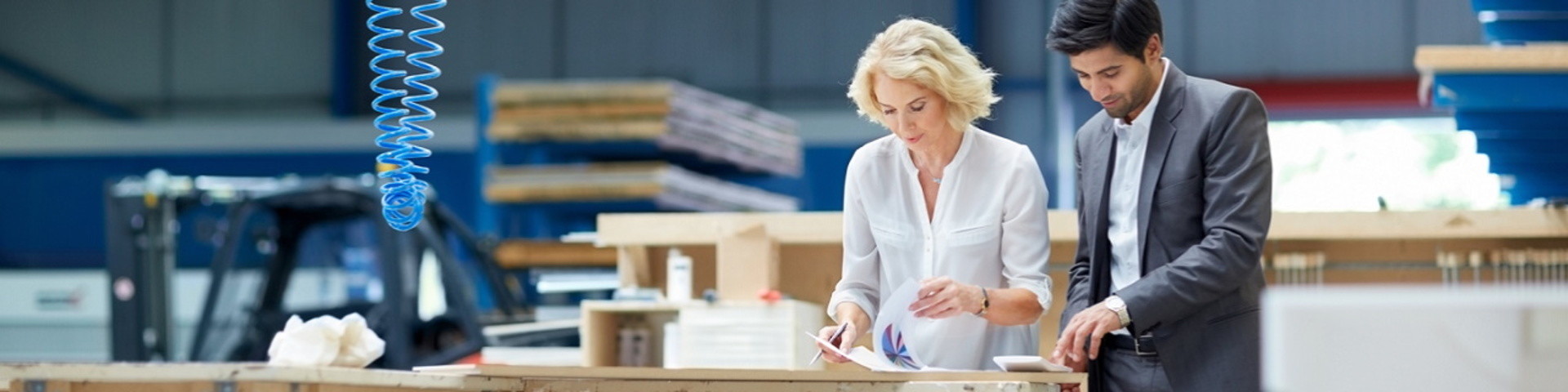
You may be interested in Estimator jobs. But, are you wondering how to get the job? This article will talk about the typical role, the work environment and the salary range. You will also find the necessary skills and experience to perform this role. Continue reading to find out more. Here are some essential qualities that a candidate for the job of Estimator should possess. Having all of these traits will make your job as an Estimator all the more attractive.
Ideal candidate for estimator role
The ideal candidate to fill the Estimator role is well-versed in mathematics and exceptional analytical skills. He or she should also possess excellent communication skills and be detail-oriented. Candidates should hold a minimum of a Bachelor's Degree and at least three years' experience in the relevant field. Candidates must be proficient in MS Office suite. They should possess excellent analytical skills and be able handle pressure.
A bachelor's degree in Construction or another related field is required to be an ideal candidate for the Estimator position. Additionally, they should be driven and enthusiastic. They must be able and willing to communicate with clients and demonstrate self-confidence. They should be able and confident to present their estimates, as well as make a positive first impression. It's crucial that the candidate is able to deliver on their promises, and they are accountable for meeting deadlines.
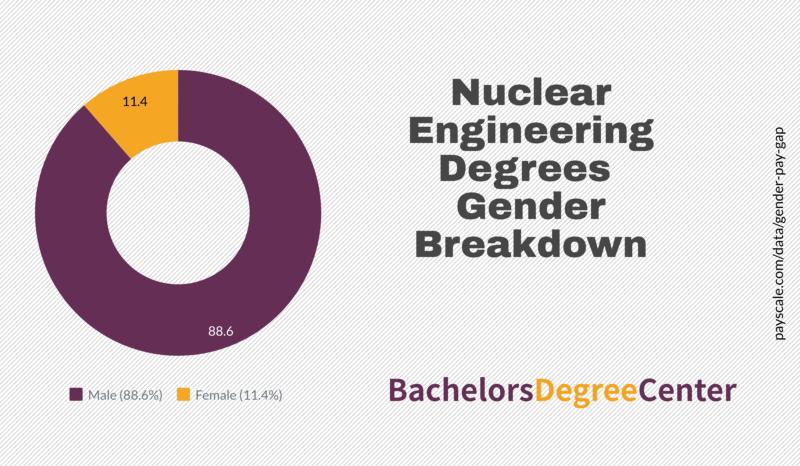
Job description
An estimator's primary task is to produce detailed reports that will help improve the company's profitability. A project estimator is responsible for using computer software and communicating effectively with employees to estimate the cost and duration of a project. They also prepare reports and present them to clients. These reports include budget risks and recommendations. Estimators can make educated guesses about project costs. Nevertheless, these workers can be extremely valuable to their employers and contribute greatly to a company's bottom line.
