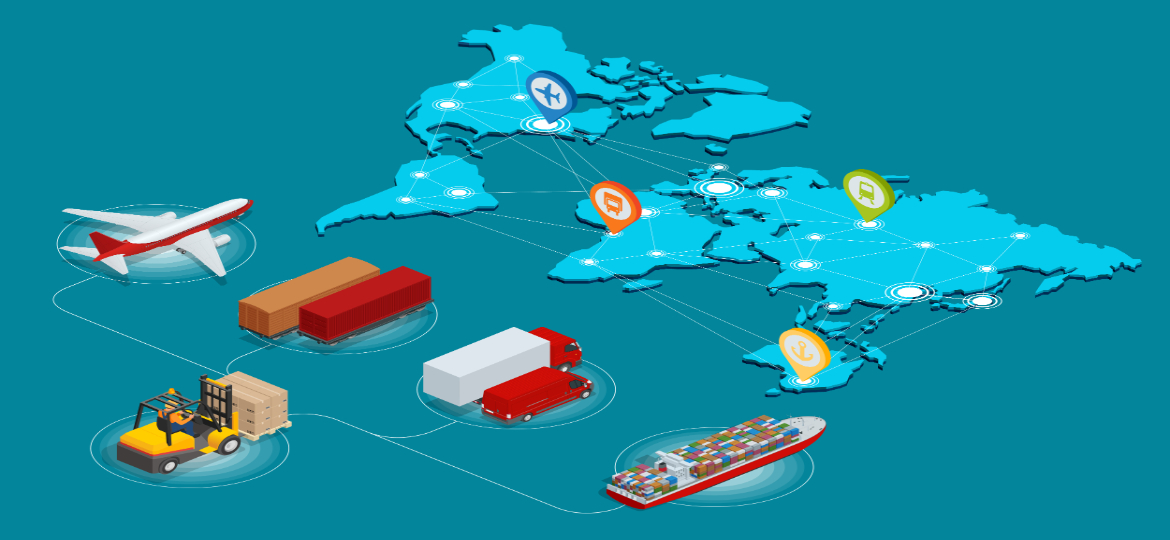
Watts did not know that when he graduated high school he would end up majoring in supply chain at Towson University. Jack Jensen's, managing director of Moore School's program in supply chain management, convinced Watts that the program was for him by promising him an opportunity to work with the school's capstone consultancy project.
The capstone project is one of the more prestigious undergraduate courses. It allows students to dive into supply chain challenges on real projects for companies or nonprofits. Jensen says that the Moore School, in partnership with 150 companies over the past eight years, has identified cost savings of more than $175,000,000 through undergraduate student projects.
During their course work, students collaborate closely with faculty advisors to analyze supply chain problems using data science tools such as Lean Manufacturing and Six Sigma. Students also learn how to organize and transform data and build models.
Students complete a capstone course project after completing their studies. They present the problem and its significance for theory and business, the background of the project, the research, the method and the results.
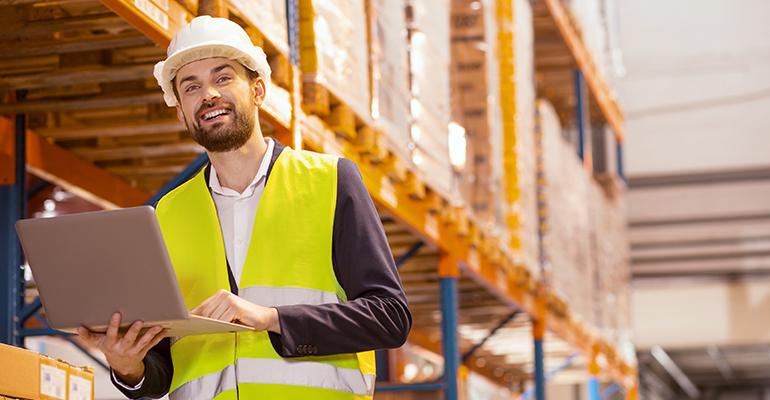
The capstone project provides a unique opportunity to put into practice the knowledge and skills you have gained throughout your degree. It is also a way to show your dedication to your education.
As a result, many schools offer their students the opportunity to complete a capstone project as part of their graduation requirements. These projects can be challenging and require a great deal of time and energy to complete.
The project is usually completed in a single semester. In general, it should take between 100-120 hours to complete.
Towson Place Apartment is a student housing community located just a short walk from campus that offers studios, one- and two-bedroom apartments. Capstone Management provides professional management and residents can enjoy a range of amenities.
Millennium Hall consists of three separate buildings, each with 400 beds. The design was created in partnership between Towson and the University. Students at both the undergraduate level and graduate school are housed in this building. The complex is comprised of studios and units with one, two, or three bedrooms, as well as a central post office and laundry.
