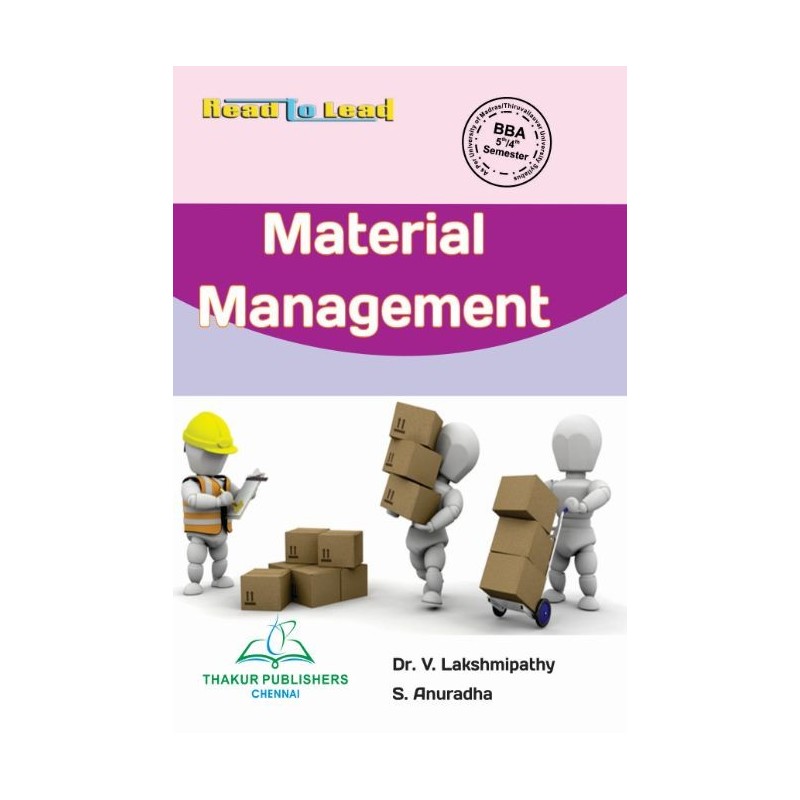
National Institute of Standards and Technology, which was founded in 1901 is one of the oldest US physical science laboratories. Its mission involves improving the quality of American life and increasing the productivity of American industry through science, technology. Located in Gaithersburg, Maryland, NIST is a member of the United States Department of Commerce. Its staff works in collaboration with federal agencies on standards, metrics, as well as best practices to improve productivity, increase economic security, and facilitate international trade. NIST plays an important role in the improvement of U.S. industrial competivity and quality assurance.
NIST's mission is to improve the quality of life by advancing scientific and technical innovation, developing and maintaining national standards of physical measurement, and promoting the innovation of U.S. industries. NIST has two locations: Gaithersburg in Maryland and Boulder in Colorado. NIST develops standards, metrics and best practices. NIST also conducts research in order to improve the technological infrastructure of the U.S.
The National Institute of Standards and Technology(NIST) was originally established as a metrology bureau. In its early years, the Bureau of Standards aimed to solve national problems in science, commerce, and technology. A variety of industries were served by standards, including electronics as well as electrical safety and automobile brake systems. The Bureau of Standards had a manufacturing facility for optical glass and was involved in multiple issues during World War I.
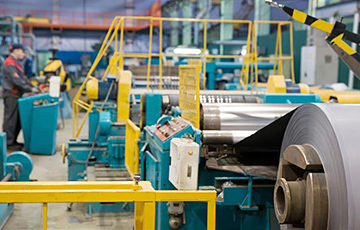
NIST also creates standards, metrics and best practices in a range of industries including electronics, transport, manufacturing and public health. NIST provides assistance to industry in the development of procedures that will improve manufacturing production. NIST also develops Federal Information Processing Standards (FIPS), which are approved for use by the Secretary of Commerce.
Journal of Research of National Institute of Standards and Technology (official scientific journal of the National Institute of Standards and Technology) is also published by National Institute of Standards and Technology. NIST's research outputs are tracked in the Nature Index. NIST is currently North America's largest research center.
In 1988, NIST was established as the National Bureau of Standards. This was to better reflect NBS's vast mission. The Omnibus Trade and Competitiveness Act of 1989, signed into law by President Reagan on August 23, 1988 expanded NBS's technical knowledge and gave NIST additional responsibilities. The law also explicitly confirmed traditional measurement services.
The NIST will continue to provide a full range of measurement services. It will also increase its technology assistance to extension service providers and coordinate state extension services with federal technologies transfer programs. To increase its reach, the program will partner with an existing network. The program will also conduct workshops on technological issues to help ensure that NIST resources are used effectively.