This job description should be customized to the specific area of interest for the applicant. Although a job description for a building estimator may require some knowledge in quantity surveying, this knowledge is not essential for all construction projects. Estimators also have to be knowledgeable in other fields, including energy, environmental, and technology. There is a job description that suits the needs of every construction company, whether they are looking for a contractor or full-time employee.
Salary
An Estimator is someone who works within the construction industry to determine project costs. Estimators have a wide variety of responsibilities and may specialize in a particular area. First, find out what experience you need to raise your estimater's salary. It is important to find a company offering an apprenticeship program. It may be worth looking for a position if you have an associates degree in estimating. Then you can move up in your career to a permanent position.
An estimator must not only provide valuable information but also have a deep understanding of building materials and techniques. This knowledge allows them to produce accurate and useful forecasts. They often work under high pressure. However, they are highly collaborative and must be able to provide accurate information and work with others. Salary information for estimators is based upon Indeed Salaries data. These figures can be affected by the location, employer, and education of candidates.
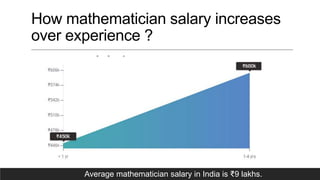
Environment for work
Primarily, you will be an estimator and prepare competitive bids for construction project. Your primary responsibility will be to prepare competitive bids for construction projects. As a bidding coordinator, you will help to set priorities and coordinate pre-bid meetings. You will also identify the labor, equipment, materials, and other requirements for each project. You will also work with project managers to prepare change orders for various projects.
While a bachelor's degree is required for most estimator jobs, some employers will hire those with only a high school diploma. Employers will consider candidates who have an associate's or five-year college diploma, but some will not hire people with just an associate's. The most sought-after degrees are mathematics, business and management. For construction estimators, you will need strong numeracy skills.
FAQ
How can excess manufacturing production be reduced?
Better inventory management is key to reducing excess production. This would decrease the time that is spent on inefficient activities like purchasing, storing, or maintaining excess stock. This would allow us to use our resources for more productive tasks.
A Kanban system is one way to achieve this. A Kanban board is a visual display used to track work in progress. A Kanban system allows work items to move through several states before reaching their final destination. Each state has a different priority level.
If work is moving from one stage to the other, then the current task can be completed and moved on to the next. However, if a task is still at the beginning stages, it will remain so until it reaches the end of the process.
This keeps work moving and ensures no work is lost. Managers can view the Kanban board to see how much work they have done. This data allows them adjust their workflow based upon real-time data.
Another way to control inventory levels is to implement lean manufacturing. Lean manufacturing emphasizes eliminating waste in all phases of production. Anything that does nothing to add value to a product is waste. Here are some examples of common types.
-
Overproduction
-
Inventory
-
Unnecessary packaging
-
Excess materials
Manufacturers can increase efficiency and decrease costs by implementing these ideas.
What are the products and services of logistics?
Logistics are the activities involved in moving goods from point A to point B.
They encompass all aspects transport, including packaging and loading, transporting, storage, unloading.
Logisticians ensure the product reaches its destination in the most efficient manner. They assist companies with their supply chain efficiency through information on demand forecasts. Stock levels, production times, and availability.
They keep track and monitor the transit of shipments, maintain quality standards, order replenishment and inventories, coordinate with suppliers, vendors, and provide support for sales and marketing.
How does a production planner differ from a project manager?
A production planner is more involved in the planning phase of the project than a project manger.
What jobs are available in logistics?
There are many jobs available in logistics. Some of them are:
-
Warehouse workers – They load, unload and transport pallets and trucks.
-
Transportation drivers - They drive trucks and trailers to deliver goods and carry out pick-ups.
-
Freight handlers - They sort and pack freight in warehouses.
-
Inventory managers – These people oversee inventory at warehouses.
-
Sales representatives: They sell products to customers.
-
Logistics coordinators – They plan and coordinate logistics operations.
-
Purchasing agents: They are responsible for purchasing goods and services to support company operations.
-
Customer service representatives - They answer calls and emails from customers.
-
Shipping clerks – They process shipping orders, and issue bills.
-
Order fillers: They fill orders based off what has been ordered and shipped.
-
Quality control inspectors: They inspect outgoing and incoming products for any defects.
-
Others - There are many other types of jobs available in logistics, such as transportation supervisors, cargo specialists, etc.
What does warehouse refer to?
