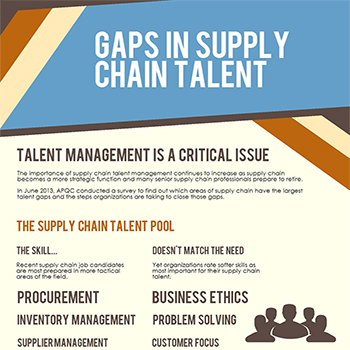
There are thousands more Connecticut manufacturing jobs that need to filled. There are currently 411 factories in Connecticut and 159,000 employees. Manufacturing is the largest contributor to the state’s gross state products and has a salary that is above the average for the state. Recent surveys by the Connecticut Business and Industry Association revealed that there are a lot of needs in the manufacturing sector. They found that 13,000 state-owned manufacturing jobs are not being filled, and that many companies struggle with younger workers.
Connecticut's manufacturing workforce is older. A third of those workers are over 55. Many companies relocated manufacturing facilities to lower labor costs, and other operations began using new machinery and automation. Although manufacturing used to be considered hazardous and dirty in the past it has gained a better reputation. Today, there are many entry-level and apprenticeship positions offered by companies. Manufacturing is the third largest job creator in Connecticut. Its high tech operations are a key competitive advantage.
Connecticut has a number of public and private education programs designed to help people become qualified for manufacturing jobs. Manufacturing Innovation Fund is one of these programs. It supports vocational high schools, high schools, and comprehensive high-schools. It also supports online training programs, pre-apprenticeships, and career activities for K-12 students.
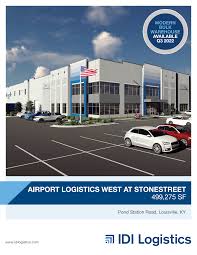
Many backgrounds go into becoming advanced manufacturing workers. Some people start in the manufacturing field right out of high school. Other workers have been working for many years in another industry before switching to it. Some may have gone to school for a degree or have been in the military for many years. Many companies will offer tuition assistance for advanced manufacturing and wage subsidies for entry-level programs.
The state's Comprehensive High Schools have also begun reintroducing technical education options. One example of this is the Grasso Tech welder program which will start in fall 2019. Employers that hire through the EB are open to hiring students from Connecticut. The Eastern Connecticut Manufacturing Pipeline, a program that supports advanced manufacturing companies in the area, is available. It was inspired by the Eastern Connecticut Workforce Investment Board's Manufacturing Pipeline.
The Manufacturing Careers Program is designed to help job seekers who are interested in manufacturing careers demonstrate their readiness for entry level work. The program connects pre-screened job seekers with manufacturers and other employers. This program includes a CNC Basics course and offers an industry-infused career path. The Advanced Manufacturing Employer Partnership offers wage subsidies to entry-level training for those who enroll in the program.
The manufacturing industry may be unfamiliar to young workers entering the workforce. These young people might not have the knowledge necessary to be able to attend these education programs. The state has allocated tens of millions of dollars for these programs. These programs have a limited reach as young people are unaware of the existence of these jobs.
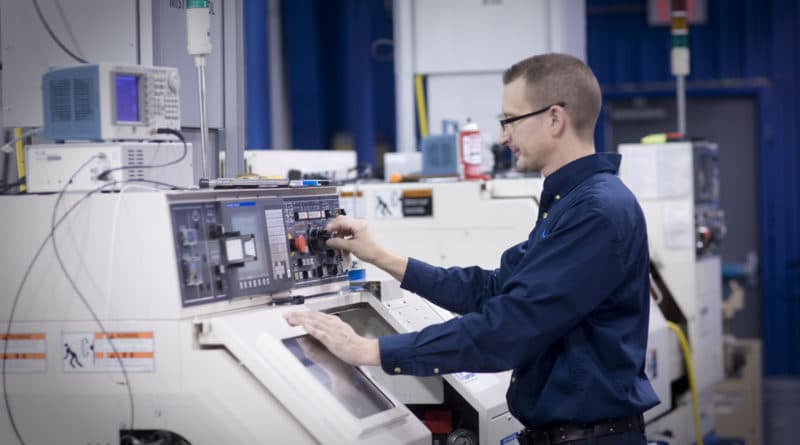
One innovative idea for helping address Connecticut's manufacturing jobs shortage is a statewide STEM Town initiative. This would mean reallocating resources, improving education programs and meeting the needs manufacturers.
FAQ
What is the distinction between Production Planning or Scheduling?
Production Planning (PP), also known as forecasting and identifying production capacities, is the process that determines what product needs to be produced at any particular time. Forecasting and identifying production capacity are two key elements to this process.
