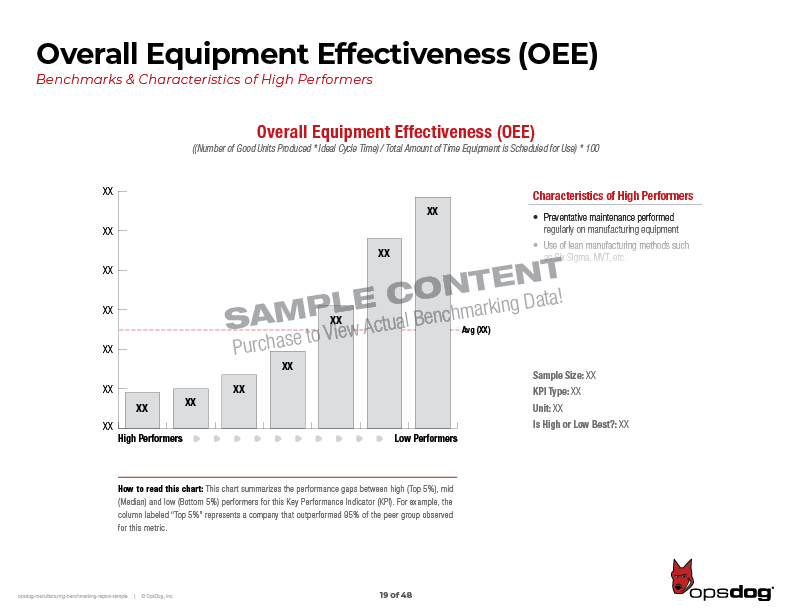
Are you searching for a job as an industrial engineer? Learn more to find out which types of jobs you can apply for. In this article, we'll discuss the types of jobs, the average salary, and the required education. We'll also cover the required skills and where to search for them. Then, you can apply for the position that is most exciting to your heart! Good luck! Before you apply for an industrial engineering job in the future, be sure to read through the job description.
Job description
Industrial engineers aren't for everyone. An industrial engineer is responsible for applying engineering principles to improve the production process and layouts of companies. This engineer is responsible to develop tools and analytics that allow companies to monitor their costs and schedules. He or she also reviews production data to determine areas for improvement and compiles equipment and material lists, as well as cost analyses, production cost estimations, and purchase orders before implementing new projects.
A job as an industrial engineer requires a degree in mechanical engineering. This field requires a solid understanding of engineering principles as well as the ability to solve problems. Industrial engineers often need to be able to combine their technical knowledge with a deeper understanding of people's capabilities and needs. Industrial engineers must have excellent organizational skills, strong analytical skills, and good communicators. They manage factories and warehouses, and improve production processes.
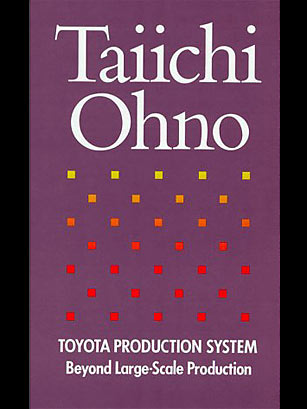
Salary range
The range of salaries for industrial engineers depends on experience. Although starting salaries are approximately $85,000, maximum compensation can reach $100,000. Below is a table that outlines the range of salaries for industrial engineers based on experience. Ventura, California is home to an Entry Level Engineer who can make approximately $86,000 per annum. An experienced Industrial Engineer can expect to earn between $85,000- $100,000 annually. An optional four-year degree is required for Project Engineers.
The average income for an industrial engineer varies according to where you live, your industry, and your years of experience. The average salary for an industrial engineer in New York is $60,700 to $140,000 each year. While it's difficult to identify the upward trend of salaries, the national averages have increased over 40% in the last 10 years. This trend is expected to continue. Monster's Salary tool can help you find out more about the salary ranges in your region.
Education required
Industrial engineers do not normally need licensing, although it may be a prerequisite for government contracts. For entry-level positions, industrial engineers don't require licensing. To be eligible for professional licensure, they must have relevant work experience and a degree obtained from an accredited institution. Most industrial engineers work in offices, factories, or labs. Many industrial engineering professionals find work in aerospace product manufacturing, architectural, engineering services, navigational devices manufacturing, and medical and control instrument production.
Many industrial engineers choose to complete internships during their college careers, which can help them gain valuable experience. Even though entry-level industrial engineering jobs don't typically require professional experience but you can gain additional engineering experience to give your company an edge. If you are interested in working for government agencies or another organization, internships could be a great option. Industrial engineers might also need security clearance in addition to their internships.

Places
You can find many jobs in industrial engineering that are highly rewarding. This field requires entry-level workers to complete calculations, test and monitor devices, and report on their findings. They may also assist in the creation of budgets and tracking metrics. A lot of standing is required for industrial engineers. Industrial engineers must be able to effectively communicate. Sometimes, they work under the guidance of more senior engineers.
Industrial engineers are employed by companies to develop efficient production processes that consume the minimum amount of energy and other resources. Their goal is to improve the efficiency of production and maximize labor efficiency. Industrial engineers work in offices, factories, and other settings to implement improvements in the operations of organizations. Entry-level positions in industrial engineering require a bachelor's degree in industrial engineering or a related field. According to Bureau of Labor Statistics, in 2021 the median industrial engineer salary will be $95,300.
FAQ
What is production management?
Production Planning is the creation of a plan to cover all aspects, such as scheduling, budgeting. Location, crew, equipment, props and other details. This document aims to ensure that everything is planned and ready when you are ready to shoot. This document should also include information on how to get the best result on set. This includes location information, crew details, equipment specifications, and casting lists.
