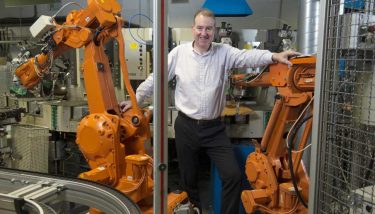
Journal impact factors
Journal impact factors in supply chain management are a useful tool to compare the relative influence of supply chain management journals. These factors are calculated from data from the ISI Web of Science and ten of the most prestigious academic supply-chain management journals. These results allow us compare and contrast the relative impact of journals and authors on the field.
Journal impact factors can be used to evaluate a journal's quality. A journal that has a high ranking will likely be high-quality because it attracts high quality research. Journal impact factors take into account the number of citations a journal receives, as well as the importance of other journals. Emerald Group Publishing Ltd. (a British publishing company) is the Journal's editor.
Scope and purpose of the journal
The journal supply chain management encompasses a wide range of topics, including transportation and logistics. Its mission is to create a dynamic forum for research-based information in these areas. These articles are welcome to be published in the journal. However, not all submitted articles will be published in this journal.
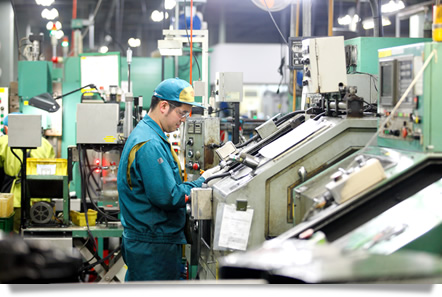
SCMij publishes international research on supply chain management. It provides a forum for discussion of empirical and theoretical research. It is open for submissions from practitioners and scholars.
Editorial board
The Editorial board of a journal evaluates the scientific content. Its membership consists of renowned scientists from different fields of knowledge. The Board maintains confidentiality of manuscript information, and is bound to the editorial codes of conduct. The journal is available for search through major search engines and is listed in numerous international scientific databases.
The Journal of Supply Chain Management’s Editorial board is comprised of experts who specialize in supply chain management as well as procurement and logistics. Each article submitted for publication undergoes peer review to ensure its relevance and practicality.
Authors of articles in the journal
The Journal of Supply Chain Management invites submissions by supply chain management, logistics, or procurement professionals. The journal publishes original research and reviews on supply chain management. Your articles should be at most three thousand words long, and you must discuss innovative techniques or ways to solve problems.
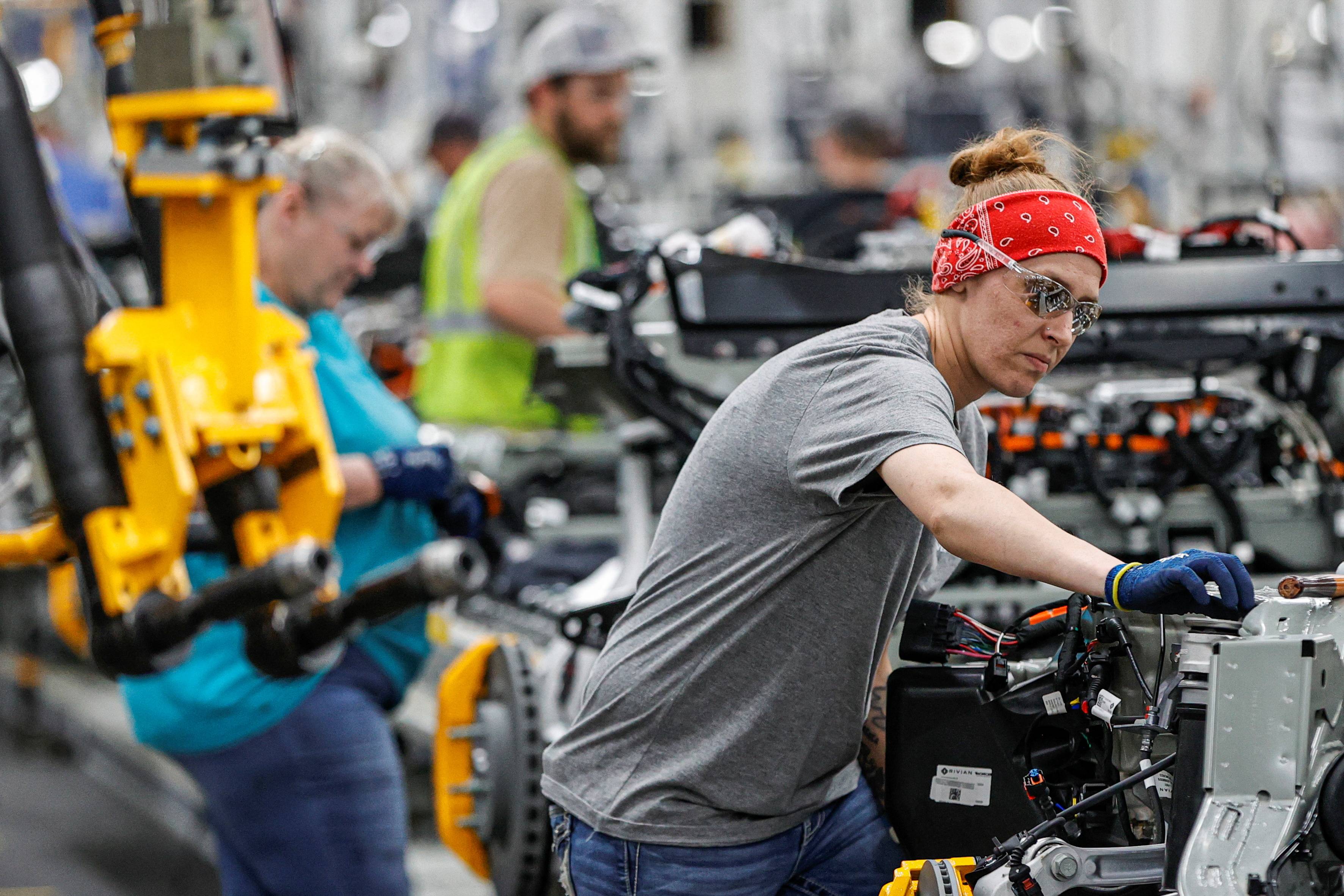
Online submissions are possible. They can be submitted in text format or as separate files with illustrations. Authors should make sure that their contact details are accurate, and the article should include the most recent address and e-mail. The journal doesn't charge for publication or submission.
Number of articles published in the journal every year