Scheduling involves the assignment of dates and times to tasks in order to complete them within the timeframe.
What does manufacturing industry mean?
Manufacturing Industries are those businesses that make products for sale. Consumers are the people who purchase these products. These companies employ many processes to achieve this purpose, such as production and distribution, retailing, management and so on. They manufacture goods from raw materials using machines and other equipment. This covers all types of manufactured goods including clothing, food, building supplies and furniture, as well as electronics, tools, machinery, vehicles and pharmaceuticals.
What are the responsibilities of a logistic manager?
A logistics manager ensures that all goods are delivered on time and without damage. This is done through his/her expertise and knowledge about the company's product range. He/she must also ensure sufficient stock to meet the demand.
Why is logistics so important in manufacturing?
Logistics are an essential component of any business. Logistics can help you achieve amazing results by helping to manage product flow from raw materials to finished products.
Logistics are also important in reducing costs and improving efficiency.
How can we reduce manufacturing overproduction?
Improved inventory management is the key to reducing overproduction. This would decrease the time that is spent on inefficient activities like purchasing, storing, or maintaining excess stock. By doing this, we could free up resources for other productive tasks.
One way to do this is to adopt a Kanban system. A Kanban board can be used to monitor work progress. Kanban systems allow work items to move through different states until they reach their final destination. Each state represents a different priority.
For instance, when work moves from one stage to another, the current task is complete enough to be moved to the next stage. But if a task remains in the beginning stages it will stay that way until it reaches its end.
This allows for work to continue moving forward, while also ensuring that there is no work left behind. Managers can view the Kanban board to see how much work they have done. This data allows them adjust their workflow based upon real-time data.
Lean manufacturing is another option to control inventory levels. Lean manufacturing is about eliminating waste from all stages of the production process. Any product that isn't adding value can be considered waste. Some common types of waste include:
-
Overproduction
-
Inventory
-
Packaging that is not necessary
-
Materials in excess
Manufacturers can reduce their costs and improve their efficiency by using these ideas.
Is automation necessary in manufacturing?
Not only is automation important for manufacturers, but it's also vital for service providers. They can provide services more quickly and efficiently thanks to automation. It helps them to lower costs by reducing human errors, and improving productivity.
What are the essential elements of running a logistics firm?
It takes a lot of skills and knowledge to run a successful logistics business. Good communication skills are essential to effectively communicate with your suppliers and clients. It is important to be able to analyse data and draw conclusions. You will need to be able handle pressure well and work in stressful situations. To improve efficiency, you must be innovative and creative. To motivate and guide your team towards reaching organizational goals, you must have strong leadership skills.
You should also be organized and efficient to meet tight deadlines.
Statistics
- Job #1 is delivering the ordered product according to specifications: color, size, brand, and quantity. (netsuite.com)
- It's estimated that 10.8% of the U.S. GDP in 2020 was contributed to manufacturing. (investopedia.com)
- In the United States, for example, manufacturing makes up 15% of the economic output. (twi-global.com)
- According to a Statista study, U.S. businesses spent $1.63 trillion on logistics in 2019, moving goods from origin to end user through various supply chain network segments. (netsuite.com)
- [54][55] These are the top 50 countries by the total value of manufacturing output in US dollars for its noted year according to World Bank.[56] (en.wikipedia.org)
External Links
How To
Six Sigma in Manufacturing:
Six Sigma refers to "the application and control of statistical processes (SPC) techniques in order to achieve continuous improvement." Motorola's Quality Improvement Department created Six Sigma at their Tokyo plant, Japan in 1986. Six Sigma's main goal is to improve process quality by standardizing processes and eliminating defects. Many companies have adopted this method in recent years. They believe there is no such thing a perfect product or service. Six Sigma aims to reduce variation in the production's mean value. This means that you can take a sample from your product and then compare its performance to the average to find out how often the process differs from the norm. If this deviation is too big, you know something needs fixing.
Understanding the dynamics of variability within your business is the first step in Six Sigma. Once you've understood that, you'll want to identify sources of variation. Also, you will need to identify the sources of variation. Random variations are caused by human errors. Systematic variations can be caused by outside factors. These are, for instance, random variations that occur when widgets are made and some fall off the production line. If however, you notice that each time you assemble a widget it falls apart in exactly the same spot, that is a problem.
After identifying the problem areas, you will need to devise solutions. It might mean changing the way you do business or redesigning it entirely. You should then test the changes again after they have been implemented. If they don’t work, you’ll need to go back and rework the plan.