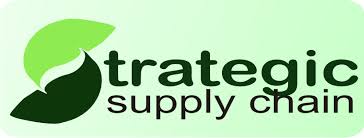
When choosing a course to suit your business, it is important that you get the most value for your money. This course will show you the importance and role of procurement management in a business. These are some factors that you need to consider when making a decision. Learn more about Cost-based pricing, Contracting and Negotiating to help you make the best deal for your business. Here are some things to look at when choosing a course supplier:
Cost-based pricing
Future Procurement is an online Cost-Based Pricing course that's designed for producers and purchasing professionals. It's designed to assist both beginners and more experienced Procurement Professionals in understanding and using Cost-Based pricing in their everyday work. The course is online and available for download. It makes it an easy and convenient way of learning about CBP as well as how it can be applied in different courses. There are a few important factors to consider when implementing CBP in your course procurement strategy.
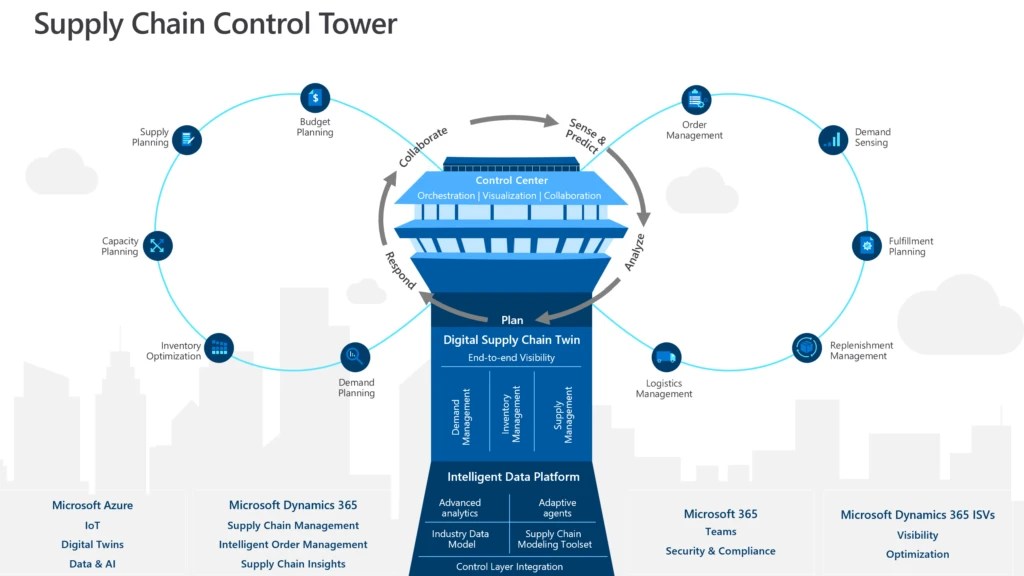
Negotiating
If you're interested in enhancing your skills in negotiation, you can take a negotiation course. There are many courses available in negotiation, both online and in-classroom. This course helps you learn the basics of communicating effectively and establishing mutually beneficial relations. This course will help you find a job in negotiation. This course is more detailed than you might think. Below are some tips for getting the most out this course.
Contracting
Students interested in contracting can benefit from the procurement workshop. It will provide information about the different activities involved during the sourcing phase. This workshop is for anyone involved in the procurement process. Here are the different purposes of the workshop:
Cooperating with external Partners
This course is delivered through a facilitated classroom and consists of six sessions. They each use case studies, workbooks, as well as real-world experiences in course procurement. Participants will engage in role-playing exercises to learn and test their understanding of the course. Participants will gain an awareness of the various sales techniques and behavior. We will be discussing some of the advantages of this workshop and what to expect from it.
Certifications
The Certificate in Course Procurement, (CPP), will allow you to learn about the basics of supply chain management. You will also gain valuable knowledge about current trends and contemporary issues in the field. This course will boost your negotiation and outcome skills, giving you an edge over your competition. The program should be completed in three years with a 2.5 grade point average. This course will also teach you about legal and regulatory considerations that affect the procurement process.
