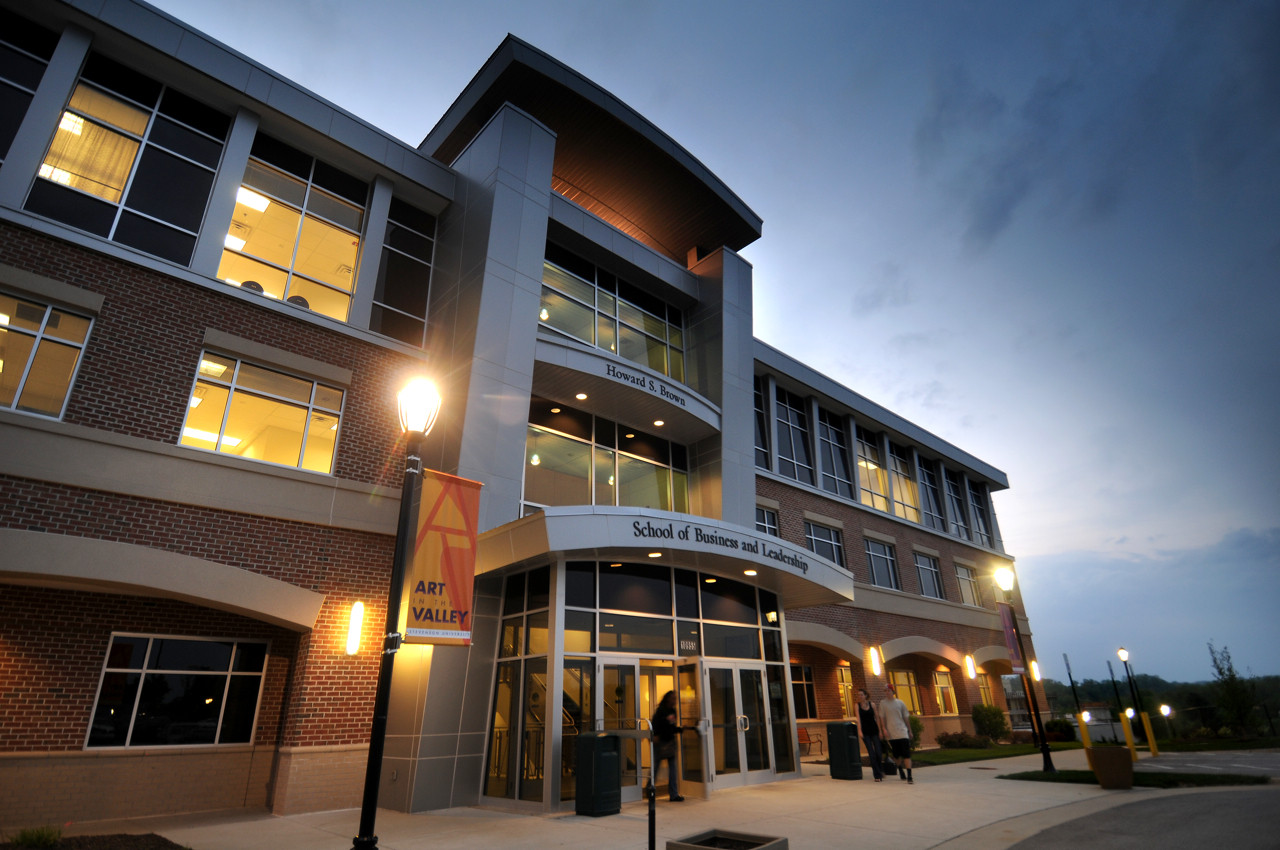
When things go awry, we need to find out why. The five whys is a technique that helps us to identify the root causes of problems.
The 5 whys are an effective tool for helping teams communicate and solve problems. It helps to foster curiosity and help teams understand each others' perspectives, so they can work with one another to find solutions. It provides a system of interrogation that can be used when team members don't know why a problem occurred or how to fix it.
What is the Five Whys Method?
The five-whys technique is an effective and simple way to find the root cause of a problem. The technique works best for simple to moderate problems but can also be used in complex cases.