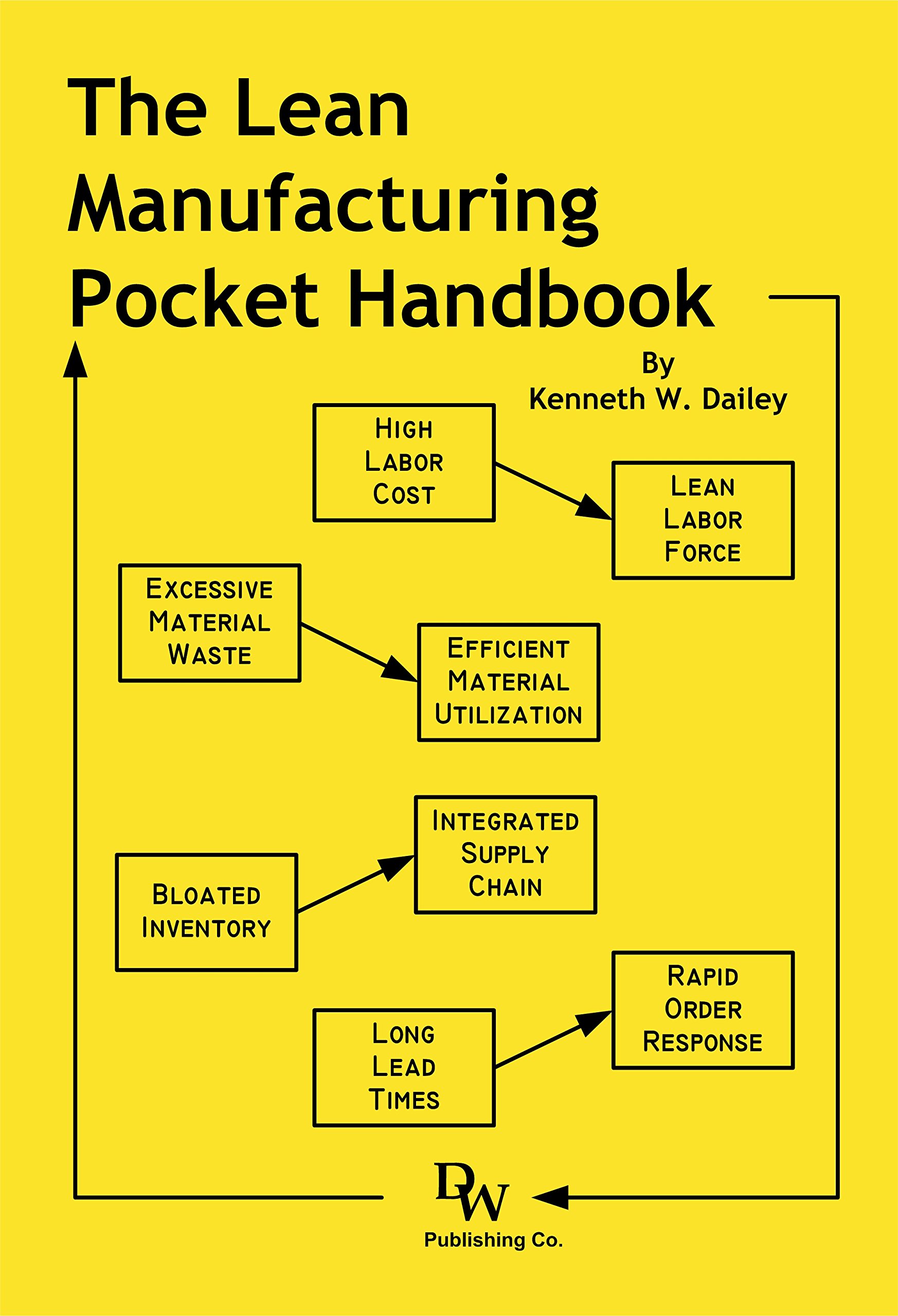
NIST will remain a trusted partner in the U.S.'s industrial competitiveness improvement efforts by providing assistance to American industry with technology, standards, practices, and best practice. In addition to developing standards, metrics, best practices, and quality assurance, NIST also assists federal agencies to develop cost-effective programs. It places great emphasis on national defense. Although its recommendations are not binding on the private sector, they provide a foundation for federal agencies.
FAQ
How does a production planner differ from a project manager?
The main difference between a production planner and a project manager is that a project manager is usually the person who plans and organizes the entire project, whereas a production planner is mainly involved in the planning stage of the project.