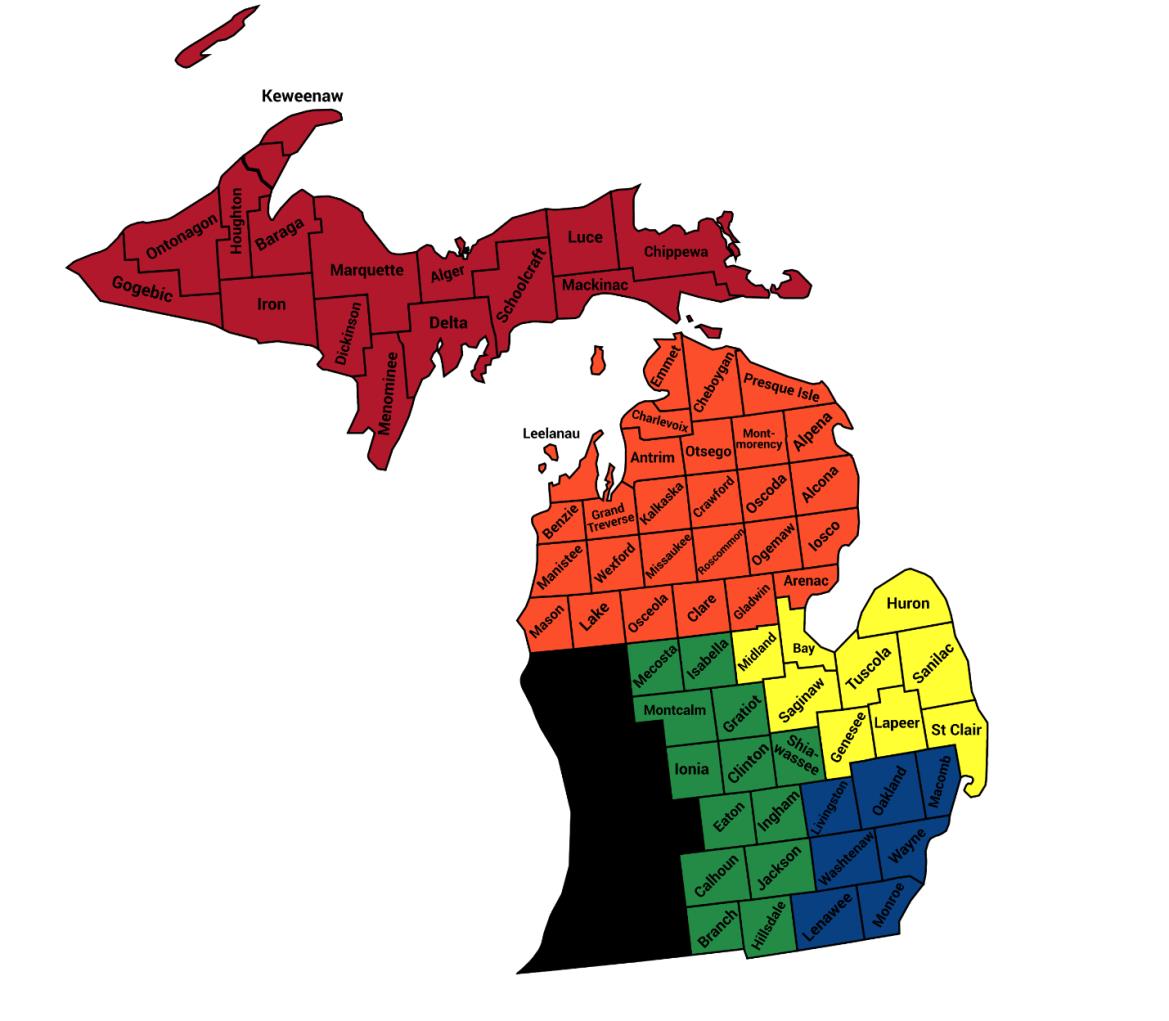
Course platforms
There are many courses platforms to choose from, each with its strengths and limitations. Some premium platforms offer high interaction and social learning. Others offer a simpler interface, with fewer features, and are simpler. Teachable, which was one of the first online course platforms, remains one of the strongest options. You might want to consider other options if you are looking for a course that can easily be promoted to the general public.
FAQ
How can manufacturing efficiency improved?
The first step is to identify the most important factors affecting production time. Then we need to find ways to improve these factors. You can start by identifying the most important factors that impact production time. Once you have identified the factors, then try to find solutions.
What is production management?
Production planning is the process of creating a plan that covers all aspects of production. This includes scheduling, budgeting and crew, location, equipment, props, and more. This document ensures that everything is prepared and available when you are ready for shooting. You should also have information to ensure the best possible results on set. It should include information about shooting locations, casting lists, crew details, equipment requirements, and shooting schedules.
It is important to first outline the type of film you would like to make. You may have already decided where you would like to shoot, or maybe there are specific locations or sets that you want to use. Once you have identified your locations and scenes, you can start working out which elements you require for each scene. For example, you might decide that you need a car but don't know exactly what model you want. This is where you can look up car models online and narrow down your options by choosing from different makes and models.
Once you have found the right vehicle, you can think about adding accessories. What about additional seating? Or perhaps you need someone walking around the back of the car? Maybe you'd like to change the interior from black to a white color. These questions can help you decide the right look for your car. Also, think about what kind of shots you would like to capture. Do you want to film close-ups, or wider angles? Maybe you want the engine or the steering wheels to be shown. These things will help you to identify the car that you are looking for.
Once you have made all the necessary decisions, you can start to create a schedule. You can use a schedule to determine when and where you need it to be shot. The schedule will show you when to get there, what time to leave, and when to return home. Everyone knows exactly what they should do and when. Hire extra staff by booking them ahead of time. It's not worth paying someone to show up if you haven't told him.