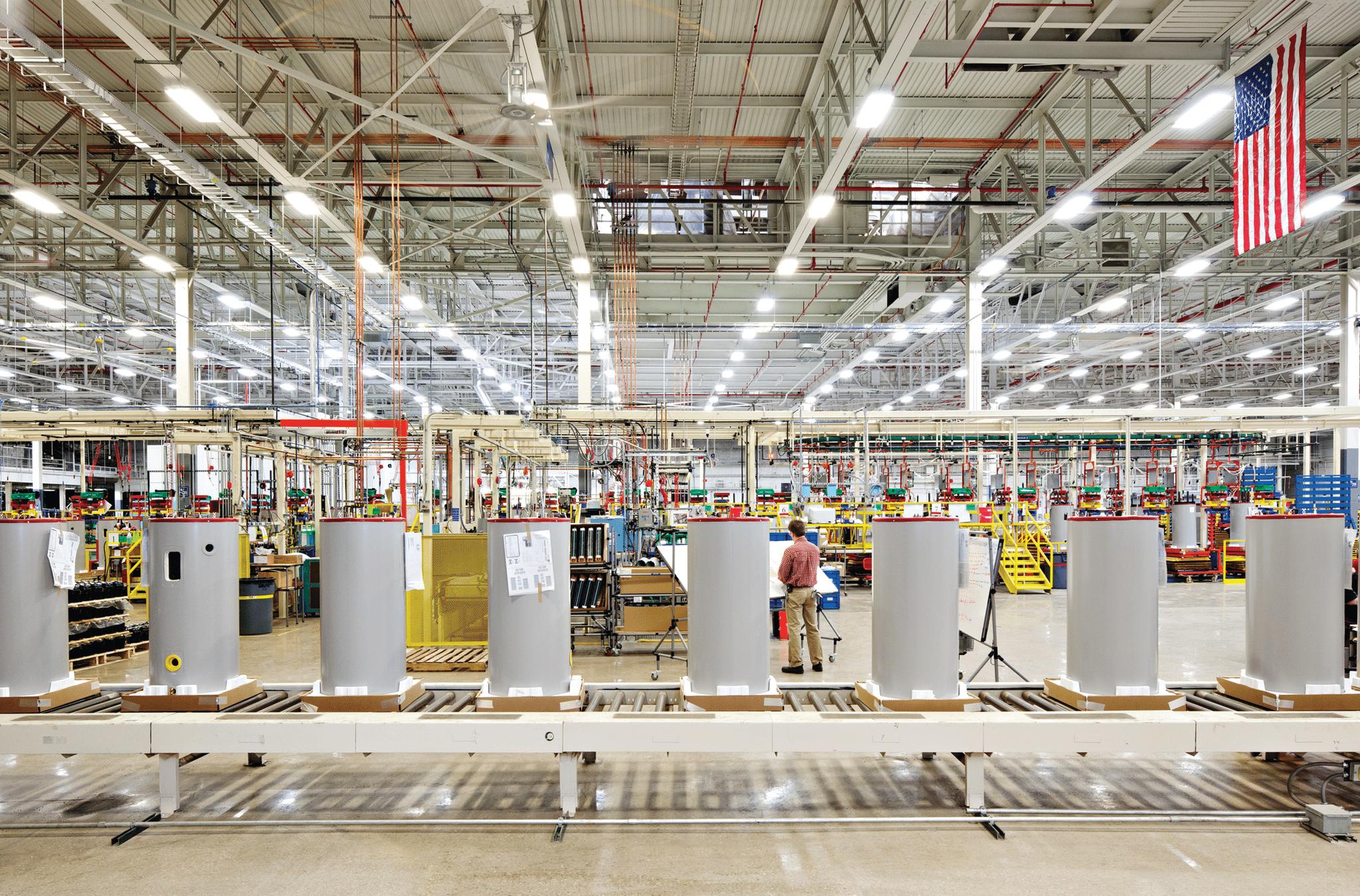
Depending on the type of problem, you may need to ask more than 5 whys. This is especially true when there are several potential root causes.
How to Use the 5 Whys Method
It is important to put together a team that has experience in the area. People from various departments and industries can be included. They will be able to provide new ideas and perspectives from a range of different departments.
After the team has been assembled, the members should begin by discussing the issue and asking the five Whys questions. This will allow the team to determine what the real problem is and determine if it can be solved immediately or whether a long term countermeasure must be put in place.
Next, they must carefully review each question and determine if a reasonable reply is produced. This step is crucial because it will help them feel confident that their analysis is going well.
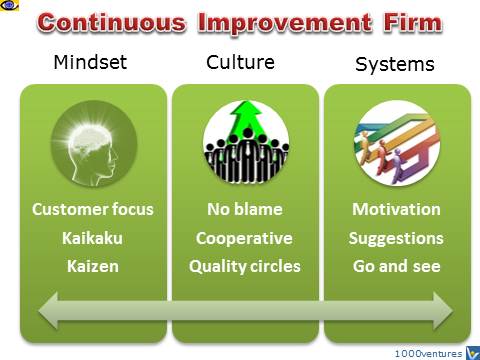
Continue asking the five whys, until you are able determine the root of the problem. Next, come up with countermeasures which will stop the issue from happening in the future. Once the root cause is determined, they should assign each of the corrective actions to a member of the team who can take responsibility for it.
The five whys are a great way to pinpoint the root causes for any issue within your organisation. This tool is particularly effective when combined with other tools such as FMEA and cause-and-effect analysis in order to better understand root causes.
FAQ
What is meant by manufacturing industries?