The first step is to decide what you want. You may have already decided where you would like to shoot, or maybe there are specific locations or sets that you want to use. Once you have identified your locations and scenes, you can start working out which elements you require for each scene. One example is if you are unsure of the exact model you want but decide that you require a car. This is where you can look up car models online and narrow down your options by choosing from different makes and models.
After you have chosen the right car, you will be able to begin thinking about accessories. What about additional seating? Or perhaps you need someone walking around the back of the car? Perhaps you would like to change the interior colour from black to white. These questions will help determine the look and feel you want for your car. Also, think about what kind of shots you would like to capture. Are you going to be shooting close-ups? Or wide angles? Maybe the engine or steering wheel is what you are looking to film. These details will help identify the exact car you wish to film.
Once you have all the information, you are ready to create a plan. A schedule will tell you when you need to start shooting and when you need to finish. A schedule for each day will detail when you should arrive at the location and when you need leave. Everyone will know what they need and when. You can also make sure to book extra staff in advance if you have to hire them. It's not worth paying someone to show up if you haven't told him.
Also, consider how many days you will be filming your schedule. Some projects take only a few days while others can last several weeks. When creating your schedule, be aware of whether you need more shots per day. Shooting multiple takes over the same location will increase costs and take longer to complete. It's better to be safe than sorry and shoot less takes if you're not certain whether you need more takes.
Budget setting is an important part of production planning. As it will allow you and your team to work within your financial means, setting a realistic budget is crucial. It is possible to reduce the budget at any time if you experience unexpected problems. However, you shouldn't overestimate the amount of money you will spend. If you underestimate the cost of something, you will have less money left after paying for other items.
Production planning is a very detailed process, but once you understand how everything works together, it becomes easier to plan future projects.
What do you mean by warehouse?
A warehouse, or storage facility, is where goods are stored prior to being sold. It can be either an indoor or outdoor space. In some cases, it may be a combination of both.
How is a production manager different from a producer planner?
The primary difference between a producer planner and a manager of a project is that the manager usually plans and organizes the whole project, while a production planner is only involved in the planning stage.
Can certain manufacturing steps be automated?
Yes! Automation has been around since ancient times. The Egyptians created the wheel thousands years ago. To help us build assembly lines, we now have robots.
There are many applications for robotics in manufacturing today. These include:
-
Automated assembly line robots
-
Robot welding
-
Robot painting
-
Robotics inspection
-
Robots that create products
Manufacturing can also be automated in many other ways. 3D printing makes it possible to produce custom products in a matter of days or weeks.
Why is logistics important in manufacturing
Logistics are an essential part of any business. They help you achieve great results by helping you manage all aspects of product flow, from raw materials to finished goods.
Logistics play a key role in reducing expenses and increasing efficiency.
What are the 7 Rs of logistics?
The acronym 7R's for Logistics stands to represent the seven basic principles in logistics management. It was developed and published by the International Association of Business Logisticians in 2004 as part of the "Seven Principles of Logistics Management".
The acronym consists of the following letters:
-
Responsible - ensure that all actions taken are within legal requirements and are not harmful to others.
-
Reliable: Have faith in your ability or the ability to honor any promises made.
-
Reasonable - make sure you use your resources well and don't waste them.
-
Realistic – consider all aspects of operations, from cost-effectiveness to environmental impact.
-
Respectful - show respect and treat others fairly and fairly
-
Reliable - Find ways to save money and increase your productivity.
-
Recognizable - Provide value-added services to customers
How can manufacturing efficiency be improved?
First, identify the factors that affect production time. The next step is to identify the most important factors that affect production time. If you don’t know where to begin, consider which factors have the largest impact on production times. Once you've identified them all, find solutions to each one.
Statistics
- According to the United Nations Industrial Development Organization (UNIDO), China is the top manufacturer worldwide by 2019 output, producing 28.7% of the total global manufacturing output, followed by the United States, Japan, Germany, and India.[52][53] (en.wikipedia.org)
- In 2021, an estimated 12.1 million Americans work in the manufacturing sector.6 (investopedia.com)
- It's estimated that 10.8% of the U.S. GDP in 2020 was contributed to manufacturing. (investopedia.com)
- You can multiply the result by 100 to get the total percent of monthly overhead. (investopedia.com)
- (2:04) MTO is a production technique wherein products are customized according to customer specifications, and production only starts after an order is received. (oracle.com)
External Links
How To
Six Sigma: How to Use it in Manufacturing
Six Sigma is defined by "the application SPC (statistical process control) techniques to achieve continuous improvements." It was developed by Motorola's Quality Improvement Department at their plant in Tokyo, Japan, in 1986. Six Sigma's core idea is to improve the quality of processes by standardizing and eliminating defects. Many companies have adopted Six Sigma in recent years because they believe that there are no perfect products and services. Six Sigma's main objective is to reduce variations from the production average. If you take a sample and compare it with the average, you will be able to determine how much of the production process is different from the norm. If this deviation is too big, you know something needs fixing.
The first step toward implementing Six Sigma is understanding how variability works in your business. Once you have a good understanding of the basics, you can identify potential sources of variation. These variations can also be classified as random or systematic. Random variations are caused by human errors. Systematic variations can be caused by outside factors. These are, for instance, random variations that occur when widgets are made and some fall off the production line. However, if you notice that every time you assemble a widget, it always falls apart at exactly the same place, then that would be a systematic problem.
Once you've identified where the problems lie, you'll want to design solutions to eliminate those problems. That solution might involve changing the way you do things or redesigning the process altogether. Once you have implemented the changes, it is important to test them again to ensure they work. If they fail, you can go back to the drawing board to come up with a different plan.