A warehouse, or storage facility, is where goods are stored prior to being sold. It can be either an indoor or outdoor space. In some cases, it may be a combination of both.
Are there ways to automate parts of manufacturing?
Yes! Yes. The Egyptians invented the wheel thousands of years ago. To help us build assembly lines, we now have robots.
In fact, there are several applications of robotics in manufacturing today. These include:
-
Assembly line robots
-
Robot welding
-
Robot painting
-
Robotics inspection
-
Robots that make products
Automation could also be used to improve manufacturing. 3D printing is a way to make custom products quickly and without waiting weeks or months for them to be manufactured.
Why should you automate your warehouse?
Modern warehousing has seen automation take center stage. The rise of e-commerce has led to increased demand for faster delivery times and more efficient processes.
Warehouses must adapt quickly to meet changing customer needs. They must invest heavily in technology to do this. Automating warehouses has many benefits. These are just a few reasons to invest in automation.
-
Increases throughput/productivity
-
Reduces errors
-
Increases accuracy
-
Boosts safety
-
Eliminates bottlenecks
-
Allows companies to scale more easily
-
It makes workers more efficient
-
Gives you visibility into all that is happening in your warehouse
-
Enhances customer experience
-
Improves employee satisfaction
-
Reduces downtime and improves uptime
-
High quality products delivered on-time
-
Removes human error
-
It ensures compliance with regulations
Statistics
- Job #1 is delivering the ordered product according to specifications: color, size, brand, and quantity. (netsuite.com)
- According to the United Nations Industrial Development Organization (UNIDO), China is the top manufacturer worldwide by 2019 output, producing 28.7% of the total global manufacturing output, followed by the United States, Japan, Germany, and India.[52][53] (en.wikipedia.org)
- You can multiply the result by 100 to get the total percent of monthly overhead. (investopedia.com)
- It's estimated that 10.8% of the U.S. GDP in 2020 was contributed to manufacturing. (investopedia.com)
- According to a Statista study, U.S. businesses spent $1.63 trillion on logistics in 2019, moving goods from origin to end user through various supply chain network segments. (netsuite.com)
External Links
How To
How to Use the Just-In-Time Method in Production
Just-intime (JIT), a method used to lower costs and improve efficiency in business processes, is called just-in-time. It's a way to ensure that you get the right resources at just the right time. This means that only what you use is charged to your account. Frederick Taylor developed the concept while working as foreman in early 1900s. Taylor observed that overtime was paid to workers if they were late in working. He then concluded that if he could ensure that workers had enough time to do their job before starting to work, this would improve productivity.
JIT teaches you to plan ahead and prepare everything so you don’t waste time. You should also look at the entire project from start to finish and make sure that you have sufficient resources available to deal with any problems that arise during the course of your project. If you anticipate that there might be problems, you'll have enough people and equipment to fix them. This way, you won't end up paying extra money for things that weren't really necessary.
There are many types of JIT methods.
-
Demand-driven: This JIT is where you place regular orders for the parts/materials that are needed for your project. This will let you track the amount of material left over after you've used it. You'll also be able to estimate how long it will take to produce more.
-
Inventory-based: You stock materials in advance to make your projects easier. This allows one to predict how much they will sell.
-
Project-driven: This is an approach where you set aside enough funds to cover the cost of your project. You will be able to purchase the right amount of materials if you know what you need.
-
Resource-based JIT is the most widespread form. You assign certain resources based off demand. You might assign more people to help with orders if there are many. If you don’t have many orders you will assign less people to the work.
-
Cost-based : This is similar in concept to resource-based. But here, you aren't concerned about how many people your company has but how much each individual costs.
-
Price-based: This is very similar to cost-based, except that instead of looking at how much each individual worker costs, you look at the overall price of the company.
-
Material-based: This approach is similar to cost-based. However, instead of looking at the total cost for the company, you look at how much you spend on average on raw materials.
-
Time-based JIT is another form of resource-based JIT. Instead of focusing only on how much each employee is costing, you should focus on how long it takes to complete your project.
-
Quality-based JIT: Another variation on resource-based JIT. Instead of looking at the labor costs and time it takes to make a product, think about its quality.
-
Value-based: This is one of the newest forms of JIT. In this case, you're not concerned with how well the products perform or whether they meet customer expectations. Instead, you're focused on how much value you add to the market.
-
Stock-based: This inventory-based approach focuses on how many items are being produced at any one time. This is used to increase production and minimize inventory.
-
Just-in time (JIT), planning: This is a combination JIT/supply chain management. It is the process that schedules the delivery of components within a short time of their order. This is important as it reduces lead time and increases throughput.