also train to use automatic cost estimator software.
FAQ
What is the best way to learn about manufacturing?
Hands-on experience is the best way to learn more about manufacturing. However, if that's not possible, you can always read books or watch educational videos.
How important is automation in manufacturing?
Automating is not just important for manufacturers, but also for service providers. Automation allows them to deliver services quicker and more efficiently. In addition, it helps them reduce costs by reducing human errors and improving productivity.
How does a production planner differ from a project manager?
The difference between a product planner and project manager is that a planer is typically the one who organizes and plans the entire project. A production planner, however, is mostly involved in the planning stages.
What is the role of a logistics manager
Logistics managers are responsible for ensuring that all goods arrive in perfect condition and on time. This is accomplished by using the experience and knowledge gained from working with company products. He/she should make sure that enough stock is on hand to meet the demands.
What are manufacturing and logistics?
Manufacturing refers the process of producing goods from raw materials through machines and processes. Logistics manages all aspects of the supply chain, including procurement, production planning and distribution, inventory control, transportation, customer service, and transport. Manufacturing and logistics are often considered together as a broader term that encompasses both the process of creating products and delivering them to customers.
Statistics
- Many factories witnessed a 30% increase in output due to the shift to electric motors. (en.wikipedia.org)
- You can multiply the result by 100 to get the total percent of monthly overhead. (investopedia.com)
- According to the United Nations Industrial Development Organization (UNIDO), China is the top manufacturer worldwide by 2019 output, producing 28.7% of the total global manufacturing output, followed by the United States, Japan, Germany, and India.[52][53] (en.wikipedia.org)
- In the United States, for example, manufacturing makes up 15% of the economic output. (twi-global.com)
- According to a Statista study, U.S. businesses spent $1.63 trillion on logistics in 2019, moving goods from origin to end user through various supply chain network segments. (netsuite.com)
External Links
How To
How to Use Six Sigma in Manufacturing
Six Sigma can be described as "the use of statistical process control (SPC), techniques to achieve continuous improvement." Motorola's Quality Improvement Department, Tokyo, Japan, developed it in 1986. Six Sigma's main goal is to improve process quality by standardizing processes and eliminating defects. This method has been adopted by many companies in recent years as they believe there are no perfect products or services. Six Sigma aims to reduce variation in the production's mean value. This means that you can take a sample from your product and then compare its performance to the average to find out how often the process differs from the norm. If the deviation is excessive, it's likely that something needs to be fixed.
The first step toward implementing Six Sigma is understanding how variability works in your business. Once you understand this, you can then identify the causes of variation. Also, you will need to identify the sources of variation. Random variations occur when people do mistakes. Symmetrical variations are caused due to factors beyond the process. You could consider random variations if some widgets fall off the assembly lines. But if you notice that every widget you make falls apart at the exact same place each time, this would indicate that there is a problem.
After identifying the problem areas, you will need to devise solutions. This could mean changing your approach or redesigning the entire process. You should then test the changes again after they have been implemented. If they don't work you need to rework them and come up a better plan.