How can manufacturing avoid production bottlenecks
You can avoid bottlenecks in production by making sure that everything runs smoothly throughout the production cycle, from the moment you receive an order to the moment the product is shipped.
This includes planning to meet capacity requirements and quality control.
The best way to do this is to use continuous improvement techniques such as Six Sigma.
Six Sigma is a management system used to improve quality and reduce waste in every aspect of your organization.
It is focused on creating consistency and eliminating variation in your work.
Are there any Manufacturing Processes that we should know before we can learn about Logistics?
No. No. But, being familiar with manufacturing processes will give you a better understanding about how logistics works.
How can efficiency in manufacturing be improved?
First, we need to identify which factors are most critical in affecting production times. Then we need to find ways to improve these factors. If you aren't sure where to begin, think about the factors that have the greatest impact on production time. Once you have identified them, it is time to identify solutions.
Statistics
- (2:04) MTO is a production technique wherein products are customized according to customer specifications, and production only starts after an order is received. (oracle.com)
- According to the United Nations Industrial Development Organization (UNIDO), China is the top manufacturer worldwide by 2019 output, producing 28.7% of the total global manufacturing output, followed by the United States, Japan, Germany, and India.[52][53] (en.wikipedia.org)
- Job #1 is delivering the ordered product according to specifications: color, size, brand, and quantity. (netsuite.com)
- [54][55] These are the top 50 countries by the total value of manufacturing output in US dollars for its noted year according to World Bank.[56] (en.wikipedia.org)
- You can multiply the result by 100 to get the total percent of monthly overhead. (investopedia.com)
External Links
How To
How to use lean manufacturing in the production of goods
Lean manufacturing (or lean manufacturing) is a style of management that aims to increase efficiency, reduce waste and improve performance through continuous improvement. It was created in Japan by Taiichi Ohno during the 1970s and 80s. He received the Toyota Production System award (TPS), from Kanji Toyoda, founder of TPS. Michael L. Watkins published the first book on lean manufacturing in 1990.
Lean manufacturing can be described as a set or principles that are used to improve quality, speed and cost of products or services. It emphasizes the elimination and minimization of waste in the value stream. Lean manufacturing is also known as just in time (JIT), zero defect total productive maintenance(TPM), and five-star (S). Lean manufacturing focuses on eliminating non-value-added activities such as rework, inspection, and waiting.
Lean manufacturing can help companies improve their product quality and reduce costs. Additionally, it helps them achieve their goals more quickly and reduces employee turnover. Lean manufacturing is considered one of the most effective ways to manage the entire value chain, including suppliers, customers, distributors, retailers, and employees. Lean manufacturing can be found in many industries. For example, Toyota's philosophy underpins its success in automobiles, electronics, appliances, healthcare, chemical engineering, aerospace, paper, food, etc.
Five fundamental principles underlie lean manufacturing.
-
Define Value - Determine the value that your business brings to society. Also, identify what sets you apart from your competitors.
-
Reduce Waste – Eliminate all activities that don't add value throughout the supply chain.
-
Create Flow – Ensure that work flows smoothly throughout the process.
-
Standardize and Simplify – Make processes as consistent, repeatable, and as simple as possible.
-
Build Relationships- Develop personal relationships with both internal as well as external stakeholders.
Lean manufacturing isn’t new, but it has seen a renewed interest since 2008 due to the global financial crisis. Many businesses have adopted lean manufacturing techniques to help them become more competitive. Some economists even believe that lean manufacturing can be a key factor in economic recovery.
Lean manufacturing is now becoming a common practice in the automotive industry, with many benefits. These include improved customer satisfaction, reduced inventory levels, lower operating costs, increased productivity, and better overall safety.
Lean manufacturing can be applied to almost every aspect of an organization. Lean manufacturing is most useful in the production sector of an organisation because it ensures that each step in the value-chain is efficient and productive.
There are three main types:
-
Just-in Time Manufacturing: This lean manufacturing method is commonly called "pull systems." JIT is a method in which components are assembled right at the moment of use, rather than being manufactured ahead of time. This approach aims to reduce lead times, increase the availability of parts, and reduce inventory.
-
Zero Defects Manufacturing (ZDM): ZDM focuses on ensuring that no defective units leave the manufacturing facility. You should repair any part that needs to be repaired during an assembly line. This also applies to finished products that need minor repairs before being shipped.
-
Continuous Improvement (CI): CI aims to improve the efficiency of operations by continuously identifying problems and making changes in order to eliminate or minimize waste. Continuous Improvement (CI) involves continuous improvement in processes, people, tools, and infrastructure.