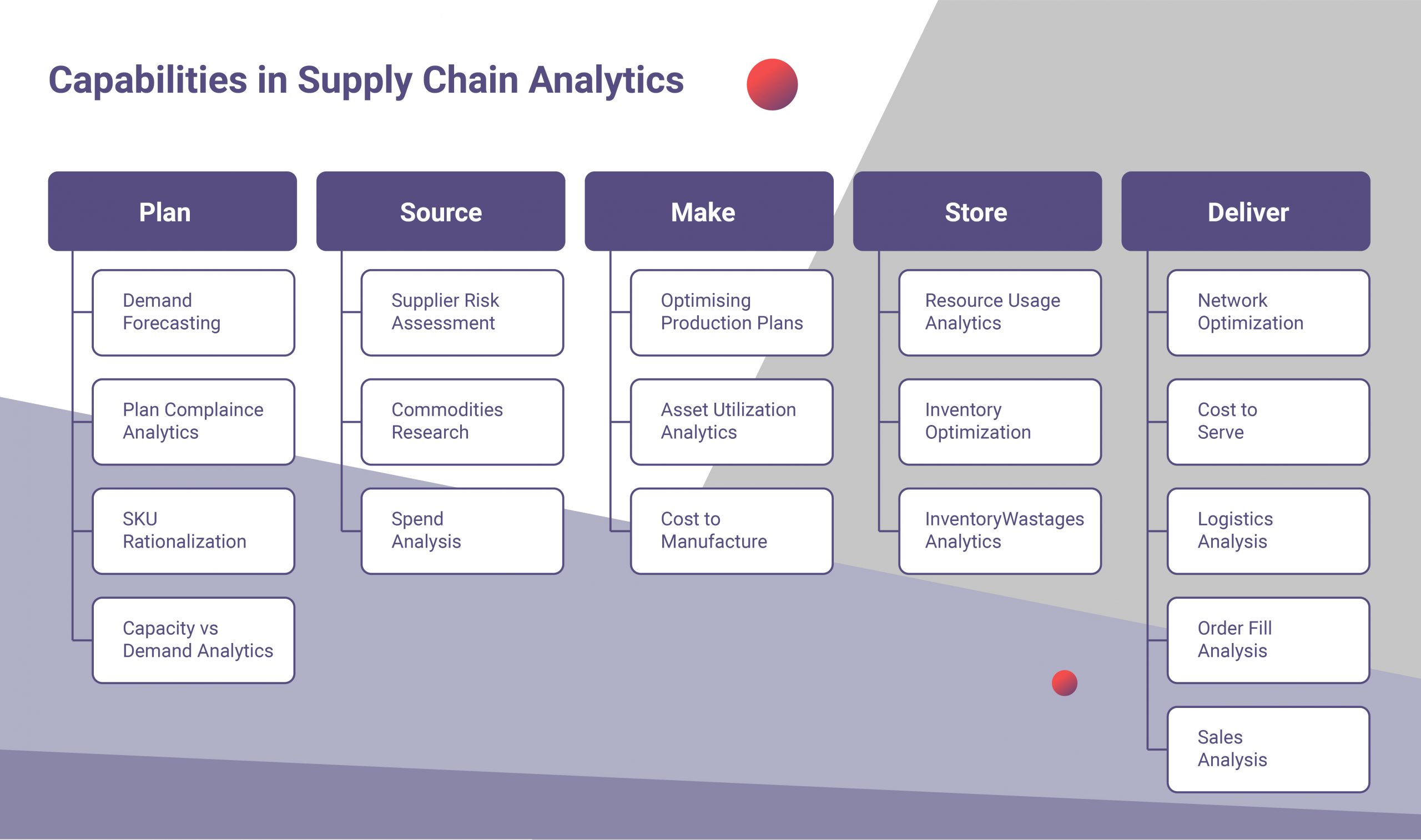
MEDCO leases Millennium Hall from TU. It owns the Paca, Tubman, and Tubman residences. Capstone Properties Inc. is hired by MEDCO to run the day-today operations.
Several families have sued MEDCO, claiming breach of contract. They claim that their lease agreements are holding them hostage as TU moves to distance learning. They claim that MEDCO will not refund lease payments or release contracts from their contracts despite following the guidelines of TU's Housing and Residence Life and University of Maryland Campus Living Services.
The lawsuit was filed on March 18, 2018, but it hasn't been resolved yet. Lucchi received responses from MEDCO’s Legal Council and he will continue to pursue this case.
FAQ
Is automation necessary in manufacturing?
Automation is important not only for manufacturers but also for service providers. They can provide services more quickly and efficiently thanks to automation. It reduces human errors and improves productivity, which in turn helps them lower their costs.
How can manufacturing efficiency be improved?
The first step is to identify the most important factors affecting production time. We must then find ways that we can improve these factors. If you don’t know how to start, look at which factors have the greatest impact upon production time. Once you've identified them all, find solutions to each one.
What does manufacturing industry mean?
Manufacturing Industries is a group of businesses that produce goods for sale. The people who buy these products are called consumers. This is accomplished by using a variety of processes, including production, distribution and retailing. These companies produce goods using raw materials and other equipment. This covers all types of manufactured goods including clothing, food, building supplies and furniture, as well as electronics, tools, machinery, vehicles and pharmaceuticals.
How can overproduction in manufacturing be reduced?
Better inventory management is key to reducing excess production. This would reduce the time needed to manage inventory. We could use these resources to do other productive tasks.
