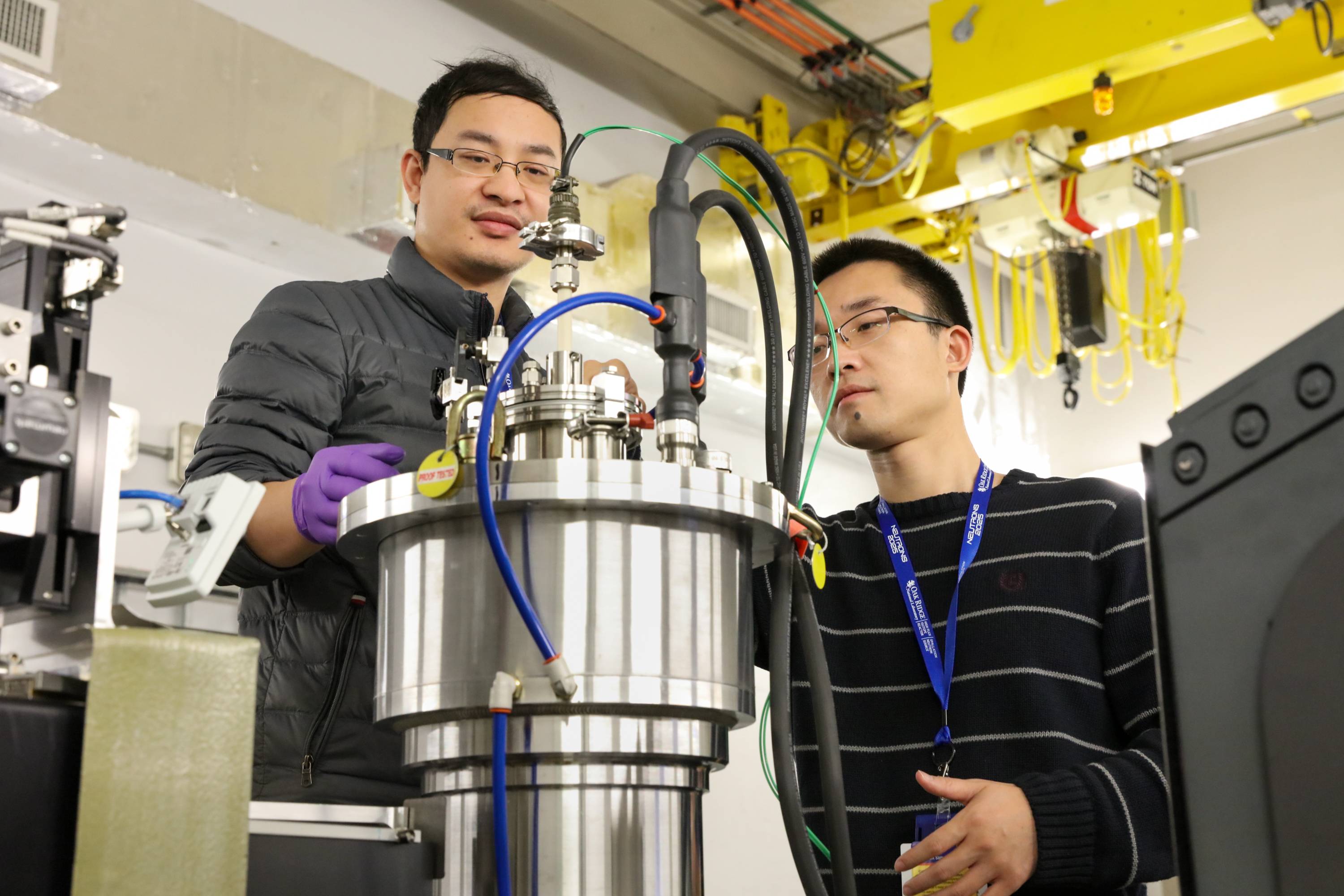
Throughout the years, global supply chains have undergone several changes. They have changed from being a problem for industrial purposes to becoming a serious economic risk. It's a good idea keep track of new developments. Global supply chains interact in many different ways.
Global value chains are a mix of flows, intangibles and capital. They reflect economies of scale, long-standing relationships and specialization. Some value chains are capital-intensive while others are more localized.
