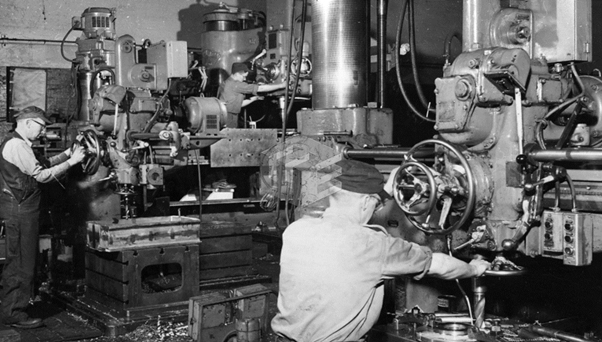
Manufacturers, whether they manufacture products for the general public or just for their own benefit, have an important role in our economy. The manufacturing industry creates jobs, supports the nation's infrastructure and provides materials to national defense. Manufacturing is actually the largest sector in our economy. Manufacturing provides goods for nearly everyone in society. Manufacturing is also a source of vital innovation. While some economists believe manufacturing will decline, others believe it'll continue to grow.
Manufacturers produce a variety products, including furniture and lighting. Each product requires a particular design, a series, of processes, and an investment into tools, labor, equipment, and in machinery. The manufacturing industries employ many skilled workers who are highly productive. In the United States, manufacturing workers earned an average of $79,000 per year in 2019.
To remain competitive in global markets, manufacturers need to use circular processes. These processes are designed to extend beyond the plant, to include the entire supply chain. Manufacturers must also consider the social costs of their processes. For example, many processes involve hazardous materials, which can affect the health of workers. The benefits of the product may outweigh the risks associated with hazardous waste cleanup, depending on how safe they are.
The manufacturing sector can play a key role in driving the economic recovery in the United States. Manufacturing's "indirect unemployment multiplier" is significant. Its purchasing power supports more that 1.4 jobs elsewhere in America. The strength of manufacturing can lead to the development and growth of local economies as well as communities.
The manufacturing sector plays an important role for economic development. But, the sector is also being under pressure. While many economists predict that manufacturing will continue growing, others think it will be outpaced by the post-goods economic. The policymakers should not forget the important role that manufacturing plays in economic innovation and resilience.
Manufacturing employs a diverse workforce. It also provides employment for workers with all levels of skill. Even workers without college degrees are paid more in the manufacturing sector than the average. Manufacturing workers are also employed in a wide range of industries. They are often employed as technicians, engineers, or production managers. There are four main types of manufacturing activities: Continuous manufacturing; batch process manufacturing; scale-based and standard activities; and discrete manufacturing.
Continuous manufacturing, also known as batch process manufacturing, involves a number of processes that run 24/7. Continuous manufacturing is used in oil refining, and food production. Although batch process manufacturing is similar in concept to continuous manufacturing, it uses a wider range of raw materials and processes. Batch process manufacturing also uses clean machinery for the next batch.
The U.S.'s manufacturing sector is a strong driver of inclusive growth. Manufacturing provides skilled jobs and domestic goods support many other jobs. Manufacturing is an important driver of economic development because of its high wages, and its "indirect job multiplier".
FAQ
How is a production manager different from a producer planner?
The major difference between a Production Planner and a Project Manager is that a Project Manager is often the person responsible for organizing and planning the entire project. While a Production Planner is involved mainly in the planning stage,
What does the term manufacturing industries mean?
Manufacturing Industries are businesses that produce products for sale. These products are sold to consumers. These companies employ many processes to achieve this purpose, such as production and distribution, retailing, management and so on. These companies produce goods using raw materials and other equipment. This covers all types of manufactured goods including clothing, food, building supplies and furniture, as well as electronics, tools, machinery, vehicles and pharmaceuticals.
How can overproduction in manufacturing be reduced?
Better inventory management is key to reducing excess production. This would decrease the time that is spent on inefficient activities like purchasing, storing, or maintaining excess stock. We could use these resources to do other productive tasks.