A Kanban system is one way to achieve this. A Kanban board can be used to monitor work progress. Kanban systems are where work items travel through a series of states until reaching their final destination. Each state is assigned a different priority.
As an example, if work is progressing from one stage of the process to another, then the current task is complete and can be transferred to the next. But if a task remains in the beginning stages it will stay that way until it reaches its end.
This allows for work to continue moving forward, while also ensuring that there is no work left behind. With a Kanban board, managers can see exactly how much work is being done at any given moment. This data allows them adjust their workflow based upon real-time data.
Lean manufacturing is another way to manage inventory levels. Lean manufacturing focuses on eliminating waste throughout the entire production chain. Anything that does not contribute to the product's value is considered waste. The following are examples of common waste types:
-
Overproduction
-
Inventory
-
Packaging that is not necessary
-
Exceed materials
Manufacturers can increase efficiency and decrease costs by implementing these ideas.
Can certain manufacturing steps be automated?
Yes! Automation has been around since ancient times. The Egyptians discovered the wheel thousands and years ago. We now use robots to help us with assembly lines.
There are many uses of robotics today in manufacturing. These include:
-
Automated assembly line robots
-
Robot welding
-
Robot painting
-
Robotics inspection
-
Robots that produce products
Automation can be applied to manufacturing in many other ways. 3D printing, for example, allows us to create custom products without waiting for them to be made.
What is production management?
Production Planning includes planning for all aspects related to production. This document will ensure everything is in order and ready to go when you need it. This document should include information about how to achieve the best results on-set. This includes shooting schedules, locations, cast lists, crew details, and equipment requirements.
The first step in filming is to define what you want. You may have already decided where you would like to shoot, or maybe there are specific locations or sets that you want to use. Once you have identified your locations and scenes it's time to begin figuring out what elements you will need for each one. One example is if you are unsure of the exact model you want but decide that you require a car. This is where you can look up car models online and narrow down your options by choosing from different makes and models.
After you've found the perfect car, it's time to start thinking about adding extras. Are you looking for people to sit in the front seats? Or perhaps you need someone walking around the back of the car? Maybe you'd like to change the interior from black to a white color. These questions will help to determine the style and feel of your car. It is also worth considering the types of shots that you wish to take. You will be filming close-ups and wide angles. Perhaps you want to show the engine or the steering wheel? All of these things will help you identify the exact style of car you want to film.
Once you have determined all of the above, you can move on to creating a schedule. A schedule will tell you when you need to start shooting and when you need to finish. A schedule for each day will detail when you should arrive at the location and when you need leave. It will help everyone know exactly what they have to do and when. If you need to hire extra staff, you can make sure you book them in advance. It's not worth paying someone to show up if you haven't told him.
It is important to calculate the amount of filming days when you are creating your schedule. Some projects can be completed in a matter of days or weeks. Others may take several days. You should consider whether you will need more than one shot per week when creating your schedule. Multiple takes at the same place will result in higher costs and longer completion times. If you aren't sure whether you need multiple shots, it is best to take fewer photos than you would like.
Budget setting is an important part of production planning. You will be able to manage your resources if you have a realistic budget. It is possible to reduce the budget at any time if you experience unexpected problems. It is important to not overestimate how much you will spend. You'll end up with less money after paying for other things if the cost is underestimated.
Production planning is a complicated process. But once you understand how everything works together, it becomes much easier to plan future project.
Statistics
- It's estimated that 10.8% of the U.S. GDP in 2020 was contributed to manufacturing. (investopedia.com)
- Job #1 is delivering the ordered product according to specifications: color, size, brand, and quantity. (netsuite.com)
- (2:04) MTO is a production technique wherein products are customized according to customer specifications, and production only starts after an order is received. (oracle.com)
- In the United States, for example, manufacturing makes up 15% of the economic output. (twi-global.com)
- Many factories witnessed a 30% increase in output due to the shift to electric motors. (en.wikipedia.org)
External Links
How To
How to use 5S to increase Productivity in Manufacturing
5S stands for "Sort", "Set In Order", "Standardize", "Separate" and "Store". Toyota Motor Corporation developed the 5S method in 1954. This methodology helps companies improve their work environment to increase efficiency.
This method aims to standardize production processes so that they are repeatable, measurable and predictable. This means that daily tasks such as cleaning and sorting, storage, packing, labeling, and packaging are possible. This knowledge allows workers to be more efficient in their work because they are aware of what to expect.
There are five steps to implementing 5S, including Sort, Set In Order, Standardize, Separate and Store. Each step requires a different action to increase efficiency. Sorting things makes it easier to find them later. When you set items in an order, you put items together. After you have divided your inventory into groups you can store them in easy-to-reach containers. Finally, when you label your containers, you ensure everything is labeled correctly.
Employees need to reflect on how they do their jobs. Employees should understand why they do the tasks they do, and then decide if there are better ways to accomplish them. To implement the 5S system, employees must acquire new skills and techniques.
In addition to increasing efficiency, the 5S method also improves morale and teamwork among employees. As they begin to see improvements, they feel motivated to continue working towards the goal of achieving higher levels of efficiency.