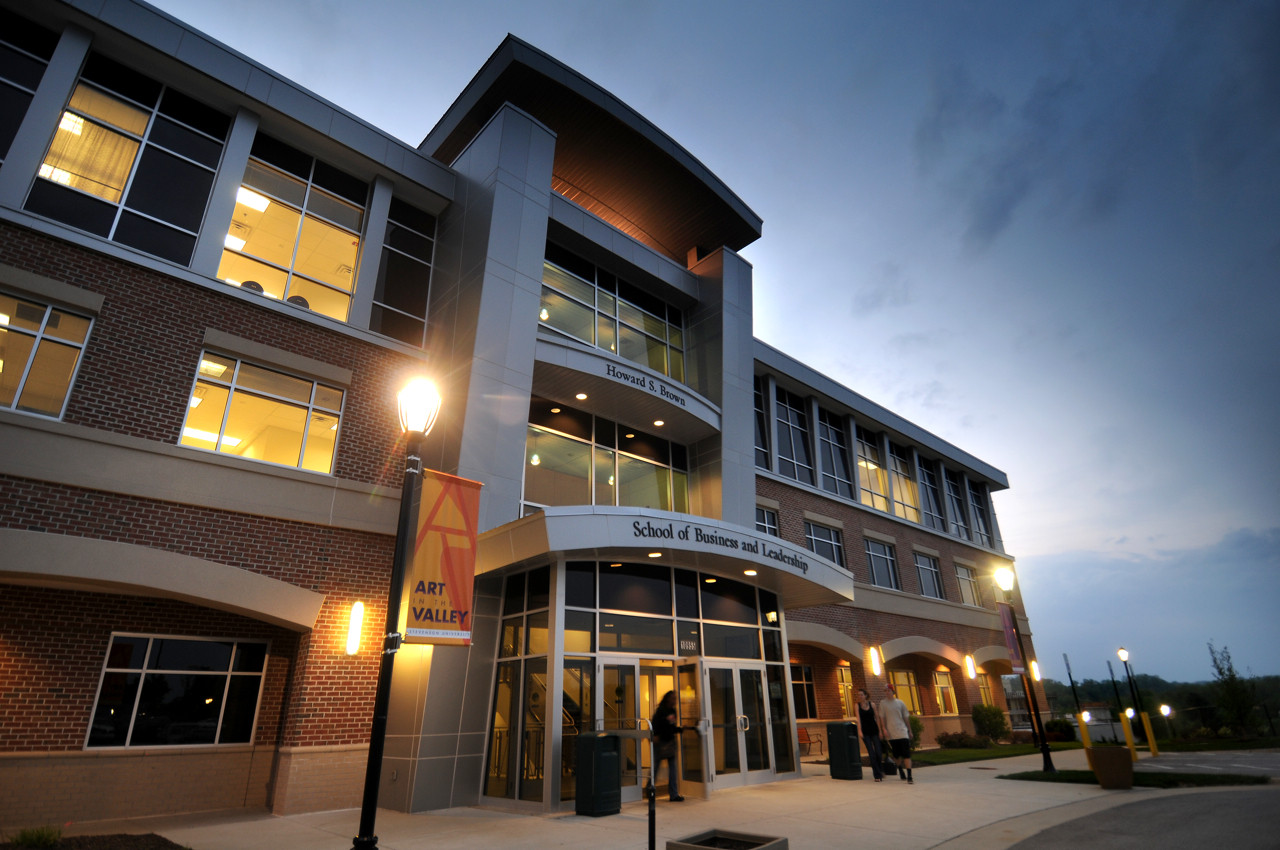
Lean training can help reduce waste and streamline processes. It encourages collaboration and results in more product. It is vital that every employee in the organization knows about lean. Training programs that are tailored to the needs and abilities of each member can make this happen.
Lean training is usually delivered in classrooms. It uses a hands on approach that combines classroom instruction with extensive hands-on experience. A typical course involves 4 to 8 hours per week of involvement by trainees. The goal is to prepare the participants to make suggestions for improvement. By using tools like value stream mapping and Plan-Do-Check-Act (PDCA), participants can improve the performance of their organization's processes.
Many companies opt to have their lean training done in-house, or hire professionals. Clemson University provides four different programs for employees.
Lean training can be a powerful tool for helping your company achieve success. More companies are using the method. You should look for a training program that covers all of the key elements of lean.
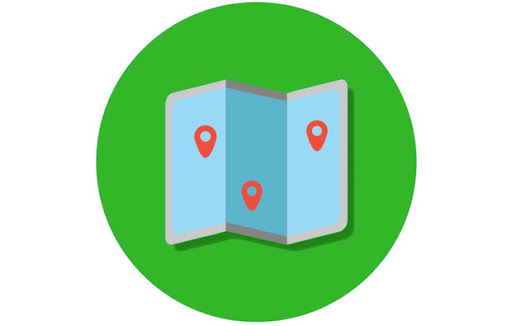
Your training should start with an introduction to lean. This workshop lasts two hours and will provide background information as well the principles. You will also learn about lean tools, such as value stream map and kanban. Additionally, you'll learn how to improve your customer experience.