Global supply chains have become more complex, dynamic and multidimensional. They are essential for global trade and the functioning economies. They are also susceptible to disruptions. These disruptions are either short-term or long-lasting. To counter these disruptions, it is important to create a flexible, resilient, and diversified supply chain. This requires a comprehensive approach including strategic initiatives and risk management. Identifying the biggest challenges and assessing the solutions is the first step towards building a supply chain that can withstand the next storm.
Additionally to considering the risks from supply chain disruptions companies need to consider the associated risks with manufacturing, energy, materials. They should also simulate extreme supply/demand disruptions in an effort to gauge their impact. They should also evaluate their inventories of crucial materials and make sure that they have enough to meet the foreseeable demand. To develop a resilient supply system, it requires a strategic approach. This could include prioritizing production, moving manufacturing to more flexible locations and improving supply chain technology.
The COVID-19 pandemic caused significant disruptions to global supply chains. Some countries imposed reciprocal tariffs, while others imposed severe sanctions. These tariffs and sanctions increased trade frictions, making it more difficult for the United States and other countries to sell certain products. These disruptions have increased price inflation. However, these disruptions have made companies more aware and re-examined the design and implementation aspects of their supply channels.
The COVID-19 pandemic caused massive disruption to global supply chains. However, these effects are still being felt. For example, the Suez Canal blockage has led to disruptions in supply chains for as long as six months. The freight costs have also increased dramatically as a result. The UK's annual inflation is now at 9%.
It is difficult not to notice that China and America are at the center of a trade war. Supply chain leaders need to question the logic behind relying so heavily upon outsourced networks. They must consider the risks associated to labor shortages as a result of economic shocks. Leaders in supply chains should also be aware of the potential benefits of cross-border finance as well as regulation that can help expand global integration.
Despite all the chaos, the world continues to be a deeply interconnected place. Global integration can be realized when firms take a holistic approach to their supply chain.
FAQ
What skills are required to be a production manager?
Being a production planner is not easy. You need to be organized and flexible. Also, you must be able and willing to communicate with clients and coworkers.
Why is logistics important for manufacturing?
Logistics are an essential component of any business. They enable you to achieve outstanding results by helping manage product flow from raw materials through to finished goods.
Logistics also play a major role in reducing costs and increasing efficiency.
What is the role and responsibility of a Production Planner?
Production planners make sure that every aspect of the project is delivered on-time, within budget, and within schedule. They ensure that the product or service is of high quality and meets client requirements.
How can manufacturing excess production be decreased?
It is essential to find better ways to manage inventory to reduce overproduction. This would decrease the time that is spent on inefficient activities like purchasing, storing, or maintaining excess stock. By doing this, we could free up resources for other productive tasks.
A Kanban system is one way to achieve this. A Kanban board, a visual display to show the progress of work, is called a Kanban board. A Kanban system allows work items to move through several states before reaching their final destination. Each state represents a different priority level.
As an example, if work is progressing from one stage of the process to another, then the current task is complete and can be transferred to the next. If a task is still in its beginning stages, it will continue to be so until it reaches the end.
This allows for work to continue moving forward, while also ensuring that there is no work left behind. With a Kanban board, managers can see exactly how much work is being done at any given moment. This information allows managers to adjust their workflow based off real-time data.
Lean manufacturing can also be used to reduce inventory levels. Lean manufacturing focuses on eliminating waste throughout the entire production chain. Anything that does not contribute to the product's value is considered waste. The following are examples of common waste types:
-
Overproduction
-
Inventory
-
Packaging that is not necessary
-
Materials in excess
By implementing these ideas, manufacturers can improve efficiency and cut costs.
How can I learn about manufacturing?
The best way to learn about manufacturing is through hands-on experience. You can read books, or watch instructional videos if you don't have the opportunity to do so.
What is production management?
Production Planning is the creation of a plan to cover all aspects, such as scheduling, budgeting. Location, crew, equipment, props and other details. This document is designed to make sure everything is ready for when you're ready to shoot. This document should include information about how to achieve the best results on-set. This includes information on shooting times, locations, cast lists and crew details.
The first step is to decide what you want. You may have decided where to shoot or even specific locations you want to use. Once you've identified the locations and scenes you want to use, you can begin to plan what elements you need for each scene. You might decide you need a car, but not sure what make or model. This is where you can look up car models online and narrow down your options by choosing from different makes and models.
