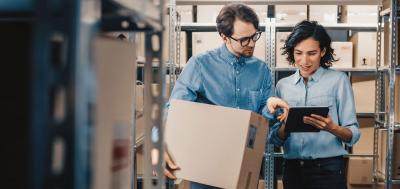
Industrial engineers use science and math to improve the efficiency of production processes. They are skilled at identifying flaws and developing solutions to improve productivity and performance. They also have the ability create efficient processes that make use of fewer resources. This career path is attractive for people who like working in groups and those who are self-sufficient. You can also advance your career and move into management.
Many industries may employ industrial engineers. They may be required to work with hazardous materials and high temperatures. They may have to travel to various locations in order for their work to be completed. They are expected to use email, phone and face-to–face communication to solve problems. They are also required to understand workplace safety laws and procedures.
Industrial engineers are valued for their ability to solve problems creatively. Many industrial engineers enjoy solving efficiency-related problems. To reduce production costs and increase efficiency, they may be asked to redesign assembly lines. They may also have to work overtime to meet deadlines. They might have the opportunity to collaborate with other engineers to create new production processes.
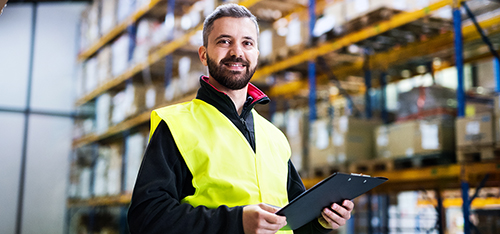
An industrial engineer must have good interpersonal skills. They should be able listen to and understand other people's words. They must be able to communicate well with their colleagues and supervisors. They should also be able use their critical thinking skills and identify alternative solutions to problems. They also have the ability to forecast changes and to take other steps to increase their chances of success.
Depending on their job, industrial engineers may have to work long hours, be in high-noise areas, or travel to other locations. Their personal and professional lives may become difficult. This can be difficult to manage, but it is possible to find ways to adjust to the demands of their work.
Industrial engineers usually have a bachelor's degree. They can then pursue a master’s or doctorate degree. This could take between two- and seven years. It is important to select a degree program that is suited for your needs. Many institutions offer online degrees for industrial engineering. These programs make it easy for students to complete their studies and avoid paying expensive tuition. They also offer flexibility in study time.
Industrial engineers may find it helpful to join professional organizations, such as the Institute of Industrial and Systems Engineers. This organization organizes conferences, publishes white papers and case studies, and supports industrial engineering professionals. It offers graduate fellowships. They can also benefit from MOOCs or certifications. They can also take part in fellowships offered by the American Society for Engineering Education.
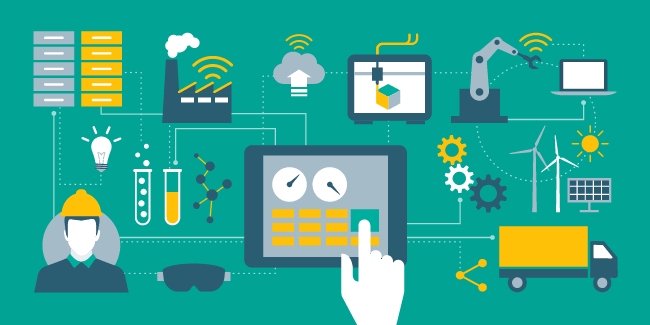
Industrial engineers can also find employment with government agencies. They may also need licensure. Some large companies may provide formal training. These employers appreciate the experience industrial engineers have.
FAQ
What is the difference in Production Planning and Scheduling, you ask?
Production Planning (PP) is the process of determining what needs to be produced at any given point in time. This is done through forecasting demand and identifying production capacities.
Scheduling refers the process by which tasks are assigned dates so that they can all be completed within the given timeframe.
What are the 7 R's of logistics?
The acronym "7R's" of Logistics stands for seven principles that underpin logistics management. It was developed and published by the International Association of Business Logisticians in 2004 as part of the "Seven Principles of Logistics Management".
The acronym consists of the following letters:
-
Responsive - ensure all actions are legal and not harmful to others.
-
Reliable – have faith in your ability and capability to keep promises.
-
Reasonable - make sure you use your resources well and don't waste them.
-
Realistic - consider all aspects of operations, including cost-effectiveness and environmental impact.