When creating your schedule, you will also need to consider the number of days you need to film. Some projects only take one or two days, while others may last weeks. It is important to consider whether you require more than one photo per day when you create your schedule. Multiple shots at the same location can increase costs and make it more difficult to complete. It's better to be safe than sorry and shoot less takes if you're not certain whether you need more takes.
Budgeting is another important aspect of production planning. You will be able to manage your resources if you have a realistic budget. You can always lower the budget if you encounter unexpected problems. It is important to not overestimate how much you will spend. If you underestimate how much something costs, you'll have less money to pay for other items.
Planning production is a tedious process. Once you have a good understanding of how everything works together, planning future projects becomes easy.
What are the requirements to start a logistics business?
To be a successful businessman in logistics, you will need many skills and knowledge. You must have good communication skills to interact effectively with your clients and suppliers. It is important to be able to analyse data and draw conclusions. You must be able to work well under pressure and handle stressful situations. To increase efficiency and creativity, you need to be creative. To motivate and guide your team towards reaching organizational goals, you must have strong leadership skills.
To meet tight deadlines, you must also be efficient and organized.
What are the responsibilities of a logistic manager?
Logistics managers are responsible for ensuring that all goods arrive in perfect condition and on time. This is done by using his/her experience and knowledge of the company's products. He/she should also ensure enough stock is available to meet demand.
What is the responsibility of a production planner?
Production planners ensure all aspects of the project are delivered within time and budget. A production planner ensures that the service and product meet the client's expectations.
What are the four types in manufacturing?
Manufacturing refers the process of turning raw materials into useful products with machines and processes. Manufacturing involves many activities, including designing, building, testing and packaging, shipping, selling, service, and so on.
Statistics
- You can multiply the result by 100 to get the total percent of monthly overhead. (investopedia.com)
- It's estimated that 10.8% of the U.S. GDP in 2020 was contributed to manufacturing. (investopedia.com)
- According to a Statista study, U.S. businesses spent $1.63 trillion on logistics in 2019, moving goods from origin to end user through various supply chain network segments. (netsuite.com)
- In the United States, for example, manufacturing makes up 15% of the economic output. (twi-global.com)
- In 2021, an estimated 12.1 million Americans work in the manufacturing sector.6 (investopedia.com)
External Links
How To
How to Use Lean Manufacturing in the Production of Goods
Lean manufacturing (or lean manufacturing) is a style of management that aims to increase efficiency, reduce waste and improve performance through continuous improvement. It was developed in Japan during the 1970s and 1980s by Taiichi Ohno, who received the Toyota Production System (TPS) award from TPS founder Kanji Toyoda. Michael L. Watkins published the "The Machine That Changed the World", the first book about lean manufacturing. It was published in 1990.
Lean manufacturing refers to a set of principles that improve the quality, speed and costs of products and services. It emphasizes eliminating waste and defects throughout the value stream. Just-in-time (JIT), zero defect (TPM), and 5S are all examples of lean manufacturing. Lean manufacturing is about eliminating activities that do not add value, such as inspection, rework, and waiting.
Lean manufacturing improves product quality and costs. It also helps companies reach their goals quicker and decreases employee turnover. Lean manufacturing is a great way to manage the entire value chain including customers, suppliers, distributors and retailers as well as employees. Many industries worldwide use lean manufacturing. For example, Toyota's philosophy underpins its success in automobiles, electronics, appliances, healthcare, chemical engineering, aerospace, paper, food, etc.
Lean manufacturing includes five basic principles:
-
Define Value: Identify the social value of your business and what sets you apart.
-
Reduce waste - Stop any activity that isn't adding value to the supply chains.
-
Create Flow – Ensure that work flows smoothly throughout the process.
-
Standardize & Simplify - Make processes as consistent and repeatable as possible.
-
Develop Relationships: Establish personal relationships both with internal and external stakeholders.
Although lean manufacturing has always been around, it is gaining popularity in recent years because of a renewed interest for the economy after 2008's global financial crisis. Many businesses have adopted lean manufacturing techniques to help them become more competitive. According to some economists, lean manufacturing could be a significant factor in the economic recovery.
Lean manufacturing has many benefits in the automotive sector. These include improved customer satisfaction, reduced inventory levels, lower operating costs, increased productivity, and better overall safety.
Lean manufacturing can be applied to almost every aspect of an organization. This is because it ensures efficiency and effectiveness in all stages of the value chain.
There are three main types:
-
Just-in-Time Manufacturing (JIT): This type of lean manufacturing is commonly referred to as "pull systems." JIT means that components are assembled at the time of use and not manufactured in advance. This approach reduces lead time, increases availability and reduces inventory.
-
Zero Defects Manufacturing, (ZDM): ZDM is focused on ensuring that no defective products leave the manufacturing facility. It is better to repair a part than have it removed from the production line if it needs to be fixed. This is also true for finished products that require minor repairs before shipping.
-
Continuous Improvement (CI: Continuous improvement aims to increase the efficiency of operations by constantly identifying and making improvements to reduce or eliminate waste. It involves continuous improvement of processes, people, and tools.