Once you've mastered the basics, you can move on to the Lean Thinking unit. Here, you'll learn about value stream mapping, error-proofing, and continuous flow. All these methods can be used to identify and reduce waste within your business.
Afterwards, you'll learn about Plan-Do-Check-Act (PDCA). PDCA is a Lean improvement technique that most practitioners use. During the course, you'll also study the root causes of problems.
Learn how to create a lean-action plan. It outlines your current state, as well as any improvements you wish to make. You'll be presented with a certificate upon completion. To obtain your certification, you must pass a multi-choice exam using the Lean Management Courseware.
You will be able apply the knowledge you have gained to your job after you have completed the program. Whether you're a manager, supervisor, or technician, you'll be able to effectively manage change and lead other team members through the process. You will ultimately be able see positive outcomes.
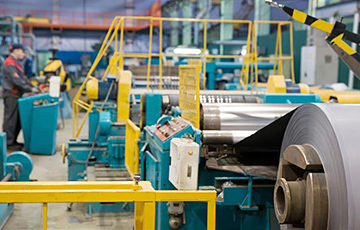
Finally, you will be able earn your Green Belt certification. The Lean training program at Virginia University Medical Center (VUMC) is managed by April Saunders. She has over 12 years of experience working in the manufacturing industry and teaches Lean to her students.
Lean Fundamentals is available in several languages. Participants are taught how to quickly implement Lean concepts in their workplaces. You can expect a positive impact on your workplace as a result of this class.
This workshop will help you get started in lean implementing in your business, or to simply brush up your skills.
FAQ
What is production management?
Production Planning refers to the development of a plan for every aspect of production. This document ensures that everything is prepared and available when you are ready for shooting. This document should include information about how to achieve the best results on-set. This includes location information, crew details, equipment specifications, and casting lists.
The first step is to decide what you want. You may have already decided where you would like to shoot, or maybe there are specific locations or sets that you want to use. Once you have identified your locations and scenes, you can start working out which elements you require for each scene. One example is if you are unsure of the exact model you want but decide that you require a car. In this case, you could start looking up cars online to find out what models are available and then narrow your choices by choosing between different makes and models.
After you have chosen the right car, you will be able to begin thinking about accessories. Do you need people sitting in the front seats? Or maybe you just need someone to push the car around. You might want to change your interior color from black and white. These questions will help you determine the exact look and feel of your car. Another thing you can do is think about what type of shots are desired. You will be filming close-ups and wide angles. Maybe you want to show the engine and the steering wheel. This will allow you to determine the type of car you want.
Once you have determined all of the above, you can move on to creating a schedule. The schedule will show you when to begin shooting and when to stop. You will need to know when you have to be there, what time you have to leave and when your return home. It will help everyone know exactly what they have to do and when. Book extra staff ahead of time if you need them. There is no point in hiring someone who won't turn up because you didn't let him know.
Your schedule will also have to be adjusted to reflect the number of days required to film. Some projects may only take a couple of days, while others could last for weeks. You should consider whether you will need more than one shot per week when creating your schedule. Multiple shots at the same location can increase costs and make it more difficult to complete. It is better to be cautious and take fewer shots than you risk losing money if you are not sure if multiple takes are necessary.
Budget setting is an important part of production planning. Setting a realistic budget is essential as it will allow you to work within your means. If you have to reduce your budget due to unexpected circumstances, you can always lower it later. It is important to not overestimate how much you will spend. If you underestimate how much something costs, you'll have less money to pay for other items.
Production planning is a detailed process. But, once you understand the workings of everything, it becomes easier for future projects to be planned.
How can overproduction in manufacturing be reduced?
It is essential to find better ways to manage inventory to reduce overproduction. This would reduce the amount of time spent on unnecessary activities such as purchasing, storing, and maintaining excess stock. This could help us free up our time for other productive tasks.
A Kanban system is one way to achieve this. A Kanban board can be used to monitor work progress. In a Kanban system, work items move through a sequence of states until they reach their final destination. Each state is assigned a different priority.
When work is completed, it can be transferred to the next stage. But if a task remains in the beginning stages it will stay that way until it reaches its end.
This helps to keep work moving forward while ensuring that no work is left behind. A Kanban board allows managers to monitor how much work is being completed at any given moment. This information allows them to adjust their workflow based on real-time data.
Lean manufacturing is another option to control inventory levels. Lean manufacturing is about eliminating waste from all stages of the production process. Anything that does nothing to add value to a product is waste. The following are examples of common waste types:
-
Overproduction
-
Inventory
-
Unnecessary packaging
-
Exceed materials
By implementing these ideas, manufacturers can improve efficiency and cut costs.
What is the responsibility of a production planner?
Production planners ensure that all project aspects are completed on time, within budget and within the scope. They also ensure the quality of the product and service meets the client's requirements.
How can manufacturing prevent production bottlenecks?