Kanban systems are one way to achieve this. A Kanbanboard is a visual tool that allows you to keep track of the work being done. A Kanban system allows work items to move through several states before reaching their final destination. Each state represents an individual priority level.
To illustrate, work can move from one stage or another when it is complete enough for it to be moved to a new stage. If a task is still in its beginning stages, it will continue to be so until it reaches the end.
This allows work to move forward and ensures that no work is missed. Managers can view the Kanban board to see how much work they have done. This allows them to adjust their workflows based on real-time information.
Lean manufacturing is another way to manage inventory levels. Lean manufacturing emphasizes eliminating waste in all phases of production. Waste includes anything that does not add value to the product. Here are some examples of common types.
-
Overproduction
-
Inventory
-
Unnecessary packaging
-
Material surplus
These ideas can help manufacturers improve efficiency and reduce costs.
What are my options for learning more about manufacturing
Hands-on experience is the best way to learn more about manufacturing. However, if that's not possible, you can always read books or watch educational videos.
Statistics
- It's estimated that 10.8% of the U.S. GDP in 2020 was contributed to manufacturing. (investopedia.com)
- In 2021, an estimated 12.1 million Americans work in the manufacturing sector.6 (investopedia.com)
- You can multiply the result by 100 to get the total percent of monthly overhead. (investopedia.com)
- According to the United Nations Industrial Development Organization (UNIDO), China is the top manufacturer worldwide by 2019 output, producing 28.7% of the total global manufacturing output, followed by the United States, Japan, Germany, and India.[52][53] (en.wikipedia.org)
- Job #1 is delivering the ordered product according to specifications: color, size, brand, and quantity. (netsuite.com)
External Links
How To
How to Use Just-In-Time Production
Just-in-time is a way to cut costs and increase efficiency in business processes. It is a process where you get the right amount of resources at the right moment when they are needed. This means that you only pay for what you actually use. Frederick Taylor developed the concept while working as foreman in early 1900s. He observed how workers were paid overtime if there were delays in their work. He decided that workers would be more productive if they had enough time to complete their work before they started to work.
The idea behind JIT is that you should plan ahead and have everything ready so you don't waste money. Also, you should look at the whole project from start-to-finish and make sure you have the resources necessary to address any issues. You can anticipate problems and have enough equipment and people available to fix them. This way you won't be spending more on things that aren’t really needed.
There are several types of JIT techniques:
-
Demand-driven: This JIT is where you place regular orders for the parts/materials that are needed for your project. This will let you track the amount of material left over after you've used it. It will also allow you to predict how long it takes to produce more.
-
Inventory-based: This allows you to store the materials necessary for your projects in advance. This allows you predict the amount you can expect to sell.
-
Project-driven : This is a method where you make sure that enough money is set aside to pay the project's cost. Knowing how much money you have available will help you purchase the correct amount of materials.
-
Resource-based JIT : This is probably the most popular type of JIT. Here, you allocate certain resources based on demand. You might assign more people to help with orders if there are many. If you don’t have many orders you will assign less people to the work.
-
Cost-based: This is a similar approach to resource-based but you are not only concerned with how many people you have, but also how much each one costs.
-
Price-based: This is a variant of cost-based. However, instead of focusing on the individual workers' costs, this looks at the total price of the company.
-
Material-based - This is a variant of cost-based. But instead of looking at the total company cost, you focus on how much raw material you spend per year.
-
Time-based JIT is another form of resource-based JIT. Instead of focusing on how much each employee costs, you focus on how long it takes to complete the project.
-
Quality-based JIT - This is another form of resource-based JIT. Instead of thinking about the cost of each employee or the time it takes to produce something, you focus on how good your product quality.
-
Value-based: This is one of the newest forms of JIT. This is where you don't care about how the products perform or whether they meet customers' expectations. Instead, your focus is on the value you bring to the market.
-
Stock-based: This stock-based method focuses on the actual quantity of products being made at any given time. This method is useful when you want to increase production while decreasing inventory.
-
Just-in time (JIT), planning: This is a combination JIT/supply chain management. It's the process of scheduling delivery of components immediately after they are ordered. This is important as it reduces lead time and increases throughput.