The Journal of Supply Chain Management published articles in multiple journals. The journal's h index is high, which means that it is high in productivity and has high citation impacts. The International Standard Serial Number for journals is 15232409 and the total ISSN of the journal.
This journal publishes articles from academics and practitioners working in the field of supply chain management. Its articles provide thought leadership on supply chain operations. It also publishes columnists and features from supply-chain practitioners and industry experts. It also publishes many case reports on companies and supply chains.
FAQ
What are manufacturing and logistics?
Manufacturing is the production of goods using raw materials. Logistics includes all aspects related to supply chain management, such as procurement, distribution planning, inventory control and transportation. Sometimes manufacturing and logistics are combined to refer to a wider term that includes both the process of creating products as well as their delivery to customers.
What is production planning?
Production Planning involves developing a plan for all aspects of the production, including scheduling, budgeting, casting, crew, location, equipment, props, etc. It is important to have everything ready and planned before you start shooting. It should also provide information about how best to produce the best results while on set. This includes shooting schedules, locations, cast lists, crew details, and equipment requirements.
First, you need to plan what you want to film. You may have decided where to shoot or even specific locations you want to use. Once you have identified your locations and scenes it's time to begin figuring out what elements you will need for each one. Perhaps you have decided that you need to buy a car but aren't sure which model. This is where you can look up car models online and narrow down your options by choosing from different makes and models.
Once you have found the right vehicle, you can think about adding accessories. Do you need people sitting in the front seats? Perhaps you have someone who needs to be able to walk around the back of your car. You may want to change the interior's color from black or white. These questions will help to determine the style and feel of your car. It is also worth considering the types of shots that you wish to take. Will you be filming close-ups or wide angles? Perhaps you want to show the engine or the steering wheel? These details will help identify the exact car you wish to film.
Once you have all the information, you are ready to create a plan. You can create a schedule that will outline when you must start and finish your shoots. A schedule for each day will detail when you should arrive at the location and when you need leave. It will help everyone know exactly what they have to do and when. Book extra staff ahead of time if you need them. It is not worth hiring someone who won’t show up because you didn’t tell him.