Avoiding production bottlenecks is as simple as keeping all processes running smoothly, from the time an order is received until the product ships.
This includes both planning for capacity and quality control.
This can be done by using continuous improvement techniques, such as Six Sigma.
Six Sigma is a management method that helps to improve quality and reduce waste.
It seeks to eliminate variation and create consistency in your work.
What type of jobs is there in logistics
There are different kinds of jobs available in logistics. Here are some examples:
-
Warehouse workers - They load and unload trucks and pallets.
-
Transportation drivers - They drive trucks and trailers to deliver goods and carry out pick-ups.
-
Freight handlers, - They sort out and pack freight in warehouses.
-
Inventory managers - They oversee the inventory of goods in warehouses.
-
Sales representatives - They sell products.
-
Logistics coordinators: They plan and manage logistics operations.
-
Purchasing agents - They purchase goods and services needed for company operations.
-
Customer service representatives are available to answer customer calls and emails.
-
Shipping clerks - They process shipping orders and issue bills.
-
Order fillers – They fill orders based upon what was ordered and shipped.
-
Quality control inspectors: They inspect outgoing and incoming products for any defects.
-
Others – There are many other types available in logistics. They include transport supervisors, cargo specialists and others.
How can I learn about manufacturing?
Hands-on experience is the best way to learn more about manufacturing. You can read books, or watch instructional videos if you don't have the opportunity to do so.
Statistics
- (2:04) MTO is a production technique wherein products are customized according to customer specifications, and production only starts after an order is received. (oracle.com)
- In 2021, an estimated 12.1 million Americans work in the manufacturing sector.6 (investopedia.com)
- It's estimated that 10.8% of the U.S. GDP in 2020 was contributed to manufacturing. (investopedia.com)
- Job #1 is delivering the ordered product according to specifications: color, size, brand, and quantity. (netsuite.com)
- According to a Statista study, U.S. businesses spent $1.63 trillion on logistics in 2019, moving goods from origin to end user through various supply chain network segments. (netsuite.com)
External Links
How To
How to use lean manufacturing in the production of goods
Lean manufacturing is an approach to management that aims for efficiency and waste reduction. It was first developed in Japan in the 1970s/80s by Taiichi Ahno, who was awarded the Toyota Production System (TPS), award from KanjiToyoda, the founder of TPS. Michael L. Watkins published the "The Machine That Changed the World", the first book about lean manufacturing. It was published in 1990.
Lean manufacturing is often defined as a set of principles used to improve the quality, speed, and cost of products and services. It emphasizes the elimination and minimization of waste in the value stream. The five-steps of Lean Manufacturing are just-in time (JIT), zero defect and total productive maintenance (TPM), as well as 5S. Lean manufacturing seeks to eliminate non-value added activities, such as inspection, work, waiting, and rework.
Lean manufacturing not only improves product quality but also reduces costs. Companies can also achieve their goals faster by reducing employee turnover. Lean Manufacturing is one of the most efficient ways to manage the entire value chains, including suppliers and customers as well distributors and retailers. Lean manufacturing is widely used in many industries. Toyota's philosophy, for example, is what has enabled it to be successful in electronics, automobiles, medical devices, healthcare and chemical engineering as well as paper and food.
Five basic principles of Lean Manufacturing are included in lean manufacturing
-
Define Value: Identify the social value of your business and what sets you apart.
-
Reduce Waste – Eliminate all activities that don't add value throughout the supply chain.
-
Create Flow - Make sure work runs smoothly without interruptions.
-
Standardize and Simplify – Make processes as consistent, repeatable, and as simple as possible.
-
Build relationships - Develop and maintain personal relationships with both your internal and external stakeholders.
Lean manufacturing is not a new concept, but it has been gaining popularity over the last few years due to a renewed interest in the economy following the global financial crisis of 2008. Many businesses have adopted lean manufacturing techniques to help them become more competitive. According to some economists, lean manufacturing could be a significant factor in the economic recovery.
Lean manufacturing is becoming a popular practice in automotive. It has many advantages. These include higher customer satisfaction levels, reduced inventory levels as well as lower operating costs.
Any aspect of an enterprise can benefit from Lean manufacturing. Because it makes sure that all value chains are efficient and effectively managed, Lean Manufacturing is particularly helpful for organizations.
There are three main types:
-
Just-in-Time Manufacturing (JIT): This type of lean manufacturing is commonly referred to as "pull systems." JIT means that components are assembled at the time of use and not manufactured in advance. This approach reduces lead time, increases availability and reduces inventory.
-
Zero Defects Manufacturing - ZDM: ZDM focuses its efforts on making sure that no defective units leave a manufacturing facility. If a part needs to be fixed during the assembly line, it should be repaired rather than scrapped. This applies to finished products, which may need minor repairs before they are shipped.
-
Continuous Improvement: Continuous Improvement aims to improve efficiency by continually identifying problems and making adjustments to eliminate or minimize waste. It involves continuous improvement of processes, people, and tools.