Manufacturing Industries are companies that manufacture products. Consumers are the people who purchase these products. These companies use various processes such as production, distribution, retailing, management, etc., to fulfill this purpose. These companies produce goods using raw materials and other equipment. This includes all types of manufactured goods, including food items, clothing, building supplies, furniture, toys, electronics, tools, machinery, vehicles, pharmaceuticals, medical devices, chemicals, and many others.
What is the difference between Production Planning and Scheduling?
Production Planning (PP) is the process of determining what needs to be produced at any given point in time. This is accomplished by forecasting the demand and identifying production resources.
Scheduling refers to the process of allocating specific dates to tasks in order that they can be completed within a specified timeframe.
Why automate your warehouse
Automation has become increasingly important in modern warehousing. E-commerce has increased the demand for quicker delivery times and more efficient processes.
Warehouses must adapt quickly to meet changing customer needs. In order to do this, they need to invest in technology. Automating warehouses has many benefits. These are some of the benefits that automation can bring to warehouses:
-
Increases throughput/productivity
-
Reduces errors
-
Accuracy is improved
-
Safety Boosts
-
Eliminates bottlenecks
-
Companies can scale up more easily
-
Makes workers more efficient
-
Gives you visibility into all that is happening in your warehouse
-
Enhances customer experience
-
Improves employee satisfaction
-
It reduces downtime, and increases uptime
-
High quality products delivered on-time
-
Removing human error
-
This helps to ensure compliance with regulations
What is the role of a production manager?
A production planner makes sure all project elements are delivered on schedule, within budget, as well as within the agreed scope. A production planner ensures that the service and product meet the client's expectations.
Statistics
- Job #1 is delivering the ordered product according to specifications: color, size, brand, and quantity. (netsuite.com)
- According to the United Nations Industrial Development Organization (UNIDO), China is the top manufacturer worldwide by 2019 output, producing 28.7% of the total global manufacturing output, followed by the United States, Japan, Germany, and India.[52][53] (en.wikipedia.org)
- In the United States, for example, manufacturing makes up 15% of the economic output. (twi-global.com)
- [54][55] These are the top 50 countries by the total value of manufacturing output in US dollars for its noted year according to World Bank.[56] (en.wikipedia.org)
- You can multiply the result by 100 to get the total percent of monthly overhead. (investopedia.com)
External Links
How To
How to use the Just-In Time Method in Production
Just-in-time is a way to cut costs and increase efficiency in business processes. It allows you to get the right amount resources at the right time. This means that only what you use is charged to your account. Frederick Taylor was the first to coin this term. He developed it while working as a foreman during the early 1900s. Taylor observed that overtime was paid to workers if they were late in working. He concluded that if workers were given enough time before they start work, productivity would increase.
JIT teaches you to plan ahead and prepare everything so you don’t waste time. The entire project should be looked at from start to finish. You need to ensure you have enough resources to tackle any issues that might arise. If you anticipate that there might be problems, you'll have enough people and equipment to fix them. This way you won't be spending more on things that aren’t really needed.
There are different types of JIT methods:
-
Demand-driven: This type of JIT allows you to order the parts/materials required for your project on a regular basis. This will allow to track how much material has been used up. This will allow to you estimate the time it will take for more to be produced.
-
Inventory-based: This is a type where you stock the materials required for your projects in advance. This allows you predict the amount you can expect to sell.
-
Project-driven: This method allows you to set aside enough funds for your project. Once you have an idea of how much material you will need, you can purchase the necessary materials.
-
Resource-based JIT : This is probably the most popular type of JIT. You assign certain resources based off demand. You will, for example, assign more staff to deal with large orders. You'll have fewer orders if you have fewer.
-
Cost-based: This is similar to resource-based, except that here you're not just concerned about how many people you have but how much each person costs.
-
Price-based: This approach is very similar to the cost-based method except that you don't look at individual workers costs but the total cost of the company.
-
Material-based - This is a variant of cost-based. But instead of looking at the total company cost, you focus on how much raw material you spend per year.
-
Time-based JIT: This is another variant of resource-based JIT. Instead of focusing only on how much each employee is costing, you should focus on how long it takes to complete your project.
-
Quality-based JIT - This is another form of resource-based JIT. Instead of worrying about the costs of each employee or how long it takes for something to be made, you should think about how quality your product is.
-
Value-based JIT: This is the latest form of JIT. This is where you don't care about how the products perform or whether they meet customers' expectations. Instead, you are focused on adding value to the marketplace.
-
Stock-based: This is an inventory-based method that focuses on the actual number of items being produced at any given time. It's useful when you want maximum production and minimal inventory.
-
Just-in-time (JIT) planning: This is a combination of JIT and supply chain management. This refers to the scheduling of the delivery of components as soon after they are ordered. It's important because it reduces lead times and increases throughput.