Also, consider how many days you will be filming your schedule. Some projects only take one or two days, while others may last weeks. While creating your schedule, it is important to remember whether you will require more than one shot per day. Multiple shots at the same location can increase costs and make it more difficult to complete. It's better to be safe than sorry and shoot less takes if you're not certain whether you need more takes.
Budgeting is another crucial aspect of production plan. A realistic budget will help you work within your means. You can always lower the budget if you encounter unexpected problems. It is important to not overestimate how much you will spend. You will end up spending less money if you underestimate the cost of something.
Production planning can be a complex process. However, once you know how everything works together it will become easier to plan future projects.
What are the goods of logistics?
Logistics is the process of moving goods from one point to another.
They include all aspects of transport, including packaging, loading, transporting, unloading, storing, warehousing, inventory management, customer service, distribution, returns, and recycling.
Logisticians ensure that products reach the right destination at the right moment and under safe conditions. They help companies manage their supply chain efficiency by providing information on demand forecasts, stock levels, production schedules, and availability of raw materials.
They also keep track of shipments in transit, monitor quality standards, perform inventories and order replenishment, coordinate with suppliers and vendors, and provide support services for sales and marketing.
Statistics
- In the United States, for example, manufacturing makes up 15% of the economic output. (twi-global.com)
- According to a Statista study, U.S. businesses spent $1.63 trillion on logistics in 2019, moving goods from origin to end user through various supply chain network segments. (netsuite.com)
- It's estimated that 10.8% of the U.S. GDP in 2020 was contributed to manufacturing. (investopedia.com)
- Many factories witnessed a 30% increase in output due to the shift to electric motors. (en.wikipedia.org)
- According to the United Nations Industrial Development Organization (UNIDO), China is the top manufacturer worldwide by 2019 output, producing 28.7% of the total global manufacturing output, followed by the United States, Japan, Germany, and India.[52][53] (en.wikipedia.org)
External Links
How To
How to Use the Just-In-Time Method in Production
Just-in-time (JIT) is a method that is used to reduce costs and maximize efficiency in business processes. It is a process where you get the right amount of resources at the right moment when they are needed. This means that your only pay for the resources you actually use. Frederick Taylor was the first to coin this term. He developed it while working as a foreman during the early 1900s. He saw how overtime was paid to workers for work that was delayed. He decided that workers would be more productive if they had enough time to complete their work before they started to work.
JIT is an acronym that means you need to plan ahead so you don’t waste your money. Look at your entire project, from start to end. Make sure you have enough resources in place to deal with any unexpected problems. You'll be prepared to handle any potential problems if you know in advance. This will ensure that you don't spend more money on things that aren't necessary.
There are many JIT methods.
-
Demand-driven JIT: You order the parts and materials you need for your project every other day. This will allow you to track how much material you have left over after using it. This will allow you to calculate how long it will take to make more.
-
Inventory-based : You can stock the materials you need in advance. This allows you to predict how much you can expect to sell.
-
Project-driven : This is a method where you make sure that enough money is set aside to pay the project's cost. If you know the amount you require, you can buy the materials you need.
-
Resource-based JIT: This is the most popular form of JIT. Here you can allocate certain resources based purely on demand. You might assign more people to help with orders if there are many. You'll have fewer orders if you have fewer.
-
Cost-based: This is similar to resource-based, except that here you're not just concerned about how many people you have but how much each person costs.
-
Price-based: This is similar to cost-based but instead of looking at individual workers' salaries, you look at the total company price.
-
Material-based - This is a variant of cost-based. But instead of looking at the total company cost, you focus on how much raw material you spend per year.
-
Time-based: This is another variation of resource-based JIT. Instead of focusing only on how much each employee is costing, you should focus on how long it takes to complete your project.
-
Quality-based JIT - This is another form of resource-based JIT. Instead of looking at the labor costs and time it takes to make a product, think about its quality.
-
Value-based JIT is the newest form of JIT. In this instance, you are not concerned about the product's performance or meeting customer expectations. Instead, your goal is to add value to the market.
-
Stock-based: This inventory-based approach focuses on how many items are being produced at any one time. This method is useful when you want to increase production while decreasing inventory.
-
Just-in-time (JIT) planning: This is a combination of JIT and supply chain management. It is the process of scheduling components' delivery as soon as they have been ordered. It's important as it reduces leadtimes and increases throughput.