-
Respectful: Treat others with fairness and equity
-
Reliable - Find ways to save money and increase your productivity.
-
Recognizable provides value-added products and services to customers
What does "warehouse" mean?
A warehouse is a place where goods are stored until they are sold. It can be indoors or out. Sometimes, it can be both an indoor and outdoor space.
What are the logistics products?
Logistics is the process of moving goods from one point to another.
They encompass all aspects transport, including packaging and loading, transporting, storage, unloading.
Logisticians ensure the product reaches its destination in the most efficient manner. Logisticians assist companies in managing their supply chains by providing information such as demand forecasts, stock levels and production schedules.
They monitor shipments in transit, ensure quality standards, manage inventories, replenish orders, coordinate with suppliers and other vendors, and offer support services for sales, marketing, and customer service.
What does it take for a logistics enterprise to succeed?
A successful logistics business requires a lot more than just knowledge. For clients and suppliers to be successful, you need to have excellent communication skills. You should be able analyse data and draw inferences. You will need to be able handle pressure well and work in stressful situations. In order to innovate and create new ways to improve efficiency, creativity is essential. You will need strong leadership skills to motivate and direct your team members towards achieving their organizational goals.
To meet tight deadlines, you must also be efficient and organized.
What are manufacturing & logistics?
Manufacturing refers to the process of making goods using raw materials and machines. Logistics encompasses the management of all aspects associated with supply chain activities such as procurement, production planning, distribution and inventory control. It also includes customer service. Manufacturing and logistics can often be grouped together to describe a larger term that covers both the creation of products, and the delivery of them to customers.
What are the jobs in logistics?
There are many kinds of jobs available within logistics. Here are some:
-
Warehouse workers - They load trucks and pallets.
-
Transportation drivers – These drivers drive trucks and wagons to transport goods and pick up the goods.
-
Freight handlers: They sort and package freight in warehouses.
-
Inventory managers – They manage the inventory in warehouses.
-
Sales reps are people who sell products to customers.
-
Logistics coordinators – They plan and coordinate logistics operations.
-
Purchasing agents - They purchase goods and services needed for company operations.
-
Customer service representatives - They answer calls and emails from customers.
-
Ship clerks - They issue bills and process shipping orders.
-
Order fillers - They fill orders based on what is ordered and shipped.
-
Quality control inspectors: They inspect outgoing and incoming products for any defects.
-
Others - There is a variety of other jobs in logistics. These include transportation supervisors and cargo specialists.
Statistics
- You can multiply the result by 100 to get the total percent of monthly overhead. (investopedia.com)
- According to the United Nations Industrial Development Organization (UNIDO), China is the top manufacturer worldwide by 2019 output, producing 28.7% of the total global manufacturing output, followed by the United States, Japan, Germany, and India.[52][53] (en.wikipedia.org)
- It's estimated that 10.8% of the U.S. GDP in 2020 was contributed to manufacturing. (investopedia.com)
- Many factories witnessed a 30% increase in output due to the shift to electric motors. (en.wikipedia.org)
- Job #1 is delivering the ordered product according to specifications: color, size, brand, and quantity. (netsuite.com)
External Links
How To
Six Sigma in Manufacturing
Six Sigma can be described as "the use of statistical process control (SPC), techniques to achieve continuous improvement." Motorola's Quality Improvement Department, Tokyo, Japan, developed it in 1986. Six Sigma's basic concept is to improve quality and eliminate defects through standardization. Many companies have adopted Six Sigma in recent years because they believe that there are no perfect products and services. Six Sigma seeks to reduce variation between the mean production value. You can calculate the percentage of deviation from the norm by taking a sample of your product and comparing it to the average. If this deviation is too big, you know something needs fixing.
Understanding how your business' variability is a key step towards Six Sigma implementation is the first. Once you have a good understanding of the basics, you can identify potential sources of variation. Also, you will need to identify the sources of variation. Random variations happen when people make errors; systematic variations are caused externally. These are, for instance, random variations that occur when widgets are made and some fall off the production line. You might notice that your widgets always fall apart at the same place every time you put them together.
Once you've identified the problem areas you need to find solutions. You might need to change the way you work or completely redesign the process. After implementing the new changes, you should test them again to see if they worked. If they don’t work, you’ll need to go back and rework the plan.