After you've found the perfect car, it's time to start thinking about adding extras. Are you looking for people to sit in the front seats? Or maybe you just need someone to push the car around. Maybe you'd like to change the interior from black to a white color. These questions will help you determine the exact look and feel of your car. Another thing you can do is think about what type of shots are desired. You will be filming close-ups and wide angles. Perhaps you want to show the engine or the steering wheel? These things will help you to identify the car that you are looking for.
Once you have established all the details, you can create a schedule. The schedule will show you when to begin shooting and when to stop. Every day will have a time for you to arrive at the location, leave when you are leaving and return home when you are done. Everyone knows exactly what they should do and when. It is possible to make arrangements in advance for additional staff if you are looking to hire. You don't want to hire someone who won't show up because he didn't know.
When creating your schedule, you will also need to consider the number of days you need to film. Some projects are quick and easy, while others take weeks. While creating your schedule, it is important to remember whether you will require more than one shot per day. Multiple shots at the same location can increase costs and make it more difficult to complete. It's better to be safe than sorry and shoot less takes if you're not certain whether you need more takes.
Budgeting is another important aspect of production planning. You will be able to manage your resources if you have a realistic budget. You can always lower the budget if you encounter unexpected problems. But, don't underestimate how much money you'll spend. You will end up spending less money if you underestimate the cost of something.
Production planning is a detailed process. But, once you understand the workings of everything, it becomes easier for future projects to be planned.
Statistics
- (2:04) MTO is a production technique wherein products are customized according to customer specifications, and production only starts after an order is received. (oracle.com)
- In 2021, an estimated 12.1 million Americans work in the manufacturing sector.6 (investopedia.com)
- It's estimated that 10.8% of the U.S. GDP in 2020 was contributed to manufacturing. (investopedia.com)
- You can multiply the result by 100 to get the total percent of monthly overhead. (investopedia.com)
- Many factories witnessed a 30% increase in output due to the shift to electric motors. (en.wikipedia.org)
External Links
How To
How to Use the Just In Time Method in Production
Just-in time (JIT), is a process that reduces costs and increases efficiency in business operations. It's the process of obtaining the right amount and timing of resources when you need them. This means that you only pay the amount you actually use. The term was first coined by Frederick Taylor, who developed his theory while working as a foreman in the early 1900s. He saw how overtime was paid to workers for work that was delayed. He decided that workers would be more productive if they had enough time to complete their work before they started to work.
JIT teaches you to plan ahead and prepare everything so you don’t waste time. You should also look at the entire project from start to finish and make sure that you have sufficient resources available to deal with any problems that arise during the course of your project. You will have the resources and people to solve any problems you anticipate. This will prevent you from spending extra money on unnecessary things.
There are many JIT methods.
-
Demand-driven JIT: You order the parts and materials you need for your project every other day. This will allow for you to track the material that you have left after using it. It will also allow you to predict how long it takes to produce more.
-
Inventory-based: You stock materials in advance to make your projects easier. This allows for you to anticipate how much you can sell.
-
Project-driven : This is a method where you make sure that enough money is set aside to pay the project's cost. If you know the amount you require, you can buy the materials you need.
-
Resource-based JIT is the most widespread form. You assign certain resources based off demand. For example, if there is a lot of work coming in, you will have more people assigned to them. If you don’t have many orders you will assign less people to the work.
-
Cost-based: This approach is very similar to resource-based. However, you don't just care about the number of people you have; you also need to consider how much each person will cost.
-
Price-based: This is a variant of cost-based. However, instead of focusing on the individual workers' costs, this looks at the total price of the company.
-
Material-based: This approach is similar to cost-based. However, instead of looking at the total cost for the company, you look at how much you spend on average on raw materials.
-
Time-based JIT: A variation on resource-based JIT. Instead of focusing on the cost of each employee, you will focus on the time it takes to complete a project.
-
Quality-based JIT is another variant of resource-based JIT. Instead of focusing on the cost of each worker or how long it takes, think about how high quality your product is.
-
Value-based JIT: One of the most recent forms of JIT. You don't worry about whether the products work or if they meet customer expectations. Instead, you are focused on adding value to the marketplace.
-
Stock-based is an inventory-based system that measures the number of items produced at any given moment. It is used when production goals are met while inventory is kept to a minimum.
-
Just-intime planning (JIT), is a combination JIT/sales chain management. It is the process that schedules the delivery of components within a short time of their order. This is important as it reduces lead time and increases throughput.